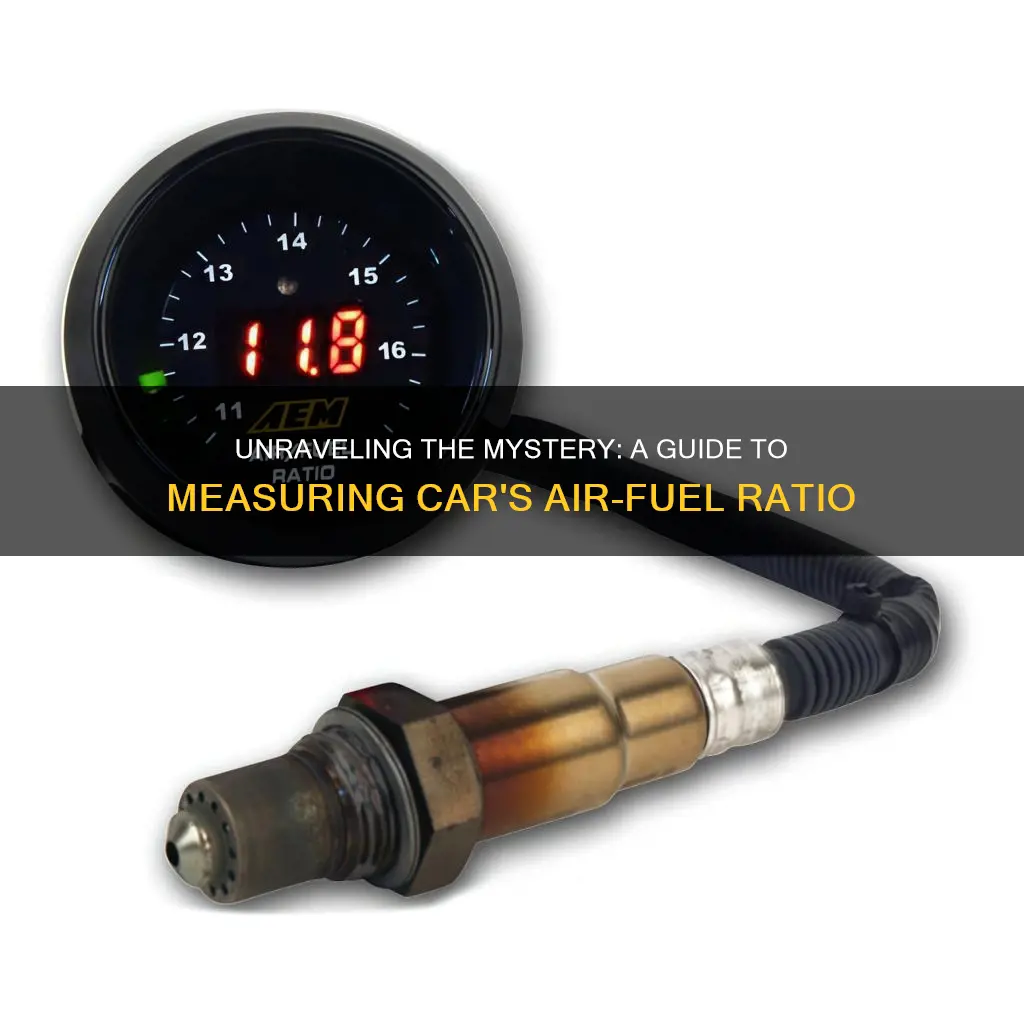
Understanding a car's air-fuel ratio is crucial for optimizing engine performance and fuel efficiency. The air-fuel ratio, often referred to as the lambda value, is the ratio of the mass of air to the mass of fuel in a combustion engine. This ratio directly impacts how efficiently an engine burns fuel, affecting its power output, emissions, and overall performance. By measuring and adjusting this ratio, mechanics and enthusiasts can fine-tune an engine's operation, ensuring it runs smoothly and efficiently while minimizing harmful emissions. This guide will explore various methods and tools used to determine a car's air-fuel ratio, providing insights into the science behind engine management systems.
What You'll Learn
- Engine Sensors: Understand how oxygen and mass airflow sensors provide data for the air-fuel ratio calculation
- Fuel Injection: Learn about the role of fuel injectors in delivering the correct fuel-air mixture
- Engine Control Unit (ECU): Discover how the ECU processes sensor data to adjust fuel delivery
- Diagnostic Tools: Explore the use of diagnostic scanners to read air-fuel ratio data and identify issues
- Performance Tuning: Adjust air-fuel ratios for optimal engine performance and fuel efficiency
Engine Sensors: Understand how oxygen and mass airflow sensors provide data for the air-fuel ratio calculation
The air-fuel ratio, a critical parameter in engine performance, is the ratio of the mass of air to the mass of fuel in a combustion engine. It is a crucial factor in determining engine efficiency, power output, and emissions. Modern vehicles use sophisticated sensors to monitor this ratio, ensuring optimal engine operation. Among these sensors, the oxygen sensor and mass airflow (MAF) sensor play pivotal roles in providing the necessary data for the air-fuel ratio calculation.
Oxygen sensors, often located in the exhaust manifold or close to the catalytic converter, measure the oxygen content in the exhaust gases. They provide real-time feedback on the oxygen levels, which is essential for the engine's electronic control unit (ECU) to make adjustments. The ECU uses this information to determine if the air-fuel mixture is lean (too much air) or rich (too much fuel). When the oxygen sensor detects a higher-than-normal oxygen level, it indicates a lean mixture, prompting the ECU to enrich the fuel injection to achieve a balanced air-fuel ratio. Conversely, a low oxygen level suggests a rich mixture, and the ECU adjusts to leaner conditions.
Mass airflow sensors, on the other hand, measure the actual mass of air entering the engine. These sensors are typically located in the intake manifold and provide a direct measurement of the air volume. By calculating the mass of air, the MAF sensor helps the ECU understand the engine's breathing rate. This data is crucial for accurate fuel injection timing and quantity calculations. The ECU uses the MAF sensor reading to determine the appropriate fuel-air mixture, ensuring the engine operates at its most efficient level.
The combination of oxygen and mass airflow sensors offers a comprehensive view of the engine's performance. Oxygen sensors provide dynamic feedback on the exhaust gases, allowing for immediate adjustments to maintain the desired air-fuel ratio. Meanwhile, MAF sensors offer a static measurement of air intake, which is vital for long-term engine management. Together, these sensors enable the ECU to fine-tune the fuel injection process, optimizing power output, fuel efficiency, and emissions control.
In summary, engine sensors, particularly oxygen and mass airflow sensors, are integral to modern vehicle technology. They provide the necessary data for the air-fuel ratio calculation, ensuring the engine operates efficiently and within environmental regulations. Understanding the role of these sensors highlights the complexity and precision required in modern automotive engineering to achieve optimal engine performance.
Navigating Fuel Tax: Tips to Avoid the Car Fuel Benefit Charge
You may want to see also
Fuel Injection: Learn about the role of fuel injectors in delivering the correct fuel-air mixture
Fuel injectors are a crucial component of modern vehicle engines, responsible for precisely delivering the correct amount of fuel to create an optimal fuel-air mixture. This process is essential for efficient combustion, ensuring the engine operates at its peak performance while minimizing emissions. The fuel injectors are designed to spray fuel in a fine mist, which mixes with the air in the combustion chamber, creating a homogeneous mixture. This mixture is then ignited, producing power and driving the vehicle's wheels.
The operation of fuel injectors is a complex process that requires precise timing and control. When the engine's computer (ECU) detects a need for fuel, it sends an electric signal to the fuel injector. This signal triggers the injector to open and spray fuel into the intake manifold or directly into the combustion chamber. The timing and duration of this spray are carefully controlled to ensure the fuel is atomized to the correct size, allowing for efficient mixing with air.
Modern fuel injectors are highly efficient and can deliver fuel at extremely high pressures, often exceeding 3000 psi. This high pressure ensures that the fuel is broken down into tiny droplets, which have a large surface area, facilitating better mixing with the air. The injectors are also designed to spray fuel in a specific pattern, optimizing the fuel-air mixture's distribution within the combustion chamber. This precise control over fuel delivery is a significant advancement from the older carburetor systems, which had less control over the fuel-air ratio.
The role of fuel injectors is particularly important in maintaining the correct air-fuel ratio, which is critical for engine performance and emissions. The ideal air-fuel ratio varies depending on the engine type and operating conditions, but it is typically around 14.7:1 (air to fuel by weight). Fuel injectors help achieve this ratio by delivering the precise amount of fuel required for complete combustion. This ensures that the engine runs smoothly, efficiently, and with minimal harmful emissions.
In summary, fuel injectors are a sophisticated system that plays a vital role in modern vehicle engines. They ensure the engine receives the correct fuel-air mixture, optimizing performance and minimizing environmental impact. Understanding the function of fuel injectors and their contribution to the air-fuel ratio is essential for anyone interested in engine mechanics and vehicle performance.
Jerking Car: Is a Bad Fuel Pump to Blame?
You may want to see also
Engine Control Unit (ECU): Discover how the ECU processes sensor data to adjust fuel delivery
The Engine Control Unit (ECU) is the brain of a modern vehicle's engine management system. It plays a crucial role in optimizing engine performance and ensuring efficient combustion by processing data from various sensors and making real-time adjustments to fuel delivery. This intricate process is fundamental to maintaining the ideal air-fuel ratio, which is critical for engine operation and emissions control.
At the heart of this process are several sensors that provide the ECU with vital information about the engine's operating conditions. The most critical sensor for air-fuel ratio determination is the oxygen sensor, often located in the exhaust manifold or near the catalytic converter. This sensor measures the oxygen content in the exhaust gases, providing feedback on the richness or leaness of the air-fuel mixture. The ECU uses this data to make precise adjustments to the fuel injection system.
When the oxygen sensor detects a lean mixture (low oxygen content), the ECU interprets this as an indication of an air-fuel ratio that is too rich. In response, the ECU increases the fuel injection to enrich the mixture, moving it closer to the ideal ratio. Conversely, if the oxygen sensor detects a rich mixture (high oxygen content), the ECU reduces the fuel injection to lean out the mixture, again aiming for the optimal air-fuel ratio. This dynamic adjustment ensures that the engine operates efficiently and produces the desired power output while minimizing harmful emissions.
The ECU's ability to process sensor data and adjust fuel delivery is a complex and rapid process. It involves continuous monitoring and calculation, taking into account various factors such as engine speed, load, temperature, and the specific characteristics of the vehicle's fuel injection system. By making these real-time adjustments, the ECU ensures that the engine operates at its most efficient and environmentally friendly state.
In summary, the Engine Control Unit (ECU) is a sophisticated system that plays a vital role in maintaining the ideal air-fuel ratio in a vehicle's engine. Through the use of sensor data, particularly from the oxygen sensor, the ECU makes precise adjustments to fuel delivery, ensuring optimal engine performance and minimal environmental impact. This process is a testament to the advanced technology employed in modern vehicles to balance power, efficiency, and emissions control.
Fuel Injection: The Evolution of Carburetors in Modern Cars
You may want to see also
Diagnostic Tools: Explore the use of diagnostic scanners to read air-fuel ratio data and identify issues
Diagnostic scanners, also known as OBD-II (On-Board Diagnostics II) scanners, are powerful tools for modern vehicle owners and mechanics alike. These devices provide a wealth of information about a vehicle's performance, including the air-fuel ratio, a critical parameter for engine efficiency and emissions control. By connecting to the vehicle's OBD-II port, which is usually located under the dashboard, these scanners can access and display real-time data from various sensors and systems.
When it comes to optimizing a car's air-fuel ratio, diagnostic scanners are invaluable. The air-fuel ratio refers to the mass ratio of air to fuel in the combustion chamber. An ideal ratio is crucial for efficient combustion, ensuring the engine runs smoothly and produces minimal emissions. Modern vehicles are equipped with sophisticated sensors, such as the oxygen sensors, that monitor this ratio and provide feedback to the engine control unit (ECU). The ECU then adjusts the fuel injection accordingly to maintain the optimal ratio.
Diagnostic scanners can read and display the live data from these sensors, giving users a clear understanding of the current air-fuel ratio. This real-time data allows for immediate identification of any deviations from the ideal ratio. For instance, a scanner might show a lean mixture, indicating too much air and insufficient fuel, or a rich mixture, suggesting the opposite. By monitoring these ratios, drivers and mechanics can quickly pinpoint potential issues, such as faulty sensors, incorrect fuel programming, or inefficient combustion.
Furthermore, these tools often provide error codes and trouble codes, which are essential for diagnosing specific problems. When an issue is detected, the scanner can store these codes, which are then displayed as error messages. These codes are specific to different vehicle makes and models, and they guide the user or mechanic towards the exact cause of the problem. For example, a code related to the air-fuel ratio might indicate a faulty mass airflow (MAF) sensor or an issue with the fuel injectors.
In summary, diagnostic scanners are essential for anyone looking to optimize their vehicle's performance and emissions. By providing access to real-time air-fuel ratio data and error codes, these tools empower both car enthusiasts and professionals to identify and address issues promptly. With the ability to read and interpret sensor data, these scanners are a vital component in modern vehicle maintenance and troubleshooting.
E85 Flexibility: Can E10 Fuel Replace E85?
You may want to see also
Performance Tuning: Adjust air-fuel ratios for optimal engine performance and fuel efficiency
To optimize engine performance and fuel efficiency, understanding and adjusting the air-fuel ratio is crucial. This ratio, often referred to as the A/F ratio, is the mixture of air and fuel that enters the engine's combustion chamber. The ideal A/F ratio varies depending on the engine type and its specific requirements, but generally, a leaner mixture (more air, less fuel) tends to improve performance and fuel economy, while a richer mixture (more fuel, less air) can lead to reduced performance and increased emissions.
The process of determining the current A/F ratio involves using specialized equipment, such as an engine analyzer or a wideband oxygen sensor. These tools can measure the actual A/F ratio and provide valuable insights into the engine's performance. For instance, a wideband oxygen sensor can monitor the oxygen levels in the exhaust, allowing for real-time adjustments to optimize the mixture.
Once you have the current A/F ratio data, you can start the process of adjustment. This typically involves modifying the fuel injection system or the air intake system. For fuel injection, you might need to adjust the fuel pressure, spray angle, or the use of fuel injectors with different flow rates. For the air intake, you could consider changing the air filter, modifying the air box, or even using a performance air intake system that increases the air flow into the engine.
Fine-tuning the A/F ratio requires patience and a methodical approach. It's essential to make small adjustments and then test the engine's performance after each change. This iterative process helps in understanding the impact of each modification and allows for precise optimization. Additionally, it's crucial to consider the engine's operating conditions, such as temperature, load, and speed, as these factors influence the ideal A/F ratio.
In summary, adjusting the air-fuel ratio is a critical aspect of performance tuning, offering a direct path to improved engine efficiency and power. By carefully measuring, modifying, and testing the A/F ratio, enthusiasts and tuners can unlock the full potential of their engines while ensuring optimal fuel efficiency. This process requires technical knowledge and a systematic approach to achieve the best results.
Fuel Filter's Role in Car Hesitation: Uncovering the Hidden Cause
You may want to see also
Frequently asked questions
The air-fuel ratio is the ratio of the mass of air to the mass of fuel in a combustion engine. It is a critical parameter because it directly affects engine performance, fuel efficiency, and emissions. An optimal air-fuel ratio ensures that the engine burns fuel efficiently, producing the desired power output while minimizing harmful pollutants.
Measuring the air-fuel ratio can be done using various methods. One common approach is to use an engine diagnostic tool, often referred to as an OBD-II scanner, which can provide real-time data on the ratio. These tools connect to the vehicle's On-Board Diagnostics (OBD) system and display the ratio as a percentage, such as 14.7:1, indicating a stoichiometric mixture. Another method involves using a fuel-air ratio gauge, which can be installed in the vehicle's intake system to provide a direct measurement.
The ideal air-fuel ratio varies depending on the engine type and design. For gasoline engines, a stoichiometric ratio of approximately 14.7:1 is often considered optimal for maximum power and fuel efficiency. However, in high-performance applications, a slightly leaner mixture (e.g., 12:1) might be used to increase power output. Diesel engines typically operate at a leaner ratio, around 15:1 to 20:1, to ensure complete combustion and reduce emissions.
Manually adjusting the air-fuel ratio is generally not recommended for most vehicle owners. It requires specialized equipment and a thorough understanding of engine tuning. Making incorrect adjustments can lead to poor engine performance, increased emissions, and even engine damage. It is best to consult a professional mechanic or use the vehicle's OBD system to monitor and adjust the ratio if necessary.