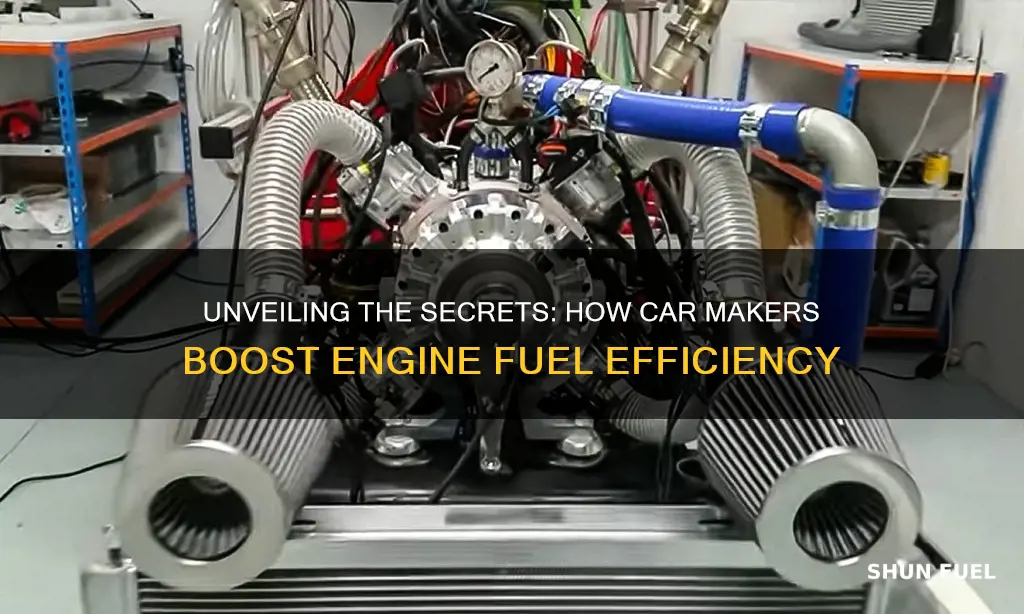
Car manufacturers employ various strategies to enhance engine fuel efficiency, aiming to reduce environmental impact and improve vehicle performance. One key approach is optimizing the combustion process through advanced engine designs, such as direct fuel injection and turbocharging, which improve power output while minimizing fuel consumption. Additionally, manufacturers focus on lightweight materials and aerodynamic enhancements to reduce drag, allowing engines to operate more efficiently. Another significant method is the integration of hybrid systems, combining electric motors with traditional engines to capture and reuse energy that would otherwise be lost during braking, thereby increasing overall fuel economy. These innovations not only contribute to more sustainable transportation but also enhance the driving experience by offering improved performance and reduced operating costs.
What You'll Learn
- Engine Design: Streamlining components to reduce friction and improve airflow
- Hybrid Technology: Combining electric motors with traditional engines for enhanced efficiency
- Turbocharging: Increasing power output without significantly boosting fuel consumption
- Direct Injection: Precise fuel delivery for optimal combustion and reduced emissions
- Lightweight Materials: Using advanced materials to lower vehicle weight and improve mileage
Engine Design: Streamlining components to reduce friction and improve airflow
Engine design plays a pivotal role in enhancing fuel efficiency, and streamlining components is a key strategy employed by car manufacturers to achieve this goal. The internal combustion engine, a complex system with numerous moving parts, is a major contributor to fuel consumption. By optimizing the design of these components, engineers can significantly reduce friction and improve airflow, leading to more efficient combustion and, ultimately, better fuel economy.
One approach to streamlining engine components is the use of lightweight materials. Aluminum and advanced alloys are increasingly being utilized in engine construction, replacing traditional heavy metals. Lighter materials reduce the overall weight of the engine, which in turn decreases the energy required to accelerate the vehicle. Additionally, these materials offer excellent heat dissipation properties, helping to maintain optimal engine temperatures and further improving efficiency.
Another critical aspect of engine design is the minimization of friction between moving parts. Friction generates heat and energy loss, which can significantly impact fuel efficiency. Manufacturers achieve this through the use of advanced bearings, low-friction seals, and improved lubrication systems. For instance, roller bearings can reduce friction in the crankshaft and camshaft systems, while specialized seals prevent oil leaks and maintain the necessary pressure for efficient lubrication.
Streamlining also involves optimizing the shape and arrangement of engine components. This includes designing intake and exhaust systems to ensure smooth airflow, reducing turbulence and pressure losses. The use of advanced manufacturing techniques, such as 3D printing, allows for intricate and precise component designs, enabling manufacturers to create more efficient and compact systems.
Furthermore, the integration of electronic controls and sensors is essential in modern engine design. These systems monitor and adjust engine parameters in real-time, optimizing performance and fuel efficiency. By fine-tuning fuel injection, ignition timing, and other critical parameters, engines can operate at their most efficient levels, ensuring that every drop of fuel contributes to forward motion.
Electric Cars: The Green Revolution or Fossil Fuel's Last Stand?
You may want to see also
Hybrid Technology: Combining electric motors with traditional engines for enhanced efficiency
Hybrid technology is a groundbreaking innovation in the automotive industry, revolutionizing the way cars are powered and significantly improving fuel efficiency. This advanced system combines the strengths of both electric motors and traditional internal combustion engines, offering a more efficient and environmentally friendly driving experience. By integrating these two power sources, manufacturers aim to reduce fuel consumption and minimize the environmental impact of vehicles.
In a hybrid system, the electric motor plays a crucial role in enhancing efficiency. It provides additional power to the wheels, especially during acceleration or when extra torque is required. When the driver needs a burst of speed or when climbing uphill, the electric motor kicks in, delivering instant power without the lag associated with traditional engines. This results in smoother acceleration and improved performance, all while consuming less fuel. The electric motor also acts as a generator, recharging the battery pack during deceleration or when the car is in idle mode, ensuring a continuous supply of energy.
The traditional internal combustion engine, often a gasoline or diesel motor, continues to play a vital role in hybrid systems. It operates as a secondary power source, providing additional assistance when the electric motor alone may not be sufficient. For example, during high-speed cruising or when the battery is depleted, the conventional engine takes over, ensuring the vehicle can maintain its speed and functionality. This dual-power approach allows for a more efficient use of energy, as the conventional engine can be optimized for fuel economy while the electric motor handles specific driving conditions.
One of the key advantages of hybrid technology is its ability to recover and reuse energy that would otherwise be wasted. Regenerative braking, for instance, captures the kinetic energy generated during braking and converts it back into electrical energy, recharging the battery. This process not only improves overall efficiency but also extends the range of the vehicle, making it more practical for everyday use. Additionally, hybrid systems often incorporate start-stop technology, where the conventional engine automatically shuts off when the car is stationary, reducing fuel consumption and emissions.
Hybrid technology offers a promising solution to the challenge of improving fuel efficiency in automobiles. By combining electric motors and traditional engines, manufacturers can create vehicles that are not only more environmentally friendly but also provide a seamless driving experience. This innovative approach has led to the development of various hybrid models, each offering unique benefits and contributing to a more sustainable future for the automotive industry.
E85 Fuel: Signs Your Car Can Run on Ethanol Blend
You may want to see also
Turbocharging: Increasing power output without significantly boosting fuel consumption
Turbocharging is a technique employed by car manufacturers to enhance engine performance while maintaining or even improving fuel efficiency. This method involves forcing extra air into the engine's combustion chamber, which, in turn, increases the power output without a proportional rise in fuel consumption. The process is achieved by utilizing a turbine to compress the air, which is then fed into the engine alongside the fuel. This compression allows for a more efficient combustion process, resulting in increased power and torque.
The key advantage of turbocharging is its ability to provide an immediate power boost, especially at lower engine speeds. When a driver requires a sudden surge of power, such as when overtaking or accelerating quickly, the turbocharger rapidly spins up, delivering an extra dose of air and fuel to the engine. This ensures that the vehicle responds promptly and effectively, all while maintaining a relatively low fuel consumption rate. The turbocharger's response time is crucial, as it can quickly adapt to the driver's needs, providing an efficient and powerful driving experience.
In the design of turbochargers, engineers focus on optimizing the turbine and compressor sizes and positions. A smaller turbine wheel can efficiently extract energy from the engine's exhaust gases, while a larger compressor wheel ensures a sufficient amount of air is forced into the engine. The positioning of these components is critical; placing the turbine in the exhaust stream and the compressor in the intake tract allows for a more compact and efficient design. This arrangement also helps to reduce the turbo lag, which is the delay between the driver's demand for power and the turbocharger's response.
One of the challenges in turbocharging is managing the increased engine load, especially during rapid acceleration or high-performance driving. To address this, manufacturers employ advanced engine management systems that carefully control the fuel injection and timing. These systems ensure that the engine receives the right amount of fuel to match the available air, preventing over-fuelling and the associated increase in fuel consumption. Additionally, the use of precision turbochargers with variable geometry can further optimize performance by adjusting the turbine's blade angle, allowing for better control over power delivery and fuel efficiency.
In summary, turbocharging is a sophisticated technology that enables car manufacturers to enhance engine power without compromising fuel efficiency. By utilizing the principles of forced induction, manufacturers can provide drivers with a responsive and powerful driving experience while maintaining a relatively low fuel consumption rate. This technique showcases the innovative approaches taken by the automotive industry to meet the demands of modern drivers, offering both performance and efficiency in a single package.
Fuel Flushing: Myth or Magic? Unlocking Car Engine Potential
You may want to see also
Direct Injection: Precise fuel delivery for optimal combustion and reduced emissions
Direct injection is a revolutionary technology that has significantly contributed to enhancing engine fuel efficiency and reducing emissions in modern automobiles. This innovative system involves injecting fuel directly into the combustion chamber, bypassing the traditional intake manifold or carburetor. By doing so, it offers several advantages that lead to improved performance and efficiency.
The primary benefit of direct injection is the precise control it provides over the fuel-air mixture. In conventional engines, fuel is mixed with air in the intake manifold, and this mixture is then drawn into the cylinders. However, this process can result in uneven fuel distribution and air-fuel ratios that are not always optimal. Direct injection, on the other hand, allows for a more accurate and controlled fuel injection process. Fuel is injected directly into the combustion chamber, ensuring that the air-fuel mixture is perfectly balanced. This precision leads to more efficient combustion, as the fuel is injected at the exact moment when the air-fuel mixture is most receptive to ignition, maximizing power output while minimizing fuel consumption.
Furthermore, direct injection enables the use of higher compression ratios, which is another factor contributing to improved fuel efficiency. Higher compression ratios mean that the air-fuel mixture can be compressed more densely before ignition, resulting in more complete combustion. This increased efficiency is particularly noticeable during part-load conditions, where engines typically operate less efficiently. With direct injection, engines can maintain optimal performance and fuel economy even when running at lower speeds or loads.
The technology also plays a crucial role in reducing emissions. By delivering fuel directly to the combustion chamber, direct injection minimizes the formation of harmful pollutants. The precise control over the fuel-air mixture allows for more efficient combustion, leading to lower emissions of nitrogen oxides (NOx) and particulate matter. Additionally, the ability to inject fuel at higher pressures and in smaller, more frequent doses further contributes to improved combustion quality and reduced emissions.
In summary, direct injection is a game-changer in the pursuit of enhanced engine fuel efficiency and reduced environmental impact. Its ability to provide precise fuel delivery, enable higher compression ratios, and minimize emissions makes it an essential component in modern engine design. As automotive manufacturers continue to refine this technology, we can expect even more efficient and environmentally friendly vehicles in the future.
Is It Safe to Open the Fuel Cap While Your Car Is Running?
You may want to see also
Lightweight Materials: Using advanced materials to lower vehicle weight and improve mileage
The automotive industry is constantly seeking ways to enhance fuel efficiency, and one of the most effective strategies involves the use of lightweight materials. By reducing the overall weight of a vehicle, manufacturers can significantly improve mileage and performance. This approach is based on the principle that a lighter car requires less energy to accelerate and maintain speed, resulting in reduced fuel consumption.
Lightweight materials, such as advanced alloys, carbon fiber composites, and high-strength polymers, are being increasingly utilized in vehicle construction. These materials offer exceptional strength-to-weight ratios, allowing engineers to create sturdy yet lightweight components. For instance, carbon fiber-reinforced polymers (CFRPs) have gained popularity in high-performance vehicles due to their exceptional strength and stiffness while being significantly lighter than traditional steel or aluminum. By incorporating these materials into the vehicle's body, chassis, and even engine components, manufacturers can achieve substantial weight savings without compromising structural integrity.
One of the key advantages of lightweight materials is their ability to reduce the vehicle's unsprung mass. Unsprung mass refers to the weight of components that are not directly attached to the wheels, such as the body, interior trim, and various accessories. By minimizing unsprung mass, manufacturers can improve the vehicle's suspension efficiency, leading to better handling, reduced tire wear, and, most importantly, enhanced fuel economy. Lighter components also contribute to a more responsive vehicle, making it easier for drivers to control and maneuver.
The use of lightweight materials extends beyond the vehicle's structure. Engine manufacturers are also adopting lightweight alloys and composites to reduce the weight of internal components. Lighter engines not only improve mileage but also contribute to better acceleration and overall performance. Additionally, lightweight materials can help in reducing the overall weight of the vehicle, which indirectly leads to improved fuel efficiency by reducing the energy required to move the car.
In summary, the adoption of lightweight materials is a crucial aspect of car manufacturing that significantly contributes to engine fuel efficiency. By utilizing advanced materials, manufacturers can create vehicles that are not only more efficient but also offer improved performance and handling. This strategy is an essential part of the ongoing efforts to make automobiles more environmentally friendly and cost-effective for consumers.
F1 Fuel: Powering the Ultimate Speed Machines
You may want to see also
Frequently asked questions
Car manufacturers employ various strategies to enhance engine fuel efficiency, aiming to optimize power output while reducing fuel consumption. These methods include advanced engine designs, lightweight materials, improved combustion processes, and the integration of advanced technologies.
Engine design is crucial for fuel efficiency. Manufacturers focus on optimizing the engine's layout, cylinder arrangement, and combustion chamber design. Modern engines often feature downsizing with turbocharging, direct fuel injection, and variable valve timing to improve power and efficiency.
Using lightweight materials in vehicle construction can significantly reduce weight without compromising structural integrity. Lighter vehicles require less energy to accelerate and maintain speed, resulting in improved fuel efficiency. Materials like aluminum, high-strength steel, and carbon fiber composites are commonly used to achieve this.
Advanced combustion technologies play a vital role in optimizing fuel-air mixture and combustion processes. Direct fuel injection, for instance, ensures precise fuel delivery, allowing for better control over the combustion process. This results in improved power output and reduced fuel consumption.
Electric and hybrid vehicle systems offer significant advantages in fuel efficiency. Hybrid vehicles combine a conventional engine with an electric motor, allowing for efficient power delivery and regenerative braking. Electric vehicles, powered solely by electricity, eliminate direct fuel consumption, leading to zero tailpipe emissions and excellent fuel economy.