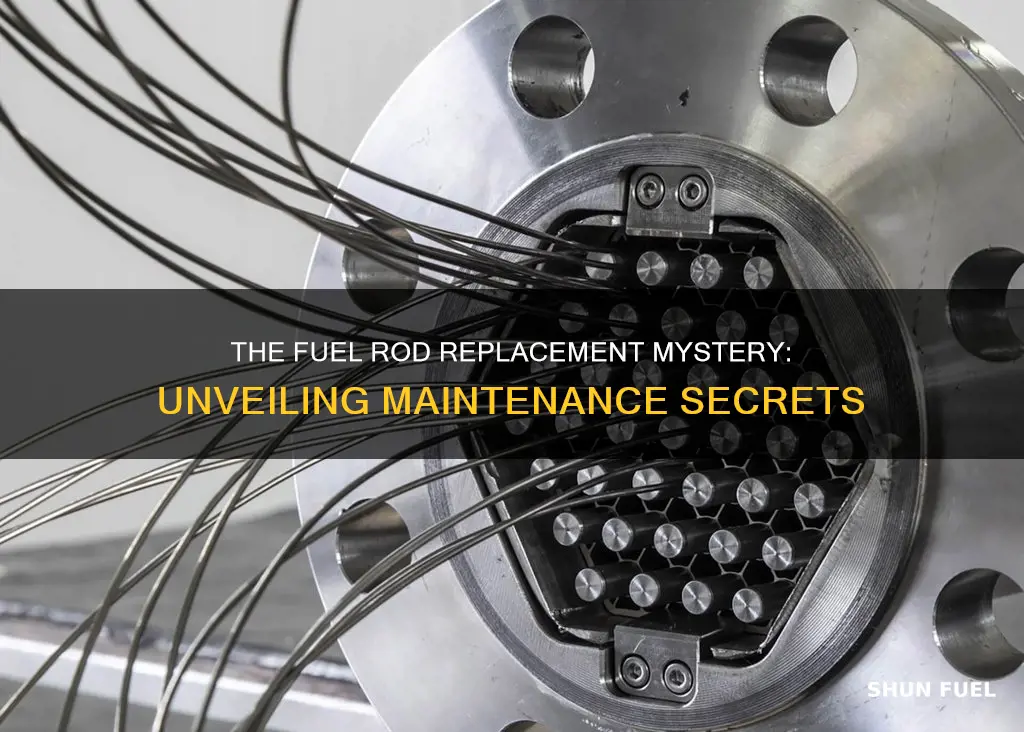
The replacement of fuel rods in nuclear reactors is a critical aspect of maintaining the facility's safety and efficiency. These rods, which are essential for the nuclear fission process, are typically replaced every 12 to 18 months. The frequency of replacement depends on various factors, including the reactor's design, the type of fuel used, and the specific operating conditions. Regularly replacing fuel rods ensures that the reactor operates at optimal performance, minimizing the risk of accidents and maximizing energy output while adhering to strict safety protocols.
Characteristics | Values |
---|---|
Frequency | Varies widely depending on the reactor type, design, and operating conditions. Generally, fuel rods are replaced every 12 to 18 months in pressurized water reactors (PWRs) and every 6 to 12 months in boiling water reactors (BWRs). |
Replacement Process | Fuel rod replacement is a complex procedure that involves removing the used fuel, inspecting and handling it safely, and inserting new fuel rods. This process requires specialized equipment and trained personnel. |
Safety Considerations | The replacement of fuel rods is a critical operation to ensure nuclear safety. It involves handling radioactive materials and requires strict adherence to protocols to prevent contamination and accidents. |
Maintenance and Upgrades | Regular fuel rod replacement is essential for maintaining reactor performance, efficiency, and safety. It allows for the removal of degraded fuel, ensuring the reactor operates within optimal parameters. |
Cost | The cost of fuel rod replacement can vary significantly. It includes expenses for fuel procurement, transportation, handling, and disposal, as well as labor and equipment maintenance. |
Environmental Impact | Proper disposal and handling of used fuel rods are crucial to minimize environmental risks. This includes long-term storage and potential reprocessing or disposal in specialized facilities. |
What You'll Learn
- Fuel Rod Replacement Frequency: Determine the optimal replacement schedule based on reactor design and operational factors
- Maintenance and Inspection Protocols: Establish procedures for regular inspections to assess rod integrity and performance
- Fuel Rod Life Expectancy: Understand the factors influencing the lifespan of fuel rods and their impact on reactor operations
- Replacement Methods and Techniques: Explore various methods for replacing fuel rods, including robotic systems and human intervention
- Regulatory Compliance and Standards: Adhere to industry regulations and guidelines for fuel rod replacement to ensure safety and efficiency
Fuel Rod Replacement Frequency: Determine the optimal replacement schedule based on reactor design and operational factors
The frequency of fuel rod replacement is a critical aspect of nuclear reactor management, directly impacting the plant's performance, safety, and longevity. This process involves removing spent or degraded fuel rods and replacing them with new ones to maintain the reactor's efficiency and ensure the safe generation of nuclear power. The optimal replacement schedule is determined by a combination of factors, including reactor design, operational conditions, and the specific characteristics of the fuel rods used.
Reactor design plays a pivotal role in dictating the replacement frequency. Different reactor types, such as pressurized water reactors (PWRs) or boiling water reactors (BWRs), have distinct fuel rod configurations and cooling systems. For instance, PWRs typically use fuel rods with a higher thermal conductivity, allowing for more efficient heat transfer and potentially extending the operational life of the rods. In contrast, BWRs may require more frequent replacements due to the direct contact between the fuel and water, leading to faster degradation. The geometry and materials of the fuel rods also influence their performance and durability, with factors like rod diameter, cladding thickness, and fuel enrichment level affecting the replacement schedule.
Operational factors are another critical consideration. The reactor's power output, cooling water flow rate, and operating temperature directly impact fuel rod degradation. Higher power outputs can lead to increased thermal stress on the fuel rods, potentially reducing their lifespan. Similarly, variations in cooling water flow can affect the rod's ability to dissipate heat, with inadequate cooling potentially causing premature failure. The reactor's operational history, including maintenance records and any previous issues, also provides valuable insights into the fuel rod's performance and helps in establishing a realistic replacement schedule.
The specific characteristics of the fuel rods themselves are essential in determining the replacement frequency. Fuel rod manufacturers provide detailed specifications, including the expected burnup, power density, and thermal-hydraulic performance. These parameters help predict the rod's degradation rate and guide the replacement strategy. For instance, fuel rods with higher burnup capabilities may have a longer operational life but may also require more stringent safety measures during replacement. Understanding the fuel rod's performance characteristics allows operators to make informed decisions about the replacement schedule, ensuring the reactor operates within safe and efficient parameters.
In summary, the optimal replacement schedule for fuel rods is a complex process that requires a comprehensive understanding of the reactor's design, operational conditions, and the fuel rod's specific attributes. By carefully considering these factors, nuclear power plant operators can ensure the safe and efficient operation of the reactor while minimizing downtime and maintenance costs. This approach also contributes to the overall reliability and sustainability of nuclear energy production.
Chevy Malibu Fuel Filter: A Step-by-Step Guide to a Smooth Ride
You may want to see also
Maintenance and Inspection Protocols: Establish procedures for regular inspections to assess rod integrity and performance
In the realm of nuclear power generation, the maintenance and inspection of fuel rods are critical components of ensuring the safety and efficiency of the overall system. Establishing comprehensive protocols for regular inspections is essential to assess the integrity and performance of these rods, which are the heart of the nuclear fuel cycle. The frequency and nature of these inspections should be tailored to the specific design and operating conditions of the reactor, but a general framework can be outlined to guide these practices.
The inspection process should begin with a detailed plan that outlines the specific areas and components of the fuel rods to be examined. This plan should consider the unique characteristics of the reactor design, including the type of fuel rods used (e.g., uranium dioxide, mixed oxide), their dimensions, and the arrangement within the reactor core. For instance, in pressurized water reactors (PWRs), the fuel rods are typically arranged in bundles, and each bundle's integrity needs to be assessed individually. The inspection plan should also define the tools and techniques to be employed, such as ultrasonic testing, visual inspections, and radiographic analysis, to ensure a comprehensive evaluation.
Regular inspections are vital to detect any signs of degradation, damage, or performance issues with the fuel rods. These inspections can be categorized into two main types: in-service inspections and out-of-service inspections. In-service inspections are conducted while the rods are still in the reactor, allowing for real-time data collection and immediate action if defects are found. This can include visual inspections using specialized cameras and instruments to assess the condition of the cladding, fuel pellets, and other components. Out-of-service inspections, on the other hand, are performed after the rods are removed from the reactor, providing a more detailed examination of the entire rod structure.
The frequency of these inspections is a critical aspect of the maintenance protocol. It is generally recommended that in-service inspections be conducted at regular intervals, such as every 12 to 18 months, depending on the reactor's design and operating history. Out-of-service inspections may be less frequent, typically every 2 to 5 years, but this can vary based on the specific requirements of the reactor and the fuel rod design. Advanced monitoring systems and sensors can also be employed to provide continuous data on rod performance, allowing for more dynamic inspection scheduling.
In addition to the inspection frequency, the data collected during these processes should be thoroughly analyzed to establish performance benchmarks and identify any anomalies. This analysis can help in predicting rod behavior over time and making informed decisions regarding maintenance and replacement strategies. For instance, if a pattern of cladding wear is detected, it may indicate a need for more frequent inspections or a design modification to improve rod longevity. By adhering to these maintenance and inspection protocols, nuclear power plants can ensure the safe and efficient operation of fuel rods, contributing to the overall reliability of the nuclear energy sector.
Fuel Filter Replacement: Essential Tools and Steps
You may want to see also
Fuel Rod Life Expectancy: Understand the factors influencing the lifespan of fuel rods and their impact on reactor operations
The lifespan of fuel rods in nuclear reactors is a critical aspect of reactor design and operation, and it significantly influences the overall efficiency and safety of the facility. Fuel rods, which are cylindrical components containing uranium or plutonium, play a vital role in the nuclear fission process, where they undergo a series of chemical and physical changes over time. Understanding the factors that affect their longevity is essential for optimizing reactor performance and ensuring the safe and efficient generation of nuclear power.
The life expectancy of fuel rods is primarily determined by the accumulation of damage during their operational cycle. This damage can be categorized into two main types: thermal damage and radiation damage. Thermal damage occurs due to the intense heat generated during the fission process, leading to the expansion and eventual degradation of the fuel rod materials. Radiation damage, on the other hand, results from the interaction of high-energy particles with the fuel rod structure, causing changes in the material's microstructure and properties. The cumulative effect of these damages can lead to a reduction in the rod's structural integrity and performance.
Several factors contribute to the overall lifespan of fuel rods. Firstly, the initial quality and composition of the fuel material play a crucial role. Higher-quality fuel with improved purity and uniformity tends to have a longer operational life. Additionally, the design and manufacturing processes of the fuel rods themselves are essential. Advanced manufacturing techniques can enhance the mechanical strength and resistance to radiation of the rods, thereby extending their service life. The reactor's operating conditions, such as temperature, pressure, and coolant flow rate, also significantly impact fuel rod longevity. Optimizing these conditions can minimize thermal and radiation damage, allowing for extended rod usage.
The frequency of fuel rod replacement is a critical consideration in reactor operations. As fuel rods age, their performance degrades, leading to a decrease in power output and an increase in the risk of reactor malfunctions. The replacement interval is typically determined by the accumulated damage and the desired level of performance maintenance. Regularly replacing fuel rods ensures that the reactor operates at peak efficiency and reduces the likelihood of unexpected failures. However, the replacement process itself is complex and requires specialized equipment and trained personnel to handle the radioactive materials safely.
In summary, the life expectancy of fuel rods is influenced by various factors, including the quality of fuel, rod design, reactor operating conditions, and the accumulation of thermal and radiation damage. Optimizing these factors can significantly impact the frequency of fuel rod replacement, which is essential for maintaining reactor efficiency and safety. Understanding these aspects is crucial for nuclear power plant operators and engineers to ensure the reliable and sustainable operation of nuclear reactors.
LLY Duramax Fuel Filter Replacement: A Step-by-Step Guide
You may want to see also
Replacement Methods and Techniques: Explore various methods for replacing fuel rods, including robotic systems and human intervention
The replacement of fuel rods in nuclear reactors is a critical process that ensures the safe and efficient operation of these facilities. The frequency of replacement depends on various factors, including the reactor design, the type of fuel used, and regulatory requirements. Typically, fuel rods are replaced every 12 to 18 months, but this can vary. The process is intricate and often requires specialized equipment and trained personnel to handle the radioactive materials safely.
One of the primary methods employed for fuel rod replacement is through the use of robotic systems. These robotic arms are designed to navigate the complex interior of the reactor vessel and precisely locate the fuel rods that need to be replaced. Robotic systems offer several advantages, including improved safety for operators as they can be controlled remotely, reducing exposure to radiation. These robots are equipped with specialized tools such as grippers and cutting mechanisms to carefully remove the old fuel rods and insert new ones. The precision of these robotic systems is crucial to ensure that the replacement process is accurate and minimizes the risk of damage to the reactor components.
Human intervention is still an essential aspect of fuel rod replacement, especially in the initial stages of the process. Skilled technicians and engineers work alongside the robotic systems to oversee the operation and make real-time adjustments. Human operators use advanced control panels to guide the robots, ensuring that the replacement is carried out according to the predetermined plan. This collaboration between humans and robots is a sophisticated approach that maximizes efficiency and safety.
The replacement process begins with the careful removal of the old fuel rods, a task that requires meticulous planning and execution. Specialized tools are used to disconnect the fuel rods from their support structures, and the used fuel is then carefully handled and stored in appropriate containers. This step is crucial to prevent any potential contamination and to maintain the integrity of the reactor's systems. Once the old fuel is removed, the new fuel rods are carefully positioned and secured in place, ensuring they are correctly aligned and firmly attached.
In addition to the use of robotic systems and human intervention, the replacement process also involves rigorous testing and inspection. Non-destructive testing methods, such as ultrasonic and radiographic inspections, are employed to verify the integrity of the new fuel rods and the surrounding components. These tests ensure that the replacement was successful and that no damage or defects have occurred during the process. The entire replacement cycle is a complex and well-regulated procedure, designed to maintain the highest standards of safety and performance in nuclear power plants.
Replacing Fuel Pump in 02 Spectra: Step-by-Step Guide
You may want to see also
Regulatory Compliance and Standards: Adhere to industry regulations and guidelines for fuel rod replacement to ensure safety and efficiency
The replacement of fuel rods in nuclear power plants is a critical process that is heavily regulated to ensure the safety and efficiency of the facility. Industry regulations and guidelines provide a framework for determining when and how fuel rods should be replaced, aiming to maintain optimal performance while minimizing risks. These standards are designed to address the unique challenges associated with nuclear fuel, which, when used, undergoes significant changes in composition and performance over time.
Regulatory bodies, such as the Nuclear Regulatory Commission (NRC) in the United States, set forth specific requirements for fuel rod replacement. These guidelines often consider factors such as the type of fuel, the reactor design, and the operating history of the plant. For instance, the NRC's regulations mandate that fuel assemblies be replaced when they have reached their design-specific burnup limits, which are determined based on extensive research and testing. These limits are carefully chosen to balance the need for efficient energy production with the requirement to prevent excessive wear and potential safety hazards.
Industry standards also emphasize the importance of regular inspection and monitoring of fuel rods. This includes visual inspections to identify any physical damage or degradation, as well as more advanced techniques like eddy current testing and ultrasonic inspection to detect internal defects. By adhering to these inspection protocols, plant operators can identify potential issues before they become critical, allowing for timely replacement and maintenance.
Furthermore, regulatory compliance often involves the implementation of a comprehensive maintenance program. This program should include scheduled replacement cycles, where fuel rods are taken out of service at predetermined intervals, regardless of their current condition. This proactive approach ensures that the plant maintains a consistent level of performance and safety, even if the fuel rods have not yet reached their maximum operational limits.
In summary, adhering to industry regulations and guidelines for fuel rod replacement is essential for nuclear power plants to operate safely and efficiently. These standards provide a structured approach to managing fuel rod performance, ensuring that replacements are conducted at optimal intervals and that the plant's overall integrity is maintained. By following these regulations, plant operators can contribute to the reliability and sustainability of nuclear energy while minimizing potential risks.
Replacing Air-Fuel Ratio Sensors in Older Vehicles
You may want to see also
Frequently asked questions
The replacement frequency of fuel rods in a nuclear reactor depends on various factors, including the type of reactor, its design, and the specific operating conditions. Typically, fuel rods are replaced every 12 to 18 months. This replacement process is a critical aspect of maintaining the reactor's performance and ensuring the safe operation of the plant.
Fuel rods undergo significant wear and degradation over time due to the high-energy environment within the reactor. The replacement is necessary when the fuel's performance drops below acceptable levels, as indicated by measurements of power density, fuel temperature, and other parameters. This ensures that the reactor operates efficiently and safely.
Replacing fuel rods involves a series of steps. First, the control rods are adjusted to absorb excess neutrons and shut down the reactor. Then, the damaged fuel assemblies are carefully removed, and new fuel rods are inserted. This process requires skilled personnel and specialized equipment to handle the radioactive materials safely.
Yes, fuel rod replacement can be a complex and challenging task. It requires precise coordination and control to manage the reactor's power level during the replacement process. Additionally, handling and disposing of the used fuel rods must be done according to strict regulations to ensure environmental safety.
The regular replacement of fuel rods is essential for the long-term sustainability of the nuclear power plant. It allows for consistent performance, ensures the availability of fuel for power generation, and helps maintain the plant's overall efficiency. Proper maintenance and replacement schedules contribute to the reliability and safety of the facility.