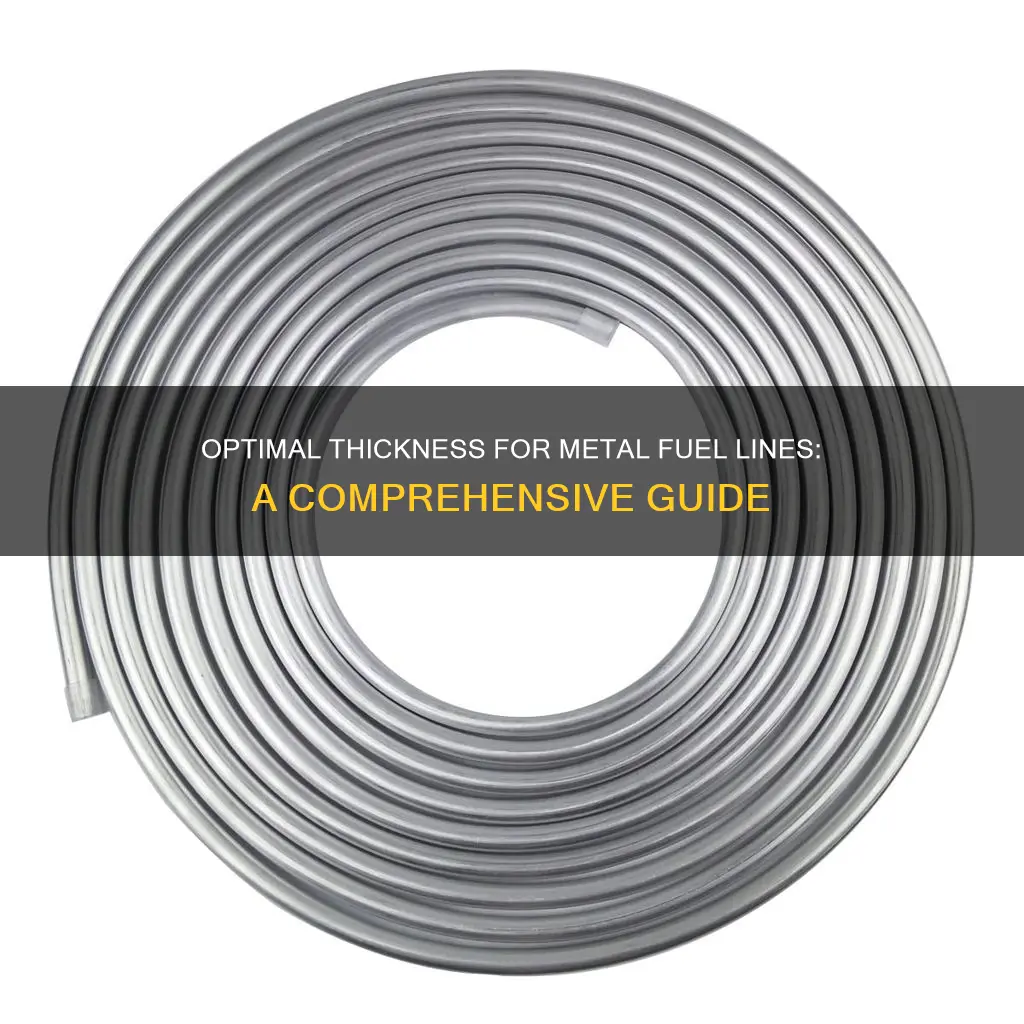
When it comes to metal fuel lines, determining the appropriate thickness is crucial for ensuring optimal performance and safety. The thickness of the metal fuel line plays a significant role in withstanding the pressure and temperature variations associated with fuel transport. In this paragraph, we will explore the factors that influence the ideal thickness of metal fuel lines and provide guidelines to help you make an informed decision for your specific application.
Characteristics | Values |
---|---|
Thickness (in inches) | 0.035 to 0.060 |
Material | Aluminum, Brass, Copper, Stainless Steel |
Temperature Range | -40°F to 300°F (-40°C to 149°C) |
Pressure Rating | Up to 150 psi (pounds per square inch) |
Application | Fuel Injection Systems, Carburetors, Engine Bay |
Color | Silver, Gold, Black |
Flexibility | Moderate to High |
Corrosion Resistance | Excellent |
Compatibility | Gasoline, Ethanol, Diesel |
Cost | Varies based on material and length |
Installation | Easy, requires fuel line connectors |
What You'll Learn
- Material Thickness: Choose metal thickness based on fuel type and pressure
- Line Diameter: Ensure fuel line diameter matches fuel pump requirements
- Flexibility: Opt for flexible metal to avoid damage
- Temperature Resistance: Select material that can withstand fuel temperature extremes
- Safety Standards: Adhere to industry standards for fuel line thickness
Material Thickness: Choose metal thickness based on fuel type and pressure
When it comes to selecting the appropriate thickness for your metal fuel lines, it's crucial to consider the type of fuel you're using and the pressure it will encounter. Different fuels have varying properties, and the pressure within the system can vary significantly. Here's a detailed guide to help you make the right choice:
Understanding Fuel Properties: Different fuels have distinct characteristics that impact the required thickness of the metal fuel lines. For instance, gasoline and diesel have different densities and viscosities, which can affect the flow rate and pressure within the fuel system. Gasoline, being less dense, may flow more easily but can still exert pressure, especially during acceleration. On the other hand, diesel is denser and thicker, requiring more robust fuel lines to handle its higher pressure. Understanding these properties is essential to ensure the fuel lines can withstand the specific demands of the fuel type.
Pressure Considerations: The pressure within the fuel system is a critical factor in determining the thickness of the metal lines. Higher pressure can lead to increased wear and potential damage to the fuel lines over time. For example, in a high-performance engine, the fuel pressure might be significantly higher, requiring thicker metal lines to prevent leaks and ensure safety. Thinner lines may not be able to handle the stress, leading to potential failures. It's important to consult the vehicle's specifications or manufacturer guidelines to determine the recommended pressure levels and choose the appropriate thickness accordingly.
Material Selection: The choice of metal for the fuel lines is also vital. Common materials include steel, aluminum, and copper alloys. Each material has its advantages and is chosen based on the specific requirements of the fuel type and pressure. For instance, steel is known for its strength and durability, making it suitable for high-pressure systems. Aluminum offers lightweight options, which can be beneficial for performance-oriented vehicles. Copper alloys provide excellent corrosion resistance, ensuring a longer lifespan, especially in harsh environments. The material's properties, such as tensile strength and ductility, should be considered to ensure it can withstand the expected stresses.
Industry Standards and Recommendations: Adhering to industry standards and manufacturer recommendations is essential. These guidelines often provide specific thickness requirements based on extensive testing and research. For instance, automotive fuel line standards might specify different thicknesses for various fuel types and engine configurations. Following these standards ensures that your fuel lines meet the necessary safety and performance criteria. It's a good practice to consult the vehicle's manual or seek advice from automotive experts to determine the recommended thickness for your specific application.
By carefully considering the fuel type, pressure, and industry standards, you can select the appropriate metal thickness for your fuel lines, ensuring optimal performance, safety, and longevity of your vehicle's fuel system. Remember, proper thickness is a critical aspect of maintaining a reliable and efficient fuel delivery system.
Unveiling the Mystery: Small Lines Behind Fuel Filter in Cadillac SRX
You may want to see also
Line Diameter: Ensure fuel line diameter matches fuel pump requirements
When it comes to ensuring the proper thickness of your metal fuel line, one critical aspect to consider is the line's diameter. The diameter of the fuel line is directly related to its ability to handle the flow rate required by your fuel pump. It's essential to match the line diameter to the pump's specifications to ensure optimal performance and prevent potential issues.
The fuel pump is a vital component in your vehicle's fuel system, responsible for delivering the required amount of fuel to the engine at the right pressure. If the fuel line's diameter is too small, it may not be able to handle the flow rate, leading to a restriction in fuel delivery. This can result in reduced engine performance, decreased power, and even potential engine damage over time. On the other hand, if the line is too large, it may not be necessary for your application, leading to unnecessary costs and potential installation challenges.
To determine the appropriate diameter, you should refer to your vehicle's manual or consult the manufacturer's specifications for the fuel pump. These sources will provide the recommended line diameter to ensure a proper fit and optimal performance. It's crucial to use the correct size to avoid any compatibility issues and to guarantee that the fuel pump operates efficiently.
In some cases, you might come across fuel pumps with different flow rates, and thus, varying line diameter requirements. For instance, a high-performance fuel pump designed for increased power output may demand a larger diameter line to handle the higher fuel flow. Conversely, a standard pump might require a smaller line. Understanding these variations is essential to make an informed decision when selecting the fuel line.
In summary, matching the fuel line diameter to the pump's requirements is a critical step in ensuring your vehicle's fuel system operates efficiently and reliably. Always refer to the manufacturer's guidelines and specifications to make the right choice for your particular vehicle and fuel pump setup. This attention to detail will contribute to the overall performance and longevity of your engine.
Fuel Line Dimensions: Unveiling the Mystery of Mantis Tiller Sizes
You may want to see also
Flexibility: Opt for flexible metal to avoid damage
When it comes to choosing the right thickness for your metal fuel line, flexibility is a crucial factor that should not be overlooked. Metal fuel lines are designed to transmit fuel from the tank to the engine, and their flexibility is essential to ensure a smooth and safe journey. The primary purpose of this flexibility is to prevent damage to the fuel line during installation, maintenance, and even in the event of minor impacts or vibrations.
Opting for flexible metal is a wise choice as it allows the fuel line to bend and adjust to the natural contours of your vehicle's engine bay. This is particularly important as fuel lines often need to navigate around various components, such as exhaust pipes, engine blocks, and other mechanical parts. A flexible metal fuel line can easily accommodate these twists and turns without kinking or putting excessive strain on the line. This flexibility is especially beneficial when dealing with older vehicles or those with unique engine layouts, where the fuel line might need to make more intricate routes.
The flexibility of the metal also contributes to the overall longevity of the fuel line. Rigid metal lines can become brittle over time, especially when exposed to temperature changes and fuel volatility. This brittleness can lead to cracks or even complete ruptures, resulting in fuel leaks, which are not only dangerous but also costly to repair. By choosing a flexible metal fuel line, you ensure that the line can withstand the natural wear and tear of the vehicle's operation, reducing the risk of premature failure.
Furthermore, the flexibility of the metal fuel line becomes even more critical during installation. Proper installation is essential to ensure a secure and reliable connection, and a flexible line allows for easier maneuvering around tight spaces and complex engine configurations. This ease of installation can save time and effort, making the entire process less stressful for both DIY enthusiasts and professional mechanics.
In summary, when considering the thickness and type of metal fuel line for your vehicle, prioritize flexibility. Flexible metal fuel lines offer the necessary adaptability to navigate through the engine bay without causing damage, ensuring a longer-lasting and more reliable fuel supply system. This simple choice can contribute to a safer and more efficient driving experience.
Mercury Outboard Fuel Line Removal: A Step-by-Step Guide
You may want to see also
Temperature Resistance: Select material that can withstand fuel temperature extremes
When it comes to choosing the right material for your metal fuel line, temperature resistance is a critical factor that should not be overlooked. Fuel lines are exposed to a wide range of temperatures, especially in automotive applications, and the material must be able to withstand these extremes without compromising performance or safety.
Extreme temperatures can cause various issues, such as fuel degradation, line hardening, or even melting, which can lead to dangerous situations. Therefore, selecting a material with excellent temperature resistance is essential. One of the key considerations is the operating temperature range of your fuel system. Different materials have varying limits, and it's crucial to choose a material that can handle the specific temperature fluctuations your application demands. For instance, if your vehicle operates in high-temperature environments, you might need a material that can resist temperatures above 300°F (150°C).
Materials like stainless steel and aluminum alloys are often preferred for their temperature resistance. Stainless steel, in particular, offers excellent durability and can withstand both high and low temperatures without significant degradation. It is commonly used in fuel lines due to its ability to resist corrosion and maintain its structural integrity over a wide temperature range. Aluminum alloys, on the other hand, provide a lightweight solution while still offering reasonable temperature resistance, making them suitable for certain applications.
Another important aspect is the material's ability to resist thermal expansion and contraction. Fuel lines need to accommodate temperature changes without becoming brittle or prone to cracking. Materials with low thermal expansion coefficients are ideal, ensuring that the fuel line maintains its flexibility and remains intact even when exposed to rapid temperature fluctuations. This is especially crucial in high-performance vehicles or those operating in extreme climates.
Additionally, consider the fuel type and its potential impact on material selection. Different fuels have varying properties, and some may require materials with specific temperature resistance characteristics. For example, ethanol-blended fuels might demand materials that can withstand higher temperatures to prevent fuel line damage. Always refer to the manufacturer's guidelines and consult experts to ensure you choose the most suitable material for your fuel line's temperature resistance requirements.
Half-Inch Double Bead Fuel Line: Top Sources Revealed
You may want to see also
Safety Standards: Adhere to industry standards for fuel line thickness
When it comes to fuel lines, safety should always be the top priority. Adhering to industry standards for fuel line thickness is crucial to ensure the reliable and safe operation of your vehicle. These standards are in place to prevent potential hazards such as fuel leaks, which can lead to dangerous situations.
The thickness of a metal fuel line is determined by various factors, including the type of vehicle, the fuel system design, and the specific requirements of the manufacturer. Industry standards, such as those set by the Society of Automotive Engineers (SAE) and the American Society of Mechanical Engineers (ASME), provide guidelines for the minimum thickness required for different fuel line applications. These standards take into account the operating pressures, temperatures, and potential hazards associated with the fuel system.
For example, in high-performance vehicles or those with high-pressure fuel systems, thicker fuel lines may be recommended to withstand the increased stress and potential for damage. Thicker lines can also provide better protection against punctures and abrasion, ensuring that the fuel remains contained and secure. It is essential to consult the vehicle's manual or seek professional advice to determine the specific thickness required for your fuel line.
Adhering to these safety standards is vital as it directly impacts the overall safety and performance of your vehicle. Non-compliance may result in fuel leaks, which can cause engine misfires, reduced performance, and even pose a fire hazard. By using the correct thickness, you ensure that the fuel lines can handle the demands of the system, providing a reliable and safe fuel supply.
In summary, when considering the thickness of your metal fuel line, always refer to industry standards and manufacturer recommendations. This ensures that your fuel system meets the necessary safety requirements, minimizing the risk of accidents and ensuring the longevity of your vehicle's performance. Remember, investing in the right thickness is an investment in your safety and the reliability of your vehicle's fuel system.
Mastering Motorcycle Fuel Line Removal: A Step-by-Step Guide
You may want to see also
Frequently asked questions
The thickness of a metal fuel line is influenced by several factors, including the type of fuel being used, the operating pressure, the temperature range, and the specific application. Different fuels have varying properties, such as density and volatility, which can impact the line's required thickness to ensure safe and efficient operation.
Operating pressure plays a critical role in determining the thickness of the metal fuel line. Higher pressure can lead to increased stress on the line, requiring thicker material to withstand the force without compromising integrity. Engineers consider the maximum expected pressure to select an appropriate gauge thickness.
Temperature is a crucial factor as it can affect the material's performance and durability. Extreme temperatures may cause expansion or contraction of the metal, leading to potential damage. Thicker lines are often used in high-temperature environments to accommodate thermal expansion and ensure the line's structural integrity.
Thickness is essential for various applications, such as automotive or aviation. In high-performance vehicles, thicker lines might be required to handle increased fuel flow rates and pressure. Conversely, in smaller, low-power applications, thinner lines may be sufficient, but still need to meet the required pressure and temperature specifications.
Yes, industry standards and guidelines provide recommendations for fuel line thickness. These standards are often based on extensive research and testing to ensure safety and performance. For example, the Society of Automotive Engineers (SAE) and the American Society of Mechanical Engineers (ASME) offer guidelines that can be referenced for specific applications.