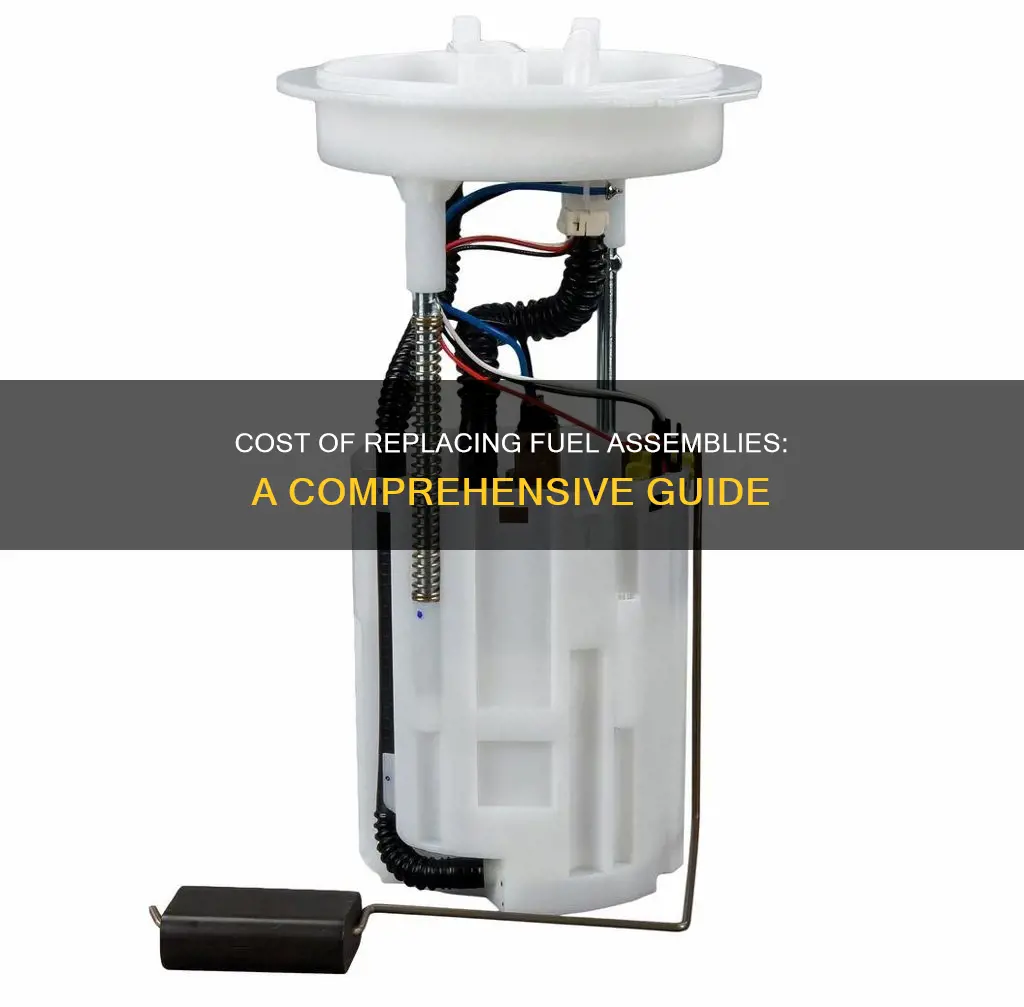
Replacing fuel assemblies in a nuclear reactor is a critical and costly process that requires careful planning and budgeting. The cost of replacing a fuel assembly can vary significantly depending on several factors, including the type of reactor, the size and complexity of the assembly, the current condition of the assembly, and the specific requirements of the replacement process. This paragraph will explore these factors and provide an overview of the costs associated with replacing fuel assemblies, offering insights into the financial considerations involved in maintaining nuclear power plants.
What You'll Learn
- Fuel Assembly Cost Factors: Consider material, size, complexity, and market availability
- Replacement Frequency: Determine how often assemblies need replacement based on usage and wear
- Maintenance and Inspection: Regular maintenance and inspections can extend assembly lifespan
- Environmental Impact: Assess the environmental impact of replacing fuel assemblies
- Budgeting and Funding: Allocate funds for replacement, considering costs and available resources
Fuel Assembly Cost Factors: Consider material, size, complexity, and market availability
When considering the cost of replacing a fuel assembly, several key factors come into play that can significantly impact the overall expense. Firstly, the choice of material is crucial. Different materials, such as uranium dioxide (UO2) or metal alloys, have varying costs associated with them. For instance, UO2 is commonly used due to its high thermal conductivity and low cost, making it an affordable option for fuel pellets. In contrast, metal alloys, like stainless steel or Inconel, offer enhanced corrosion resistance but at a higher price point. The material selection directly influences the assembly's performance and longevity, thus affecting the replacement cost.
Size and complexity of the fuel assembly are additional considerations. Larger assemblies often require more material and intricate manufacturing processes, leading to higher costs. The complexity of the design, including the number of fuel pellets, the arrangement of cladding, and the presence of control elements, can also drive up expenses. For instance, a fuel assembly with a higher number of pellets and a more intricate control element design may be more challenging to produce, requiring specialized equipment and skilled labor.
Market availability and supply chain dynamics play a significant role in determining replacement costs. The availability of raw materials, such as uranium oxide or metal powders, can impact prices. Fluctuations in the market, influenced by global events or economic factors, may lead to increased costs for fuel assembly replacement. Additionally, the lead time for sourcing materials and the availability of specialized manufacturing facilities can affect the overall timeline and cost.
Furthermore, the specific requirements of the nuclear power plant and the fuel assembly's intended use should be considered. Different plants may have unique design specifications, and the fuel assembly must meet these standards. Customization or modifications to meet specific plant requirements can add to the overall cost. It is essential to ensure that the replacement assembly complies with regulatory standards and provides the necessary performance and safety features.
In summary, the cost of replacing a fuel assembly is influenced by various factors, including material choice, size and complexity, market availability, and specific plant requirements. A comprehensive understanding of these factors is essential for accurate cost estimation and effective planning in the nuclear power industry. By carefully considering these aspects, stakeholders can make informed decisions regarding fuel assembly replacement, ensuring optimal performance and cost-effectiveness.
Replacing the Fuel Filter in Your EU1000: Step-by-Step Guide
You may want to see also
Replacement Frequency: Determine how often assemblies need replacement based on usage and wear
When it comes to determining the replacement frequency of fuel assemblies, it's crucial to consider the specific usage and wear patterns of the system in question. Fuel assemblies, which are essential components in nuclear reactors, contain a large number of fuel rods that undergo significant thermal and mechanical stresses during operation. Over time, these stresses can lead to degradation of the fuel rods and other components, necessitating their replacement.
The frequency of replacement is typically based on the accumulated 'burnup' of the fuel, which is a measure of the amount of fissionable material that has been used up in the reactor. Burnup is usually expressed in 'full-power days' or 'full-power hours', indicating the number of days or hours the reactor operates at full power. The specific burnup limit for replacement can vary depending on the reactor design, fuel type, and regulatory guidelines. For instance, some reactors may require replacement after a certain number of full-power days, while others might use a combination of burnup and time-based criteria.
Usage patterns also play a significant role in determining replacement frequency. High-power reactors or those with continuous operation may experience more rapid wear and tear, requiring more frequent replacements. In contrast, lower-power reactors or those with intermittent operation might have longer intervals between replacements. It's important to monitor and record the actual usage data, including reactor power levels, operating hours, and any maintenance activities that could impact fuel assembly performance.
Wear and tear on fuel assemblies can be influenced by various factors, including the material properties of the fuel and cladding, the design of the reactor, and the cooling system's efficiency. For example, in pressurized water reactors, the water's temperature and flow rate can affect the fuel's performance and longevity. Regular inspections and monitoring of the fuel assemblies can provide valuable data on their condition, helping to identify any signs of premature wear or damage.
In summary, determining the replacement frequency of fuel assemblies involves a careful analysis of usage patterns, burnup limits, and wear factors. By considering these aspects, operators can ensure the safety and efficiency of the reactor while minimizing downtime and maintenance costs. It is essential to adhere to the specific guidelines provided by the reactor manufacturer and regulatory bodies to maintain the integrity of the fuel assembly replacement process.
Replacing the Fuel Filter in a 2001 Escape: Step-by-Step Guide
You may want to see also
Maintenance and Inspection: Regular maintenance and inspections can extend assembly lifespan
Regular maintenance and inspections are crucial for ensuring the longevity and optimal performance of fuel assemblies in nuclear power plants. These procedures are designed to identify and address potential issues before they escalate into major problems, ultimately preventing costly and potentially dangerous failures. The frequency and scope of these maintenance activities may vary depending on the specific plant, the type of fuel assembly, and regulatory requirements. However, a comprehensive maintenance program typically includes both routine checks and more in-depth inspections.
Routine maintenance involves less invasive procedures that can be performed regularly to keep the fuel assembly in good condition. This includes visual inspections to check for any signs of corrosion, damage, or wear, as well as measurements of key parameters such as temperature, pressure, and radiation levels. These routine checks are essential for early detection of anomalies and can help identify minor issues that, if left unattended, could lead to more significant problems. For instance, monitoring radiation levels can indicate changes in the fuel's performance or potential issues with the cooling system.
More extensive inspections are often required at specific intervals or after significant events, such as a power surge or a change in operating conditions. These inspections might involve taking the assembly out of service, disassembling it, and performing detailed examinations. During these inspections, technicians can assess the condition of the fuel pellets, cladding, and other components, looking for signs of degradation, cracks, or other defects. Advanced techniques such as ultrasonic testing and eddy current inspection can be employed to detect internal flaws that might not be visible to the naked eye.
The process of disassembly and inspection requires specialized equipment and trained personnel. Technicians use precision tools to carefully remove components, ensuring that the assembly remains intact and can be reassembled without issues. Once disassembled, each part is thoroughly examined, and any defects or issues are documented. This detailed record-keeping is vital for tracking the health of the fuel assembly over time and for making informed decisions about future maintenance and potential replacements.
By implementing a rigorous maintenance and inspection program, nuclear power plant operators can significantly extend the lifespan of their fuel assemblies, reduce the risk of unexpected failures, and ensure the continued safe operation of the plant. Regular maintenance not only helps to maintain the integrity of the fuel but also contributes to the overall reliability and safety of the nuclear power generation process.
Dodge Neon Fuel Pump Swap: A Step-by-Step Guide
You may want to see also
Environmental Impact: Assess the environmental impact of replacing fuel assemblies
The process of replacing fuel assemblies in nuclear power plants can have significant environmental implications, and it is crucial to understand and mitigate these impacts to ensure the safety and sustainability of nuclear energy. Here's an assessment of the environmental considerations:
Waste Management: One of the primary environmental concerns is the management of radioactive waste generated during the replacement process. Fuel assemblies contain highly radioactive materials, and when they are removed and replaced, the spent fuel becomes a hazardous waste. Proper disposal and storage of this waste are essential to prevent environmental contamination. Nuclear facilities must adhere to strict regulations and employ secure waste management systems to ensure the long-term stability of the waste and minimize the risk of radiation exposure to the surrounding ecosystem.
Water Usage and Pollution: Replacing fuel assemblies often involves extensive water usage for cooling and cleaning purposes. This can put a strain on local water resources, especially in areas with limited water availability. Additionally, there is a risk of water pollution if not managed properly. Nuclear plants must implement efficient water treatment processes to prevent the release of radioactive particles or chemicals into nearby water bodies, which could have detrimental effects on aquatic life and local ecosystems.
Air Quality and Radiation Exposure: During the replacement process, there is a potential for increased air pollution and radiation exposure. The handling and transportation of fuel assemblies may release radioactive particles into the air, posing risks to workers and nearby communities. To minimize these risks, nuclear facilities should employ advanced filtration systems and strict protocols for air quality monitoring. Regular training and personal protective equipment for workers can also help reduce the impact on human health.
Ecosystem Disruption: Construction and maintenance activities related to fuel assembly replacement can temporarily disrupt local ecosystems. This may include clearing vegetation, altering land use, and creating temporary access roads. These changes can affect wildlife habitats, migration patterns, and overall biodiversity. Mitigation measures such as habitat restoration, wildlife monitoring, and implementing temporary conservation measures can help minimize the ecological footprint of these activities.
Long-Term Environmental Monitoring: It is essential to establish long-term environmental monitoring programs to assess the impact of fuel assembly replacement over time. This includes regular testing of soil, water, and air quality in the surrounding areas. By collecting and analyzing data, nuclear power plant operators can identify any potential environmental degradation and take corrective actions to ensure compliance with environmental standards.
The Future of Energy: Renewable Resources Take Center Stage
You may want to see also
Budgeting and Funding: Allocate funds for replacement, considering costs and available resources
When it comes to budgeting and funding the replacement of a fuel assembly, a comprehensive approach is essential to ensure a successful outcome. Here's a detailed guide on how to allocate funds effectively:
Research and Cost Estimation: Begin by gathering information from various sources. Google searches can provide initial insights into the costs associated with fuel assembly replacement. Look for industry reports, case studies, and expert opinions to estimate the total expenditure. Consider factors such as the type of fuel assembly, its size, the complexity of the replacement process, and any additional equipment or services required. Obtaining multiple quotes from different suppliers or contractors can help you make an informed decision and identify potential cost-saving opportunities.
Breakdown of Expenses: Create a comprehensive list of expenses related to the replacement project. This should include the cost of the new fuel assembly itself, which may vary depending on the supplier and the specific requirements. Labor costs are another significant factor; consider the number of workers needed, their expertise, and the duration of the replacement process. Don't forget to account for equipment rental or purchase, safety gear, and any necessary permits or licenses. Additionally, allocate funds for incidentals, such as travel expenses for site visits or emergency costs that may arise during the project.
Prioritize and Allocate: Prioritize the expenses based on their importance and urgency. For instance, the cost of the fuel assembly and labor might be the primary focus, while other expenses can be adjusted according to the budget. Allocate funds accordingly, ensuring that critical components and services are adequately covered. Consider creating a contingency fund to handle unexpected expenses or delays, which can significantly impact the overall budget.
Explore Funding Options: Depending on the scale and complexity of the project, you may need to explore various funding avenues. Government grants or subsidies related to energy infrastructure or environmental initiatives could provide financial support. Approach financial institutions or investors who specialize in funding large-scale projects. For smaller-scale replacements, consider seeking grants from local or regional organizations that promote sustainable energy practices.
Regular Review and Adjustment: Budgeting is an ongoing process that requires regular review and adjustment. As the project progresses, monitor the actual expenses against the allocated budget. Identify areas where costs can be optimized without compromising quality. Be prepared to make adjustments to ensure the project stays within the allocated funds. Regular reviews will also help identify any potential issues early on, allowing for timely decision-making and resource reallocation.
Kia Rio Fuel Pump Replacement: Step-by-Step Guide
You may want to see also
Frequently asked questions
The cost of replacing a fuel assembly can vary significantly depending on several factors. Firstly, the type and size of the fuel assembly play a crucial role, as different assemblies have varying complexities and materials. For instance, a fuel assembly for a commercial nuclear power plant will be more expensive than one for a smaller, residential generator. Secondly, the location and accessibility of the assembly impact the labor costs. Replacing a fuel assembly in a hard-to-reach area or requiring specialized equipment will generally be more costly. Lastly, the urgency and any additional services required, such as emergency response or extended warranty, can also affect the overall price.
The frequency of fuel assembly replacement depends on the specific application and usage. In nuclear power plants, fuel assemblies are typically replaced every 12 to 18 months. This replacement cycle ensures optimal performance and safety, as the fuel undergoes degradation over time, leading to reduced efficiency and potential safety risks. For industrial or commercial applications, the replacement interval may vary based on the load and operating conditions. Regular maintenance and monitoring are essential to determine the appropriate replacement schedule for each fuel assembly.
Replacing a fuel assembly is a complex task that requires specialized knowledge, skills, and equipment. It is generally not recommended for DIY enthusiasts or non-experts due to the potential risks and legal implications. Fuel assemblies contain radioactive materials, and improper handling can lead to exposure and environmental hazards. Professional technicians and engineers have the necessary training and tools to safely remove, replace, and dispose of the assembly, ensuring compliance with regulatory standards. It is advisable to consult with qualified professionals or authorized service providers for fuel assembly replacement.