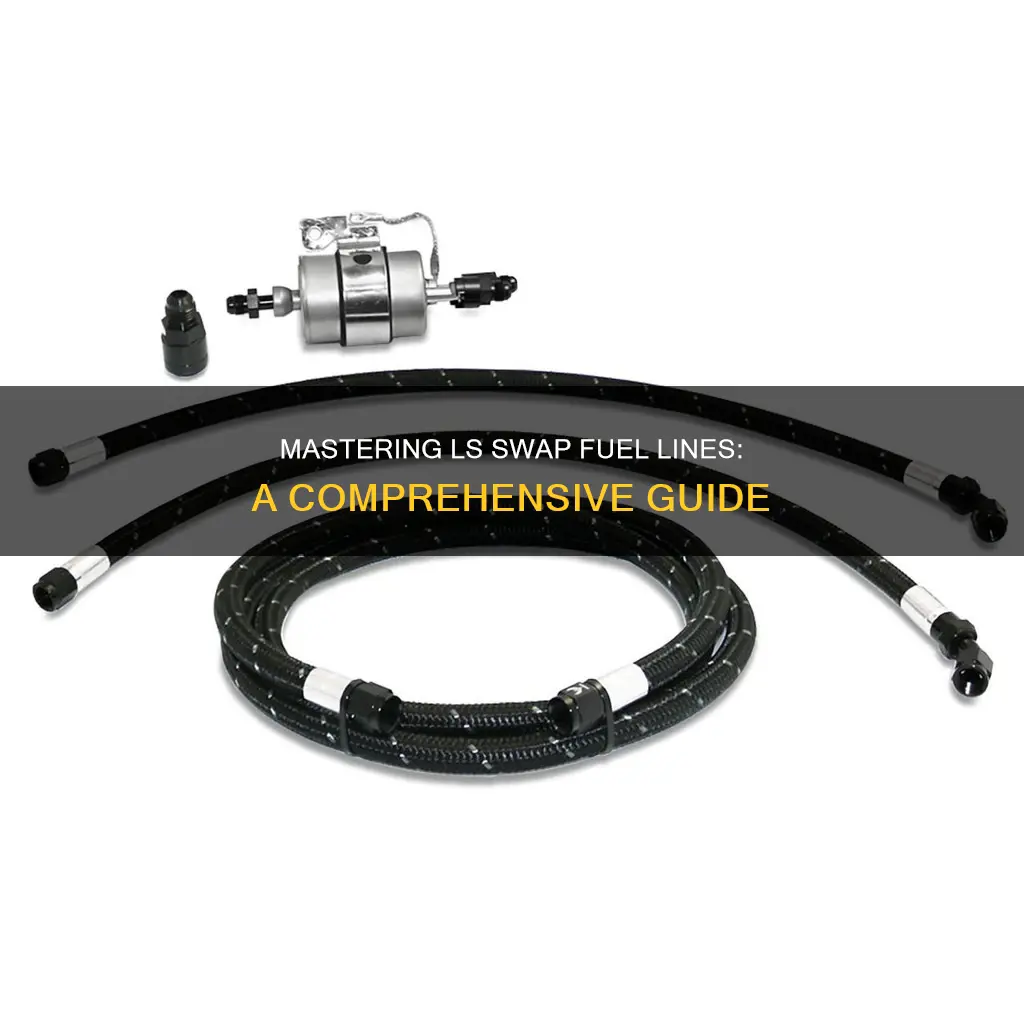
Building fuel lines for an LS swap is a crucial step in engine modifications, ensuring optimal performance and reliability. This process involves careful planning and execution to match the fuel system to the new engine's requirements. The LS swap, a popular engine swap in automotive enthusiasts, requires a well-designed fuel line system to handle the increased power and efficiency. This guide will provide a comprehensive overview of the steps involved in creating a robust fuel line setup, covering materials, routing, and installation techniques to ensure a seamless integration for maximum performance.
What You'll Learn
- Materials Selection: Choose appropriate tubing, fittings, and fuel injectors for LS swap
- Routing and Support: Plan fuel line path, ensuring it's secure and away from heat sources
- Fuel Pump Placement: Install the fuel pump close to the engine for optimal performance
- Fuel Filter and Pump: Use a high-flow filter and pump to prevent pressure drops
- Testing and Adjustments: Test fuel pressure and flow, making adjustments for optimal performance
Materials Selection: Choose appropriate tubing, fittings, and fuel injectors for LS swap
When it comes to building fuel lines for an LS swap, material selection is crucial to ensure optimal performance and longevity. Here's a detailed guide on choosing the right components:
Tubing: The primary component of your fuel lines is the tubing, which should be made from high-quality materials like 304 stainless steel or aluminum. Stainless steel is renowned for its corrosion resistance, making it ideal for fuel systems as it can withstand the corrosive nature of gasoline. It's also flexible and durable, ensuring it can handle the rigors of an LS engine swap. Alternatively, aluminum tubing offers a lightweight solution, reducing overall system weight. However, it requires careful consideration due to its lower corrosion resistance compared to stainless steel. For optimal performance, choose tubing with a smooth inner surface to minimize fuel flow restrictions.
Fittings: Fittings are essential for connecting the tubing and ensuring a secure and leak-free system. Brass or stainless steel fittings are commonly used. Brass provides a cost-effective option with good corrosion resistance, while stainless steel offers superior durability and longevity. When selecting fittings, ensure they are compatible with the chosen tubing material and have a tight seal to prevent fuel leaks. Consider the size and type of fittings required for your specific LS swap, as different engine configurations may demand unique fitting configurations.
Fuel Injectors: Upgrading to high-flow fuel injectors is often a crucial part of an LS swap. These injectors provide increased fuel capacity and precision, allowing for better engine performance and responsiveness. When selecting injectors, consider the flow rate and spray pattern to match the engine's requirements. Higher-flow injectors might be necessary for powerful LS engines to ensure efficient fuel delivery. Additionally, ensure the injectors are compatible with your fuel pump and have the necessary electrical connections for seamless integration into the engine's management system.
In summary, for a successful LS swap fuel system, focus on using high-quality materials like stainless steel or aluminum for tubing, choose corrosion-resistant brass or stainless steel fittings, and select high-flow fuel injectors tailored to the engine's needs. This meticulous material selection will contribute to a reliable and high-performance fuel system.
Mastering Fuel Line Connections: A Guide to Secure Fittings
You may want to see also
Routing and Support: Plan fuel line path, ensuring it's secure and away from heat sources
When building fuel lines for an LS swap, proper routing and support are crucial to ensure the system's reliability and longevity. The fuel lines should be carefully planned to avoid any potential issues, such as heat damage or interference with other components. Here's a detailed guide on how to approach this aspect of the project:
Planning the Route: Begin by visualizing the engine bay and identifying the optimal path for the fuel lines. The goal is to keep the lines as straight and direct as possible while maintaining a safe distance from heat-generating components. Consider the layout of the engine, the position of the LS engine, and the existing plumbing in the vehicle. Measure and mark the desired route on the engine bay, ensuring it doesn't interfere with other parts or the vehicle's structure.
Securing the Lines: Once the route is planned, it's essential to secure the fuel lines to prevent movement and potential damage. Use appropriate tie-downs or brackets to attach the lines to the engine bay, fender wells, or any sturdy surfaces. Ensure that the ties are tight and secure to withstand the vibrations and forces experienced during driving. Consider using heat shields or protective sleeves to shield the fuel lines from direct contact with hot engine components, exhaust systems, or other heat sources.
Avoiding Heat Sources: One of the critical aspects of routing fuel lines is keeping them away from heat sources. The LS engine, especially when equipped with a high-performance exhaust system, generates significant heat. Direct exposure to this heat can cause the fuel lines to degrade over time. Route the lines away from the exhaust manifold, headers, and any other hot components. If necessary, use heat-resistant materials or insulators to protect the fuel lines.
Flexibility and Slack: Allow for some flexibility in the fuel line routing to accommodate engine movement and potential vibrations. This flexibility can be achieved by using appropriate bends and allowing for a slight amount of slack in the lines. However, be cautious not to create excessive bends or kinks, as this can restrict fuel flow and cause pressure drops. Aim for a balanced approach, ensuring both flexibility and structural integrity.
Testing and Inspection: After completing the fuel line installation, thoroughly test the system to ensure proper fuel flow and pressure. Check for any leaks or restrictions in the lines. Inspect the routing and support system to confirm that it can withstand the rigors of the vehicle's operation. Regularly maintain and inspect the fuel lines to identify any signs of wear or damage, especially in areas where they are exposed to heat or mechanical stress.
By carefully planning the route, securing the fuel lines, and avoiding heat sources, you can create a robust and reliable fuel system for your LS swap project. This attention to detail will contribute to the overall performance and longevity of your vehicle's fuel delivery system.
Mastering Fuel Line Maintenance: A Guide to Using Fuel Line Cleaner
You may want to see also
Fuel Pump Placement: Install the fuel pump close to the engine for optimal performance
When performing an LS swap, one of the critical aspects to consider is the placement of the fuel pump. The fuel pump's location significantly impacts the engine's performance and overall reliability. By installing the fuel pump closer to the engine, you can optimize the fuel delivery system and ensure a more efficient and powerful engine operation.
The primary advantage of placing the fuel pump near the engine is the reduction of pressure drop. In a typical fuel system, the pump creates pressure to send fuel through the lines to the injectors or carburetor. When the pump is located far from the engine, the fuel has to travel a longer distance, resulting in a loss of pressure and reduced fuel flow. By bringing the pump closer to the engine, you minimize this pressure drop, allowing for a more consistent and robust fuel supply. This is especially crucial for high-performance applications where fuel demand is high, and maintaining optimal pressure is essential for efficient combustion.
Additionally, a closer fuel pump placement simplifies the routing of fuel lines. With the pump nearby, you can design the fuel lines to be shorter and more direct, reducing the risk of fuel pressure loss due to line restrictions or bends. This also makes the installation process more manageable, as you won't need to route fuel lines over long distances, potentially causing unnecessary complications.
Optimal fuel pump placement also contributes to better engine response and overall drivability. A fuel pump positioned closer to the engine can provide a more immediate and responsive fuel supply, resulting in quicker engine starts and improved throttle response. This is particularly beneficial for high-performance vehicles where quick acceleration and precise control are desired.
In summary, installing the fuel pump close to the engine during an LS swap is a crucial step to ensure optimal performance. It minimizes pressure drop, simplifies fuel line routing, and enhances engine response. By giving attention to this detail, you can create a robust and efficient fuel delivery system, ultimately contributing to a more powerful and reliable LS engine setup.
John Deere Fuel Line Size 72: What You Need to Know
You may want to see also
Fuel Filter and Pump: Use a high-flow filter and pump to prevent pressure drops
When performing an LS swap, ensuring a robust fuel system is crucial for optimal performance and reliability. One critical aspect often overlooked is the fuel filter and pump. Using a high-flow filter and pump can significantly improve the fuel system's efficiency and prevent pressure drops, which are common issues in modified engines.
A high-flow fuel filter is designed to handle the increased fuel volume and pressure that come with a powerful engine upgrade. It allows for a higher flow rate, ensuring that the engine receives the required fuel without any restrictions. This is particularly important when using larger fuel injectors or when the engine's power output has been significantly increased. By using a high-flow filter, you can maintain a consistent fuel pressure throughout the system, preventing any potential issues caused by pressure drops.
The fuel pump also plays a vital role in this setup. A high-flow pump is capable of delivering the increased fuel demand of the LS engine without straining. It ensures that the engine receives the necessary fuel volume at the required pressure, even during high-performance driving conditions. This is especially critical when the engine's power output has been enhanced, as it may require more fuel than the stock system can provide.
To install these components, you'll need to consider the specific requirements of your LS swap. Start by researching compatible high-flow filters and pumps that can handle the increased fuel flow. Proper placement of these components is essential; typically, the filter should be positioned close to the engine to minimize pressure loss, and the pump should be capable of delivering fuel to the engine's requirements.
In summary, when building fuel lines for an LS swap, prioritizing the fuel filter and pump is essential. High-flow filters and pumps ensure a consistent fuel supply, preventing pressure drops and maintaining optimal engine performance. By investing in these components, you can ensure that your LS engine receives the fuel it needs to operate efficiently and reliably, even under demanding conditions.
Mastering Fuel Line Maintenance: Quick Release Connector Removal Tips
You may want to see also
Testing and Adjustments: Test fuel pressure and flow, making adjustments for optimal performance
When it comes to building fuel lines for an LS swap, testing and adjustments are crucial to ensure optimal performance and reliability. After installing the new fuel lines, it's essential to verify that the fuel pressure and flow are within the desired range. Here's a step-by-step guide to help you with this process:
Fuel Pressure Testing: Start by locating the fuel pressure gauge, which is typically connected to the fuel rail. This gauge will provide real-time feedback on the fuel pressure. The ideal pressure range can vary depending on the engine and personal preferences, but a common target is around 60-70 psi (pounds per square inch). If the pressure is too low, it may result in poor fuel atomization and reduced power. On the other hand, excessive pressure can lead to fuel pump strain and potential issues. Adjust the fuel pressure regulator if necessary to fine-tune the pressure. This might involve turning the adjustment screw clockwise to increase pressure or counterclockwise to decrease it.
Flow Testing: To test fuel flow, you'll need a fuel flow meter or a method to measure the volume of fuel passing through the lines. Start the engine and allow it to idle. Monitor the fuel flow rate, which should be consistent and within the expected range for your engine configuration. If the flow is inconsistent or too low, it could indicate a restriction in the fuel lines or a faulty fuel pump. Check for any clogs or obstructions and ensure that the fuel filter is clean and free from debris. Consider replacing the filter if it appears worn out, as a restricted filter can impact fuel delivery.
Adjustments and Fine-Tuning: Based on your test results, make the necessary adjustments to optimize performance. If the fuel pressure is too low, try increasing the pressure regulator setting gradually until you reach the desired range. Similarly, if the flow is inadequate, check for any modifications or additions to the fuel lines that might be causing restrictions. Ensure that all connections are secure and free from leaks. Tighten any loose fittings and consider using fuel line protectors to prevent damage from heat or vibration.
Remember, the goal is to achieve a balanced fuel-air mixture for efficient combustion. Proper testing and adjustments will ensure that your LS swap engine receives the correct amount of fuel at the right pressure, resulting in improved performance and reliability. It's a critical step that requires attention to detail and a methodical approach to fine-tune your fuel system.
Fuel Line Removal: A Guide to Pump Disconnection on Ford Ranger A98
You may want to see also
Frequently asked questions
To begin the process, you'll require a fuel line kit specifically designed for your LS engine swap. This kit typically includes various sizes of fuel lines, fittings, clamps, and possibly a fuel filter. Essential tools include a fuel line cutter, a crimping tool for fittings, a fuel line brush for cleaning, and a fuel pressure gauge to ensure proper installation.
The fuel line sizes depend on the specific application and performance goals. Generally, larger fuel lines (e.g., 3/8" or 1/2") are preferred for high-performance LS swaps to handle increased fuel flow. Consider the distance between the fuel pump and the engine, as longer runs may require larger-diameter lines. Consult with experts or online resources for specific recommendations based on your engine's power output and desired performance.
Start by cleaning the fuel lines and removing any old fuel line gel or debris. Cut the lines to the desired length, ensuring a slight overlap for crimping. Use a fuel line brush to ensure a clean surface for the fittings. Crimp the fittings securely, following the manufacturer's instructions. Tighten the clamps firmly but avoid over-tightening, as it can restrict fuel flow. Test the system for leaks and ensure all connections are secure before finalizing the installation.