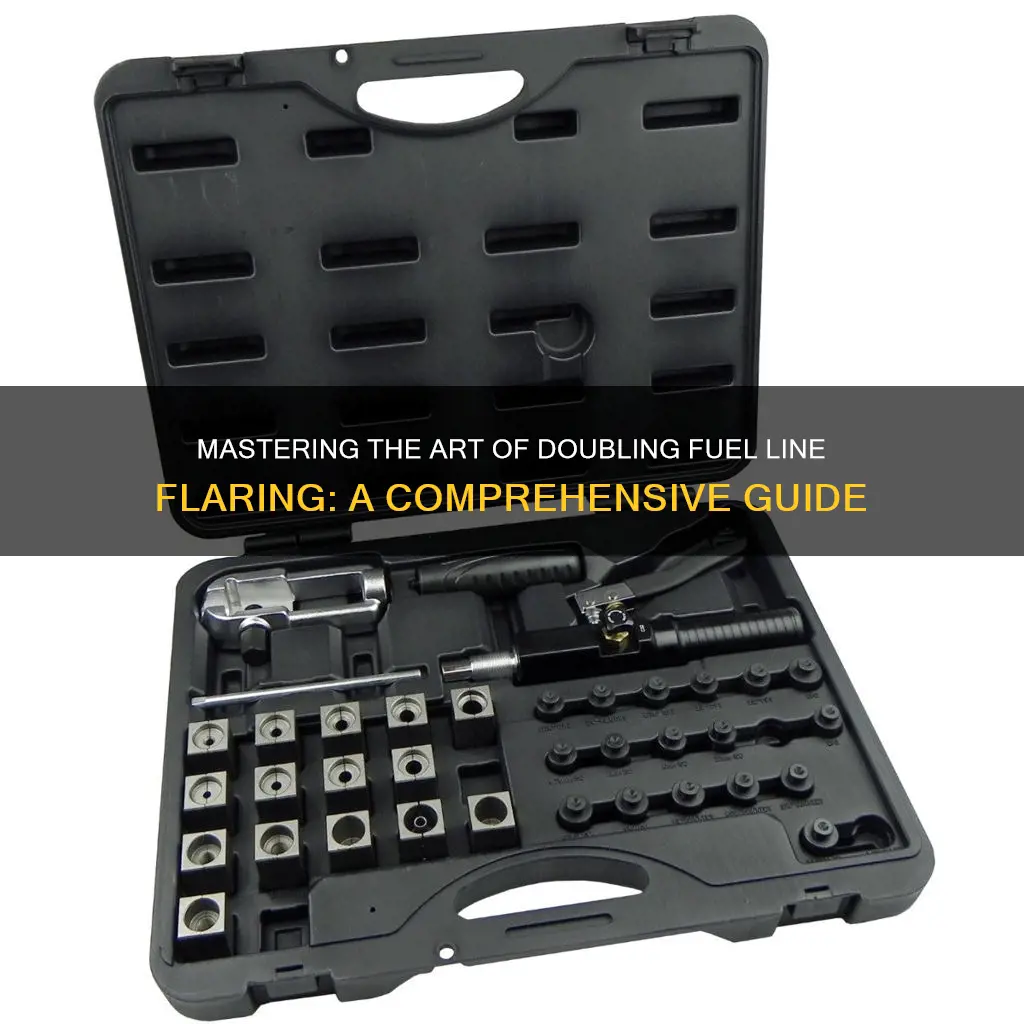
Doubling a 3/8 fuel line is a common task in automotive and marine applications, often required for engine modifications or system upgrades. This process involves creating a flare that is twice the size of a standard flare, ensuring a secure and leak-free connection. The technique requires precision and the right tools, including a flare tool and a die, to achieve a tight and reliable seal. This guide will provide a step-by-step process for successfully doubling a 3/8 fuel line flare, ensuring a professional and safe installation.
What You'll Learn
- Materials and Tools: Gather necessary supplies like fuel line, flare nuts, and a flare gun
- Preparation: Clean and inspect the fuel line for damage or debris
- Flare Process: Use a flare gun to create a flare at each end of the fuel line
- Tighten Connections: Securely fasten flare nuts to ensure a tight seal
- Testing: Verify the connection by checking for leaks and proper flow
Materials and Tools: Gather necessary supplies like fuel line, flare nuts, and a flare gun
To begin the process of double flaring a 3/8 fuel line, you'll need to gather the essential materials and tools. This ensures you have everything required to complete the task efficiently and effectively. Here's a detailed breakdown of the supplies you should collect:
Fuel Line: The primary component you'll be working with is the 3/8 fuel line. Ensure you have a length of fuel line that is suitable for the application and meets the required specifications. It's important to inspect the fuel line for any damage or wear before starting the flaring process.
Flaring Nuts: These nuts are specifically designed to create the flare connection. You'll need a set of flare nuts in the appropriate size for your fuel line. Common sizes include 1/4, 3/8, and 1/2 inches. Make sure to get the correct size that matches the fuel line diameter.
Flaring Gun: A flare gun is a specialized tool used to create the flare connection. It applies pressure to the fuel line and flare nut, forming a tight seal. Choose a flare gun that is compatible with the size of the flare nuts you've selected. Different models may offer various features, such as adjustable pressure settings or ergonomic designs, so select one that suits your preferences and the task at hand.
Other Tools: In addition to the above, you might want to have some basic hand tools readily available. This includes a pair of pliers for holding the fuel line securely during the flaring process, a wrench or spanner for tightening the flare nuts, and possibly a pipe cutter or file for any necessary adjustments or modifications to the fuel line.
Having all these materials and tools ready will ensure that you can proceed with the double flaring process smoothly and efficiently, minimizing any potential delays or complications. It's always a good practice to double-check the compatibility of the supplies with your specific fuel line and application to ensure a successful outcome.
Reverse-Engineer Your Mustang: Fuel Line Swap Guide
You may want to see also
Preparation: Clean and inspect the fuel line for damage or debris
Before you begin the process of double flaring a 3/8 fuel line, it is crucial to ensure that the preparation stage is thorough. Start by cleaning the fuel line to remove any dirt, debris, or contaminants that may interfere with the flaring process. Use a mild detergent or a specialized fuel line cleaner to wash the line. Rinse it thoroughly with clean water to eliminate any residue. This step is essential to ensure a clean and smooth surface for the flare.
Next, inspect the fuel line for any signs of damage or wear. Look for cracks, punctures, or any other visible defects. Check for kinks or bends that might affect the line's flexibility and integrity. It is critical to identify and address any issues before proceeding with the flaring. If you notice any damage, you may need to replace the affected section of the fuel line or seek professional assistance.
Pay close attention to the connections and fittings. Ensure that they are in good condition and securely attached. Over time, fittings can become corroded or damaged, leading to potential leaks or reduced performance. If you find any faulty connections, consider replacing them with new, high-quality fittings to ensure a reliable and safe fuel line system.
Additionally, check for any existing flares or bends in the fuel line. These should be straight and free of any sharp turns that could cause stress on the material. Any pre-existing damage or incorrect bends might require adjustment or correction before the double flaring process can be applied.
By thoroughly cleaning and inspecting the fuel line, you can ensure that the double flaring process is performed correctly and effectively. This preparation step is vital to guarantee a successful and long-lasting repair or modification to your fuel line system.
Polaris Ranger Fuel Line: Location and Access Guide
You may want to see also
Flare Process: Use a flare gun to create a flare at each end of the fuel line
The process of double flaring a 3/8 fuel line is a crucial step in ensuring a secure and leak-free connection, especially in automotive or industrial applications where fuel lines are used. This method involves creating a flare at both ends of the fuel line, providing a robust and reliable joint. Here's a detailed guide on how to achieve this:
Gather the Tools and Materials: Before beginning, ensure you have the necessary tools and materials. You'll need a flare gun, which is a specialized tool designed for creating flares. The flare gun should be compatible with the 3/8 fuel line size. Additionally, have the fuel line itself, cutting tools (such as a pipe cutter or a utility knife), and a supply of replacement flares or flare inserts. It's essential to use the correct size and type of flare for your specific application.
Prepare the Fuel Line: Start by cutting the fuel line to the desired length using the appropriate cutting tool. Ensure a clean and precise cut to facilitate a better flare creation process. After cutting, inspect the ends of the fuel line for any debris or imperfections. Use a wire brush or a small file to smooth and clean the surfaces, ensuring a solid base for the flare.
Create the Flare: Now, it's time to use the flare gun. Position the flare gun onto one end of the fuel line, aligning the threads or the flare gun's base with the fuel line's end. Apply firm pressure and activate the flare gun according to the manufacturer's instructions. The gun will create a flare, forming a raised ridge around the fuel line's end. Repeat this process for the other end of the fuel line, ensuring symmetry and consistency in the flare creation.
Check and Secure the Flare: Once both flares are created, inspect them closely. The flare should be smooth, continuous, and free of any sharp edges. If necessary, use a file or sandpaper to refine the flare's shape and ensure a tight fit. Then, insert the replacement flares or flare inserts into the newly created flares. Tighten the connections securely using the appropriate tools, such as a wrench or a flare tool, to ensure a leak-free seal.
Final Steps: After securing the flares, test the fuel line connection by applying pressure and checking for any leaks. If everything is in order, you've successfully double flared the 3/8 fuel line. This method provides an excellent seal, making it ideal for applications where fuel lines are exposed to vibrations or extreme conditions. Remember to follow safety guidelines when using power tools and always wear appropriate personal protective equipment.
The Strange Sound of Frozen Fuel Lines: A Guide
You may want to see also
Tighten Connections: Securely fasten flare nuts to ensure a tight seal
When working with double flare 3/8 fuel lines, ensuring tight and secure connections is crucial to prevent leaks and maintain the integrity of your fuel system. Here's a step-by-step guide to achieving this:
Start by preparing the flare nut and the fuel line. Ensure the flare nut is clean and free of any debris or contaminants. Check that the fuel line is free of any bends or kinks that might affect the flare process. It's essential to have a smooth and straight surface for the best connection.
Now, it's time to flare the fuel line. Use a flare tool specifically designed for this purpose. Position the tool over the fuel line, aligning it with the flare nut. Apply firm pressure to the tool, following the manufacturer's instructions for the correct amount of force. The goal is to create a tight, crimped connection between the fuel line and the flare nut. Take your time with this step to ensure a proper flare.
After flaring, inspect the connection closely. The flare nut should be securely attached to the fuel line, forming a tight seal. Check for any gaps or imperfections in the flare. If there are any, carefully re-flare the connection and recheck. Ensuring a tight seal is vital to prevent fuel leaks and potential engine damage.
Once you're satisfied with the flare, it's time to tighten the connection. Use a wrench to secure the flare nut in place. Apply a steady and firm force, turning the nut clockwise until it is snug. Avoid over-tightening, as it can damage the fuel line or flare nut. The goal is to achieve a secure hold without applying excessive force.
Finally, test the connection by applying pressure and checking for any leaks. If everything is tight and secure, your double flare 3/8 fuel line connection is ready for use. Remember, proper tightening ensures the longevity of your fuel system and prevents any unwanted fuel loss.
Unclogging a Fuel Line: A Home Tank's Quick Fix
You may want to see also
Testing: Verify the connection by checking for leaks and proper flow
When working with double flare 3/8 fuel lines, it's crucial to ensure that the connections are secure and leak-free. Here's a detailed guide on how to verify the connections and test for proper flow:
Leak Testing: Start by applying a small amount of diesel fuel or a suitable sealant around the threads of the double flare connection. This step is essential as it helps identify any potential leaks. After applying the fuel, rotate the fitting and ensure it is tight. Then, observe the connection for any signs of fuel escaping. If there are no leaks, you can proceed to the next step. However, if you notice any fuel seeping or dripping, it indicates a potential issue with the connection. In such cases, you might need to tighten the fitting further or consider using a different sealant to ensure a secure seal.
Flow Testing: Once the connections are secure, it's time to test the flow of fuel. Attach a fuel pressure gauge to the line, ensuring it is properly connected and secure. Start the engine and allow it to idle for a few minutes to reach a stable operating temperature. With the engine running, check the fuel pressure gauge. The reading should be within the recommended range specified for your vehicle. If the pressure is too low, it could indicate a restriction or leak in the system. Conversely, if the pressure is abnormally high, it might suggest a blockage or an issue with the fuel pump. Adjustments or further investigation may be required to resolve these issues.
Additionally, you can perform a visual inspection to ensure the fuel is flowing correctly. Check for any signs of fuel accumulation or pooling around the connection points. If you notice any fuel buildup, it could indicate a potential leak or a misaligned connection. Addressing these issues promptly is essential to prevent further complications.
Remember, proper testing and verification are critical to maintaining a safe and efficient fuel system. By following these steps, you can ensure that your double flare 3/8 fuel line connections are secure, leak-free, and functioning correctly.
Fuel Line Fix: Disconnecting the 1998 Jeep Wrangler's Connector
You may want to see also
Frequently asked questions
A double flare 3/8 fuel line is a type of fuel line used in automotive applications, typically for fuel injection systems. It is designed with a double flare connection at one end, which allows for a secure and leak-free attachment to fuel injectors or other fuel system components. The 3/8-inch diameter refers to the inside diameter of the fuel line, indicating its size and flow capacity.
Double flaring a 3/8 fuel line is a process that requires specific tools and techniques. Here's a general overview: First, ensure you have the necessary tools, including a fuel line cutter, a flaring tool, and a suitable solvent cleaner. Cut the fuel line to the desired length, then clean the ends thoroughly. Use the flaring tool to create a double flare on one end, following the manufacturer's instructions for the specific tool you are using. This process typically involves bending the fuel line material in two stages to create a tight, secure connection.
Yes, there are a few potential issues to consider. Firstly, ensure that the fuel line material is compatible with the fuel type and system pressure. Using the wrong material can lead to degradation or leaks over time. Secondly, proper flaring is crucial for a secure connection. If the flare is not tight enough, it may result in fuel leaks. Finally, check for any bends or kinks in the fuel line, as these can restrict fuel flow and cause engine performance issues.