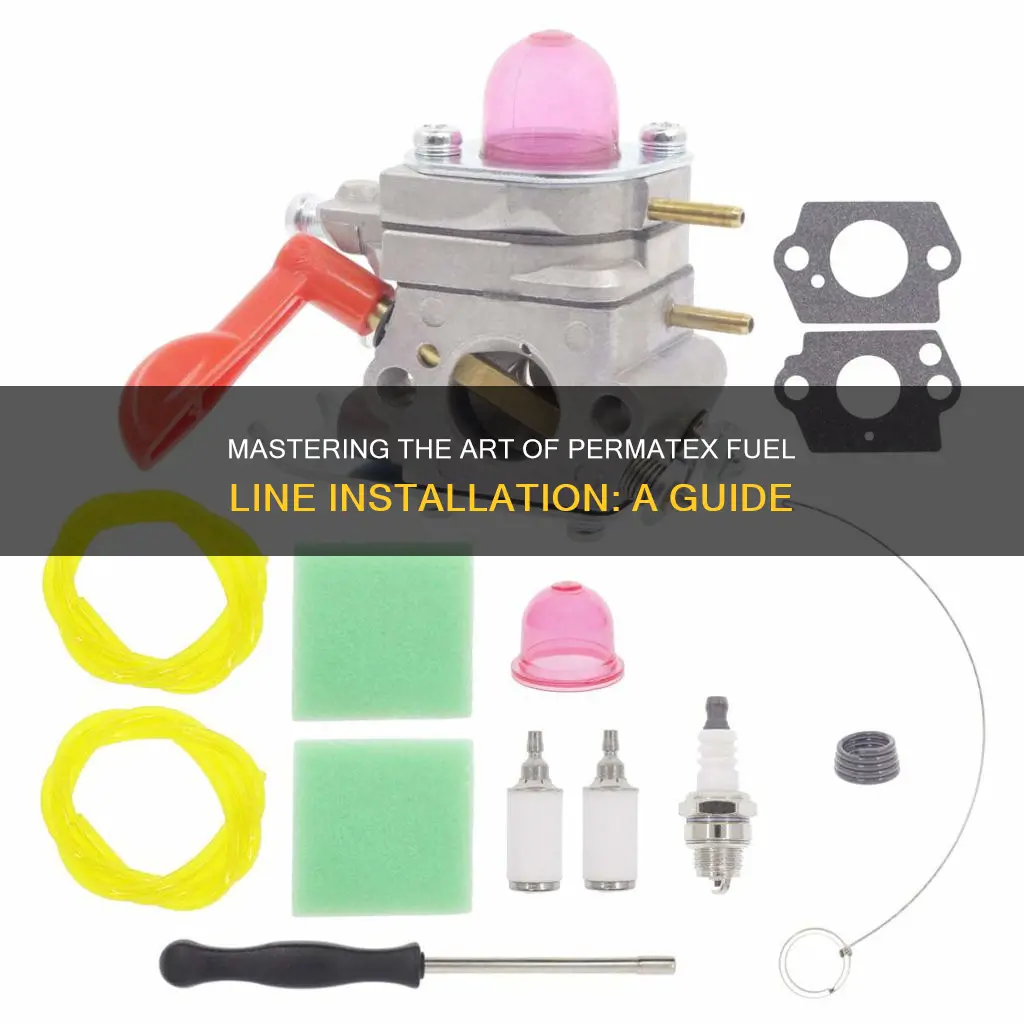
When working on a carburetor, ensuring the fuel line is properly connected and secured is crucial for optimal engine performance. Permatex, a versatile silicone-based compound, is commonly used to create a tight seal between the fuel line and the carburetor. This process involves carefully cleaning the surfaces, applying a thin layer of Permatex, and then using a tool to create a secure bond. Properly permatexing the fuel line helps prevent fuel leaks, ensures a reliable fuel supply to the engine, and contributes to the overall longevity of the vehicle's mechanical components.
Characteristics | Values |
---|---|
Permatex Application | Apply Permatex (a brand of silicone-based thread seal tape) to the fuel line and carburetor connection to ensure a secure and leak-free seal. |
Cleanliness | Ensure the fuel line and carburetor are clean and free of any debris or old Permatex residue before application. |
Amount of Permatex | Use a small amount of Permatex, enough to cover the threads and create a thick layer around the connection. |
Application Technique | Wrap the Permatex around the threads in a clockwise direction, ensuring full coverage. Avoid applying too much pressure. |
Drying Time | Allow the Permatex to dry for the recommended time, typically a few hours, before reassembling the carburetor. |
Reassembly | Reattach the carburetor and fuel line, ensuring a tight fit. Check for leaks and verify proper functionality. |
Maintenance | Periodically inspect and reapply Permatex if necessary to maintain a secure connection. |
Compatibility | Ensure Permatex is compatible with the fuel line material to avoid any potential damage. |
Safety Precautions | Wear gloves and work in a well-ventilated area when applying Permatex to avoid inhaling fumes. |
What You'll Learn
- Fuel Line Material: Choose the right material for the fuel line, considering factors like temperature resistance and flexibility
- Clamping: Secure the fuel line with appropriate clamps to prevent leaks and ensure a tight fit
- Routing: Route the fuel line away from heat sources and vibrations to prevent damage
- Length: Ensure the fuel line is the correct length to reach the carburetor without excessive slack
- Testing: Test the fuel line for leaks and proper functionality after installation
Fuel Line Material: Choose the right material for the fuel line, considering factors like temperature resistance and flexibility
When it comes to choosing the right material for your fuel line, especially for a carburetor setup, there are several key factors to consider. Firstly, temperature resistance is crucial. Fuel lines are exposed to varying temperatures, especially in engines that operate in different climates or conditions. The material should be able to withstand both extreme cold and high heat without becoming brittle or losing its flexibility. For this reason, rubber or silicone-based materials are often preferred as they offer a good balance of temperature resistance and durability. These materials can handle the expansion and contraction that occurs with temperature changes without cracking or leaking.
Flexibility is another essential characteristic of fuel line material. Fuel lines need to be able to move and bend as the engine operates, especially in older vehicles where the carburetor is often located lower than the fuel tank. A flexible material ensures that the line can accommodate these movements without kinking or breaking. Materials like rubber or braided stainless steel are excellent choices here, as they provide the necessary flexibility while also maintaining a certain level of rigidity to prevent excessive sagging or bending.
Additionally, the material should be resistant to fuel degradation. Over time, certain fuels can cause rubber to degrade, leading to cracks and leaks. Choosing a material that is specifically designed to resist fuel-related degradation is important. For instance, some fuel lines use a layer of protective coating or a specific type of rubber that is less susceptible to fuel-related damage. This ensures the long-term reliability and safety of the fuel system.
In some cases, a combination of materials might be used to optimize the fuel line's performance. For example, a rubber inner tube could be combined with a protective outer layer of braided stainless steel for added flexibility and corrosion resistance. This hybrid approach can provide the best of both worlds, ensuring the fuel line can withstand various conditions while maintaining its integrity.
Lastly, it's important to consider the installation process and the overall design of the fuel system. Some materials might require specific tools or techniques for a secure and leak-free installation. Understanding the compatibility of the chosen material with the existing fuel system components is essential to ensure a successful and safe repair or upgrade.
Fuel Line Fix: A Guide to Repairing 1992 Dodge Dakota's Leaks
You may want to see also
Clamping: Secure the fuel line with appropriate clamps to prevent leaks and ensure a tight fit
When working on a carburetor, ensuring a secure and leak-free fuel line connection is crucial for optimal engine performance. Clamping is a critical step in this process, providing a reliable and durable solution to keep the fuel line in place. Here's a detailed guide on how to properly clamp the fuel line:
Start by selecting the right type of clamp for your specific application. The choice of clamp depends on various factors, including the diameter of the fuel line, the material it's made of, and the overall design of the carburetor. Common types of clamps used for fuel lines include stainless steel bands, metal clips, or rubber-lined clamps. Ensure that the clamp you choose is compatible with the fuel line's specifications to achieve a secure and leak-free connection.
Position the fuel line carefully, ensuring it is routed correctly and away from any potential sources of vibration or damage. Once the line is in the desired position, it's time to apply the clamp. Slide the clamp onto the fuel line, making sure it covers the entire length of the line where it connects to the carburetor. The clamp should be positioned in a way that it securely holds the line without causing any kinks or bends that could lead to damage.
To secure the clamp, start by tightening it gently by hand. This initial tightening ensures that the clamp makes contact with the fuel line and provides a foundation for further adjustment. Then, using a wrench or a specialized tool designed for clamping, tighten the clamp further. The goal is to achieve a firm and even grip without applying excessive force, as this could damage the fuel line or carburetor. Take your time and use controlled movements to ensure a precise fit.
After tightening the clamp, inspect the fuel line for any signs of movement or play. If the line is secure and doesn't move when gently tugged, you've likely achieved a successful clamp. However, if there's any movement, you may need to make minor adjustments by slightly loosening the clamp and re-tightening it to find the perfect fit. Remember, the goal is to create a tight seal that prevents fuel leaks while allowing the line to move freely without any restrictions.
By following these clamping techniques, you can ensure that the fuel line is securely attached to the carburetor, minimizing the risk of leaks and optimizing engine performance. Proper clamping is a fundamental aspect of carburetor maintenance and should be given careful attention to maintain the overall health and efficiency of the engine.
Can Fuel Lines Rust? Uncovering the Truth
You may want to see also
Routing: Route the fuel line away from heat sources and vibrations to prevent damage
When working on a carburetor and installing a fuel line, proper routing is crucial to ensure the longevity and reliability of the system. One essential aspect of this process is routing the fuel line away from potential sources of heat and vibrations. This practice is vital to prevent damage to the fuel line and maintain the overall performance of the engine.
Heat sources are a significant concern as they can cause the fuel line to expand and contract rapidly, leading to potential cracks or leaks. It is recommended to route the fuel line away from hot engine components, such as exhaust manifolds, headers, and even the engine block itself. By keeping the fuel line at a safe distance from these heat sources, you minimize the risk of thermal stress and potential failure. For example, if your carburetor is located near the front of the engine, ensure the fuel line is routed away from the engine's front side, where it might come into contact with hot exhaust components.
Vibrations from the engine's operation can also take a toll on the fuel line. The constant movement and shaking of the engine can cause the fuel line to rub against other components, leading to wear and potential damage. To mitigate this, it is advised to route the fuel line away from areas where it might come into contact with the engine's moving parts. This could include areas near the timing belt, camshaft, or any other components that vibrate during operation. By keeping the fuel line secure and away from these vibration-prone areas, you ensure its stability and reduce the chances of damage.
To achieve this, consider using rubber or plastic ties to secure the fuel line in place. These ties can be wrapped around the fuel line at regular intervals, providing support and preventing it from coming into contact with hot or vibrating components. Additionally, ensure that the fuel line is not tightly bent or kinked, as this can also lead to damage over time.
By following these routing guidelines, you create a protective barrier around the fuel line, safeguarding it from the detrimental effects of heat and vibrations. This simple yet effective practice contributes to the overall reliability and performance of your carburetor system.
Dirt Bike Fuel Line Sizing: Essential Guide for Optimal Performance
You may want to see also
Length: Ensure the fuel line is the correct length to reach the carburetor without excessive slack
When working on a carburetor, ensuring the fuel line is the correct length is crucial for optimal performance and reliability. The fuel line should be long enough to reach the carburetor without any excessive slack, as this can lead to issues such as reduced fuel flow and potential engine misfires. Here's a detailed guide on how to achieve the right length:
Start by removing the old fuel line and carefully measuring the distance from the fuel tank to the carburetor. Take note of any bends or angles in the line, as these can affect the overall length. It's important to have a precise measurement to ensure a proper fit. When purchasing a replacement fuel line, select one that matches this length. A line that is too short will restrict fuel flow, while an overly long one may cause unnecessary movement and potential damage.
The ideal fuel line should be taut when connected to the carburetor and the fuel tank. You should not be able to bend it excessively without causing strain on the connections. If the line has too much slack, it can lead to fuel sloshing and air entering the line, resulting in poor engine performance. To ensure the correct length, consider the mounting points and any potential adjustments that can be made to the line's position. Sometimes, a slight modification to the mounting hardware can help achieve the desired tension.
During the installation process, pay close attention to the routing of the new fuel line. It should follow a path that avoids sharp bends and potential damage. Proper routing ensures that the line remains taut and minimizes the risk of kinking, which can restrict fuel flow. Take the time to plan the route, considering the engine's layout and any obstructions.
In summary, achieving the correct length for the fuel line is essential for a successful carburetor repair or modification. By taking accurate measurements, selecting the right-length replacement line, and ensuring proper tension and routing, you can optimize fuel delivery to the engine. This attention to detail will contribute to improved engine performance and reliability.
Fuel Line Protests: Dakota's Burning Questions
You may want to see also
Testing: Test the fuel line for leaks and proper functionality after installation
After completing the installation of the Permatex on the fuel line of your carburetor, it's crucial to thoroughly test the system to ensure its effectiveness and reliability. The primary goal of this test is to identify and address any potential leaks or issues that might compromise the engine's performance. Here's a step-by-step guide on how to conduct this test:
Step 1: Prepare the Vehicle: Ensure the engine is cool to the touch, as hot engines can cause the fuel to expand, leading to false positives during the test. Park the vehicle on a level surface to facilitate accurate readings.
Step 2: Inspect the Fuel Line: Visually inspect the fuel line for any visible signs of damage, cracks, or disconnections. Even small punctures can lead to significant issues during operation. Pay close attention to the areas where the fuel line connects to the carburetor and any other components.
Step 3: Apply a Leak Detection Fluid: A common and effective method is to use a liquid leak detector, such as a soapy water solution or a commercial leak detection fluid. Carefully apply this solution to the fuel line, ensuring it covers all connections and potential leak points. Allow a sufficient amount of time for the fluid to dry, typically a few minutes.
Step 4: Start the Engine: With the leak detection fluid applied, start the engine and let it run for a few minutes. Observe the engine's behavior and listen for any unusual noises. If the engine runs smoothly without any sputtering or hesitation, it's a positive sign. However, if you notice any leaks or bubbles forming on the surface of the leak detection fluid, it indicates a potential issue.
Step 5: Check for Leaks: After the engine has been running, inspect the fuel line again. Look for any signs of fuel seeping or dripping, especially around the connections. If you find any leaks, it's essential to recheck the installation and ensure all components are properly secured. In some cases, you might need to adjust the fuel line's position or tighten connections.
Step 6: Evaluate Functionality: Beyond leak detection, assess the fuel line's functionality. Check for any signs of fuel pressure issues, such as an engine that struggles to start or idles erratically. Ensure that the fuel line is not restricting the flow, which could lead to poor engine performance.
Step 7: Document and Adjust: If any issues are identified, document them for future reference. Make the necessary adjustments to the fuel line's installation, ensuring all connections are secure and the line is properly routed. Re-test the system to confirm the problem has been resolved.
By following these testing procedures, you can ensure that the Permatex-treated fuel line is functioning correctly and securely, contributing to the overall reliability and performance of your carburetor-equipped engine.
Copper Nickel Fuel Lines: Legal in PA? Uncover the Truth
You may want to see also
Frequently asked questions
To ensure a successful installation, start by cleaning the fuel line thoroughly. Remove any old fuel, debris, or contaminants using a fuel line cleaner or a mild solvent. This step is crucial to ensure a proper bond and prevent any potential leaks.
Apply a thin, even layer of Permatex along the entire length of the fuel line, making sure to cover the entire surface. Use a small brush or your fingers to spread the sealant evenly, ensuring it forms a continuous barrier. Avoid applying too much pressure, as it may cause the sealant to bulge or distort the line.
It is recommended to allow sufficient time for the Permatex to cure before reassembling the fuel line. Typically, Permatex requires a few hours to develop its full bonding strength. After curing, you can safely reuse the fuel line, but it's essential to test the system for any leaks before operating the vehicle.
Yes, when applying Permatex, focus on the connection points and ensure a generous amount is applied to both surfaces. Use a small brush to spread the sealant, creating a smooth, continuous layer. Allow the Permatex to cure according to the manufacturer's instructions, and then reassemble the carburetor, ensuring a tight and secure fit.