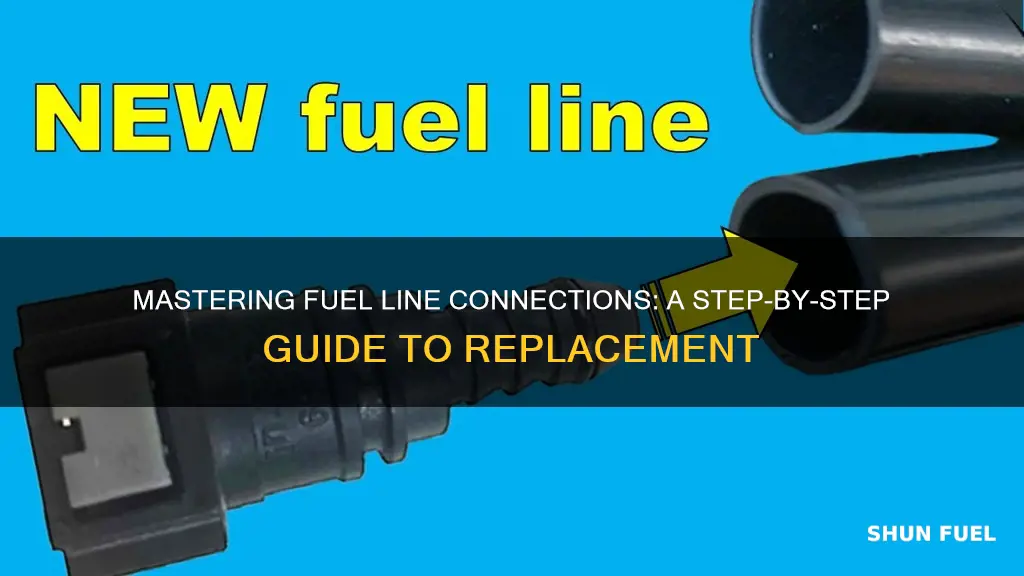
Assembling fuel line replacement connectors requires careful attention to detail and adherence to specific steps. This process ensures a secure and leak-free connection, which is crucial for maintaining the integrity of your vehicle's fuel system. By following a structured approach, you can efficiently replace damaged or worn-out fuel lines, ensuring optimal performance and safety. The following guide will provide a comprehensive overview of the necessary steps to assemble these connectors effectively.
Characteristics | Values |
---|---|
Preparation | Ensure you have the necessary tools and materials, including the replacement fuel line, connectors, and a fuel line cutter. |
Safety | Wear protective gloves and goggles to avoid contact with fuel. |
Fuel Line Inspection | Check the existing fuel line for any damage or leaks before removing it. |
Cutter Usage | Cut the old fuel line at the desired length, ensuring a clean and precise cut. |
Connector Compatibility | Verify that the replacement connectors are compatible with the fuel line size and type. |
Assembly Steps | 1. Slide the connector onto the fuel line. 2. Secure the connector using the provided clamp or retaining ring. 3. Tighten the connector securely but avoid over-tightening. |
Leak Test | After assembly, perform a leak test by applying pressure to the connectors and checking for any fuel leakage. |
Documentation | Keep records of the assembly process, including the order of connectors and any adjustments made. |
Safety Check | Inspect all connections for tightness and integrity. Ensure no fuel leaks are present. |
Final Steps | Dispose of the old fuel line properly and store the replacement connectors for future use. |
What You'll Learn
- Prepare Tools: Gather necessary tools like wrenches, pliers, and fuel line replacement connectors
- Inspect Fuel Line: Check for damage, leaks, and ensure the line is clean and dry
- Remove Old Connector: Carefully disconnect the old connector, being mindful of any fuel residue
- Clean and Prepare: Clean the fuel line and connector ends to ensure a secure connection
- Install New Connector: Slide the new connector onto the fuel line and tighten securely
Prepare Tools: Gather necessary tools like wrenches, pliers, and fuel line replacement connectors
Before you begin the process of replacing a fuel line connector, it's crucial to ensure you have all the necessary tools and components ready. This preparation will make the task more efficient and less stressful. Here's a step-by-step guide on what you need to gather:
Wrenches and Pliers: These are essential tools for any fuel line replacement job. You will typically need a set of wrenches, including both standard and adjustable types, to loosen and tighten the fuel line fittings. Wrenches with different sizes and jaw sizes are often required to accommodate various fuel line connectors and fittings. Additionally, pliers are indispensable for gripping and turning small components, especially when dealing with tight spaces and delicate connections.
Fuel Line Replacement Connectors: This is the core component of your repair. Ensure you have the correct type and size of replacement connectors that match your vehicle's fuel line specifications. Different vehicles may use different connector types, so it's crucial to identify the specific connectors required for your make and model. Having the right connectors will ensure a proper fit and prevent any potential leaks.
Other Essential Tools: Depending on your vehicle and the complexity of the fuel system, you might need additional tools. For instance, a fuel line cutter or a fuel line debander can be useful for preparing the old fuel line and creating a clean cut. You may also consider having a fuel line inspection camera or a borescope to visualize the inside of the fuel lines and identify any potential issues. These tools can make the repair process more efficient and help ensure a thorough job.
By gathering these tools and components in advance, you'll be well-prepared to tackle the fuel line replacement. This organized approach will save you time and effort during the repair process, ensuring a successful outcome. Remember, having the right tools and being prepared is half the battle when it comes to automotive repairs.
Replacing Fuel Line on a Weedeater: A Step-by-Step Guide
You may want to see also
Inspect Fuel Line: Check for damage, leaks, and ensure the line is clean and dry
When inspecting the fuel line, it's crucial to ensure it is in optimal condition to prevent any potential issues. Start by visually examining the fuel line for any signs of damage, such as cracks, punctures, or corrosion. Look for any visible wear and tear, especially at the points where the fuel line connects to the fuel tank, pump, and engine. Inspect the fittings and connectors for any signs of deterioration or damage, as these can be potential leak points.
Next, check for any leaks. A simple way to do this is to spray a small amount of soapy water along the length of the fuel line. If you notice any bubbles forming, it indicates a potential leak. Leaks can occur at connections, fittings, or even within the fuel line itself. Address any leaks immediately, as they can lead to fuel loss, engine performance issues, and potential safety hazards.
Ensure that the fuel line is clean and dry. Over time, fuel lines can accumulate dirt, debris, and moisture, which can lead to corrosion and reduced performance. Use a fuel line cleaner to remove any built-up contaminants. Rinse the line thoroughly to eliminate any remaining cleaner and ensure it is completely dry before proceeding with the replacement or repair.
Pay attention to the condition of the fuel line's protective covering. This covering is designed to shield the line from damage and corrosion. Inspect it for any tears, punctures, or signs of wear. If the covering is damaged, it may be necessary to replace the fuel line to prevent further issues.
Remember, regular inspection and maintenance of the fuel line are essential to ensure the proper functioning of your vehicle's fuel system. By checking for damage, leaks, and keeping the line clean and dry, you can identify potential problems early on and take the necessary steps to address them, ultimately ensuring a reliable and efficient fuel supply to your engine.
Replacing Preformed Fuel Lines in Your 02 Chevy Silverado
You may want to see also
Remove Old Connector: Carefully disconnect the old connector, being mindful of any fuel residue
When replacing a fuel line connector, the first crucial step is to safely and meticulously remove the old one. This process requires a steady hand and a careful approach to avoid any potential hazards. Begin by locating the specific connector you intend to replace. It is typically found along the fuel line, often near the engine or fuel tank. Once identified, use a pair of pliers or a specialized fuel line removal tool to carefully grip and pull the connector away from the fuel line. Apply gentle, steady pressure to disconnect the connector from the fuel line, ensuring you do not force it to prevent damage. As you work, be mindful of any fuel residue that may have accumulated around the connector. Fuel can be messy and potentially harmful, so take precautions to avoid spills or splashes. Consider wearing gloves and using a rag to wipe away any fuel residue before and during the removal process.
Take your time with this step, as rushing can lead to mistakes. If the connector is stubborn and does not come off easily, you may need to apply a small amount of fuel line solvent to loosen any stubborn connections. However, use this sparingly, as excessive solvent can be harmful. Once the old connector is removed, inspect the surrounding area for any signs of damage or corrosion. Clean the area if necessary to ensure a proper seal when installing the new connector. Remember, the goal is to create a safe and efficient fuel system, so every step should be executed with precision and care.
Fuel Filter Maintenance for 2007 Mazdaspeed3: When and Why?
You may want to see also
Clean and Prepare: Clean the fuel line and connector ends to ensure a secure connection
To ensure a successful fuel line replacement, the initial step is to thoroughly clean and prepare the fuel line and its connector ends. This process is crucial as it ensures a secure and leak-free connection, preventing potential issues down the line. Start by gathering the necessary tools and materials, including a fuel line cleaner, a soft-bristled brush, and a clean rag.
Begin by disconnecting the fuel line from the vehicle's fuel tank or source. This step requires careful handling to avoid any spills or damage. Once disconnected, use the fuel line cleaner to remove any built-up contaminants, such as fuel residue, dirt, or corrosion. Apply the cleaner directly to the fuel line and connector ends, ensuring complete coverage. Allow the cleaner to work for the recommended time, which is typically a few minutes, to loosen and dissolve any stubborn deposits.
After the cleaning agent has done its work, rinse the fuel line thoroughly with clean water to remove any remaining cleaner and debris. Ensure that all traces of the cleaning solution are washed away to prevent any potential chemical reactions or residue buildup. Use a gentle stream of water and a soft brush to scrub the fuel line, ensuring that you reach all areas, including the interior of the connector ends.
Once the fuel line is thoroughly rinsed, use a clean rag to wipe it down, removing any excess water. Pay close attention to the connector ends, as these areas are critical for a proper connection. Ensure that the surfaces are completely dry before proceeding to the next step. A well-cleaned and prepared fuel line and connector assembly will facilitate a secure and reliable connection during the replacement process.
By taking the time to clean and prepare the fuel line and connector ends, you are setting the foundation for a successful fuel line replacement. This meticulous approach ensures that the new connectors will fit snugly and establish a strong bond, minimizing the risk of leaks or other complications. Remember, a clean and prepared system is the key to a smooth and efficient repair process.
Honda Civic Fuel Filter: When to Replace and How
You may want to see also
Install New Connector: Slide the new connector onto the fuel line and tighten securely
To begin the installation process, ensure you have the necessary tools and components ready. You'll need the new fuel line connector, a suitable wrench or socket, and possibly a cleaning agent to remove any old fuel residue. Start by locating the damaged or faulty connector on the fuel line. Carefully remove any existing connector by unscrewing or unclipping it, being mindful of any fuel that may still be present.
Once the old connector is removed, inspect the fuel line for any signs of damage or wear. Ensure that the new connector is the correct size and type for your specific fuel line. Take note of the orientation of the connector on the fuel line, as some may have specific directions for optimal performance.
Now, carefully slide the new connector onto the fuel line. Ensure it is aligned properly and fits snugly over the fuel line. You may need to apply some gentle force to get it started, but be careful not to force it too much to avoid damaging the fuel line. Once the connector is in place, use the appropriate tool to tighten it securely. Follow the manufacturer's guidelines for the correct torque value to ensure a proper seal and effective connection.
After tightening the connector, inspect it for any leaks or signs of damage. Check that the connector is firmly attached and that there is no fuel seeping through. If everything looks secure, you can proceed to test the fuel system to ensure there are no further issues.
Remember, when working with fuel lines, it's crucial to exercise caution and follow safety protocols to prevent any accidents or fuel-related hazards. Always wear protective gear and ensure proper ventilation when handling fuel.
Replacing the Fuel Filter: A Guide for 1995 Plymouth Breeze Owners
You may want to see also
Frequently asked questions
You will need a set of wrenches or pliers of various sizes, a fuel line cutter, a fuel line crimper, and a fuel line replacement connector kit. Having these tools will ensure you can properly connect and secure the new fuel line.
Start by cutting the old fuel line to the appropriate length, ensuring there is a smooth, straight edge to work with. Then, insert the fuel line into the connector, making sure it is aligned correctly. Use the crimper to apply firm pressure and create a secure connection, being careful not to over-crimp.
It is generally recommended to replace the entire fuel line when using replacement connectors. Old fuel lines may have accumulated contaminants or damage over time, which can affect the performance and safety of the fuel system. Fresh fuel line ensures a reliable connection and minimizes the risk of leaks.