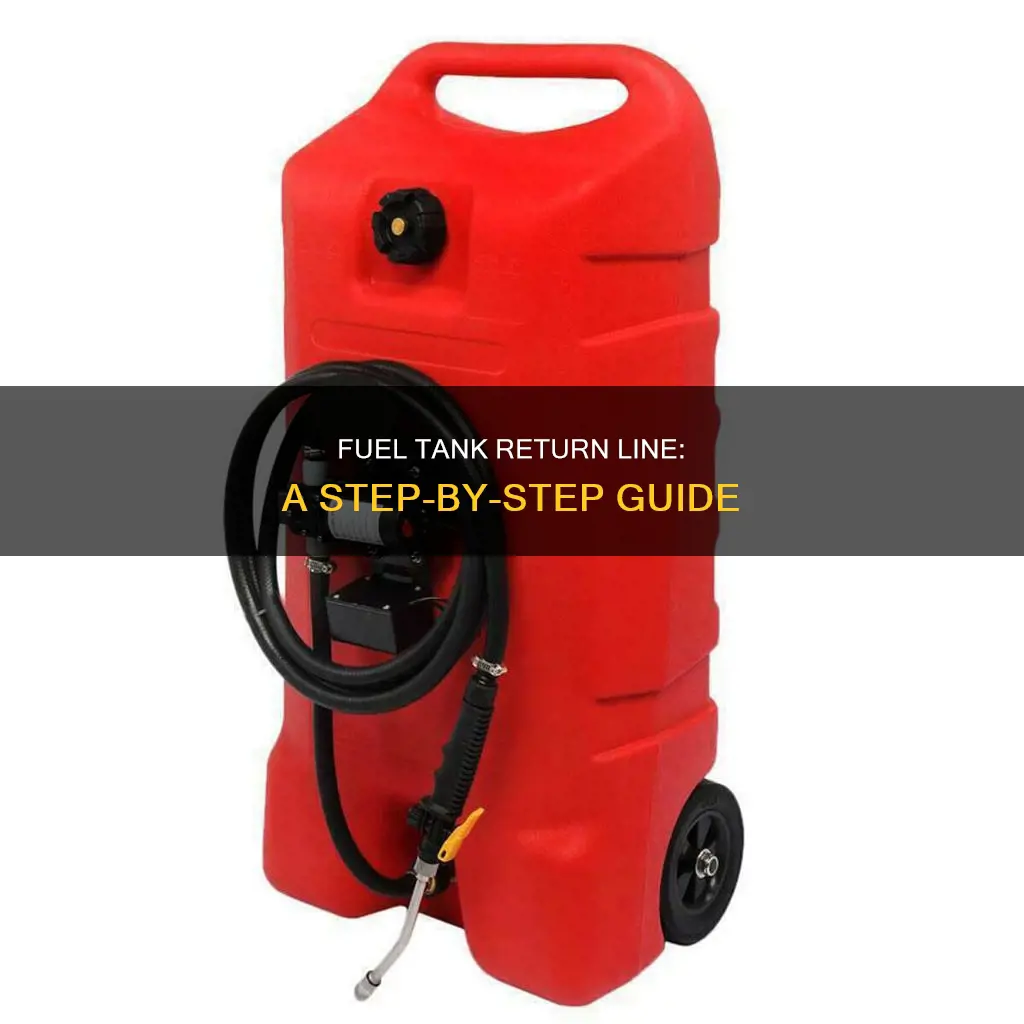
Adding a return line to a portable fuel tank is a crucial step in ensuring efficient fuel management and preventing contamination. This process involves connecting a dedicated line from the tank to the engine's fuel system, allowing fuel to flow back into the tank when not in use. By implementing this simple modification, you can optimize fuel usage, reduce the risk of fuel degradation, and maintain a clean and reliable fuel supply for your portable generator or vehicle. This guide will provide a step-by-step overview of the process, ensuring a successful and safe installation.
What You'll Learn
- Tank Inspection: Check for compatibility and access points before adding a return line
- Line Routing: Plan a path that avoids fuel sloshing and potential leaks
- Fittings and Connections: Use appropriate fittings and ensure tight connections to prevent leaks
- Fuel Compatibility: Verify the return line material is compatible with the fuel type
- Safety Measures: Implement safety checks to prevent fuel spillage and ensure proper installation
Tank Inspection: Check for compatibility and access points before adding a return line
Before attempting to add a return line to your portable fuel tank, it's crucial to conduct a thorough inspection to ensure compatibility and identify any potential access points. This process is essential to guarantee a successful and safe installation. Here's a step-by-step guide to help you through this critical phase:
- Compatibility Check: Begin by confirming that the return line is compatible with your fuel tank. Different tanks have varying sizes, shapes, and mounting configurations. Measure the dimensions of your tank's fuel opening and compare them with the specifications of the return line you intend to use. Ensure that the line's diameter and length are appropriate for a secure fit. Check the manufacturer's guidelines or consult online resources for specific compatibility information related to your tank model.
- Access Point Assessment: Locate the access points on your fuel tank. These are typically small openings or ports designed for maintenance and fueling. Access points can be located on the top, side, or bottom of the tank, depending on the design. Identify the closest and most accessible point to the fuel line's connection, as this will make the installation process easier. Ensure that the chosen access point is not obstructed by any tank components or mounting hardware.
- Inspect for Obstructions: Carefully examine the area around the access point for any potential obstructions. Remove any debris, dirt, or contaminants that might interfere with the return line installation. Check for sharp edges, protruding parts, or existing damage that could affect the line's placement. A clear and unobstructed path is essential to ensure a smooth installation process.
- Consider Tank Material: Different fuel tanks are made from various materials, such as plastic, metal, or composite. The material of your tank can impact the installation process. For example, some materials may require specific tools or techniques to create a secure connection. Research or consult with experts to understand the best practices for your tank's material to ensure a compatible and durable return line setup.
By following these inspection steps, you can ensure that your portable fuel tank is ready for the addition of a return line, minimizing the risk of installation errors and potential issues. Compatibility and access considerations are vital to the success and safety of any fuel system modification.
Fuel Line Woes: When Connectors Unravel
You may want to see also
Line Routing: Plan a path that avoids fuel sloshing and potential leaks
When adding a return line to a portable fuel tank, proper line routing is crucial to prevent fuel sloshing and potential leaks. Here's a detailed guide on how to plan the path of the return line:
- Understand the Tank's Geometry: Begin by visualizing the shape and dimensions of your fuel tank. Note the location of the fuel fill port, the position of the tank's bottom, and any existing lines or components that might interfere with the return line's path. Understanding the tank's geometry will help you anticipate potential issues and plan a route that avoids sharp bends or tight spaces.
- Avoid High-Vibration Areas: Fuel tanks can experience vibrations during transportation or when the vehicle is in motion. To prevent fuel sloshing and potential leaks, route the return line away from high-vibration areas. This might include avoiding direct routes near the engine, suspension components, or any moving parts that could cause the line to rub or vibrate excessively.
- Maintain a Consistent Slope: Aim to maintain a gentle slope for the return line to ensure proper fuel flow. A slight downward slope from the tank to the fuel pump or reservoir will allow gravity to assist in the fuel's return. Avoid sharp upward slopes that could lead to air locking or fuel accumulation.
- Use Flexible Materials: Opt for flexible fuel lines made from materials like rubber or polyurethane. These materials can bend and conform to the tank's shape without kinking or restricting flow. Ensure the lines are not too stiff, as this can make routing difficult and may lead to sharp bends that could cause leaks.
- Secure the Line: Properly secure the return line to the tank and surrounding components using appropriate fasteners or ties. This prevents the line from moving or becoming damaged due to vibration or impact. Avoid tight bends or kinks by allowing the line to move freely around the tank and any obstacles.
- Consider the Pump's Location: If your fuel system includes a pump, ensure the return line is routed to the pump's intake side. This allows the pump to draw fuel from the tank efficiently and prevents the line from becoming a restriction in the fuel flow.
By carefully planning the route of the return line, you can minimize the risk of fuel sloshing, leaks, and potential system issues. Following these guidelines will help ensure a smooth and efficient fuel transfer system in your portable fuel tank setup.
Ethanol's Role in Diesel Fuel: A Comprehensive Overview
You may want to see also
Fittings and Connections: Use appropriate fittings and ensure tight connections to prevent leaks
When adding a return line to a portable fuel tank, ensuring proper fittings and connections is crucial to prevent any leaks and maintain the integrity of the fuel system. The primary goal is to create a secure and leak-free pathway for the fuel to flow back to the tank from the engine or the source of fuel consumption.
Start by selecting the right fittings for your specific fuel tank and return line setup. Fittings should be compatible with the materials used in the fuel tank and lines to avoid any chemical reactions or degradation over time. Common materials for fuel tanks and lines include plastic, rubber, and metal. For example, if your fuel tank is made of plastic, choose fittings made of the same material or a compatible alternative like polypropylene or nylon. Metal fittings can be used for metal tanks, ensuring a secure and durable connection.
The key to a successful connection is a tight seal. Leaks can occur if the fittings are not properly aligned or if there is insufficient force applied to create a secure bond. When connecting the return line to the fuel tank, ensure that the fittings are clean and free of any debris or contaminants. Use a suitable sealant or adhesive, if required, to enhance the connection's strength and prevent leaks. Tighten the fittings securely, but be careful not to overtighten, as this can damage the fittings or the fuel tank.
Consider the type of fittings you need based on the design of your fuel tank and return line. Common fittings include compression fittings, which use a compression nut and sleeve to create a tight seal, and barbed fittings, which feature a barbed end and a compression nut for a secure connection. Some fuel tanks may require specialized fittings, so it's essential to consult the manufacturer's guidelines or seek professional advice if needed.
Additionally, pay attention to the orientation and positioning of the fittings. Ensure that the return line is correctly aligned with the fuel tank's inlet port, allowing for a smooth and efficient flow of fuel. Proper alignment prevents unnecessary strain on the fittings and reduces the risk of leaks. Regularly inspect the connections to identify any signs of wear or damage, especially in high-pressure areas, and replace or repair as necessary to maintain a safe and functional fuel system.
Mastering Diesel Fuel Lines: Regular Maintenance Tips
You may want to see also
Fuel Compatibility: Verify the return line material is compatible with the fuel type
When adding a return line to a portable fuel tank, it's crucial to consider fuel compatibility to ensure the safety and efficiency of your setup. The primary concern here is the material of the return line and its interaction with the fuel type you'll be using. Different fuels have varying chemical compositions, and some materials may not be suitable for all fuel types. For instance, gasoline and diesel have distinct properties, and using the wrong material for the return line can lead to issues.
The return line is responsible for directing the fuel back to the tank after it has been used, and its material directly impacts the fuel's journey. For gasoline, a common choice is a return line made of high-density polyethylene (HDPE) or a similar material that is resistant to gasoline's corrosive effects. HDPE is a good option because it is lightweight, flexible, and can withstand the fuel's properties without degrading over time. On the other hand, diesel fuel requires a different approach. Materials like stainless steel or brass are often preferred for diesel return lines due to their superior resistance to corrosion and the fuel's higher acidity.
To verify compatibility, it's essential to research the specific fuel you'll be using and the recommended materials for return lines. Many manufacturers provide guidelines or even specific part numbers for return lines compatible with their fuel types. Consulting the fuel's documentation or contacting the manufacturer can offer valuable insights. Additionally, understanding the fuel's properties, such as its octane level, additives, and any potential contaminants, is crucial in selecting the right material for the return line.
In some cases, you might need to consider the fuel's temperature and pressure characteristics. For instance, high-pressure diesel fuel may require a more robust material to handle the increased stress. The return line material should be able to withstand the fuel's properties without compromising its integrity or leaking. By carefully selecting the material based on fuel compatibility, you ensure a safe and efficient fuel system.
Remember, using the correct material for the return line is a critical aspect of maintaining a portable fuel tank system. It prevents fuel contamination, ensures proper fuel flow, and minimizes the risk of fuel-related issues. Always prioritize compatibility to guarantee the longevity and reliability of your fuel setup.
Mastering the Art of Fuel Line Removal: A Guide for 1998 Sierra 2500 Owners
You may want to see also
Safety Measures: Implement safety checks to prevent fuel spillage and ensure proper installation
When adding a return line to a portable fuel tank, safety should always be the top priority. Here are some essential safety measures to prevent fuel spillage and ensure a proper installation:
Inspect the Tank and Lines: Before beginning any work, thoroughly inspect the fuel tank and the existing fuel lines. Check for any signs of damage, cracks, or leaks. Ensure that the tank is in good condition and that the lines are intact and free from any blockages. This initial assessment is crucial to identify potential issues and ensure a safe working environment.
Prepare the Necessary Tools: Gather all the required tools and equipment for the installation. This includes wrenches, pliers, fuel line connectors, and any other specialized tools recommended by the manufacturer. Having the right tools will make the process easier and safer, reducing the risk of accidents and errors.
Follow Manufacturer's Guidelines: Adhere to the manufacturer's instructions and specifications for the return line installation. Each fuel tank and line setup may have unique requirements, so it's essential to consult the provided guidelines. These instructions will detail the proper placement of the return line, the type of connectors to use, and any specific safety precautions to take during the installation process.
Secure the Return Line: When installing the return line, ensure it is securely attached to the fuel tank and properly routed. Use appropriate connectors and fittings to create a tight seal. Double-check the connections to guarantee no fuel can leak out. Properly securing the line prevents spills and ensures the system functions as intended.
Test for Leaks: After completing the installation, perform a thorough leak test. Apply a small amount of soapy water or a suitable fuel-system diagnostic fluid to the connections and observe for any bubbles or leaks. This test will help identify any potential issues and ensure that the return line is installed correctly without any fuel leaks.
Regular Maintenance: Implement a regular maintenance routine to keep the fuel system in optimal condition. Check the fuel lines and connections periodically for any signs of wear and tear, corrosion, or damage. Promptly address any issues to prevent fuel leaks and ensure the safety and longevity of the fuel tank and return line system.
By following these safety measures, you can effectively prevent fuel spillage and ensure a successful installation of the return line to your portable fuel tank. It is crucial to prioritize safety throughout the entire process to avoid any potential hazards associated with fuel handling.
Optimizing Performance: Choosing the Right Fuel Line for Your Johnson 200
You may want to see also
Frequently asked questions
A return line is an essential component when using a portable fuel tank, especially for engines that require a constant fuel supply. It allows the fuel to flow back into the tank after it has been used, ensuring that the tank remains full and preventing fuel wastage. This is crucial for maintaining the engine's performance and longevity.
If you notice that your fuel tank is not refilling properly after use, or if you experience fuel starvation during operation, it might be time to consider adding a return line. These issues often arise when the fuel tank is not designed with a return mechanism, leading to inefficient fuel management.
While it is possible to install a return line on a portable fuel tank, it is recommended to seek professional assistance or guidance. Fuel systems can be complex, and improper installation may lead to fuel leaks or engine damage. It's best to consult a qualified mechanic or a professional with experience in fuel system modifications.
The primary advantage is the improved fuel management system, ensuring a constant supply of fuel to the engine. This setup also helps in maintaining a clean fuel system, reducing the risk of fuel contamination and engine issues. Additionally, it provides better control over fuel levels, allowing for more efficient usage and longer operating times.