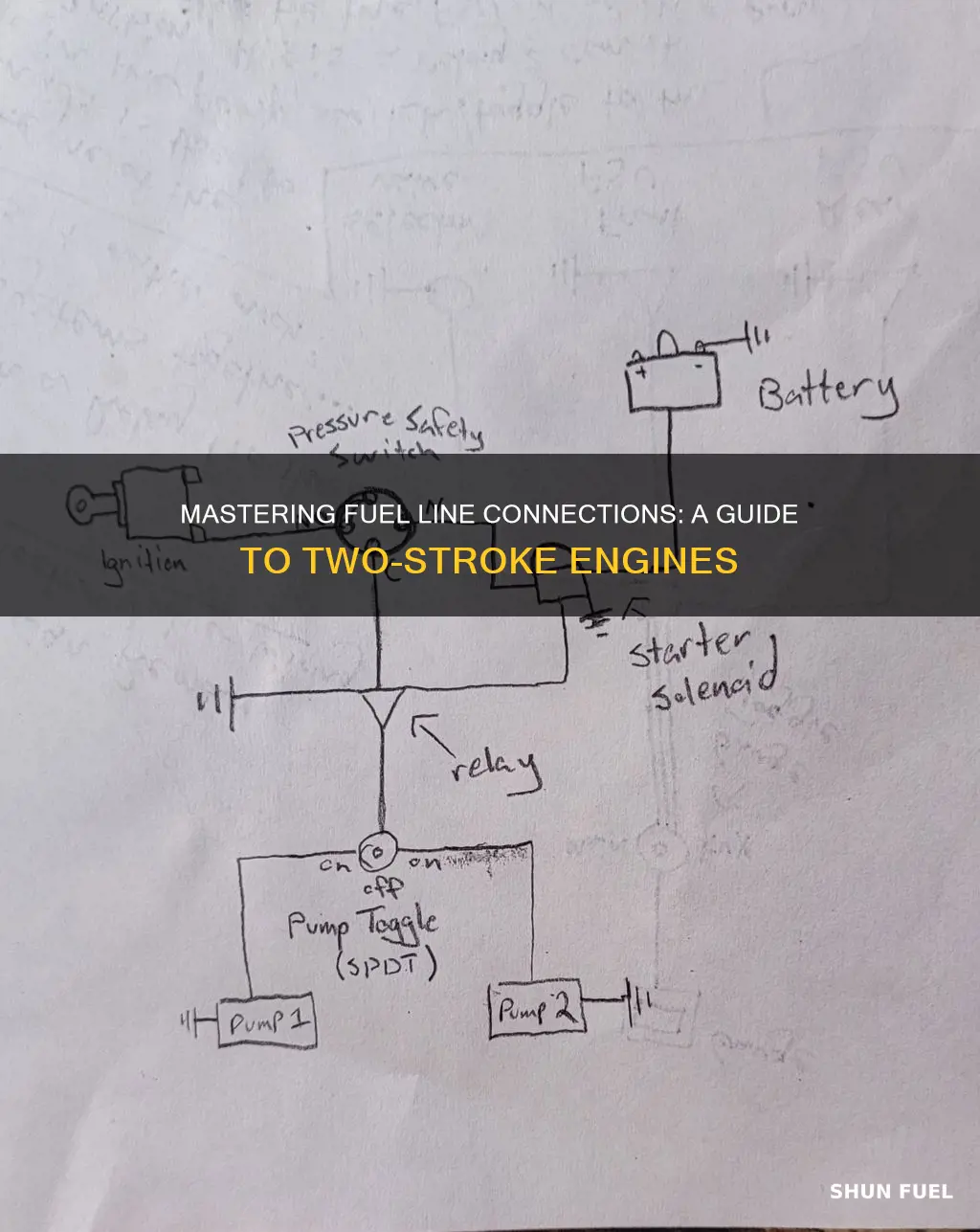
Connecting a fuel line to a two-stroke engine is a crucial step in ensuring the engine runs efficiently and reliably. This process involves routing the fuel line from the fuel tank to the carburetor, where it mixes with air and is drawn into the engine's cylinders. Proper installation is essential to prevent fuel leaks and ensure optimal performance. The fuel line must be securely attached to the carburetor and the fuel tank using appropriate fittings and clamps to maintain a tight seal. This guide will provide a step-by-step process for connecting the fuel line, ensuring a smooth and efficient fuel supply to the engine.
What You'll Learn
- Fuel Line Routing: Ensure proper placement to avoid damage and maintain optimal flow
- Fitting Selection: Choose fittings compatible with fuel line material and engine requirements
- Clamping Techniques: Secure fuel lines with appropriate clamps for a tight, leak-free connection
- Fuel Filter Installation: Position filters to prevent contaminants from entering the engine
- Testing for Leaks: Inspect connections and perform pressure tests to ensure no fuel leaks
Fuel Line Routing: Ensure proper placement to avoid damage and maintain optimal flow
When connecting a fuel line to a two-stroke engine, proper routing is crucial to ensure optimal performance and longevity of the engine. The fuel line serves as the pathway for the fuel-air mixture to reach the engine's combustion chamber, so any damage or restriction can lead to poor engine operation. Here's a detailed guide on how to ensure proper fuel line routing:
- Route Planning: Begin by carefully planning the path of the fuel line. It should be positioned to avoid any potential hazards or areas of high stress. For two-stroke engines, the fuel line often runs from the fuel tank, through the engine's cylinder head, and into the carburetor. Consider the engine's layout and any nearby components that could cause damage if the fuel line is not properly secured.
- Secure Mounting: Once the route is planned, secure the fuel line in place using appropriate mounting hardware. This can include rubber or plastic hoses, metal brackets, or clips. Ensure that the fuel line is taut and not allowed to sag or rub against any moving parts. Proper mounting prevents excessive movement, which could lead to damage over time.
- Avoid Heat Sources: Two-stroke engines generate a significant amount of heat, so it's essential to route the fuel line away from heat sources such as exhaust pipes, engine blocks, or other hot components. Prolonged exposure to high temperatures can cause the fuel line to degrade, leading to potential leaks or blockages. Consider using heat shields or insulation to protect the fuel line.
- Protect Against Vibration: Engine vibrations can cause fuel lines to loosen or damage over time. To mitigate this, use vibration-resistant mounting techniques. This might include rubber vibration dampeners or securing the fuel line to sturdy engine components that can absorb the vibrations. Proper vibration protection ensures the fuel line remains intact and maintains a consistent flow.
- Regular Inspection: After installation, regularly inspect the fuel line for any signs of damage, cracks, or leaks. Two-stroke engines can be demanding on their components, so routine checks are essential. Inspect the fuel line for any signs of wear, especially where it connects to the engine and the fuel tank. Promptly address any issues to prevent fuel leaks and potential engine damage.
By following these guidelines, you can ensure that the fuel line is properly routed, avoiding potential damage and maintaining optimal fuel flow to the two-stroke engine. Proper placement and protection of the fuel line contribute to the overall reliability and performance of the engine.
Fuel Line Removal: A Step-by-Step Guide for 2005 Chrysler PT Cruiser Owners
You may want to see also
Fitting Selection: Choose fittings compatible with fuel line material and engine requirements
When connecting a fuel line to a two-stroke engine, the selection of fittings is a critical step to ensure optimal performance and longevity. The primary consideration is compatibility with the fuel line material and the specific requirements of your engine. Different materials, such as rubber, vinyl, or synthetic compounds, have varying levels of flexibility and resistance to fuel-related chemicals. Therefore, it's essential to choose fittings that match the fuel line's material to avoid potential leaks, cracks, or premature deterioration.
For instance, if your fuel line is made of rubber, opt for rubber fittings designed to withstand the corrosive nature of gasoline or diesel. These fittings should be able to withstand the fuel's chemical properties, including its volatility and potential for degradation over time. Similarly, vinyl fuel lines require specific vinyl fittings that can handle the material's flexibility and resistance to fuel-related chemicals.
Engine requirements also play a significant role in fitting selection. Two-stroke engines often have unique fuel delivery systems, such as carburetor setups or direct injection systems. The fittings should accommodate the specific fuel flow rates and pressure requirements of your engine. For instance, high-performance two-stroke engines might demand fittings that can handle increased fuel flow and pressure to meet the engine's power demands.
Additionally, consider the mounting and connection methods of the fittings. Some engines may require fittings with threads that match the fuel line's internal diameter, ensuring a secure and leak-free connection. Others might benefit from fittings with quick-connect couplings for easier installation and maintenance. Understanding your engine's design and fuel system will help you choose the appropriate fitting types and sizes.
In summary, selecting the right fittings is crucial for a successful fuel line connection to a two-stroke engine. Compatibility with the fuel line material and engine-specific requirements are key factors to consider. By choosing the appropriate fittings, you can ensure a reliable fuel supply, optimize engine performance, and extend the lifespan of your fuel line and engine components.
Mastering Fuel Line Antifreeze: A Comprehensive Guide to Winter Car Care
You may want to see also
Clamping Techniques: Secure fuel lines with appropriate clamps for a tight, leak-free connection
When connecting fuel lines to two-stroke engines, proper clamping techniques are essential to ensure a secure and leak-free connection. The fuel lines must be tightly held in place to prevent any fuel leaks, which can cause engine performance issues and potential damage. Here's a detailed guide on how to achieve this:
Choosing the Right Clamps: Select fuel line clamps specifically designed for the application. These clamps should be made of durable materials like stainless steel or high-quality plastics that can withstand the engine's operating conditions. Look for clamps with a smooth interior surface to avoid damaging the fuel lines. The clamp size should be appropriate for the diameter of the fuel line; a good rule of thumb is to use a clamp that is at least 1.5 times the width of the fuel line.
Preparation: Before clamping, ensure the fuel lines are clean and free of any debris or contaminants. Use a cloth or a soft brush to wipe down the surfaces where the clamps will be applied. This step is crucial to ensure a tight seal. If the fuel line has any bends or kinks, straighten it carefully to maintain a smooth flow.
Clamping Process: Start by positioning the clamp around the fuel line. Place the clamp's center over the fuel line's center, ensuring it is centered and aligned properly. Use a pair of pliers or a specialized fuel line clamping tool to tighten the clamp securely. Apply firm pressure evenly to avoid marring the fuel line. The goal is to create a snug fit without crushing or damaging the line. Repeat this process for any additional fuel lines connected to the engine.
Tightening and Adjusting: After clamping, check the connections for tightness. Gently pull on the fuel lines to ensure they are securely held in place. If any movement is detected, tighten the clamps further, being careful not to overtighten, as this can cause damage. Adjust the clamps so that they are snug against the fuel lines but not so tight that they restrict flow.
Leak-Testing: Once the clamps are in place, it's essential to test for leaks. Start the engine and listen for any unusual noises, especially hissing sounds, which could indicate a fuel leak. Inspect the clamps and connections for any signs of fuel seepage. If leaks are found, carefully adjust the clamps and ensure a proper seal.
By following these clamping techniques, you can ensure that the fuel lines are securely connected to your two-stroke engine, providing a reliable and efficient power source. Proper clamping is a critical step in maintaining the engine's performance and longevity.
Catalyst Fuel Line Removal: A Step-by-Step Guide for 2006 Jeep Liberty Owners
You may want to see also
Fuel Filter Installation: Position filters to prevent contaminants from entering the engine
When installing a fuel filter for a two-stroke engine, proper positioning is crucial to ensure optimal performance and longevity. The primary goal is to prevent contaminants from entering the engine, which can cause significant damage over time. Here's a step-by-step guide on how to position the fuel filter correctly:
Start by identifying the fuel line that supplies fuel to the engine. This line typically runs from the fuel tank to the carburetor. Locate the point where the fuel line splits into smaller branches, one leading directly to the carburetor and the other potentially to a fuel pump or additional components. This branching point is an ideal location for the fuel filter. It should be positioned close to the engine but not directly on the intake stroke path to avoid any interference with the engine's operation.
The filter should be mounted in a way that allows for easy access during maintenance. A common practice is to secure it with a clamp or a dedicated mounting bracket. Ensure the filter is firmly attached to avoid any movement that could lead to disconnection. It's essential to choose a mounting position that doesn't restrict fuel flow or create unnecessary pressure points, as this could lead to fuel line damage or reduced performance.
Consider the orientation of the filter. It should be positioned vertically, with the inlet (fuel-in) side facing downward. This orientation ensures that any contaminants that might accumulate in the filter will settle at the bottom, allowing for easy cleaning or replacement when necessary. A vertical position also helps to prevent air bubbles from forming in the fuel line, which can occur if the filter is mounted horizontally.
Additionally, ensure that the filter is not located in a position where it could be easily damaged by engine components or vibrations. Protect the filter from physical impact and excessive heat, as these factors can compromise its effectiveness. Proper positioning and mounting will not only help in maintaining a clean fuel supply but also contribute to the overall reliability and efficiency of your two-stroke engine.
Optimizing Performance: Choosing the Right Dual Fuel Line for Your Holley Avenger Carb
You may want to see also
Testing for Leaks: Inspect connections and perform pressure tests to ensure no fuel leaks
When connecting a fuel line to a two-stroke engine, ensuring a tight and secure fit is crucial to prevent any fuel leaks. One effective method to verify the integrity of these connections is by conducting a thorough leak test. This process involves inspecting the fuel line connections and applying pressure to ensure there are no leaks. Here's a step-by-step guide on how to perform this test:
Start by visually inspecting all the connections. Look for any signs of damage, cracks, or corrosion on the fuel line itself and the fittings. Even minor damage can lead to fuel leaks, so it's essential to be meticulous. Check for any loose fittings or connections that might have been overlooked during the installation process. Ensure that all components are properly aligned and secured.
Next, you'll need to prepare the fuel system for the pressure test. This typically involves disconnecting the fuel line from the engine and temporarily blocking the outlet to create a closed system. You can use a piece of rubber or a small block to seal the end of the fuel line. It's important to do this in a well-ventilated area to avoid inhaling any fuel vapor.
Now, it's time to apply pressure. You can use a hand pump or a small air compressor to create a controlled amount of pressure in the fuel line. Start with a low pressure and gradually increase it while monitoring for any leaks. Pay close attention to the connections you previously inspected, as these areas are most susceptible to leaks. If you notice any fuel escaping, immediately release the pressure and identify the source of the leak.
To make the test more comprehensive, you can use a soapy water solution. Apply a thin layer of soap around the connections and observe if any bubbles form. Bubbles indicate the presence of air or fuel escaping, helping you pinpoint potential leak areas. If you find any leaks, carefully disassemble the affected connections and re-tighten them, ensuring a secure seal.
After completing the pressure test and addressing any leaks, it's crucial to re-evaluate the connections. Re-inspect the fuel line and fittings to ensure no further damage has occurred during the testing process. Once you're satisfied with the results, reconnect the fuel line to the engine and secure it according to the manufacturer's guidelines. Properly sealing the fuel connections will not only prevent leaks but also ensure optimal engine performance.
Maximizing Fuel Line Lifespan: Expert Tips for Long-Lasting Performance
You may want to see also
Frequently asked questions
A fuel line is a crucial component in a two-stroke engine's fuel system, responsible for delivering the fuel-air mixture to the engine's cylinder. It ensures that the engine receives the correct amount of fuel for efficient combustion.
Connecting the fuel line to the carburetor involves attaching it to the carburetor's float bowl or a dedicated fuel inlet. Ensure a tight connection to prevent fuel leaks. The fuel line should be positioned at an optimal angle to allow gravity-fed fuel flow.
Yes, you'll need a fuel line connector or a fuel line adapter that matches the diameter of your fuel line and the carburetor's inlet. Additionally, have a fuel line clamp or a hose clamp to secure the connection.
For two-stroke engines, it is recommended to use fuel lines made from materials like nylon or PVC, which offer good flexibility and resistance to fuel degradation. Avoid using rubber fuel lines as they may not withstand the fuel's corrosive properties.
While it is possible to use a fuel pump with a two-stroke engine, it is not always necessary. Two-stroke engines often rely on the carburetor's float bowl for fuel supply. However, if you have a high-performance engine or need more fuel pressure, a fuel pump can be an effective upgrade.