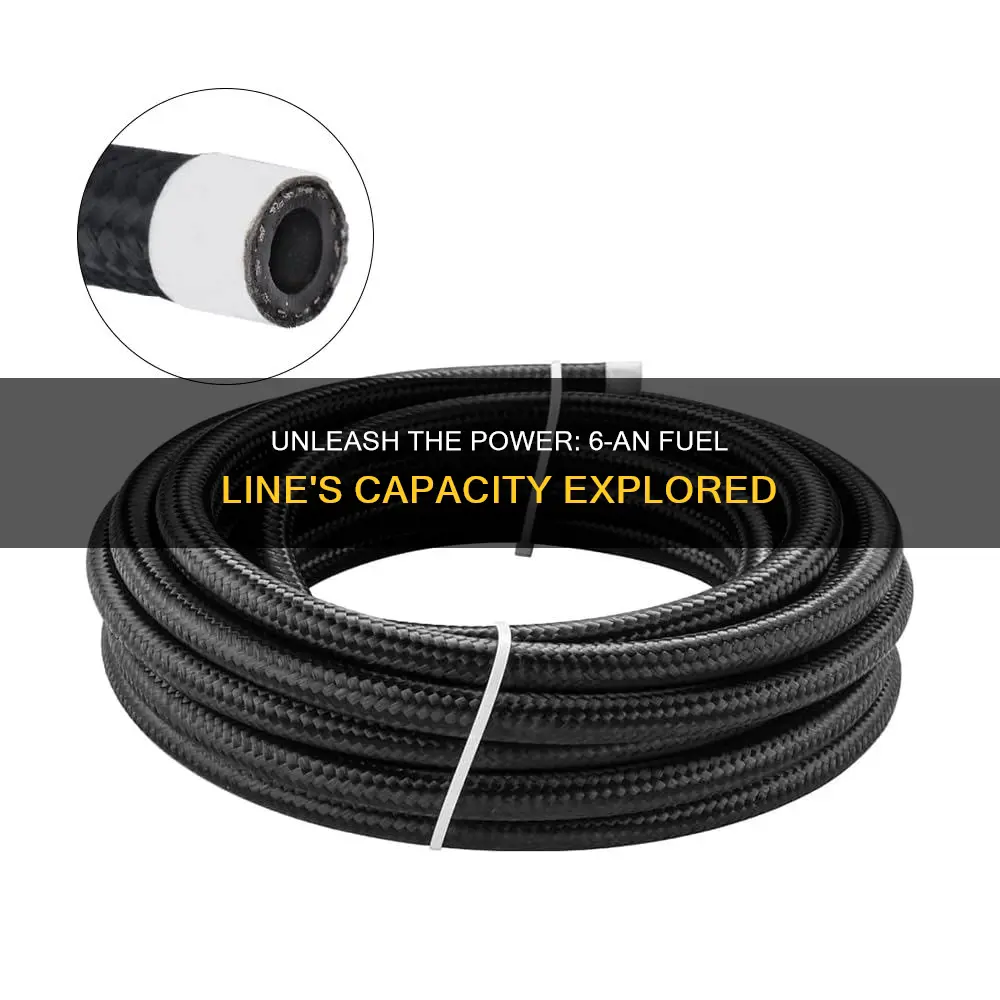
When it comes to fuel lines, the amount of power they can support depends on several factors, including the diameter, material, and length of the line. In this article, we will explore the maximum power capacity of a 6-inch fuel line and the considerations to keep in mind when selecting the right fuel line for your application.
Characteristics | Values |
---|---|
Power Rating | 6 AN fuel lines typically support power ratings ranging from 100 to 300 horsepower (hp) or more, depending on the specific application and manufacturer. |
Pressure Rating | These lines can handle pressures up to 3000 pounds per square inch (psi) or higher, ensuring they can withstand the demands of high-performance engines. |
Diameter | The diameter of 6 AN fuel lines varies, but common sizes include 0.25 inches, 0.312 inches, and 0.375 inches, allowing for efficient fuel flow. |
Material | Common materials include stainless steel, aluminum, and brass, each offering different advantages in terms of durability, weight, and corrosion resistance. |
Length | Line lengths can vary widely, from a few inches to several feet, depending on the vehicle's layout and fuel system design. |
Compatibility | 6 AN fuel lines are designed to be compatible with various fuel types, including gasoline, diesel, and racing fuels, making them versatile for different automotive applications. |
Temperature Range | They can withstand a wide temperature range, typically from -40°F to 400°F, ensuring reliable performance in extreme weather conditions. |
Flexibility | These lines offer flexibility to accommodate engine movements and provide a smooth fuel delivery path. |
Ease of Installation | 6 AN fuel lines are often designed with ease of installation in mind, featuring quick-connect fittings and straightforward assembly. |
What You'll Learn
- Pressure Rating: Determine the fuel line's pressure limit for safe operation
- Flow Capacity: Assess the line's ability to handle fuel flow rates
- Temperature Tolerance: Evaluate the line's performance under varying temperatures
- Material Strength: Consider the material's strength and durability for power support
- Safety Factors: Apply safety margins to ensure the line can handle excess power
Pressure Rating: Determine the fuel line's pressure limit for safe operation
When considering the power a fuel line can support, it's crucial to focus on its pressure rating, which is a critical factor in ensuring safe and efficient operation. The pressure limit of a fuel line is determined by its design and material composition, and it's essential to understand this rating to avoid potential issues.
The pressure rating of a fuel line is typically specified by the manufacturer and is often indicated on the line itself or in the accompanying documentation. This rating is a maximum pressure value that the line can withstand without compromising its structural integrity. It is a safety measure to prevent overpressure, which could lead to fuel line failure, leaks, or even explosions in extreme cases. For instance, a common pressure rating for fuel lines in automotive applications might range from 100 to 300 psi (pounds per square inch), depending on the vehicle's engine requirements and the type of fuel used.
To determine the pressure limit of a fuel line, one should consult the manufacturer's guidelines. These guidelines often include a detailed table or chart that specifies the pressure rating for different sizes and types of fuel lines. For example, a 6-AN (American National Standards Institute) fuel line, which is a common size for high-performance applications, may have a pressure rating of 300 psi or higher, ensuring it can handle the power output of high-performance engines. It's important to match the fuel line's pressure rating to the engine's requirements to avoid any potential performance issues or safety hazards.
In addition to the manufacturer's specifications, it's also beneficial to consider the fuel line's material and construction. Different materials, such as steel, aluminum, or rubber, have varying pressure tolerances. For instance, a steel fuel line might have a higher pressure rating than a rubber-reinforced line due to its stronger material properties. Understanding these material differences is essential when selecting the appropriate fuel line for a specific application.
In summary, determining the pressure limit of a fuel line is a critical step in ensuring its safe and efficient operation. By consulting manufacturer guidelines, considering material properties, and matching the fuel line's pressure rating to the engine's requirements, one can ensure optimal performance and avoid potential risks associated with overpressure. This knowledge is particularly important in high-performance applications where power output can be significantly higher, requiring fuel lines with appropriate pressure ratings to handle the demands.
Unclogging the Jeep Cherokee: A Guide to Removing the Fuel Line
You may want to see also
Flow Capacity: Assess the line's ability to handle fuel flow rates
When evaluating the power-handling capability of a fuel line, it's crucial to consider its flow capacity, which refers to its ability to manage the rate of fuel flow. This is a critical aspect of ensuring optimal engine performance and safety. The flow capacity of a fuel line is typically measured in gallons per minute (GPM) or liters per minute (LPM), depending on the system's measurement system.
To assess the flow capacity, you need to understand the specific requirements of your engine. Different engines have varying fuel flow rates, and the fuel line must be able to accommodate these rates to deliver fuel efficiently. For instance, high-performance engines often require higher flow rates to meet their power demands. You can find the recommended flow rate for your engine in the vehicle's manual or consult a reputable source that provides engine specifications.
The flow capacity of a fuel line is influenced by several factors. Firstly, the diameter of the line plays a significant role. Larger diameters allow for higher flow rates, as they provide more space for fuel to pass through. However, it's essential to balance this with the material of the line, as some materials may have limitations in terms of pressure and temperature. The length of the fuel line also matters; longer lines may experience more resistance, affecting the overall flow capacity.
Another critical aspect is the presence of restrictions or obstructions within the fuel line. Any bends, valves, or fittings can reduce the flow rate. It is essential to ensure that the line is free from such restrictions to maximize its flow capacity. Additionally, the condition of the fuel line itself is vital. Over time, fuel lines can develop cracks or become corroded, leading to reduced flow capacity and potential fuel leaks. Regular inspections and maintenance are necessary to identify and address these issues.
In summary, assessing the flow capacity of a fuel line involves understanding the engine's fuel flow requirements, considering the line's diameter, length, and potential restrictions, and ensuring the line's overall condition. By carefully evaluating these factors, you can determine the maximum power that a fuel line can support and ensure optimal engine performance while maintaining safety standards.
Understanding Fuel Line Sizes: A Comprehensive Guide
You may want to see also
Temperature Tolerance: Evaluate the line's performance under varying temperatures
When assessing the temperature tolerance of a 6-AN fuel line, it's crucial to understand the material's performance under varying thermal conditions. This evaluation is essential for ensuring the line can handle the power and pressure it's designed to support without compromising its integrity. Here's a detailed breakdown of how to approach this assessment:
Understanding Temperature Tolerance:
Temperature tolerance refers to the range of temperatures a fuel line can withstand without permanent deformation or damage. It's a critical factor, especially in high-performance applications where fuel lines are exposed to extreme heat. The goal is to identify the line's breaking point and ensure it operates within a safe margin.
Testing Methods:
- Thermal Cycling: Subject the fuel line to rapid temperature fluctuations, simulating real-world conditions. This involves heating and cooling the line rapidly to test its resilience.
- Long-Term Exposure: Expose the line to sustained high temperatures for extended periods to assess its performance over time.
- Temperature Gradient Testing: Apply heat to specific sections of the line to understand how temperature variations along its length affect its performance.
Performance Evaluation:
- Flexibility and Movement: Observe how the line behaves under temperature changes. It should maintain its flexibility and not become brittle or overly rigid.
- Pressure Retention: Measure the line's ability to retain pressure at different temperatures. A qualified fuel line should maintain pressure without significant leaks or degradation.
- Material Integrity: Inspect the line for any signs of cracking, warping, or material failure. Look for changes in color or texture that could indicate thermal stress.
Material Considerations:
Different materials offer varying temperature tolerances. For instance, stainless steel fuel lines are known for their excellent temperature resistance, while some rubber compounds may degrade at higher temperatures. Understanding the chosen material's thermal properties is vital for accurate evaluation.
Safety Margins:
It's essential to operate fuel lines within safe temperature limits. Engineers often design systems with a temperature margin to account for potential variations and ensure reliable performance. This margin provides a buffer, allowing the line to handle slightly higher temperatures without risk.
By rigorously testing and evaluating temperature tolerance, you can ensure that a 6-AN fuel line is capable of supporting the required power and pressure while maintaining its structural integrity. This evaluation process is a critical aspect of designing and implementing fuel systems in various applications.
Fuel Line Routing: Carb Trimmer Basics
You may want to see also
Material Strength: Consider the material's strength and durability for power support
When determining the power support capacity of a 6-inch fuel line, it's crucial to consider the material's strength and durability. The material used for the fuel line plays a significant role in its ability to withstand pressure, temperature fluctuations, and the corrosive effects of fuel. Here's a detailed breakdown of how material strength impacts power support:
- Material Selection: Different materials offer varying levels of strength and durability. Common materials for fuel lines include steel, aluminum, and various types of plastics like PVC or polypropylene. Steel is known for its high tensile strength, making it suitable for high-pressure applications. However, it can be heavier and more susceptible to corrosion over time. Aluminum offers a good balance of strength and weight, but it may not be as durable in corrosive environments. Plastics, such as PVC or polypropylene, are lightweight and resistant to corrosion, making them ideal for fuel lines in many applications.
- Tensile Strength: This is a critical property that indicates how much force a material can withstand before breaking. For a 6-inch fuel line, you want a material with a high tensile strength to ensure it can handle the pressure and forces exerted by the fuel. For example, a fuel line made from high-density polyethylene (HDPE) with a tensile strength of 10,000-12,000 psi (pounds per square inch) would be suitable for most automotive applications.
- Flexural Strength: Flexural strength is essential for fuel lines as they need to withstand bending and flexing during operation. A material with good flexural strength will ensure the fuel line remains intact even when it is manipulated or routed around various components. Materials like polypropylene or PVC often excel in this area due to their flexibility and resistance to cracking.
- Corrosion Resistance: Fuel lines are exposed to corrosive substances, so the material's ability to resist corrosion is vital. Materials like stainless steel or certain types of plastics (e.g., fluoropolymer-lined fuel lines) offer excellent corrosion resistance, ensuring the fuel line's longevity and reliability.
- Temperature Considerations: The operating temperature of the fuel line is another critical factor. Some materials may degrade or become brittle at high temperatures, while others can maintain their structural integrity. It's essential to choose a material that can withstand the expected temperature range of the fuel system.
In summary, when assessing the power support capacity of a 6-inch fuel line, the material's strength and durability are key considerations. Selecting the right material ensures the fuel line can handle the required pressure, temperature, and environmental conditions, providing a reliable and safe power supply for your application.
Fixing a Steel Fuel Line: A Step-by-Step Guide
You may want to see also
Safety Factors: Apply safety margins to ensure the line can handle excess power
When determining the power capacity of a fuel line, it's crucial to incorporate safety factors to ensure the line can withstand potential excess power. This is a critical aspect of system design and maintenance, especially in high-performance applications. The primary goal is to prevent damage, leaks, or failures that could lead to hazardous situations.
Safety margins are a fundamental concept in engineering and are applied to account for variations and uncertainties in system performance. In the context of fuel lines, these margins ensure that the line can handle more power than its rated capacity, providing a buffer against unexpected increases in power output. The margin is typically calculated as a percentage of the rated power, with a common practice being to add a 20-50% safety factor. For instance, if a fuel line is rated for 600 horsepower, a safety margin of 20% would allow for a maximum of 720 horsepower (600 + 120).
To apply this safety factor, engineers and technicians should follow a systematic approach. First, they need to identify the maximum expected power output in the specific application. This could be based on manufacturer specifications, performance testing, or real-world usage data. Next, they should select an appropriate safety margin percentage, considering the specific risks and requirements of the system. For example, in a high-performance racing car, a higher safety margin might be chosen to account for the extreme conditions and potential for sudden power spikes.
The application of safety margins involves adjusting the design or operating parameters of the fuel line. This could include increasing the diameter of the line, using materials with higher strength-to-weight ratios, or implementing pressure relief mechanisms. For instance, a larger diameter fuel line can handle more power by reducing the pressure drop and allowing for a higher flow rate, thus providing a safety margin against power increases. Similarly, materials with superior mechanical properties can ensure the line can withstand higher pressures and temperatures, further enhancing its safety.
In summary, incorporating safety factors and applying appropriate safety margins are essential practices when determining the power capacity of a fuel line. This ensures that the system can handle excess power without compromising safety, reliability, and performance. By following these guidelines, engineers and technicians can design and maintain fuel lines that are robust, efficient, and capable of meeting the demands of various applications.
Heater Hose: A Creative Fuel Line Solution?
You may want to see also
Frequently asked questions
A 6-AN fuel line is designed to handle a specific amount of pressure and power, typically up to 300-400 horsepower. This size of fuel line is commonly used in high-performance engines and racing applications where higher power outputs are expected. It is important to ensure that the fuel line is compatible with the engine's requirements and that the overall fuel system can handle the power output to prevent any potential issues or failures.
The power capacity of a 6-AN fuel line is influenced by several factors. Firstly, the material and thickness of the fuel line play a crucial role, as thicker walls can withstand higher pressures. Secondly, the length of the fuel line matters; longer lines may experience increased pressure drop, affecting power delivery. Additionally, the type of fuel being used, such as ethanol or methanol, can impact the line's performance and durability. It is essential to consider these factors when selecting a fuel line to ensure it can handle the intended power output.
While a 6-AN fuel line is generally suitable for high-performance engines, it may not be sufficient for extremely high-power applications. For power outputs exceeding 400 horsepower, larger diameter fuel lines or custom solutions might be required. Upgrading to a 8-AN or 10-AN fuel line can provide increased capacity to handle the higher power demands. It is recommended to consult with engine experts or fuel system specialists to determine the appropriate fuel line size for a specific power level.