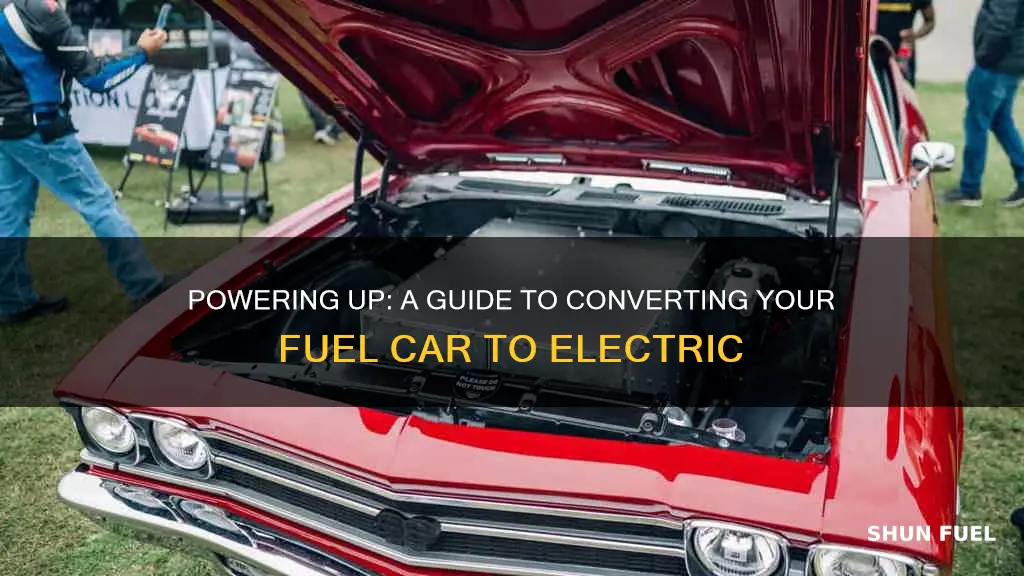
Converting a fuel car to an electric vehicle is an exciting and sustainable project that can significantly reduce environmental impact. This process involves replacing the internal combustion engine with an electric motor and a battery pack, which can be a complex but rewarding endeavor. It requires careful planning, technical expertise, and a deep understanding of automotive systems. The conversion process typically includes retrofitting the vehicle's electrical system, managing power distribution, and ensuring the car's performance and safety meet or exceed the original specifications. This guide will provide an overview of the key steps and considerations for successfully converting a fuel car to an electric, offering valuable insights for enthusiasts and environmental advocates alike.
What You'll Learn
- Battery Selection: Choose suitable batteries for power and range
- Motor Installation: Install electric motors and drivetrain components
- Charging Systems: Design and integrate charging ports and infrastructure
- Power Electronics: Utilize converters and inverters for efficient energy transfer
- Safety Measures: Implement safety protocols for electrical systems
Battery Selection: Choose suitable batteries for power and range
When converting a fuel car to electric, one of the most critical decisions is selecting the right batteries to power your vehicle. The battery pack is the heart of your electric car, providing the energy needed to drive and determine the car's overall performance and range. Here's a detailed guide on how to choose suitable batteries for power and range:
Understand Your Requirements: Begin by assessing your specific needs. Consider the car's original fuel consumption, the desired range for your electric vehicle, and the typical driving conditions. For instance, if you plan to drive long distances regularly, you'll need a battery pack with a higher energy density and capacity. Understanding your requirements will help narrow down the battery options.
Battery Chemistry: There are various types of batteries available, each with its own advantages and disadvantages. The most common choices for electric vehicles are lithium-ion batteries due to their high energy density, lightweight, and relatively low self-discharge rate. However, other chemistries like lead-acid or nickel-metal hydride (NiMH) can also be considered, especially for cost-effective solutions. Research the pros and cons of each chemistry to find the best fit for your project.
Energy Density and Capacity: Energy density is a critical factor, measured in watt-hours per kilogram (Wh/kg). Higher energy density means more energy can be stored in a smaller and lighter package, allowing for improved range. For example, lithium-ion batteries typically offer higher energy densities than lead-acid batteries. Calculate the required energy capacity based on your driving needs and choose batteries that meet or exceed this value.
Voltage and Current Rating: Each battery type has specific voltage and current ratings. Ensure that the batteries you select match or exceed the voltage and current requirements of your electric car's motor and charging system. Mismatched ratings can lead to inefficiencies or even damage to the vehicle's components.
Safety and Temperature Considerations: Electric vehicle batteries should be chosen with safety in mind. Look for batteries with built-in safety mechanisms, such as over-voltage and over-current protection. Additionally, consider the operating temperature range of the batteries. If your vehicle will be used in extreme climates, ensure the batteries can handle those conditions without compromising performance or safety.
Packaging and Installation: The physical packaging of the batteries is essential for a successful installation. Ensure the batteries are designed to fit your car's battery compartment and can be easily integrated into the vehicle's electrical system. Consider the weight distribution and any modifications required to accommodate the new battery pack.
By carefully considering these factors, you can select the most suitable batteries for your electric car conversion project, ensuring optimal power delivery and an impressive range. Remember, the right battery choice is fundamental to the success and efficiency of your electric vehicle.
Fuel Injector Issues: Why Your Car Won't Start
You may want to see also
Motor Installation: Install electric motors and drivetrain components
The installation of electric motors and drivetrain components is a crucial step in converting a fuel car to an electric vehicle. This process involves replacing the internal combustion engine with an electric motor and setting up the necessary drivetrain to transfer power from the motor to the wheels. Here's a detailed guide on how to approach this installation:
Motor Selection and Preparation: Begin by choosing an electric motor suitable for your vehicle's requirements. Consider factors such as power output, torque, and size. Ensure the motor's specifications align with the desired performance and range of your electric car. Once you have the motor, inspect it for any signs of damage or wear. Clean and lubricate the motor's components as per the manufacturer's guidelines to ensure optimal performance.
Drivetrain Assembly: Disassemble the original drivetrain, including the transmission, driveshaft, and differential, if applicable. Clean and inspect these components to ensure they are in good condition. You may need to replace or repair any worn-out parts. Then, assemble the new electric drivetrain, starting with the motor mount. Secure the motor to the vehicle's chassis using the provided mounting hardware. Connect the motor's output shaft to the input shaft of the transmission or directly to the driveshaft, depending on your vehicle's design. Ensure all connections are tight and properly aligned.
Wiring and Control Systems: Electric motors require a sophisticated wiring harness to connect them to the power source and control units. Route the wires through the vehicle's frame and secure them using appropriate insulation and protective covers. Connect the motor's power supply to the battery, ensuring the correct polarity. Install the motor control unit (MCU) or inverter, which regulates the motor's speed and torque. Wire the MCU to the motor, battery, and other vehicle sensors to enable precise control and monitoring.
Testing and Calibration: After the motor and drivetrain installation, conduct thorough testing. Start the vehicle and check for any unusual noises or vibrations. Monitor the motor's performance, including speed, torque, and temperature. Use diagnostic tools to ensure the motor, inverter, and control systems are functioning correctly. Calibrate the motor control unit to optimize performance and efficiency. This may involve adjusting parameters such as voltage, frequency, and torque curve.
Final Adjustments and Safety Checks: Once the motor and drivetrain are installed and tested, perform final adjustments to ensure smooth operation. Fine-tune the vehicle's performance by adjusting the motor control settings, suspension, and braking systems. Conduct a comprehensive safety inspection, checking all electrical connections, fuses, and grounding points. Ensure the vehicle meets the required safety standards and regulations for electric vehicles.
Unveiling the Mystery: How Car Fuel Tank Covers Protect Your Ride
You may want to see also
Charging Systems: Design and integrate charging ports and infrastructure
When converting a fuel car to electric, the design and integration of charging systems are critical components that require careful planning and consideration. The goal is to ensure efficient and safe charging capabilities while seamlessly integrating the charging ports and infrastructure into the vehicle's design. Here's an overview of the process:
Charging Port Design: The first step is to select the appropriate charging port(s) for your electric vehicle conversion. Common charging port types include the CHAdeMO, CCS (Combined Charging System), and Tesla's proprietary connector. Each port has its own specifications and power handling capabilities. For instance, CHAdeMO ports are typically used for rapid charging, while CCS ports offer both direct current (DC) and alternating current (AC) charging options. The chosen port(s) should align with industry standards and the vehicle's charging requirements. Consider factors such as port size, location on the vehicle, and the type of charging cable needed.
Infrastructure Planning: Designing the charging infrastructure involves determining the power supply and wiring configuration. You'll need to install a suitable power source, often a wall-mounted charger or a dedicated charging station, depending on the charging speed and power requirements. The electrical system must be designed to handle the increased power draw of electric motors, so proper sizing of wiring, fuses, and circuit breakers is essential. Ensure that the charging infrastructure complies with local electrical codes and regulations to guarantee safety.
Integration and Placement: The placement of charging ports is crucial for user convenience and aesthetics. Consider the vehicle's design and the driver's natural reach. Typically, charging ports are located on the front or rear of the vehicle, allowing for easy access during parking. The ports should be positioned to avoid interference with other vehicle components and provide a clear view for the driver. Proper integration ensures that the charging ports blend seamlessly with the overall vehicle design, enhancing the electric car's visual appeal.
Communication and Control: Modern electric vehicles often incorporate communication systems that allow for smart charging and monitoring. Design the charging system to include communication protocols, such as CAN bus or Ethernet, to enable data exchange between the charging port, vehicle control unit, and potentially a central charging station. This enables features like remote monitoring, charging schedule management, and over-the-air updates. Advanced charging systems may also include features like pre-conditioning, where the vehicle's heating or cooling system can be activated during charging to optimize performance and comfort.
Safety Considerations: Safety is paramount in the design and integration of charging systems. Implement measures to prevent electrical hazards, such as grounding systems, circuit protection, and overcurrent protection. Consider adding safety features like residual current devices (RCDs) to protect against electric shocks. Additionally, ensure that the charging system meets or exceeds industry safety standards and regulations, including those related to fire prevention and thermal management.
By carefully designing and integrating charging ports and infrastructure, you can create a seamless and efficient charging experience for electric vehicle owners, contributing to the widespread adoption of electric mobility.
Petrol Cars: Uncovering the Mystery of Fuel Filters
You may want to see also
Power Electronics: Utilize converters and inverters for efficient energy transfer
Power electronics play a crucial role in the conversion of traditional fuel-based vehicles to electric powertrains. The primary goal is to ensure efficient energy transfer and management, which is essential for the overall performance and range of an electric vehicle (EV). Converters and inverters are key components in this process, enabling the conversion of electrical energy from the battery to the motor and vice versa.
In the context of EV conversion, converters are used to regulate the voltage and current levels, ensuring that the electrical system operates optimally. These converters can be of various types, including DC-DC converters, which are commonly employed to step down the high-voltage output of the battery pack to a level suitable for the motor. This step-down process is vital to match the voltage requirements of the electric motor, allowing for efficient power transfer.
Inverters, on the other hand, are responsible for converting the direct current (DC) from the battery into alternating current (AC) that the electric motor needs to operate. This conversion is critical as it enables the motor to run at varying speeds and provide the necessary torque for acceleration and driving. Modern inverters can also include sophisticated control algorithms to optimize performance, ensuring that the motor receives the right amount of power at the right time.
The efficiency of these power electronics components is paramount for several reasons. Firstly, it directly impacts the overall efficiency of the EV, ensuring that energy is not wasted during the conversion process. Secondly, efficient energy transfer contributes to longer battery life, as excessive heat generation and power losses can degrade the battery's performance over time. Lastly, optimizing power electronics can lead to improved range, allowing EVs to travel further on a single charge, which is a significant advantage over their fuel-based counterparts.
When converting a fuel car to electric, it is essential to carefully select and design the power electronics system. This includes considering the specific requirements of the vehicle, such as its weight, intended use, and desired range. Engineers and technicians must also ensure that the converters and inverters are compatible with the battery pack and motor, as well as the vehicle's electrical architecture. Proper sizing and selection of these components will result in a well-balanced and efficient electric vehicle conversion.
Mastering Idle Control: Adjusting Fuel Injection for Optimal Performance
You may want to see also
Safety Measures: Implement safety protocols for electrical systems
When converting a fuel car to electric, implementing robust safety protocols for the electrical systems is paramount to ensure the vehicle's reliability and the safety of its occupants. Here are some critical safety measures to consider:
- Electrical System Design and Layout: Begin by carefully planning the electrical layout of the vehicle. This involves determining the placement of batteries, wiring harnesses, and electrical components to minimize potential hazards. Keep the electrical system organized and well-structured to facilitate easy maintenance and troubleshooting. Ensure that all wiring is properly insulated and protected to prevent short circuits and fire risks. Consider using high-temperature-rated insulation and protective sleeves, especially in areas prone to heat generation or mechanical stress.
- Battery Management and Protection: The electric car's heart is its battery pack, so implementing advanced battery management systems is essential. These systems should monitor and control various parameters, including voltage, current, temperature, and state of charge. Set up safety mechanisms such as over-voltage and under-voltage protection, over-current and short-circuit protection, and temperature monitoring to prevent battery damage and potential hazards. Consider using battery management systems that offer cell balancing to maintain optimal performance and extend the battery's lifespan.
- Grounding and Bonding: Proper grounding and bonding techniques are critical to electrical safety. Ensure that all electrical components and systems are properly grounded to provide a safe path for electrical currents. Use high-quality grounding straps and connections to minimize resistance and potential hazards. Regularly inspect and maintain the grounding system to ensure its effectiveness.
- Electrical Insulation and Protection: Implement comprehensive insulation measures to safeguard against electrical hazards. Use insulated materials for wiring, terminals, and connectors to prevent accidental contact with live electrical parts. Apply protective coatings or sleeves to wires and components exposed to the elements or potential damage. Consider using waterproof and weather-resistant insulation for outdoor electrical connections.
- Regular Maintenance and Inspections: Establish a comprehensive maintenance schedule for the electric vehicle's electrical systems. This includes routine inspections to identify and address potential issues promptly. Check for signs of damage, corrosion, or loose connections during inspections. Keep detailed records of maintenance activities and any identified issues to ensure a well-maintained and safe vehicle.
- Emergency Shutdown and Fault Detection: Implement advanced fault detection systems that can identify and respond to electrical malfunctions. These systems should trigger an emergency shutdown or warning signal in case of critical failures. Ensure that the vehicle has a reliable and accessible power-off mechanism to prevent further damage and potential risks.
By adhering to these safety measures, you can significantly reduce the risks associated with converting a fuel car to electric, ensuring a safer and more reliable electric vehicle. It is crucial to stay updated with the latest industry standards and regulations to maintain compliance and provide a secure driving experience.
Summer Car Care: 2-Stroke Fuel Tips for a Smooth Ride
You may want to see also
Frequently asked questions
Converting a traditional internal combustion engine (ICE) vehicle to electric offers several advantages. Firstly, it significantly reduces environmental impact by eliminating tailpipe emissions, contributing to cleaner air and a smaller carbon footprint. Electric vehicles (EVs) are also known for their high energy efficiency, resulting in lower operating costs compared to gasoline or diesel cars. Additionally, EVs provide a smooth and quiet driving experience due to their instant torque delivery, and they often have lower maintenance requirements as they have fewer moving parts.
Yes, it is possible to convert most fuel-based cars to electric vehicles. However, the process can vary depending on the make and model of the vehicle. Some cars may require more modifications to accommodate the electric drivetrain, especially if the original design was not intended for an electric conversion. It's essential to consider factors like the car's battery capacity, motor power, and the availability of suitable components for the conversion. Consulting with experienced professionals or engineers who specialize in EV conversions can help determine the feasibility and potential challenges for a specific vehicle.
The conversion of a fuel car to electric typically involves several critical components. These include a high-capacity electric battery pack, an electric motor or motors to replace the ICE, a power electronics system to control energy flow, and a charging system for replenishing the battery. Additionally, modifications to the vehicle's wiring, cooling system, and suspension may be necessary to accommodate the new electric drivetrain. The process often requires skilled technicians to ensure proper installation and integration of these components.
The cost of converting a fuel car to electric can vary widely depending on various factors. These factors include the make and model of the vehicle, the complexity of the conversion, the choice of components, and labor costs. On average, a basic conversion can range from $5,000 to $15,000, while more advanced or high-performance conversions might cost upwards of $30,000. It's advisable to obtain quotes from multiple conversion specialists to get a more accurate estimate based on your specific vehicle and requirements.