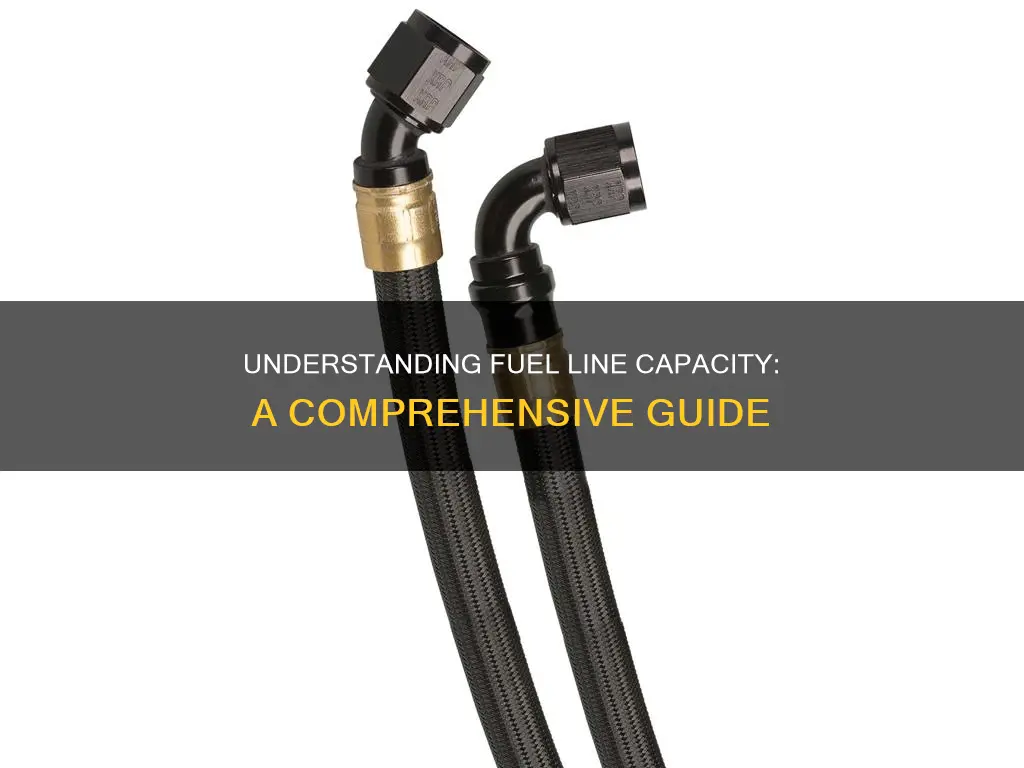
Understanding the amount of fuel in a fuel line is crucial for vehicle maintenance and performance. The fuel line, a critical component in the fuel delivery system, carries gasoline or diesel from the tank to the engine. Knowing how much fuel is in the line at any given time is essential for ensuring optimal engine operation, preventing fuel starvation, and avoiding potential engine damage. This knowledge is particularly important for drivers who frequently start and stop their vehicles, as it helps in managing fuel efficiency and reducing emissions.
What You'll Learn
- Fuel Line Capacity: Determine the maximum fuel volume a line can hold
- Fuel Line Diameter: Calculate the line's diameter to estimate fuel volume
- Fuel Line Length: Measure the line's length to assess fuel capacity
- Fuel Line Material: Understand the material's impact on fuel volume retention
- Fuel Line Pressure: Assess pressure to predict fuel volume in the line
Fuel Line Capacity: Determine the maximum fuel volume a line can hold
The capacity of a fuel line is a critical factor in ensuring optimal fuel delivery to an engine. It is essential to understand the maximum fuel volume a line can accommodate to prevent issues such as fuel starvation or excessive pressure, which can lead to engine performance problems. Determining the fuel line capacity involves several key considerations and measurements.
One approach to determining the maximum fuel volume is to physically measure the fuel line itself. This can be done by using a graduated cylinder or a similar measuring device. Start by cutting a section of the fuel line that is representative of the entire line's diameter and length. Then, fill the cylinder with water and carefully slide the fuel line into it, ensuring it is fully submerged. Measure the volume of water displaced by the fuel line, as this will indicate the line's internal volume. This method provides a direct measurement of the fuel line's capacity.
Another way to assess fuel line capacity is by using pressure and flow rate measurements. This method involves connecting a fuel pump to the line and measuring the pressure and flow rate at different fuel levels. By plotting these measurements, you can determine the point at which the fuel line becomes full. The maximum fuel volume can then be calculated based on the pressure and flow rate data. This approach is particularly useful for fuel lines with complex geometries or those that are difficult to access physically.
Additionally, understanding the engine's fuel requirements is crucial. Different engines have varying fuel needs, and the fuel line capacity should be sufficient to meet these demands. For instance, high-performance engines may require larger fuel volumes to ensure efficient operation. By knowing the engine's specifications, you can estimate the necessary fuel line capacity and ensure a reliable fuel supply.
In summary, determining the maximum fuel volume a line can hold is essential for maintaining engine performance and reliability. Physical measurements, pressure and flow rate assessments, and engine-specific requirements all play a role in this process. By carefully considering these factors, you can ensure that the fuel line is appropriately sized to handle the fuel demands of the engine, thereby optimizing overall system efficiency.
Optimizing Performance: Choosing the Right Fuel Line for Your 50 HP Outboard
You may want to see also
Fuel Line Diameter: Calculate the line's diameter to estimate fuel volume
The diameter of a fuel line is a critical factor in determining the volume of fuel it can hold. This is because the diameter directly influences the cross-sectional area of the line, which in turn affects the amount of fuel that can pass through it in a given time. A larger diameter means a greater cross-sectional area, allowing for more fuel to flow, while a smaller diameter reduces the flow capacity.
To calculate the diameter of a fuel line, you need to know the inside diameter, which is the measurement of the line's inner surface. This can often be found in the fuel line's specifications or on the manufacturer's documentation. The formula to calculate the volume of fuel in a line is based on the cross-sectional area and the length of the line. The cross-sectional area (A) is given by the formula A = π * (d/2)^2, where 'd' is the inside diameter of the line.
Once you have the inside diameter, you can use this formula to find the area. For example, if the inside diameter is 0.5 inches, the calculation would be A = π * (0.5/2)^2 = approximately 0.0785 square inches. This area represents the cross-section of the fuel line and is crucial for understanding the fuel capacity.
The next step is to consider the length of the fuel line. The volume of fuel (V) can be calculated using the formula V = A * L, where 'L' is the length of the line in inches. For instance, if the fuel line is 12 inches long, the volume would be V = 0.0785 * 12 = approximately 0.942 cubic inches. This calculation provides an estimate of the fuel volume the line can hold.
It's important to note that this calculation provides an estimate and actual fuel capacity may vary depending on factors like fuel line material, temperature, and pressure. However, understanding the relationship between fuel line diameter and volume is essential for optimizing fuel systems and ensuring efficient fuel delivery in various applications, from automotive to industrial settings.
Fuel and Brake Line Costs: A Breakdown of Expenses
You may want to see also
Fuel Line Length: Measure the line's length to assess fuel capacity
To determine the fuel capacity of a vehicle, one crucial aspect to consider is the length of the fuel line. This measurement is essential as it directly relates to the amount of fuel that can be stored and subsequently supplied to the engine. By assessing the fuel line length, you can gain valuable insights into the vehicle's fuel capacity and overall performance.
Measuring the fuel line length is a straightforward process that can be done with a few simple tools. Start by locating the fuel tank, which is typically found beneath the vehicle or in the engine compartment. Access the fuel tank's opening, which may require removing certain panels or covers. Once inside, carefully measure the distance from the fuel tank's inlet port to the end of the fuel line. This measurement will provide an accurate indication of the fuel line's length.
The length of the fuel line is significant because it determines the maximum volume of fuel that can be accommodated. Longer fuel lines generally allow for larger fuel tanks, enabling the vehicle to carry more fuel. This is particularly important for vehicles with high mileage or those used for long-distance travel, as it ensures a sufficient fuel supply for extended journeys. Additionally, longer fuel lines can contribute to improved fuel efficiency, as the engine has access to a more substantial fuel reserve.
It is worth noting that the fuel line length should be measured with precision to ensure accurate results. Any discrepancies in measurement can lead to incorrect fuel capacity assessments. Using a flexible measuring tape or a ruler with fine markings can help achieve accurate readings. It is also recommended to measure the fuel line in multiple sections, especially if the fuel tank has a complex shape, to account for any variations in the line's path.
Understanding the fuel line length is a fundamental step in assessing a vehicle's fuel capacity and overall performance. By measuring this critical component, you can make informed decisions regarding fuel management, ensuring that your vehicle is adequately supplied with fuel for various driving conditions. This knowledge can also be valuable when considering fuel-related upgrades or modifications to optimize the vehicle's performance.
Replacing Fuel Lines: A Step-by-Step Guide for Your 2007 Cadillac CTS
You may want to see also
Fuel Line Material: Understand the material's impact on fuel volume retention
The material used in a fuel line plays a crucial role in determining how much fuel is retained and how efficiently it is delivered to the engine. Different materials have varying properties that can affect the volume of fuel held and its overall performance. Understanding these material characteristics is essential for optimizing fuel systems and ensuring optimal engine operation.
One key factor is the material's ability to withstand fuel-related stresses. Fuel lines are exposed to high pressures and temperatures, especially in high-performance engines. Materials like steel or aluminum alloys are commonly used due to their strength and durability. These metals can handle the mechanical demands of the fuel system, ensuring that the fuel line doesn't collapse or deform under pressure, which could lead to fuel loss or inefficient delivery.
The flexibility of the material is another critical aspect. Fuel lines need to accommodate engine vibrations and movement during operation. Materials such as rubber or synthetic compounds are often chosen for their flexibility. These materials allow the fuel line to bend and stretch without compromising the integrity of the fuel flow. This flexibility is vital to maintaining a consistent fuel supply to the engine, especially in applications where the fuel line route is not straight or fixed.
Additionally, the material's resistance to fuel degradation is essential. Some materials, when in contact with fuel, can cause chemical reactions, leading to fuel oxidation and the formation of varnish or sludge. This can result in reduced fuel volume and performance issues. Materials like stainless steel or specialized fuel-resistant polymers are preferred as they minimize fuel degradation and ensure the fuel remains in optimal condition.
Furthermore, the choice of material can impact the overall weight and cost of the fuel system. Lighter materials might be preferred in certain applications to reduce the engine's overall weight. However, this must be balanced with the material's ability to retain fuel volume and withstand operating conditions. Manufacturers often select materials that offer a good compromise between performance, durability, and cost-effectiveness.
In summary, the material selection for fuel lines is a critical consideration in engine design. It directly influences the fuel volume retention, delivery efficiency, and overall engine performance. Engineers must carefully evaluate the properties of different materials to ensure the fuel line meets the specific requirements of the engine, providing a reliable and efficient fuel supply.
Alcohol-Resistant Fuel Lines: The Ultimate Guide to Compatibility
You may want to see also
Fuel Line Pressure: Assess pressure to predict fuel volume in the line
The pressure within a fuel line is a critical factor in determining the volume of fuel it contains. This is because the pressure directly influences the density and flow rate of the fuel, which in turn affects the overall amount of fuel available for the engine. By assessing the pressure in the fuel line, you can make an educated prediction about the volume of fuel present, ensuring optimal engine performance and fuel efficiency.
To measure fuel line pressure, you'll need a fuel pressure gauge, which is a specialized tool designed for this purpose. These gauges are typically connected to the fuel line, allowing you to read the pressure directly. It's important to note that fuel line pressure can vary depending on several factors, including engine speed, temperature, and the overall health of the fuel system. Therefore, it's essential to take these variables into account when interpreting the pressure reading.
When you connect the gauge to the fuel line, ensure a secure and tight connection to avoid any leaks or inaccurate readings. Start by reading the pressure at idle, as this provides a baseline for comparison. Then, gradually increase the engine speed to higher RPMs and observe the pressure changes. Typically, as the engine revs up, the fuel pressure should increase proportionally to meet the higher fuel demand. Any significant deviations from this trend could indicate potential issues with the fuel pump, injectors, or other fuel system components.
In addition to measuring pressure, it's beneficial to monitor the fuel line's response time. When the engine is started, the fuel pump should activate promptly, and the pressure should rise within a few seconds. If the pressure doesn't increase or takes an unusually long time to stabilize, it may suggest a problem with the fuel pump or related components. This information, combined with the pressure readings, can help diagnose potential fuel system issues.
Understanding fuel line pressure is a valuable skill for mechanics and car enthusiasts alike. By regularly checking and analyzing this pressure, you can ensure that your fuel system is functioning optimally, leading to improved engine performance and fuel economy. It's a simple yet effective method to gauge the health of your fuel line and overall fuel system, allowing for prompt identification and resolution of potential problems.
Fuel Line Replacement: Cost Breakdown and Factors
You may want to see also
Frequently asked questions
Checking the fuel level in your fuel line is an important part of vehicle maintenance. You can do this by removing the fuel line and using a measuring tool to determine the volume of fuel it contains. Alternatively, you can use a fuel gauge, which is typically located on the dashboard, to get an estimate of the fuel level.
Yes, it is recommended to check the fuel line periodically, especially if you notice any issues with your vehicle's performance or fuel efficiency. Regular checks can help identify potential problems, such as fuel leaks or contamination, and ensure your vehicle operates optimally.
Refilling the fuel line is not a common practice. If your vehicle is running low on fuel, it's best to add more fuel to the tank rather than refilling the line. The fuel line is designed to hold a specific amount of fuel, and overfilling can lead to engine issues.
A clogged or restricted fuel line can cause reduced engine performance, difficulty starting the vehicle, and erratic behavior. You may also notice a decrease in fuel efficiency and the engine may start to stall. It's important to address this issue promptly to prevent further damage.
Fuel contamination can occur due to various factors, such as old fuel, improper storage, or engine issues. To prevent contamination, use fresh fuel, store it correctly, and regularly maintain your vehicle's engine. Using a fuel stabilizer can also help maintain fuel quality and prevent clogs in the fuel system.