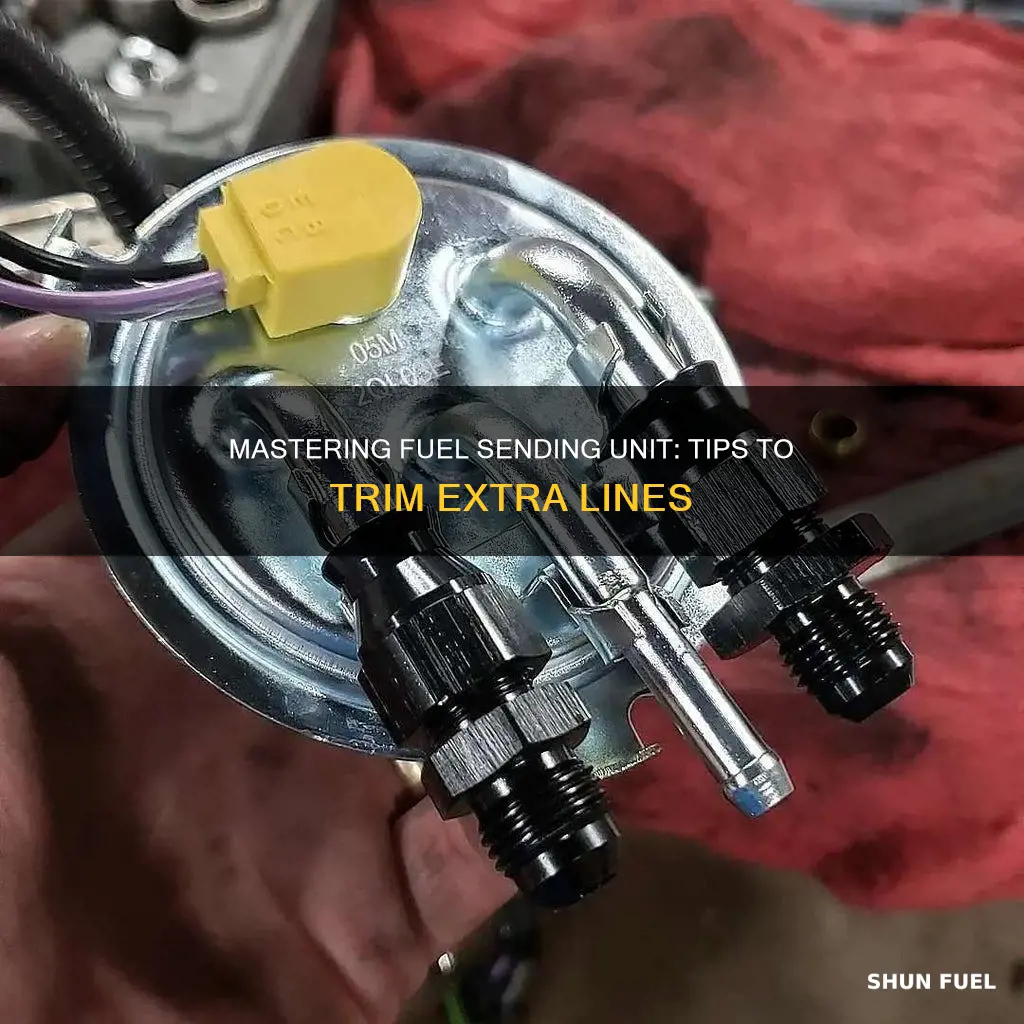
Understanding how to cap extra lines on a fuel sending unit is crucial for maintaining the proper functionality of your vehicle's fuel system. This process involves ensuring that the fuel level sensor, which sends signals to the fuel gauge, operates accurately. By capping extra lines, you prevent fuel from entering the sending unit when the tank is full, which can lead to inaccurate readings and potential issues with the fuel gauge. This guide will provide a step-by-step explanation of the process, ensuring you can effectively cap extra lines and maintain the reliability of your vehicle's fuel monitoring system.
What You'll Learn
- Fuel Sending Unit Design: Understand the physical structure and components to identify potential cap locations
- Sealing Techniques: Explore various methods like gaskets, O-rings, or welding for secure line sealing
- Material Compatibility: Ensure chosen materials withstand fuel conditions without degradation
- Pressure Resistance: Test caps for durability against fuel pressure fluctuations to prevent leaks
- Maintenance and Inspection: Regularly check and replace caps to maintain optimal performance
Fuel Sending Unit Design: Understand the physical structure and components to identify potential cap locations
The fuel sending unit, a critical component in vehicle fuel systems, is responsible for monitoring and regulating the fuel level in the tank. When designing or modifying this unit, understanding its physical structure and components is essential to identify suitable locations for capping extra lines. This process involves a detailed examination of the unit's design to ensure effective and safe capping.
To begin, one must familiarize themselves with the fuel sending unit's overall structure. This unit typically consists of a float, a sender assembly, and a wiring harness. The float, often made of lightweight materials, floats on the fuel surface, providing a visual indication of the fuel level. The sender assembly, usually located near the float, contains sensors that measure the fuel level and send signals to the vehicle's engine control unit (ECU). The wiring harness connects these sensors and the ECU, allowing for proper communication and control.
Identifying potential cap locations requires a methodical approach. Start by examining the sender assembly, as it often houses the critical components for capping. The assembly may include a fuel level sensor, a temperature sensor, and wiring connections. Carefully inspect the area around these components, ensuring that any modifications or additions do not interfere with their functionality. Look for any existing openings or ports that could be utilized for capping, such as small holes or grooves along the assembly's surface.
Additionally, consider the float's position and movement. The float's design allows it to rise and fall with the fuel level, providing accurate measurements. When capping extra lines, it is crucial to ensure that the float's movement remains unobstructed. Check for any protruding parts or obstacles that might interfere with the float's operation and adjust the design accordingly.
Furthermore, the wiring harness should be a key consideration. It connects various sensors and the ECU, so any modifications must not compromise the unit's electrical integrity. Examine the harness for any potential routing options that could accommodate the capping process without causing damage or interference. Properly managing the wiring will ensure the fuel sending unit's reliability and performance.
In summary, understanding the fuel sending unit's physical structure and components is vital for successful capping. By carefully inspecting the sender assembly, float, and wiring harness, designers can identify suitable locations for capping extra lines while maintaining the unit's functionality and safety. This detailed approach ensures that the fuel sending unit continues to operate efficiently, providing accurate fuel level readings to the vehicle's ECU.
Fixing a Leaking Fuel Line: A Step-by-Step Guide
You may want to see also
Sealing Techniques: Explore various methods like gaskets, O-rings, or welding for secure line sealing
When dealing with capping extra lines on a fuel sending unit, the choice of sealing technique is crucial to ensure a secure and reliable connection. Here's an exploration of various methods to achieve this:
Gaskets: One of the most common and effective sealing techniques is using gaskets. These are made of materials like rubber or silicone and provide a flexible, yet robust seal. When capping extra lines, you can use a gasket to create a tight seal between the fuel sending unit and the new line. The gasket should be cut to fit the specific dimensions of the line and the unit's port. Ensure the gasket is lubricated to facilitate a smooth installation, and then press it firmly into place. Gaskets are ideal for applications where vibration or movement is expected, as they can accommodate minor misalignments without compromising the seal.
O-Rings: O-rings are another excellent sealing solution, offering a precise and durable seal. These are typically made of synthetic rubber or silicone and are designed to create a tight, circular seal. When capping extra lines, insert the O-ring into the fuel sending unit's port, ensuring it is the correct size and shape for the line. O-rings provide a reliable seal, especially in high-pressure applications, and can be used in conjunction with gaskets for added security. They are often used in fuel systems due to their ability to withstand the corrosive nature of fuel.
Welding: For a more permanent and robust solution, welding can be employed. This method involves joining the extra line to the fuel sending unit using specialized welding techniques. It is crucial to ensure that the welding process is done by a skilled professional to avoid any potential issues. Welding provides an extremely strong and reliable seal, making it ideal for high-performance or industrial applications. However, it requires careful preparation and may not be suitable for all fuel sending unit designs. After welding, proper cleaning and inspection of the weld area are essential to ensure a secure and safe connection.
Each of these sealing techniques offers unique advantages, and the choice depends on the specific requirements of your fuel sending unit and the application. It is essential to consider factors such as pressure, temperature, and the corrosive nature of the fuel when selecting the appropriate sealing method. Proper installation and regular maintenance will further ensure the longevity and reliability of the sealed connection.
Mastering the Art of Draining Gas: A Step-by-Step Guide
You may want to see also
Material Compatibility: Ensure chosen materials withstand fuel conditions without degradation
When it comes to capping extra lines on a fuel sending unit, material compatibility is a critical aspect that cannot be overlooked. The fuel sending unit is an essential component in a vehicle's fuel system, responsible for accurately measuring and delivering fuel to the engine. Therefore, the materials used in its construction must be carefully selected to ensure they can withstand the harsh conditions of the fuel environment without any degradation.
One of the primary concerns is the compatibility of materials with the fuel itself. Different types of fuels, such as gasoline, diesel, or ethanol blends, have varying properties and compositions. For example, ethanol-blended fuels are more corrosive and can cause degradation of certain materials over time. Therefore, it is crucial to choose materials that are resistant to corrosion and have a stable performance in the presence of these fuels. Common materials used for fuel-related components include stainless steel, aluminum alloys, and specialized polymers designed for fuel applications. These materials are chosen for their inherent resistance to corrosion, oxidation, and fuel-induced degradation.
Additionally, the operating temperature of the fuel sending unit should be considered. Fuel temperatures can vary significantly depending on the vehicle's operating conditions and climate. High temperatures can accelerate material degradation, especially in the case of plastics or rubbers used in seals or gaskets. It is essential to select materials with a suitable temperature range that can withstand both extreme cold and hot conditions without losing their structural integrity or performance.
Another factor to consider is the compatibility of materials with the fuel system's operating pressures. Fuel sending units are designed to operate within specific pressure ranges, and materials must be able to withstand these pressures without failing or leaking. Materials with appropriate mechanical properties, such as strength and elasticity, are chosen to ensure they can handle the stresses and strains associated with fuel system operations.
Furthermore, the chosen materials should also be resistant to fuel-related contaminants. Fuel can contain various additives and impurities that may have adverse effects on certain materials. For instance, some fuels may contain water, which can lead to corrosion or material swelling in incompatible materials. Therefore, selecting materials with inherent resistance to water absorption and corrosion is essential to ensure long-term reliability.
In summary, when capping extra lines on a fuel sending unit, it is imperative to consider material compatibility with the fuel, operating temperatures, pressures, and potential contaminants. By carefully selecting materials that are resistant to corrosion, temperature variations, and fuel-related degradation, you can ensure the longevity and reliable performance of the fuel sending unit, contributing to the overall efficiency and safety of the vehicle's fuel system.
Unclog Fuel Lines: The Ultimate Gas Additive Guide
You may want to see also
Pressure Resistance: Test caps for durability against fuel pressure fluctuations to prevent leaks
When dealing with fuel systems, ensuring the integrity of the fuel sending unit is crucial for optimal engine performance and longevity. One critical aspect often overlooked is the capping of extra lines, which can significantly impact the overall system's reliability. This process involves sealing off any additional fuel lines that may have been installed, ensuring they do not interfere with the primary fuel flow or cause potential leaks.
The primary concern with extra lines is the potential for fuel pressure fluctuations. Fuel pressure must be carefully managed to ensure the engine receives the correct amount of fuel for efficient combustion. Any disruption in this delicate balance can lead to engine misfires, reduced performance, and even potential damage to the engine over time. By capping these extra lines, you create a sealed environment that prevents any unwanted fuel flow, thus maintaining the desired pressure.
To test the caps for pressure resistance, a comprehensive approach is necessary. Start by applying varying levels of fuel pressure to the system and monitoring for any signs of leaks. This can be done using specialized equipment that measures fuel pressure and flow rates. The goal is to simulate real-world driving conditions to ensure the caps can withstand the stresses of fluctuating fuel pressure. Additionally, consider using pressure gauges to visually inspect for any fuel escaping around the caps, ensuring they are tight and secure.
Another critical aspect of this test is the duration of the pressure application. Fuel pressure can vary significantly over time, especially during rapid acceleration or deceleration. Therefore, the test should be conducted over an extended period to account for these dynamic changes. This long-term testing will help identify any potential issues that may arise due to prolonged exposure to varying fuel pressures.
In addition to pressure resistance, the caps should also be evaluated for their ability to withstand temperature changes, as fuel temperature can also affect pressure. By conducting these tests, you can ensure that the caps are not only durable but also capable of maintaining a secure seal under various environmental conditions. This level of testing is essential to guarantee the long-term reliability of the fuel sending unit and the overall fuel system.
2001 Neon Fuel Line: Size and Compatibility Guide
You may want to see also
Maintenance and Inspection: Regularly check and replace caps to maintain optimal performance
When it comes to maintaining the performance and longevity of your fuel sending unit, regular maintenance and inspection are crucial, especially when it comes to the caps that connect it to the fuel tank. These caps play a vital role in ensuring a consistent and accurate fuel level reading, which is essential for proper vehicle operation. Here's a detailed guide on why and how to regularly check and replace these caps:
Understanding the Importance of Cap Maintenance:
The caps on the fuel sending unit are designed to seal the connection between the unit and the fuel tank, preventing fuel leaks and ensuring a tight fit. Over time, these caps can wear out or become damaged due to various factors such as age, temperature changes, or physical impact. If left unattended, the consequences can be detrimental. Leaks in the fuel system can lead to engine misfires, reduced performance, and even potential safety hazards. Additionally, a damaged cap might result in an inaccurate fuel gauge reading, causing confusion and potential overfilling or underfilling of the fuel tank.
Regular Inspection Routine:
Implement a regular inspection routine as part of your vehicle's maintenance schedule. Here's what you should look out for:
- Visual Inspection: Start by visually examining the caps for any signs of damage, cracks, or warping. Check for any visible fuel leaks around the cap's connection point. Even a small leak can accumulate over time, leading to performance issues.
- Tightness Check: Ensure that the caps are securely tightened. Loosen the caps periodically to verify their tightness, especially if your vehicle has been driven over rough terrain or through extreme weather conditions.
- Fuel Level Accuracy: Periodically check the fuel gauge reading against the actual fuel level in the tank. If there's a noticeable discrepancy, it may indicate a faulty cap or sending unit, requiring immediate attention.
Replacing Worn-Out Caps:
If you notice any issues during your inspections, it's essential to take prompt action:
- Replace Damaged Caps: If the cap is cracked, warped, or shows signs of fuel leakage, replace it immediately. This is a straightforward process that often requires removing the old cap and installing a new one, ensuring a proper seal.
- Consider Cap Condition: Even if there are no visible issues, it's good practice to replace the caps periodically, especially if your vehicle is older or has high mileage. This proactive approach can prevent unexpected fuel system problems.
Professional Assistance:
For complex fuel system issues or if you're unsure about the process, it's advisable to consult a professional mechanic. They can provide expert advice and ensure that the replacement is done correctly, adhering to manufacturer specifications.
By following this maintenance and inspection protocol, you can ensure that the caps on your fuel sending unit remain in optimal condition, contributing to the overall reliability and performance of your vehicle's fuel system. Regular care will help prevent costly repairs and keep your vehicle running smoothly.
Understanding the Mantis Fuel Line: Black Fuel Line Dimensions
You may want to see also
Frequently asked questions
Capping extra lines on a fuel sending unit is a process used to ensure the unit's accuracy and reliability in measuring fuel levels. By removing unnecessary connections, it minimizes the risk of electrical interference and potential malfunctions.
Extra lines are typically identified as unused wires or connections that are not part of the standard wiring harness. These lines might be visible as loose ends or additional ports on the fuel sending unit. It's important to consult the vehicle's wiring diagram or seek professional guidance to ensure you cap the correct lines.
Yes, capping extra lines can indirectly contribute to better fuel efficiency. By reducing electrical noise and potential short circuits, the fuel sending unit's performance is optimized, ensuring accurate fuel level readings. This accuracy helps the engine's electronic control unit (ECU) make precise fuel injection calculations, leading to improved fuel economy.
If not done correctly, capping extra lines might lead to issues. It's crucial to follow a systematic approach and ensure that the capping process doesn't interfere with the unit's functionality. Incorrect capping could result in fuel level gauge malfunctions or even engine performance problems.
The tools required for capping extra lines may vary depending on the vehicle and the specific lines to be capped. Basic tools like wire cutters, crimping tools, and heat shrink tubing can be helpful. However, for complex wiring harnesses, it is recommended to consult a professional mechanic or refer to the vehicle's service manual for detailed instructions and the appropriate tools.