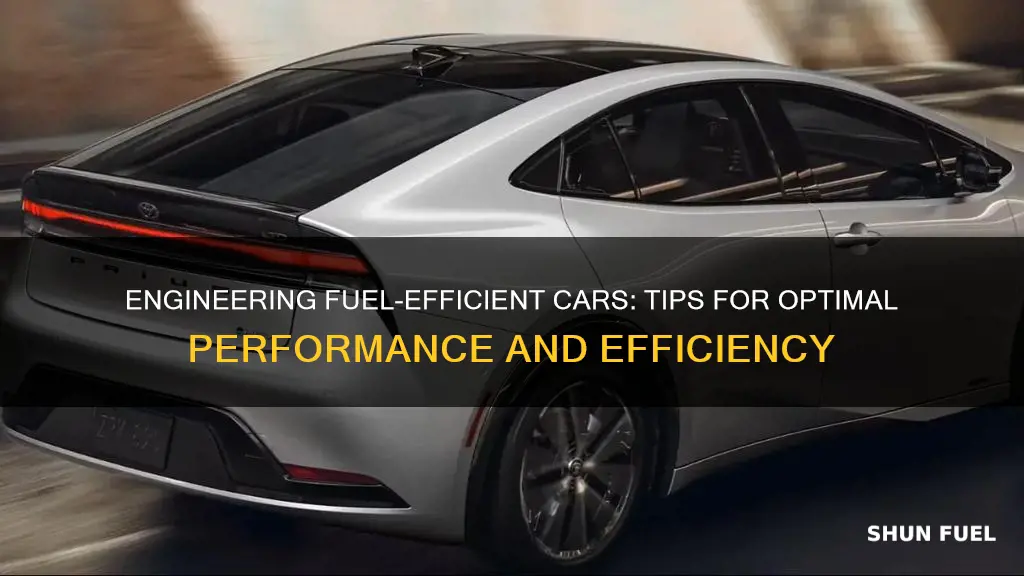
Designing a fuel-efficient car is a complex process that involves optimizing various aspects of vehicle engineering. It requires a deep understanding of aerodynamics, lightweight materials, efficient engines, and advanced technologies to minimize fuel consumption. The goal is to create a vehicle that offers excellent mileage, reduces emissions, and provides a comfortable driving experience. This involves meticulous planning and integration of different systems, from the engine's power output to the vehicle's overall design, to achieve the highest possible fuel efficiency without compromising performance and safety.
What You'll Learn
- Aerodynamics: Streamline body design to reduce drag and improve fuel efficiency
- Lightweight Materials: Utilize advanced materials to decrease vehicle weight without compromising safety
- Engine Optimization: Enhance engine performance to maximize power while minimizing fuel consumption
- Transmission Efficiency: Design efficient gear systems to optimize power transfer and fuel economy
- Hybrid/Electric Powertrains: Explore alternative powertrains to reduce reliance on traditional internal combustion engines
Aerodynamics: Streamline body design to reduce drag and improve fuel efficiency
Aerodynamics plays a crucial role in designing fuel-efficient cars, as it directly impacts the vehicle's performance and fuel consumption. The primary goal is to minimize drag, which is the force that opposes the motion of the car through the air. By streamlining the body design, engineers can significantly reduce this drag force, allowing the car to glide more smoothly and efficiently.
One key aspect of aerodynamic design is the shape and contour of the car's exterior. The vehicle's body should be designed with smooth, curved surfaces that follow the car's natural airflow. This means avoiding sharp edges and angles that create turbulence and increase drag. For instance, the roof should slope gently towards the rear, and the sides should have a graceful transition to the rear, reducing the formation of wake and turbulence.
The front end of the car is particularly important in aerodynamics. Designers should focus on creating a streamlined front fascia, which includes the grille, headlights, and air intakes. A well-designed front end should direct airflow efficiently, reducing the pressure difference between the front and rear of the car. This can be achieved by incorporating air ducts and vents strategically placed to manage airflow and minimize drag.
Additionally, the rear of the vehicle is critical to achieving optimal aerodynamics. The car's tail should be designed with a smooth, sloping roofline that extends to the rear, creating a fastback or coupe-like appearance. This design helps to reduce the wake and turbulence behind the car, improving stability and fuel efficiency. Furthermore, the inclusion of a spoiler or a small rear wing can aid in managing airflow, especially at higher speeds, by creating downforce and reducing lift.
Incorporating these aerodynamic principles into the car's design can lead to substantial fuel savings. By reducing drag, the vehicle requires less power to maintain speed, resulting in improved fuel efficiency. This not only benefits the environment by reducing emissions but also provides economic advantages for drivers, as they spend less on fuel over the lifetime of the vehicle.
Does Turning Your Car On While Pumping Fuel Save Gas?
You may want to see also
Lightweight Materials: Utilize advanced materials to decrease vehicle weight without compromising safety
The use of lightweight materials is a critical aspect of designing fuel-efficient cars, as it directly impacts the vehicle's overall weight and, consequently, its fuel consumption. By employing advanced materials, engineers can achieve a significant reduction in vehicle weight while maintaining or even enhancing safety standards. This approach is a cornerstone of modern automotive engineering, aiming to optimize performance and efficiency.
One of the primary materials that have revolutionized lightweight car design is carbon fiber-reinforced polymer (CFRP). Carbon fiber, known for its exceptional strength-to-weight ratio, is a composite material that can replace traditional steel or aluminum in various car components. For instance, the body panels, hood, and even the chassis can be crafted from CFRP, significantly reducing the vehicle's weight. This material's high strength allows for thinner, yet more rigid, structures, which not only reduces weight but also improves the overall structural integrity of the car.
Another innovative material is high-strength steel, which offers a balance between strength and weight. This type of steel is engineered to provide superior performance in terms of load-bearing capacity while being significantly lighter than conventional steel. By utilizing high-strength steel in critical areas such as the frame and body, designers can ensure the vehicle's structural integrity is maintained or even improved, despite the reduced weight. This material is particularly useful in safety-critical components, such as the crumple zones, where energy absorption is essential during collisions.
Additionally, the development of advanced alloys has played a pivotal role in lightweight car design. These alloys, such as those based on magnesium or titanium, offer improved strength and corrosion resistance compared to traditional alloys. By incorporating these advanced alloys into engine components, transmission parts, and even wheels, manufacturers can achieve substantial weight savings without sacrificing performance or durability. The use of lightweight alloys also contributes to better fuel efficiency, as reduced weight translates to lower fuel consumption.
Furthermore, the integration of lightweight materials extends beyond the body and chassis. Interior components, such as seats, dashboards, and door panels, can be designed with lightweight materials like foam-filled polymers or woven fabrics. These materials provide comfort and functionality while contributing to the overall weight reduction of the vehicle. By carefully selecting and optimizing materials across the entire vehicle, engineers can achieve a harmonious balance between weight reduction and safety.
In summary, the utilization of advanced lightweight materials is a key strategy in the pursuit of fuel-efficient cars. Through the application of carbon fiber, high-strength steel, advanced alloys, and innovative polymers, engineers can significantly decrease vehicle weight without compromising safety. This approach not only contributes to better fuel efficiency but also enhances the overall performance and driving experience, making it an essential aspect of modern automotive design.
Keep Your Ride Clean: The Ultimate Guide to Fuel Tank Maintenance
You may want to see also
Engine Optimization: Enhance engine performance to maximize power while minimizing fuel consumption
Engine optimization is a critical aspect of designing fuel-efficient vehicles, aiming to strike a balance between power generation and fuel economy. One key strategy is to focus on improving the engine's thermal efficiency, which directly impacts fuel consumption. This involves optimizing the combustion process to ensure that a higher percentage of the fuel's energy is converted into useful work, thereby reducing the amount of fuel required to achieve the same power output.
A common approach to engine optimization is the use of advanced combustion technologies. This includes implementing direct fuel injection systems, which precisely control the fuel-air mixture, allowing for more efficient combustion. By optimizing the fuel injection timing and spray angle, engines can achieve leaner burn rates, reducing the amount of fuel needed and improving overall efficiency. Additionally, the use of advanced ignition systems, such as spark plugs with improved heat range and durability, can enhance combustion quality, leading to better fuel economy.
Another important consideration is the engine's mechanical design. Streamlining the engine's internal components, such as the cylinder head and piston design, can reduce friction and improve overall efficiency. This includes using lightweight materials for pistons and connecting rods, optimizing the engine's layout to minimize parasitic losses, and implementing advanced lubrication systems to reduce wear and friction. By minimizing these losses, the engine can operate more efficiently, resulting in better fuel economy.
Engine optimization also involves the use of advanced materials and manufacturing processes. For instance, employing lightweight alloys for engine components can reduce the overall weight of the vehicle, leading to improved fuel efficiency. Additionally, utilizing advanced manufacturing techniques, such as 3D printing, can enable the production of complex engine parts with optimized geometries, further enhancing performance and fuel economy.
Furthermore, the integration of electronic control units (ECUs) plays a vital role in engine optimization. These ECUs can monitor and adjust engine parameters in real-time, ensuring optimal performance under various driving conditions. By continuously learning and adapting to the vehicle's behavior, the ECU can fine-tune fuel injection, ignition timing, and other critical parameters, resulting in improved power output and fuel efficiency. This level of control allows for a more dynamic and responsive engine, contributing to the overall fuel-efficiency goals of the vehicle design.
Top Fuel Funny Car: Weighty Secrets Unveiled
You may want to see also
Transmission Efficiency: Design efficient gear systems to optimize power transfer and fuel economy
Transmission efficiency is a critical aspect of designing fuel-efficient vehicles, as it directly impacts how effectively the engine's power is transferred to the wheels. The goal is to minimize energy losses during gear changes and optimize power transfer, which can significantly improve fuel economy. Here's a detailed approach to achieving this:
Gear Ratio Optimization: The first step is to carefully select gear ratios for each gear in the transmission. Gear ratios determine the speed and torque relationship between the engine and the wheels. By choosing optimal ratios, engineers can ensure that the engine operates at its most efficient speed range for a given vehicle speed. For example, a lower gear ratio can provide better acceleration and torque, while a higher ratio can improve fuel efficiency at higher speeds. Advanced computer simulations and modeling techniques are often employed to analyze various gear ratios and their impact on overall vehicle performance.
Smooth Power Transfer: Efficient power transfer is essential to minimize energy losses. This can be achieved by designing gear systems that provide smooth and seamless transitions between gears. One approach is to use advanced transmission control systems that adjust gear shifts based on driving conditions and driver input. For instance, some transmissions can anticipate the driver's needs and shift gears proactively, ensuring that the engine speed remains within the optimal range for fuel efficiency. This technology often involves sensors, actuators, and sophisticated control algorithms to manage the complex gear changes.
Variable Transmission Systems: Developing variable transmission systems, such as continuously variable transmissions (CVTs), can offer significant advantages in terms of transmission efficiency. CVTs provide an infinite number of gear ratios, allowing for seamless and continuous power transfer. This design enables the engine to operate at its most efficient speed for any given vehicle speed, resulting in improved fuel economy. CVTs are particularly useful in urban driving conditions where frequent stop-and-go driving is common, as they can provide quick and smooth gear changes without the traditional 'gear shift' feel.
Material and Construction Considerations: The choice of materials and construction techniques also plays a vital role in transmission efficiency. Modern transmissions often utilize lightweight materials like advanced alloys and composites to reduce overall weight. Lighter transmissions contribute to better fuel economy by reducing the vehicle's overall mass, especially in hybrid and electric vehicles where weight is a critical factor. Additionally, optimizing the manufacturing process to ensure precise gear alignment and smooth operation can minimize friction and energy losses.
Regenerative Braking Integration: While primarily associated with drivetrain efficiency, regenerative braking systems can also impact transmission design. By capturing and reusing kinetic energy during braking, these systems can reduce the load on the engine and improve overall fuel efficiency. Transmission designs can be optimized to work in conjunction with regenerative braking, ensuring smooth power transfer and efficient energy recovery during deceleration.
Air-Fuel Ratio: Do You Need a Gauge in Your Car?
You may want to see also
Hybrid/Electric Powertrains: Explore alternative powertrains to reduce reliance on traditional internal combustion engines
The automotive industry is undergoing a transformative shift towards more sustainable and environmentally friendly vehicles, and a key focus is on developing hybrid and electric powertrains to reduce the dependence on conventional internal combustion engines (ICEs). This shift is driven by the urgent need to combat climate change and reduce the environmental impact of the transportation sector. Hybrid and electric powertrains offer a promising solution by combining the benefits of traditional combustion engines with the efficiency and cleanliness of electric motors.
One of the primary advantages of hybrid and electric powertrains is their ability to significantly improve fuel efficiency. Hybrid vehicles, such as the widely recognized Toyota Prius, utilize a combination of a small ICE and one or more electric motors. The electric motor provides additional power during acceleration and can also act as a generator, recharging the battery while the vehicle is decelerating or idling. This dual-power system allows hybrids to achieve impressive fuel economy, often surpassing that of conventional vehicles. By reducing the reliance on the ICE for everyday driving, hybrids minimize fuel consumption and emissions, making them an attractive choice for environmentally conscious consumers.
Electric vehicles (EVs) take this concept further by eliminating the ICE entirely. EVs are powered solely by electric motors, which are driven by electricity stored in advanced batteries. This design offers several advantages, including instant torque delivery, smooth acceleration, and reduced noise levels. Moreover, EVs produce zero tailpipe emissions, making them a clean and sustainable transportation option. As battery technology advances, the range of EVs continues to increase, addressing the range anxiety associated with early electric vehicles. Governments and automotive manufacturers worldwide are investing in EV infrastructure, including charging stations, to support the widespread adoption of electric powertrains.
The development of hybrid and electric powertrains also opens up opportunities for innovative vehicle designs. These alternative powertrains can be integrated into various vehicle types, from compact city cars to luxury SUVs. For instance, plug-in hybrid electric vehicles (PHEVs) offer the flexibility of an ICE for long-distance travel while providing electric-only driving for shorter commutes. This versatility allows manufacturers to cater to diverse consumer preferences and market demands. Additionally, the use of electric powertrains enables the optimization of vehicle aerodynamics and lightweight materials, further enhancing overall efficiency.
In summary, hybrid and electric powertrains represent a significant advancement in the quest for fuel-efficient and environmentally friendly automobiles. By reducing the reliance on traditional ICEs, these alternative powertrains offer improved fuel economy, lower emissions, and a more sustainable approach to transportation. As technology continues to evolve, the automotive industry is embracing these innovations, paving the way for a greener and more efficient future on the roads. This transition is crucial in the fight against climate change and the pursuit of a more sustainable global transportation system.
Fuel Injection: Do These Cars Still Need a Distributor Cap?
You may want to see also
Frequently asked questions
When designing a fuel-efficient vehicle, several critical factors come into play. Firstly, engine efficiency is paramount; this includes optimizing the combustion process, using advanced materials, and implementing technologies like direct fuel injection. Secondly, aerodynamic design plays a significant role; streamlining the car's body reduces drag, allowing for better fuel economy. Lightweight materials, such as carbon fiber or advanced alloys, can also contribute to improved efficiency by reducing the overall weight of the vehicle. Additionally, the transmission and drivetrain should be designed for optimal power delivery and efficiency, ensuring smooth acceleration and efficient energy transfer.
Material selection is crucial in achieving fuel efficiency. Traditional steel is heavy, but modern alternatives like high-strength steel, aluminum alloys, and carbon fiber composites offer significant weight reduction. Lighter materials reduce the car's overall mass, leading to improved fuel economy. For instance, carbon fiber, despite being expensive, provides exceptional strength-to-weight ratios, making it an attractive choice for high-performance, fuel-efficient vehicles. Additionally, the use of advanced polymers and composites in various car components can further enhance efficiency by minimizing weight without compromising structural integrity.
Yes, engine downsizing, often combined with turbocharging or hybrid technology, is a proven strategy for enhancing fuel efficiency. Smaller engines with higher power-to-weight ratios can deliver excellent performance while consuming less fuel. Turbochargers provide the necessary boost to smaller displacement engines, ensuring they can match or exceed the power output of larger, naturally aspirated engines. Hybrid systems, which integrate an electric motor with a smaller gasoline or diesel engine, further optimize fuel efficiency by utilizing regenerative braking and intelligent energy management. This approach not only reduces fuel consumption but also contributes to lower emissions.
Tire technology is an often-overlooked aspect of fuel efficiency. Low-rolling-resistance tires, designed to minimize energy loss during contact with the road, can significantly improve fuel economy. These tires are constructed with advanced materials and designs that reduce friction, allowing for smoother rolling and less energy dissipation as heat. Additionally, maintaining proper tire pressure is essential. Underinflated tires create more rolling resistance, forcing the engine to work harder and consume more fuel. Regularly checking and adjusting tire pressure can lead to noticeable improvements in fuel efficiency and overall vehicle performance.