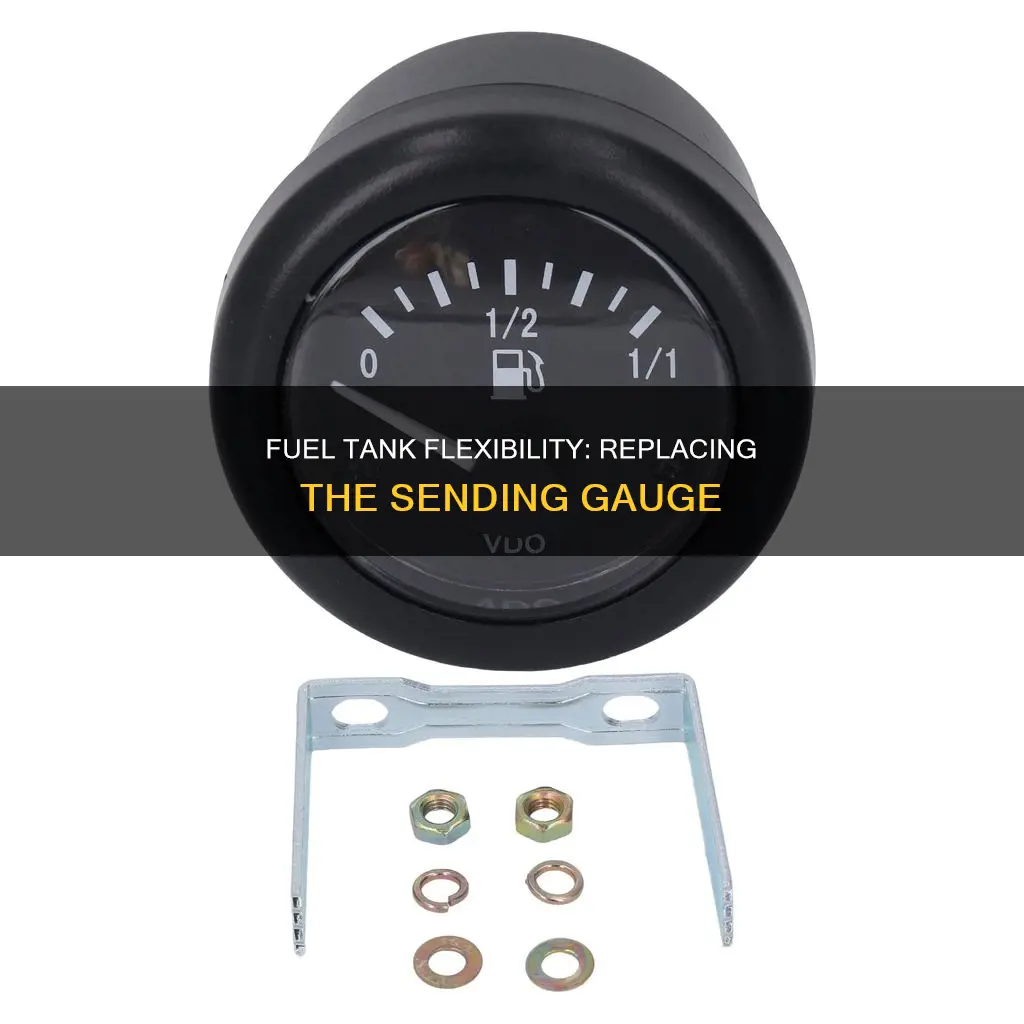
The sending gauge, a critical component in a fuel tank's monitoring system, plays a vital role in providing accurate fuel level readings to the driver. However, over time, this gauge can wear out or malfunction, leading to inaccurate fuel level indications. This raises the question: Can the sending gauge be replaced in a fuel tank? Understanding the feasibility and process of replacing this gauge is essential for vehicle owners to ensure reliable fuel level monitoring and maintain their vehicles' performance.
Characteristics | Values |
---|---|
Reusability | Yes, the sending gauge can often be replaced without replacing the entire fuel tank. |
Common Issues | Sending gauges can fail due to sensor problems, electrical issues, or wear and tear. |
Symptoms of Failure | Engine warning lights, inaccurate fuel level readings, or no fuel level indication. |
Replacement Process | 1. Drain the fuel tank. 2. Remove the old sending gauge. 3. Install the new gauge, ensuring proper connections. 4. Refill the tank and test. |
DIY vs. Professional | DIY replacement is possible for those with mechanical skills, but professional assistance is recommended for complex systems. |
Cost | The cost varies depending on the make and model, but it's generally more affordable than replacing the entire tank. |
Warranty | Check the manufacturer's warranty for the sending gauge, as it may cover replacements under certain conditions. |
Safety Considerations | Ensure the fuel tank is empty and properly drained before attempting any replacement to avoid fuel spills. |
What You'll Learn
- Materials Compatibility: Exploring suitable materials for a new sending gauge to avoid corrosion
- Electrical Connections: Ensuring proper wiring and grounding for the replacement gauge
- Pressure Tolerance: Testing the new gauge's ability to withstand fuel tank pressure
- Sealing Techniques: Using effective seals to prevent fuel leaks
- Calibration Methods: Adjusting the replacement gauge for accurate fuel level readings
Materials Compatibility: Exploring suitable materials for a new sending gauge to avoid corrosion
When considering replacing the sending gauge in a fuel tank, it's crucial to focus on materials compatibility to prevent corrosion and ensure the longevity of the new gauge. The sending gauge, also known as a fuel level sensor, is a critical component that measures the amount of fuel in the tank and sends this information to the vehicle's engine control unit (ECU). Over time, the original gauge can deteriorate due to exposure to fuel, moisture, and other environmental factors, leading to inaccurate readings and potential performance issues.
One of the primary concerns in materials selection is corrosion resistance. The sending gauge is typically in close contact with the fuel, which can vary in composition and quality. Some fuels contain additives and impurities that can accelerate corrosion. Therefore, the chosen material must be able to withstand the corrosive effects of the fuel without degrading over time. Common materials used for such applications include stainless steel, which offers excellent corrosion resistance due to its chromium content, forming a protective oxide layer on its surface. Alternatively, certain alloys like Monel or Inconel, known for their high resistance to corrosion in harsh environments, can be considered.
Additionally, the chosen material should be compatible with the surrounding environment, including the temperature and pressure conditions within the fuel tank. The gauge must operate reliably across a range of temperatures and pressures without compromising its structural integrity. For instance, materials like brass or bronze might not be suitable due to their lower melting points, which could lead to melting or warping under extreme conditions. Instead, materials with higher melting points, such as aluminum alloys or certain types of steel, can provide better performance and durability.
Another aspect to consider is the electrical conductivity of the material, especially if the sending gauge is an electronic sensor. The material should have suitable electrical properties to ensure accurate signal transmission to the ECU. Copper or copper alloys are often used for their excellent electrical conductivity, making them ideal for electronic components. However, it's essential to ensure that the chosen material also meets the required mechanical and environmental standards.
In summary, when replacing the sending gauge, careful consideration of materials compatibility is vital. The selected material should exhibit superior corrosion resistance to withstand the fuel's corrosive nature, operate reliably across various environmental conditions, and possess the necessary electrical conductivity for accurate sensor function. By choosing the right materials, you can ensure a long-lasting and efficient sending gauge replacement, addressing the issue of 'can the sending gauge be replaced in a fuel tank' with a well-informed and practical solution.
Fuel Injector Replacement: Perks of Replacing in Sets
You may want to see also
Electrical Connections: Ensuring proper wiring and grounding for the replacement gauge
When replacing the sending gauge in a fuel tank, ensuring proper electrical connections is crucial to guarantee accurate fuel level readings and prevent any potential issues. Here's a detailed guide on how to approach the electrical connections:
Wiring the New Gauge: Begin by carefully disconnecting the old sending gauge's wiring. Take note of the color-coded wires and their respective functions. Typically, you'll find wires for power, ground, and signal. Strip the insulation from the wires, ensuring you expose the correct amount of wire for soldering or connecting with the new gauge. When installing the new gauge, match the wires to the corresponding terminals. The power wire should be connected to the positive terminal, the ground wire to the negative terminal, and the signal wire to the gauge's output. Secure the connections with electrical tape or heat-shrink tubing to prevent any accidental disconnections.
Grounding: Proper grounding is essential for the electrical system's reliability and safety. Locate the ground wire from the new gauge and connect it to a solid metal surface within the fuel tank, such as the tank itself or a dedicated grounding point. Ensure the connection is clean and free of corrosion. Additionally, check the vehicle's chassis for a reliable ground point and connect the gauge's ground wire to it. This step ensures that any electrical interference or noise is minimized, providing accurate readings.
Testing and Verification: After completing the wiring and grounding, it's crucial to test the new gauge's functionality. Start the vehicle's engine and check the fuel gauge's response. Ensure it accurately reflects the fuel level as you add or remove fuel from the tank. Verify that the gauge responds promptly and accurately to changes in fuel volume. If everything functions correctly, you can be confident that the electrical connections are secure and the new sending gauge is operating as intended.
Remember, when working with electrical components, it's essential to exercise caution and ensure you have a thorough understanding of the vehicle's wiring diagram. If you're unsure, consulting a professional mechanic or referring to the vehicle's manual is highly recommended to avoid any potential hazards or system malfunctions.
Replacing Tecumseh TVXL220 Fuel Line: A Step-by-Step Guide
You may want to see also
Pressure Tolerance: Testing the new gauge's ability to withstand fuel tank pressure
The process of replacing the sending gauge in a fuel tank involves ensuring the new gauge can withstand the pressure and conditions within the tank. This is a critical aspect of the replacement, as the gauge must be able to accurately measure fuel levels and pressure without being compromised by the environment.
When testing the pressure tolerance of the new gauge, it is essential to simulate the actual conditions inside a fuel tank. This includes subjecting the gauge to the typical pressure ranges it will encounter. Fuel tanks can experience varying levels of pressure depending on the vehicle's speed, engine load, and other factors. By testing the gauge under these conditions, you can ensure its accuracy and reliability.
One method to test pressure tolerance is to use a specialized test equipment that can create a controlled environment. This equipment can simulate the fuel tank's pressure and temperature, allowing for a comprehensive evaluation. The gauge should be connected to this system, and its readings should be monitored while applying different pressure levels. The goal is to observe if the gauge's performance remains stable and accurate without any signs of malfunction or distortion.
Additionally, it is crucial to consider the physical design and materials of the gauge. The sending gauge should be constructed with durable components that can withstand the corrosive nature of fuel and the internal pressure. Materials such as stainless steel or specialized alloys might be used to ensure longevity and resistance to degradation.
During the testing phase, it is recommended to document the gauge's behavior under various pressure conditions. This documentation should include notes on the gauge's accuracy, response time, and any observed anomalies. By thoroughly testing the pressure tolerance, you can identify any potential issues and ensure that the new sending gauge meets the required standards for reliable fuel level monitoring.
Replacing RDX Fuel Filter: Step-by-Step Guide for Easy Maintenance
You may want to see also
Sealing Techniques: Using effective seals to prevent fuel leaks
When it comes to preventing fuel leaks in a vehicle's fuel tank, the use of effective sealing techniques is crucial. One common issue that can arise is the need to replace the sending gauge, which measures the fuel level and sends this information to the engine control unit. While this component can be replaced, it is essential to ensure that the tank is properly sealed to avoid any potential leaks.
One sealing technique involves the use of o-rings or gaskets. These are circular seals made of rubber or a similar material that can be installed around the fuel tank's openings and connections. O-rings provide a tight, flexible seal, ensuring that no fuel can escape. They are commonly used in fuel tank assemblies and can be easily replaced if worn out. It is important to choose the correct size and type of o-ring for the specific application to ensure a proper fit.
Another effective sealing method is the use of fuel tank seals, which are designed to create a barrier around the fuel tank. These seals are typically made of durable materials such as rubber or silicone and are engineered to withstand the harsh conditions inside a fuel tank. They are often used in conjunction with o-rings to provide an additional layer of protection. Fuel tank seals can be custom-made or purchased as pre-formed seals, ensuring a precise fit.
Additionally, the use of fuel tank sealing tape can be beneficial. This tape is specifically designed to adhere to the interior surfaces of the tank and create a secure seal. It is particularly useful for repairing small holes or cracks in the tank's walls. The tape is applied carefully, ensuring full coverage, and can provide a long-lasting solution to prevent fuel leaks.
In summary, when dealing with fuel tank sealing, it is essential to employ various techniques to ensure a robust and reliable system. By using o-rings, fuel tank seals, and sealing tape, you can effectively prevent fuel leaks and maintain the integrity of the fuel system. These methods provide a comprehensive approach to sealing, offering flexibility, durability, and precision to accommodate different fuel tank designs and requirements.
Fuel Filter Replacement: Enhancing Engine Performance and Efficiency
You may want to see also
Calibration Methods: Adjusting the replacement gauge for accurate fuel level readings
The process of replacing a sending gauge in a fuel tank and calibrating it for accurate fuel level readings involves several steps and requires a systematic approach. This is crucial to ensure that the new gauge provides reliable and precise fuel level information to the driver. Here's an overview of the calibration methods:
Initial Setup and Preparation: Before beginning the calibration, it is essential to have the necessary tools and equipment. This includes a fuel tank gauge replacement kit, which typically consists of the new sending gauge, wiring harnesses, and any additional components required for the specific vehicle model. Ensure that you have access to a fuel pressure gauge and a fuel pressure regulator to monitor and control the fuel pressure during the calibration process. Additionally, gather the vehicle's service manual or technical specifications to guide your calibration process.
Fuel Tank Drain and Preparation: Start by draining the fuel tank to ensure an accurate reading. Locate the fuel drain valve, usually found beneath the vehicle, and open it to release the fuel. Allow the tank to drain completely, and then securely close the valve. This step is crucial to prevent any fuel spillage and to ensure a safe working environment. Once drained, clean the fuel tank interior to remove any debris or contaminants that might interfere with the gauge installation.
Installing the New Sending Gauge: With the fuel tank empty and prepared, proceed with the installation of the new sending gauge. Carefully follow the manufacturer's instructions or the vehicle's service manual for specific guidance. Typically, the sending gauge is connected to the fuel tank via a fuel line. Ensure a secure and tight connection to prevent any fuel leaks. After installation, allow a brief period for the system to stabilize, as the fuel pressure may need to equalize.
Calibration Process: Calibration involves adjusting the new sending gauge to match the actual fuel level accurately. This is done by using the fuel pressure gauge and regulator to control the fuel pressure and volume. Start by setting the fuel pressure to a known value, typically the manufacturer's recommended pressure. Then, gradually increase or decrease the fuel pressure in small increments while monitoring the gauge's reading. Adjust the gauge's sensitivity or offset settings until the displayed fuel level matches the actual fuel level indicated by the fuel pressure gauge. This process may require fine-tuning and multiple iterations to achieve precision.
Testing and Verification: After the initial calibration, it is essential to test the system thoroughly. Refill the fuel tank and observe the gauge's response to changes in fuel level. Ensure that the gauge provides accurate readings as the fuel is added or removed. Perform this test multiple times to verify consistency and accuracy. If any discrepancies are noted, carefully review the calibration settings and make adjustments as necessary.
Final Adjustments and Fine-Tuning: If the gauge still requires adjustments, consider the following: Check the gauge's sensitivity and offset settings, making small changes to see if it improves accuracy. Verify the fuel pressure regulator's calibration and ensure it is functioning correctly. Inspect the fuel line connections for any blockages or restrictions that might affect fuel flow. Fine-tune the calibration process until the gauge provides consistently accurate fuel level readings.
By following these calibration methods, you can ensure that the replacement sending gauge provides reliable and precise fuel level information, enhancing the overall functionality of the fuel tank system. Proper calibration is essential for driver safety, efficient fuel management, and maintaining the vehicle's performance.
Outboard Fuel Maintenance: Replacing the Water Separator
You may want to see also
Frequently asked questions
Yes, replacing the sending gauge is a relatively straightforward process. It is a common task for DIY enthusiasts and mechanics, and the specific steps may vary depending on the vehicle model and gauge type.
The sending gauge, also known as the fuel level sensor, can malfunction due to several reasons. These include corrosion or damage to the sensor, poor connections, or issues with the wiring harness. Environmental factors like extreme temperatures or fuel contamination can also contribute to its failure.
There are several signs that may indicate a faulty sending gauge. These include inaccurate fuel level readings, erratic behavior, or the gauge not working at all. You might also notice issues with the fuel gauge's operation, such as slow responses or sudden spikes in the fuel level display.
While some individuals with mechanical knowledge might attempt a DIY replacement, it is generally recommended to have a professional mechanic handle this task. The process requires precision and an understanding of the vehicle's electrical system to ensure proper installation and avoid further complications.
The tools required for this replacement vary depending on the vehicle. Basic tools like screwdrivers, wrenches, and wire connectors are often sufficient. However, more complex procedures might demand specialized tools, such as a fuel tank removal kit or diagnostic equipment, to ensure a successful repair.