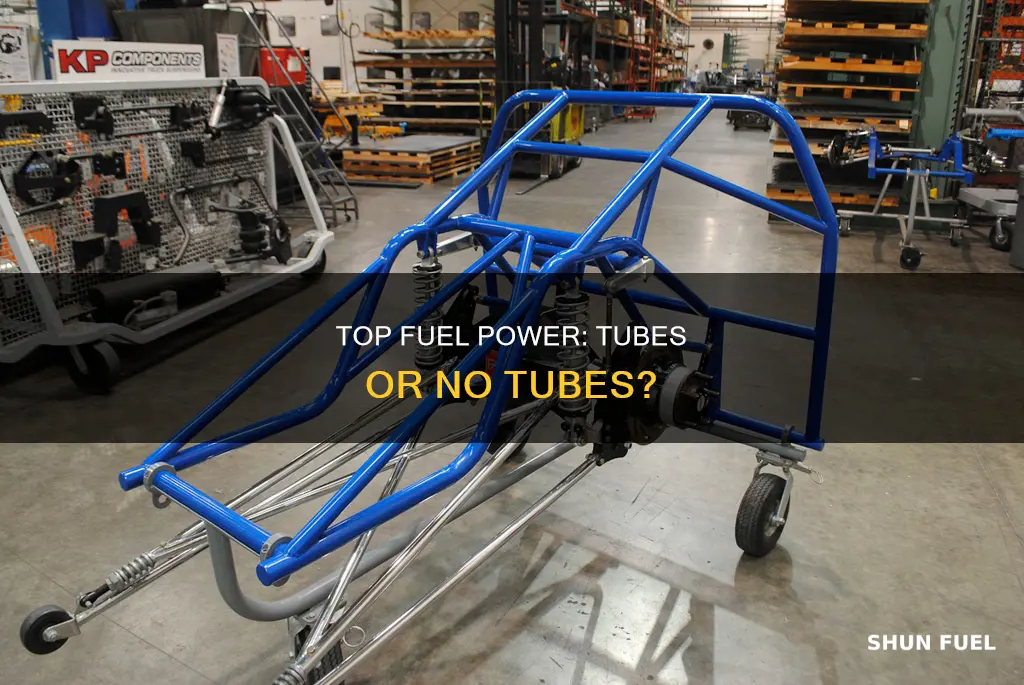
Top Fuel cars, known for their incredible speed and power, are a staple of drag racing. One of the most intriguing aspects of these vehicles is their unique fuel system, which involves the use of tubes to deliver fuel to the engine. In this paragraph, we will explore the role of tubes in Top Fuel cars and how they contribute to the intense performance of these machines.
Characteristics | Values |
---|---|
Engine Type | Nitromethane-powered V8 |
Power Output | Over 10,000 horsepower |
Top Speed | Approximately 320 mph (515 km/h) |
Thrust | Around 1000 pounds (447 kg) of thrust |
Transmission | Manual, 4-speed |
Tires | Large, drag-specific tires with no inner tubes |
Body Material | Lightweight carbon fiber or aluminum |
Weight | Typically around 2,000 pounds (907 kg) |
Length | About 20 feet (6 meters) |
Width | Around 8 feet (2.4 meters) |
Height | Less than 5 feet (1.5 meters) |
Fuel Consumption | Extremely high, requiring frequent refueling |
Fuel Efficiency | Very low, with fuel usage proportional to power output |
Aerodynamics | Highly optimized for high-speed stability |
Safety Features | Extensive roll cage, fire suppression systems |
What You'll Learn
- Engine Design: Top Fuel cars use unique, powerful engines with specific tube configurations
- Performance: Tubes enhance performance by directing exhaust and managing engine pressure
- Safety: Proper tube design is crucial for safety, preventing explosions and engine damage
- Materials: Advanced materials are used to create durable, heat-resistant tubes for extreme conditions
- Tuning: Tuning tube systems is essential for optimizing power and controlling engine output
Engine Design: Top Fuel cars use unique, powerful engines with specific tube configurations
Top Fuel cars are renowned for their extreme performance and unique engine design, which is a critical component of their success on the drag strip. These engines are specifically engineered to produce an immense amount of power, often exceeding 10,000 horsepower, and are a far cry from the standard automotive setups. One of the key features that sets Top Fuel engines apart is their use of specific tube configurations, which are integral to the overall design and performance.
The tube configuration in these engines is a complex arrangement of exhaust pipes and headers designed to optimize power and efficiency. Unlike conventional cars, Top Fuel engines utilize a unique system where the exhaust gases are directed through a series of tubes, often in a circular or spiral pattern, before exiting the vehicle. This design is crucial as it helps to manage the extreme temperatures and pressures generated by the powerful combustion process. The tubes are typically made from heat-resistant materials to withstand the intense heat, ensuring the engine's longevity and reliability during high-speed runs.
Engineers have carefully calculated the dimensions and layout of these tubes to maximize power output. The length, diameter, and angle of the tubes are precisely determined to control the exhaust gas flow, ensuring optimal performance. This intricate design also helps to minimize back pressure, allowing the engine to breathe more efficiently and extract every last bit of power from the fuel and air mixture. The specific tube configuration is a well-guarded secret among Top Fuel teams, as it is a critical factor in their competitive advantage.
Furthermore, the tube configuration also plays a vital role in noise reduction. Top Fuel cars are known for their thunderous roar, which is a result of the powerful exhaust system. The carefully designed tubes help to dampen and direct the noise, ensuring it remains within acceptable limits while still providing an exhilarating sound for spectators. This balance between power and noise management is a testament to the intricate engineering that goes into Top Fuel engine design.
In summary, the unique engine design of Top Fuel cars, with their specific tube configurations, is a key element in achieving the extraordinary performance these vehicles are known for. The careful arrangement of exhaust tubes manages extreme temperatures, optimizes power output, and contributes to the distinctive sound that makes Top Fuel racing so captivating. This specialized engine design is a prime example of how innovative engineering can be applied to create some of the most powerful and exciting vehicles on the planet.
The Ultimate Guide to the Most Fuel-Efficient Cars
You may want to see also
Performance: Tubes enhance performance by directing exhaust and managing engine pressure
The use of tubes in Top Fuel drag racing cars is a critical component that significantly impacts performance. These tubes serve multiple purposes, primarily focusing on exhaust management and engine pressure optimization. By carefully directing the exhaust gases, these tubes ensure that the engine's power is efficiently transferred to the rear wheels, propelling the car forward with maximum force. This is especially crucial in Top Fuel racing, where the goal is to achieve the highest possible acceleration over a short distance.
One of the key advantages of these tubes is their ability to manage engine pressure. Top Fuel engines operate at extremely high power levels, generating immense pressure within the combustion chambers. Without proper exhaust management, this pressure could lead to engine damage or even catastrophic failure. The tubes act as a controlled exhaust system, allowing the exhaust gases to escape efficiently while maintaining the necessary pressure for optimal performance. This pressure management is vital for maintaining the engine's power output and ensuring the car's reliability during the race.
The design and placement of these tubes are carefully considered to optimize performance. They are typically routed through the car's body, often in a straight line, to minimize turbulence and ensure a smooth flow of exhaust gases. This straight path helps maintain a consistent pressure differential, allowing the engine to operate at its peak efficiency. Additionally, the tubes are often made of lightweight materials to reduce overall weight, which is crucial in drag racing where every pound matters.
Furthermore, the tubes play a role in noise management. Top Fuel cars are known for their thunderous roar, which is a result of the high-pressure exhaust gases escaping. The tubes help control and direct this noise, ensuring it exits the car in a controlled manner. This not only contributes to the overall performance but also meets the safety regulations, as excessive noise can be a hazard for both the drivers and spectators.
In summary, the tubes in Top Fuel cars are essential for enhancing performance by effectively managing exhaust and engine pressure. Their strategic placement and design ensure optimal power transfer, reliability, and noise control, all of which are critical factors in achieving success on the drag strip. Understanding the role of these tubes provides valuable insight into the intricate engineering that powers these high-performance vehicles.
Car Fuel Type: Quick Guide to Knowing What Your Vehicle Needs
You may want to see also
Safety: Proper tube design is crucial for safety, preventing explosions and engine damage
The design and construction of tubes in Top Fuel cars are critical aspects that directly impact the vehicle's performance and safety. These cars operate under extreme conditions, with powerful engines producing immense force and heat, making the choice of materials and design a complex engineering challenge. Proper tube design is essential to ensure the vehicle's longevity and the safety of the crew.
One of the primary concerns in tube design is the prevention of explosions. Top Fuel cars use highly compressed fuel and air mixtures, which are ignited by a powerful spark plug. The rapid combustion process generates an enormous amount of energy, and any failure in the tube system could lead to a catastrophic explosion. Engineers must carefully select materials that can withstand the extreme pressures and temperatures involved. For instance, the tubes should be made of high-strength alloys that can resist the intense heat generated by the engine without compromising structural integrity.
Additionally, the tube design should incorporate features that prevent the buildup of pressure. This is crucial as excessive pressure can lead to tube failure, causing potentially dangerous situations. One approach is to use a series of small, evenly spaced orifices or perforations along the length of the tube. These openings allow for the controlled release of pressure, reducing the risk of explosions. The design must also consider the flow rate and ensure that the pressure is distributed evenly to avoid localized hotspots.
Furthermore, the tubes should be designed to withstand the mechanical stresses imposed by the engine's operation. The engine's movement and vibrations can cause the tubes to flex and bend, potentially leading to cracks or failures. Engineers often employ techniques such as tube bracing, using rigid materials, and implementing flexible joints to accommodate the engine's movement while maintaining structural integrity.
In summary, the tube design in Top Fuel cars is a critical safety feature that requires meticulous attention to detail. By selecting appropriate materials, incorporating pressure relief mechanisms, and accounting for mechanical stresses, engineers can ensure that the tubes can withstand the extreme conditions of the engine. This meticulous design approach is essential to prevent explosions, engine damage, and ensure the overall safety of the vehicle and its crew.
Green Energy, Green Cars? Unveiling Fuel Cell Technology's Environmental Impact
You may want to see also
Materials: Advanced materials are used to create durable, heat-resistant tubes for extreme conditions
The use of advanced materials in the construction of Top Fuel dragsters is a critical aspect of their design, especially when it comes to the tubes that form the backbone of these powerful machines. These tubes, often referred to as 'tubing,' are designed to withstand the extreme conditions encountered during a race, including intense heat, high pressure, and rapid acceleration. The primary goal is to ensure the structural integrity of the vehicle while also optimizing performance.
One of the key materials utilized in these tubes is a specialized type of steel known for its exceptional strength and heat resistance. This steel is carefully selected and treated to meet the rigorous demands of the sport. The manufacturing process involves precise welding techniques to join the steel into seamless tubes, ensuring a continuous and robust structure. The welding process is a critical step, as it must create a strong bond without introducing any weaknesses or imperfections that could compromise the tube's integrity.
Advanced composites and alloys are also employed to further enhance the tubes' performance. These materials offer improved heat dissipation, which is crucial for managing the extreme temperatures generated by the powerful engines. By incorporating these advanced composites, the tubes can better withstand the thermal stresses experienced during a race, ensuring they remain stable and functional even at extremely high temperatures.
The design and material selection of these tubes are highly specialized and often involve extensive research and development. Engineers and designers work closely to optimize the tube's dimensions, wall thickness, and material composition to achieve the perfect balance between strength, weight, and heat resistance. This meticulous approach ensures that the tubes can handle the immense forces and stresses encountered during a Top Fuel race, contributing to the overall success and safety of the vehicle.
In summary, the use of advanced materials in creating durable, heat-resistant tubes is a vital component of Top Fuel car design. These materials, including specialized steels, composites, and alloys, are carefully engineered to meet the extreme demands of the sport, ensuring the structural integrity and performance of the vehicle. The process involves meticulous manufacturing and design, showcasing the intricate relationship between materials and performance in the world of high-speed racing.
Can I Run Phillips 66 100LL Fuel in My Car?
You may want to see also
Tuning: Tuning tube systems is essential for optimizing power and controlling engine output
Tuning the exhaust system of a Top Fuel dragster is a critical aspect of performance optimization, especially in the quest for maximum power and controlled engine output. These cars are renowned for their extreme power, often exceeding 10,000 horsepower, and the exhaust system plays a pivotal role in managing this output. The primary goal of tuning the exhaust is to ensure efficient power delivery while maintaining control over the engine's performance.
One of the key components in this system is the exhaust tubes, which are responsible for directing the high-pressure, high-temperature exhaust gases away from the driver and toward the ground-effect body, which provides downforce. These tubes are meticulously designed and positioned to optimize flow, ensuring that the exhaust gases are expelled efficiently and rapidly. The tuning process involves adjusting the diameter, length, and angle of these tubes to achieve the desired performance characteristics. For instance, larger diameter tubes can increase flow capacity, allowing for more efficient power release, while smaller tubes might be used to restrict flow, creating a power band that peaks at a specific RPM range.
The tuning process also involves considering the material of the exhaust tubes. Different metals, such as stainless steel or aluminum, offer varying levels of heat resistance and weight. Choosing the right material is crucial, as it directly impacts the durability and performance of the system. For instance, stainless steel is known for its excellent heat resistance and corrosion resistance, making it a popular choice for high-performance applications.
Additionally, the tuning process often includes the use of various exhaust control devices. These devices, such as wastegates and blow-off valves, are strategically placed to control the flow of exhaust gases, especially during the critical stages of the race. Wastegates, for example, are used to manage boost pressure, ensuring that the engine doesn't over-boost and potentially damage itself. Blow-off valves release excess pressure, improving throttle response and overall performance.
In summary, tuning the exhaust tube system in Top Fuel cars is a complex and precise process. It involves careful consideration of tube dimensions, materials, and the strategic use of control devices to optimize power output and manage the extreme conditions of drag racing. This meticulous tuning ensures that the engine's power is harnessed effectively, providing the necessary acceleration down the drag strip while maintaining control and safety.
Fuel Injector Power: Can You Damage Your Car?
You may want to see also
Frequently asked questions
Yes, Top Fuel cars do utilize tubes, but not in the conventional sense like the ones you might see in a bicycle or a car's suspension. Instead, these cars use a unique system called a "tuber" or "tuber system." This system is a type of fuel injection that delivers nitrous oxide (N2O) to the engine, providing an extra boost of power. The "tuber" is a small, flexible tube that connects the nitrous oxide tank to the engine, allowing for precise control and delivery of the nitrous.
The tuber system is a sophisticated setup that involves a solenoid-operated valve, which opens when the driver activates the nitrous button. This valve releases a controlled amount of nitrous oxide into the engine's intake manifold, increasing power output. The tuber system is designed to be quick-acting, providing an instant power boost when needed during a race.
Absolutely! The use of tubes in the tuber system offers several benefits. Firstly, it allows for a more efficient and controlled delivery of nitrous oxide, ensuring that the engine receives the precise amount needed for optimal performance. Secondly, the flexibility of the tubes enables them to withstand the extreme forces and vibrations experienced during high-speed runs, making them a reliable component.
In a conventional fuel injection system, fuel and air are mixed and injected into the engine's cylinders. In contrast, the tuber system specifically delivers nitrous oxide, which is a powerful oxidizer, to the engine's intake. This additional nitrous oxide increases the combustion efficiency, resulting in a significant power gain. The tuber system is designed to work in conjunction with the existing fuel injection to provide a unique and powerful performance enhancement.
Safety is a critical aspect of any racing application. In the case of Top Fuel cars, the tuber system must be designed and installed with strict safety standards in mind. This includes using high-quality materials that can withstand extreme temperatures and pressures, as well as implementing fail-safe mechanisms to prevent any potential hazards. Proper maintenance and regular inspections are also essential to ensure the system's reliability and safety.