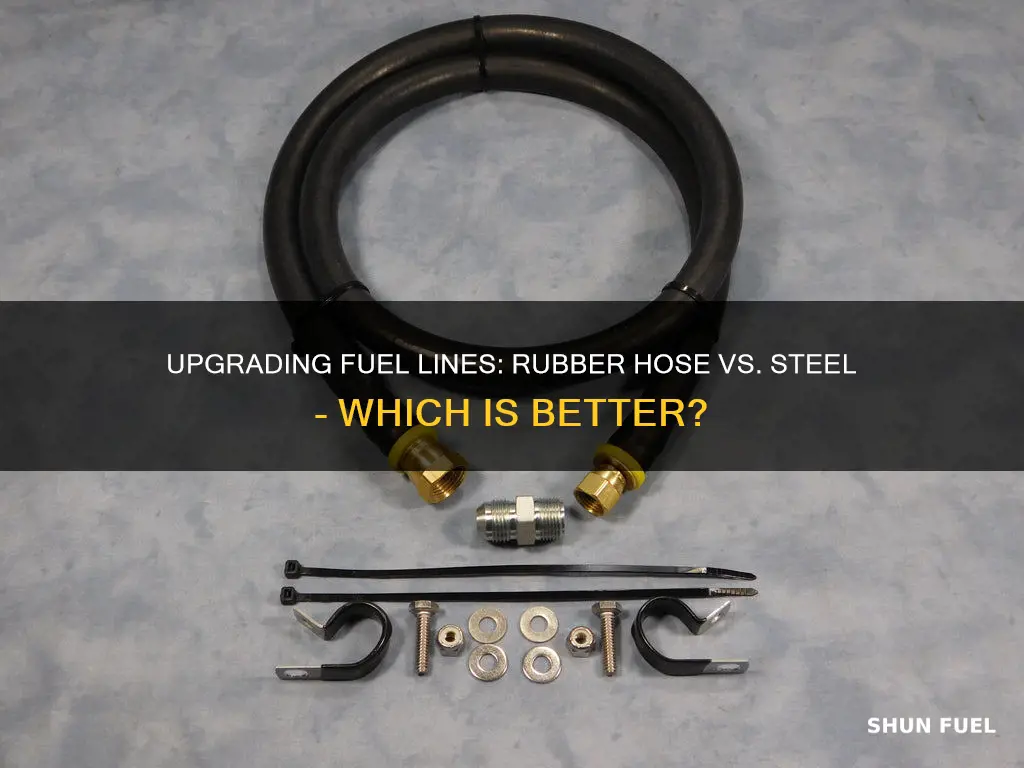
Replacing steel fuel lines with rubber hoses is a common modification for vehicle owners, but it's important to understand the implications and potential risks. While rubber hoses are more flexible and easier to install, they may not be as durable or reliable as steel fuel lines, which are designed to withstand high pressure and temperature changes. This introduction sets the stage for a discussion on the pros and cons of making this replacement, highlighting the need for careful consideration and potentially expert advice.
Characteristics | Values |
---|---|
Durability | Rubber hoses are generally less durable than steel fuel lines and may not withstand the same level of pressure and temperature changes. |
Flexibility | Rubber hoses offer more flexibility, making installation easier and allowing for more route options. |
Corrosion Resistance | Steel fuel lines are more resistant to corrosion and can handle harsher environments. Rubber hoses may degrade over time due to fuel exposure. |
Cost | Steel fuel lines are typically more expensive than rubber hoses. |
Maintenance | Rubber hoses may require more frequent replacement due to wear and tear, while steel lines can last longer. |
Compatibility | Ensure the rubber hose is compatible with the fuel type and temperature range of your vehicle. |
Installation | Installation of rubber hoses is generally simpler, but proper crimping or clamping is crucial for a secure connection. |
Weight | Steel fuel lines are heavier, which might be a consideration for some vehicles. |
Longevity | Steel fuel lines often have a longer lifespan, especially in high-performance or extreme conditions. |
Availability | Both materials are widely available, but the specific sizes and types may vary. |
What You'll Learn
- Safety: Rubber hoses may lack the structural integrity of steel fuel lines, potentially leading to fuel leaks and safety hazards
- Durability: Rubber hoses can be more flexible but may degrade faster under heat, pressure, and UV exposure
- Compatibility: Ensure the rubber hose is compatible with the fuel type and system to avoid material incompatibility issues
- Cost: Rubber hoses are generally cheaper, but the long-term cost of maintenance and replacement may be higher
- Installation: Replacing steel lines with rubber hoses requires careful installation to ensure a secure and leak-free connection
Safety: Rubber hoses may lack the structural integrity of steel fuel lines, potentially leading to fuel leaks and safety hazards
When considering replacing a steel fuel line with a rubber hose, it's crucial to prioritize safety and understand the potential risks associated with this modification. Rubber hoses, while flexible and lightweight, may not possess the same structural integrity as steel fuel lines, which are designed to withstand high pressure and extreme temperatures. This difference in material properties can lead to several safety concerns.
One of the primary risks is the potential for fuel leaks. Steel fuel lines are engineered to maintain a tight seal and prevent fuel from escaping. They are typically made of sturdy materials that can resist the corrosive effects of fuel over time. In contrast, rubber hoses may degrade or become brittle, especially when exposed to fuel's harsh chemicals. This degradation can result in cracks or punctures, allowing fuel to leak, which poses a fire hazard and can also damage the surrounding components.
The flexibility of rubber hoses might be an advantage in some cases, but it can also be a disadvantage when it comes to safety. Rubber hoses may not be as rigid as steel lines, making them more susceptible to damage from vibrations, impacts, or temperature fluctuations. Over time, the hose could develop permanent bends or kinks, leading to restricted fuel flow or, in severe cases, a complete blockage. Such issues can cause engine misfires, reduced performance, or even engine stall, creating dangerous situations while driving.
Additionally, the installation process is critical to ensuring safety. If the rubber hose is not properly secured and tightened, it may not provide the necessary support and protection against mechanical stress. This can lead to premature failure, potentially causing fuel to spill onto hot engine components, increasing the risk of fire or engine damage.
In summary, while replacing a steel fuel line with a rubber hose might seem like a simple modification, it is essential to consider the potential safety implications. The structural differences between the two materials can lead to fuel leaks, reduced performance, and increased fire hazards. To ensure the highest level of safety, it is recommended to consult with automotive experts or professionals who can provide guidance on the most suitable materials and installation practices for your specific vehicle.
Solar Panels: Fossil Fuel's Replacement Hurdles Explained
You may want to see also
Durability: Rubber hoses can be more flexible but may degrade faster under heat, pressure, and UV exposure
When considering the replacement of a steel fuel line with a rubber hose, it's crucial to understand the potential trade-offs, particularly regarding durability. Rubber hoses offer several advantages, such as increased flexibility, which can be beneficial in certain applications. However, their durability is a critical factor that requires careful consideration.
One of the primary concerns with rubber hoses is their sensitivity to environmental factors. Rubber is known to degrade more rapidly when exposed to heat, pressure, and ultraviolet (UV) radiation. In the context of a fuel line, these factors can significantly impact the hose's performance and longevity. High temperatures, for instance, can cause the rubber to become brittle and crack over time, leading to potential fuel leaks and system failures. Similarly, pressure fluctuations can stress the hose, potentially causing it to fail prematurely.
UV exposure is another critical factor, especially in outdoor environments. Rubber hoses can deteriorate when exposed to direct sunlight, becoming discolored and losing their structural integrity. This degradation can result in reduced flexibility and, ultimately, a higher risk of hose failure. In contrast, steel fuel lines are generally more resistant to these environmental stressors, making them a more reliable long-term solution.
To ensure the durability of a rubber hose replacement, it is essential to choose a high-quality product specifically designed for the fuel line application. Some manufacturers offer rubber hoses with additives that enhance their heat and UV resistance, providing a more robust solution. Additionally, regular inspections and maintenance can help identify and address any issues early on, ensuring the system's overall reliability.
In summary, while rubber hoses offer flexibility advantages, their durability may be compromised under certain conditions. It is essential to weigh the benefits against the potential risks and consider the specific environmental factors present in the application. Proper selection and maintenance can help mitigate these concerns, ensuring a safe and reliable fuel system.
Replacing Fuel Filter in Craftsman Weedwacker: Step-by-Step Guide
You may want to see also
Compatibility: Ensure the rubber hose is compatible with the fuel type and system to avoid material incompatibility issues
When considering replacing a steel fuel line with a rubber hose, compatibility is a critical factor to ensure the safety and efficiency of your fuel system. Rubber hoses are generally more flexible and easier to install compared to steel lines, but their suitability depends on several factors related to the fuel type and system in question.
The first step is to identify the type of fuel you are dealing with. Different fuels have varying chemical compositions and properties, which can affect the choice of materials. For instance, gasoline and diesel have different octane levels and contain different additives, which can impact the choice of rubber compounds. Some rubbers are more resistant to gasoline's volatile nature, while others are better suited for the lubricating properties of diesel. It is essential to select a rubber hose that is specifically designed for the fuel type you are using to prevent degradation, leaks, or other performance issues.
Additionally, the fuel system's design and pressure requirements must be considered. Rubber hoses typically have a lower pressure rating compared to steel lines, so it's crucial to ensure that the hose can withstand the pressure and temperature fluctuations within your fuel system. Check the manufacturer's specifications for both the rubber hose and the existing fuel line to determine if the hose can handle the system's operating conditions. This includes considering the flow rate, temperature extremes, and any potential contaminants in the fuel that could affect the hose's performance.
Furthermore, the compatibility of the rubber hose with the fuel system's components is vital. Rubber hoses may not be suitable for all fuel system parts, especially those made from specific materials. For example, some fuel tanks or fuel injectors might have rubber gaskets or seals that could be affected by the new hose material. It is essential to ensure that the hose does not interfere with or damage these components and that it can be securely attached without causing any leaks.
In summary, when replacing a steel fuel line with a rubber hose, compatibility is key. Selecting the right rubber hose that is compatible with the fuel type, system pressure, and existing components will ensure a safe and efficient fuel delivery system. Always refer to manufacturer guidelines and consult experts if needed to make an informed decision and avoid potential issues related to material incompatibility.
Nuclear Energy: The Sustainable Fossil Fuel Alternative?
You may want to see also
Cost: Rubber hoses are generally cheaper, but the long-term cost of maintenance and replacement may be higher
When considering the cost implications of replacing a steel fuel line with a rubber hose, it's important to look at both the initial expense and the long-term financial impact. Rubber hoses are often more affordable upfront, which can be a significant factor for those seeking a cost-effective solution. This initial cost advantage is primarily due to the lower material and manufacturing expenses associated with rubber compared to steel. As a result, replacing a fuel line with a rubber hose might seem like a budget-friendly option.
However, the long-term cost of maintenance and replacement should not be overlooked. Rubber hoses have a tendency to degrade over time, especially when exposed to fuel, which can lead to cracking, softening, or even failure. This degradation may result in frequent replacements, as rubber hoses typically have a shorter lifespan than steel lines. The recurring need for replacements can quickly negate the initial savings, making it a less economical choice in the long run.
Furthermore, the maintenance requirements for rubber hoses can be more frequent and labor-intensive. Regular inspections and potential repairs or replacements may be necessary to ensure the system's reliability and safety. These additional maintenance costs can accumulate over time, further impacting the overall financial burden.
In contrast, steel fuel lines are known for their durability and longevity. While they may have a higher initial cost, their resistance to fuel degradation and longer lifespan can result in reduced maintenance and replacement expenses over time. This makes steel lines a more cost-effective option in the long term, despite the higher upfront investment.
In summary, while rubber hoses offer a lower initial cost, the long-term financial implications, including maintenance and replacement expenses, can be higher. It is essential to consider these factors when making a decision, ensuring that the chosen solution provides both short-term savings and long-term reliability.
Replacing Fuel Injector Parts: A Step-by-Step Guide for Beginners
You may want to see also
Installation: Replacing steel lines with rubber hoses requires careful installation to ensure a secure and leak-free connection
Replacing steel fuel lines with rubber hoses is a common modification for vehicle owners seeking a more flexible and potentially cost-effective solution. However, the installation process demands precision and attention to detail to ensure a safe and efficient outcome. Here's a step-by-step guide to help you navigate this task:
Preparation: Before you begin, ensure you have the necessary tools and materials, including the new rubber hoses, fittings, and any required adhesives or sealants. Clean the existing steel lines to remove any dirt or debris, ensuring a smooth surface for the new hose to fit snugly. It is crucial to inspect the steel lines for any signs of damage or corrosion that might affect the installation.
Cutting and Fitting: Measure and mark the steel lines where you plan to cut, ensuring the length is appropriate for the new hose. Use a sharp, clean blade to carefully cut the steel, maintaining a straight edge. Now, it's time to attach the fittings. Slide the fittings onto the ends of the rubber hoses, ensuring they are secure and aligned properly. Use a fitting tool if available to ensure a tight connection. For the steel line ends, you might need to use a file or sandpaper to create a slightly larger diameter to accommodate the hose, then attach the fittings.
Connection and Sealing: When connecting the rubber hose to the steel line, apply a bead of adhesive or sealant to the inside of the steel line and the outside of the hose, following the manufacturer's instructions. Slide the hose onto the steel line, ensuring it is centered and secure. Use a crimping tool if provided with the fittings to create a tight, leak-free seal. Repeat this process for all connections, ensuring each joint is secure and well-sealed.
Testing and Final Touches: After all the connections are made, start the vehicle's engine and check for any leaks. If no leaks are found, you can proceed with further testing. Ensure all connections are tight and secure, and consider using a fuel pressure gauge to verify the system's integrity. If any leaks occur, carefully inspect the connections and re-tighten or re-seal as necessary.
Remember, the key to a successful installation is patience and attention to detail. Take your time during the installation process, and don't rush any steps. This careful approach will ensure a reliable and safe fuel system, providing peace of mind for your vehicle's performance.
Replacing the Fuel Pump in a 2001 Chevy Impala
You may want to see also
Frequently asked questions
Yes, it is possible to replace a steel fuel line with a rubber hose, but it's important to consider the potential drawbacks. Rubber hoses are more flexible and less rigid than steel, which can be beneficial for certain applications, especially in areas with limited space or where the fuel line needs to bend around obstacles. However, rubber hoses may not be as durable or long-lasting as steel, and they can be more susceptible to damage from heat, chemicals, and UV radiation.
Rubber hoses offer several advantages. They are typically lighter, easier to install, and can provide a more flexible connection, especially in high-vibration environments. Rubber is also a good insulator, which can help prevent fuel leaks and reduce the risk of electrical issues. Additionally, rubber hoses are often more cost-effective and have a longer lifespan when properly maintained.
Yes, there are specialized rubber hoses designed for fuel lines, often made from compounds like natural rubber, synthetic rubber, or a blend of both. These hoses are formulated to withstand the corrosive properties of fuel, including gasoline, diesel, and ethanol blends. Look for hoses that are reinforced with braided steel or polyester to ensure they can handle the pressure and temperature variations associated with fuel systems.
Achieving a secure seal is crucial to prevent fuel leaks. Start by cleaning the fuel line and the hose ends to remove any dirt or debris. Use a suitable fuel line sealant or tape to ensure a tight bond between the hose and the fuel line. Ensure that the hose is properly routed and secured to prevent excessive movement or stress on the connection. Regularly inspect the hose for any signs of wear or damage, especially at the connection points.
While rubber hoses are generally not suitable for high-pressure fuel systems, there are specialized hoses designed for such applications. These hoses often feature additional layers of reinforcement and are made from materials that can withstand higher pressures. It's essential to consult the vehicle's manual or seek professional advice to determine the appropriate hose specifications for your specific fuel system and engine requirements.