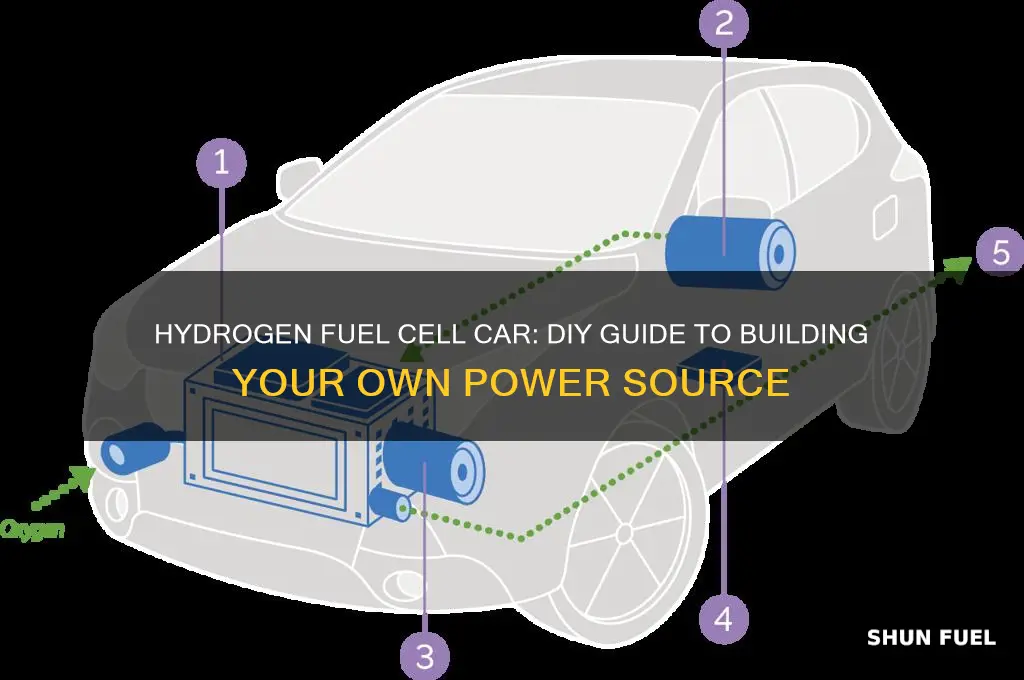
Building a hydrogen fuel cell for a car is a complex but rewarding project that can contribute to a more sustainable future. This guide will provide an overview of the key steps involved in constructing a hydrogen fuel cell, from understanding the basic principles of fuel cell technology to sourcing materials and assembling the components. We will explore the necessary components, such as the electrolyte, catalyst, and membrane, and discuss the importance of each in the fuel cell's efficiency and performance. Additionally, we will delve into the process of creating the hydrogen storage system, ensuring safety, and integrating the fuel cell into a vehicle's power system. By the end of this guide, readers will have a comprehensive understanding of the process and the potential to build their own hydrogen fuel cell for a car.
What You'll Learn
- Materials Selection: Choose suitable catalysts, membranes, and electrolytes for efficient hydrogen fuel cell operation
- Stack Design: Optimize cell architecture for power density, durability, and compact size
- Hydrogen Storage: Develop safe, high-capacity methods to store hydrogen for continuous vehicle operation
- Cooling Systems: Implement effective cooling to manage heat generation and maintain optimal operating temperatures
- Integration with Engine: Seamlessly integrate the fuel cell with the car's existing systems for efficient power generation
Materials Selection: Choose suitable catalysts, membranes, and electrolytes for efficient hydrogen fuel cell operation
When it comes to building a hydrogen fuel cell for a car, materials selection is a critical aspect that can significantly impact the efficiency and performance of the fuel cell. The right choice of catalysts, membranes, and electrolytes is essential to ensure optimal operation and longevity. Here's a detailed breakdown of the materials considerations:
Catalysts:
- Catalysts play a pivotal role in facilitating the electrochemical reactions within the fuel cell. The most commonly used catalysts for hydrogen fuel cells are platinum (Pt), palladium (Pd), and their alloys. These metals are highly efficient in promoting the oxidation of hydrogen and the reduction of oxygen.
- For the anode (hydrogen-side), platinum-based catalysts are often preferred due to their excellent activity and stability. However, the high cost of platinum has led to research into alternative catalysts like palladium, which offers a more cost-effective solution without compromising performance.
- On the cathode (oxygen-side), catalysts such as platinum-ruthenium (PtRu) or platinum-iridium (PtIr) alloys are used to enhance the oxygen reduction reaction. These catalysts provide better performance and durability compared to pure platinum.
Membranes:
- The membrane, also known as the electrolyte membrane, is a critical component that separates the anode and cathode compartments while allowing protons (H+) to pass through. The primary function of the membrane is to facilitate proton conduction while blocking electrons, ensuring a continuous flow of current.
- Proton-exchange membrane (PEM) fuel cells typically use membranes made from perfluorinated sulfonated polymers, such as Nafion. These membranes have good proton conductivity and chemical stability, making them suitable for high-temperature operations.
- Alternatively, solid-oxide fuel cells (SOFCs) utilize ceramic membranes, like yttrium-stabilized zirconia (YSZ), which exhibit excellent proton conductivity at higher temperatures. These membranes are more suitable for stationary applications but can also be adapted for automotive use.
Electrolytes:
- Electrolytes are substances that conduct ions (protons or electrons) within the fuel cell. In hydrogen fuel cells, the electrolyte is typically the same as the membrane, ensuring a continuous proton pathway.
- For PEM fuel cells, the electrolyte membrane itself acts as the electrolyte, allowing protons to migrate from the anode to the cathode while blocking electrons.
- In SOFCs, the electrolyte is a solid ceramic material that facilitates the movement of oxygen ions (O2-) from the cathode to the anode, enabling the electrochemical reactions.
The choice of materials for catalysts, membranes, and electrolytes is a complex process, requiring a deep understanding of electrochemistry and material science. Researchers and engineers are continually exploring new materials and compositions to improve efficiency, reduce costs, and enhance the overall performance of hydrogen fuel cells for automotive applications.
Unraveling the Mystery: What's the Role of a Car's Fuel Filter?
You may want to see also
Stack Design: Optimize cell architecture for power density, durability, and compact size
When designing the stack for a hydrogen fuel cell vehicle, optimizing the cell architecture is crucial to achieving high power density, ensuring durability, and maintaining a compact size. Here's a detailed breakdown of the key considerations:
Power Density:
- Electrode Design: The electrodes (anode and cathode) are the heart of the fuel cell. Optimize their design for maximum surface area, allowing for more hydrogen and oxygen to react, thereby increasing power output. Consider using porous materials with high surface area-to-volume ratios, such as metal-supported catalysts or carbon-based materials.
- Gas Diffusion Layers (GDLs): Choose GDLs with excellent gas permeability and wicking properties to efficiently transport reactants to the electrodes while minimizing resistance.
- Flow Channels: Design the flow channels for optimal gas flow distribution, ensuring uniform reactant concentration across the cell. Proper channel geometry prevents dead zones and promotes efficient mass transfer.
Durability:
- Catalyst Stability: Select catalysts that are resistant to poisoning and degradation under operating conditions. Platinum, palladium, and their alloys are commonly used, but research into more cost-effective and durable alternatives is ongoing.
- Electrolyte Membrane: Choose a robust electrolyte membrane that can withstand the harsh environment inside the fuel cell, including high temperatures, pressures, and chemical exposure.
- Mechanical Strength: The stack components, including the electrodes, GDLs, and membranes, need to be mechanically robust to withstand the expansion and contraction during operation.
Compact Size:
- Miniaturization Techniques: Explore miniaturization techniques such as thin-film deposition, nanostructured electrodes, and 3D printing to reduce the size of individual cells while maintaining performance.
- Stack Configuration: Consider innovative stack configurations, such as planar or tubular designs, that allow for more efficient use of space and potentially higher power density.
- Material Selection: Opt for lightweight materials for the stack components to reduce overall weight and improve compactness.
Key Considerations:
- Balance: Achieving the right balance between power density, durability, and compactness is essential. Trade-offs may be necessary, and careful optimization is required.
- Cost: The cost of materials and manufacturing processes significantly impacts the overall viability of hydrogen fuel cell vehicles. Explore cost-effective alternatives and manufacturing techniques.
- Research and Development: Continuous research and development are crucial to pushing the boundaries of fuel cell technology and improving performance, durability, and cost-effectiveness.
E85 Fuel Flexibility: Can Any Car Run on Ethanol?
You may want to see also
Hydrogen Storage: Develop safe, high-capacity methods to store hydrogen for continuous vehicle operation
The challenge of storing hydrogen safely and efficiently for vehicle use is a critical aspect of developing hydrogen fuel cell technology. Hydrogen, a highly flammable gas, requires innovative storage solutions to ensure the safety and practicality of its use in transportation. One of the primary goals is to develop storage methods that offer high capacity, allowing for continuous operation of vehicles without frequent refueling.
One promising approach is the utilization of compressed gas storage tanks. These tanks are designed to withstand high pressures, typically around 350-700 bars, to store hydrogen in a dense and compact form. The key advantage of this method is its simplicity and the ability to scale up production. However, it presents challenges in terms of weight and volume, especially when considering the need for additional safety measures to prevent leaks and ensure the structural integrity of the vehicle.
Another innovative storage concept is the use of metal hydrides. These compounds can absorb and release hydrogen gas through a chemical reaction. Sodium alanate, for instance, is a metal hydride that can store hydrogen at relatively high densities. This method offers the benefit of a lightweight and compact storage solution, making it ideal for vehicles. However, the process of hydrogen release and absorption can be slow, which may impact the overall efficiency of the vehicle's operation.
Liquid hydrogen storage is yet another strategy, where hydrogen is cooled to extremely low temperatures, turning it into a liquid state. This method provides high energy density, allowing for longer vehicle ranges. However, it requires specialized equipment and infrastructure to handle and store the liquid hydrogen safely. Additionally, the process of liquefaction and vaporization can be energy-intensive, which needs to be carefully managed to ensure overall system efficiency.
To address these challenges, ongoing research focuses on improving the efficiency and safety of hydrogen storage systems. This includes developing advanced materials and storage tank designs, as well as exploring new hydrogen storage forms, such as hydrogen-binding organic compounds and carbon-based materials. The ultimate goal is to create a storage system that provides the necessary capacity, safety, and convenience for widespread adoption of hydrogen fuel cell vehicles.
Car Fuel Pump Location: Under the Hood or Behind the Seat?
You may want to see also
Cooling Systems: Implement effective cooling to manage heat generation and maintain optimal operating temperatures
When building a hydrogen fuel cell for a car, implementing an efficient cooling system is crucial to ensure optimal performance and longevity. Hydrogen fuel cells generate electricity through an electrochemical reaction, which produces heat as a byproduct. This heat needs to be managed carefully to prevent overheating and maintain the fuel cell's efficiency and reliability. Here's a detailed guide on how to approach cooling systems for your hydrogen fuel cell vehicle:
- Heat Dissipation Methods: The primary goal is to dissipate the generated heat effectively. One common approach is to use a liquid cooling system, where a coolant (often a mixture of water and additives) circulates through the fuel cell stack. This coolant absorbs heat from the fuel cell and carries it away to a radiator or a heat exchanger. The radiator then releases the heat to the surrounding air, ensuring the fuel cell operates at a safe temperature. Alternatively, air cooling can be employed, where fans and heat sinks are used to draw air over the fuel cell, dissipating heat directly into the environment.
- Coolant Selection: Choosing the right coolant is essential. It should have excellent heat transfer properties and be compatible with the fuel cell materials to prevent corrosion or degradation. Coolants like ethylene glycol-water mixtures or specialized synthetic coolants are often used due to their stability and ability to handle the corrosive nature of some fuel cell components. The coolant should also have a high boiling point to withstand the operating temperatures of the fuel cell.
- Cooling System Design: The design of the cooling system should consider the specific requirements of your fuel cell stack. This includes determining the appropriate flow rate of the coolant to ensure efficient heat exchange. Proper placement of coolant inlets and outlets within the fuel cell stack is vital for optimal cooling. Additionally, the system should be designed to handle any potential leaks or failures, ensuring the vehicle's safety.
- Temperature Control and Monitoring: Implementing a temperature control system is essential to maintain the fuel cell's operating temperature within an optimal range. This can be achieved by using temperature sensors placed at various points in the fuel cell stack and coolant system. These sensors provide real-time data, allowing the system to adjust coolant flow rates or activate additional cooling methods if temperatures deviate from the desired range.
- Insulation and Heat Management: Proper insulation of the fuel cell components can help minimize heat loss to the surroundings. Insulating materials should be used to cover exposed surfaces, especially where heat is generated. This ensures that the generated heat is contained and directed towards the cooling system. Additionally, managing the overall thermal management of the vehicle, including the engine and other components, can help maintain a balanced operating temperature for the fuel cell.
By implementing an effective cooling system, you can ensure that your hydrogen fuel cell operates efficiently and reliably, contributing to the overall performance and longevity of the vehicle. It is a critical aspect of fuel cell technology that requires careful consideration and design to meet the demands of a practical, high-performance hydrogen car.
Can I Run My Car's Engine as Fuel? Exploring Alternatives
You may want to see also
Integration with Engine: Seamlessly integrate the fuel cell with the car's existing systems for efficient power generation
The integration of a hydrogen fuel cell into a vehicle's engine system is a crucial aspect of building a practical and efficient hydrogen-powered car. This process involves seamlessly combining the fuel cell with the existing automotive infrastructure to ensure optimal power generation and overall performance. Here's a detailed guide on how to achieve this integration:
Understanding the Engine Architecture: Begin by thoroughly understanding the car's engine architecture, including its electrical and mechanical systems. Identify the key components such as the battery, alternator, wiring harness, and control units. This knowledge is essential for designing an integration system that works in harmony with the vehicle's existing setup. For instance, you need to determine the optimal placement of the fuel cell to ensure efficient cooling and easy access to the necessary connections.
Power Generation and Distribution: The fuel cell generates electricity through the electrochemical reaction of hydrogen and oxygen, producing water as a byproduct. This electricity can be used to power the car's electrical systems and even charge the vehicle's battery, if applicable. Integrate the fuel cell system with the car's power distribution network. This involves connecting the fuel cell's output to the vehicle's electrical system, ensuring proper voltage and current levels. You might need to design custom wiring harnesses to handle the unique power requirements of the fuel cell.
Engine Control and Synchronization: Seamless integration requires precise control and synchronization between the fuel cell and the internal combustion engine (ICE), if present. If the vehicle has a hybrid system, the fuel cell must work in conjunction with the ICE to optimize power output and efficiency. Develop control algorithms that manage the fuel cell's power output based on the engine's load and speed. This ensures that the fuel cell provides the required power without interfering with the ICE's operation. Advanced sensors and feedback systems can be employed to monitor and adjust the fuel cell's performance in real-time.
Cooling and Ventilation: Efficient cooling is critical for both the fuel cell and the surrounding engine components. Design an effective cooling system that can handle the heat generated by the fuel cell stack. This might involve integrating a dedicated cooling circuit or utilizing the car's existing cooling system with modifications. Proper ventilation is also essential to manage the hydrogen gas and prevent any safety hazards. Ensure that the fuel cell's ventilation system is integrated with the vehicle's overall ventilation architecture.
Safety and Monitoring: Implement robust safety measures and monitoring systems to ensure the safe operation of the fuel cell. This includes pressure and temperature sensors, leak detection systems, and fail-safe mechanisms. The integration should allow for real-time monitoring of the fuel cell's performance, hydrogen levels, and overall system health. This data can be used for diagnostics and to optimize the vehicle's performance.
By carefully considering these integration aspects, engineers can create a hydrogen fuel cell system that seamlessly blends with the car's existing infrastructure, resulting in a high-performance, efficient, and environmentally friendly vehicle. This integration process is a key challenge in the development of hydrogen-powered automobiles, but with the right approach, it can be achieved successfully.
Understanding Your Car's Fuel: A Comprehensive Guide
You may want to see also
Frequently asked questions
The primary components include a hydrogen storage system, typically a high-pressure tank or a metal hydride storage, an electrolyte, usually a polymer membrane, and an anode and cathode catalyst. The electrolyte facilitates the movement of protons, while the catalysts enable the electrochemical reactions.
In a fuel cell, hydrogen gas is fed into the anode, where it undergoes a chemical reaction with oxygen from the air, producing water as a byproduct. This reaction generates protons and electrons. The protons move through the electrolyte to the cathode, while the electrons are directed through an external circuit, creating an electric current. The cathode then combines the protons, electrons, and oxygen to form water.
Hydrogen fuel cells offer several benefits for automotive applications. They produce electricity through a clean and efficient process, emitting only water vapor and warm air, making them environmentally friendly. Fuel cells provide a high power-to-weight ratio, resulting in quick acceleration. They also offer a longer driving range compared to battery-electric vehicles and can be refueled rapidly, similar to conventional gasoline or diesel cars.