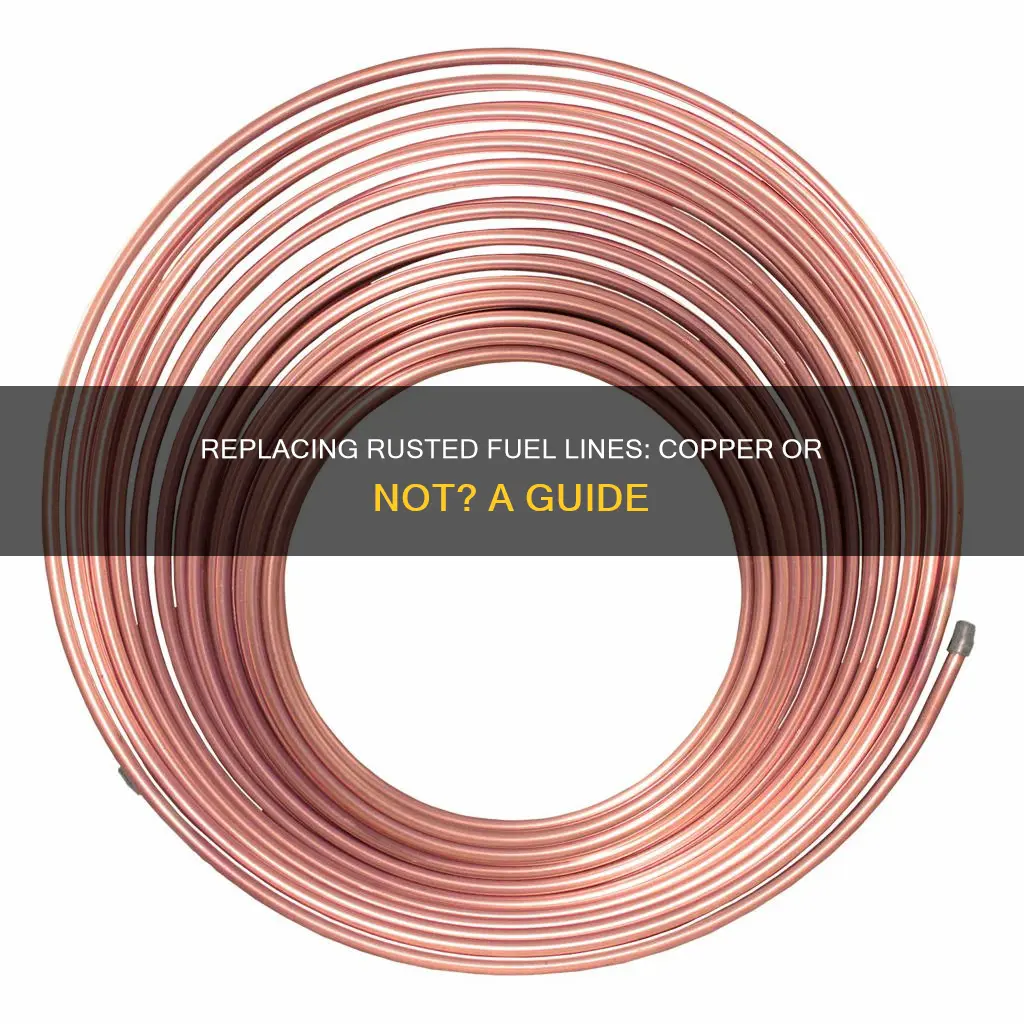
Replacing a rusted fuel line is a common car repair, but choosing the right material is crucial. While copper is a popular choice for its durability and corrosion resistance, it's important to consider the potential risks. Copper can react with certain fuels, leading to the release of copper compounds, which may be harmful if ingested or inhaled. Additionally, copper can be more expensive and harder to work with than traditional materials like steel or stainless steel. This introduction sets the stage for a discussion on the pros and cons of using copper for fuel line replacement.
Characteristics | Values |
---|---|
Compatibility | Copper is not compatible with gasoline or diesel fuel as it can cause corrosion and degradation of the fuel over time. |
Durability | Copper is more durable than steel and can withstand higher temperatures, making it a better choice for fuel lines in high-temperature environments. |
Corrosion Resistance | Copper is highly resistant to corrosion, especially in the presence of fuel, which makes it a suitable replacement for rusted fuel lines. |
Flexibility | Copper is more flexible than steel, allowing for easier installation and routing of fuel lines. |
Cost | Copper fuel lines can be more expensive than steel alternatives, but the increased durability and resistance to corrosion may justify the higher cost. |
Maintenance | Copper fuel lines may require more frequent maintenance due to their higher cost and potential for corrosion. |
Availability | Copper fuel lines may be less readily available compared to steel, and specialized suppliers may be required. |
Installation | Proper installation techniques are crucial when replacing rusted fuel lines with copper to ensure a secure and leak-free connection. |
What You'll Learn
- Material Compatibility: Copper and fuel lines must be compatible to prevent corrosion and leaks
- Pressure Rating: Copper lines must meet or exceed fuel line pressure requirements
- Flexibility: Copper's flexibility ensures it can withstand engine vibrations and movement
- Temperature Tolerance: Copper can handle fuel temperature fluctuations without degradation
- Installation Techniques: Proper crimping, soldering, and sealing methods are crucial for a successful replacement
Material Compatibility: Copper and fuel lines must be compatible to prevent corrosion and leaks
When considering replacing a rusted fuel line, it is crucial to understand the compatibility of materials to ensure the system's longevity and safety. Copper, a popular choice for its malleability and corrosion resistance, is often a go-to material for such replacements. However, its compatibility with fuel lines is a critical factor to consider.
The primary concern with using copper for fuel lines is the potential for corrosion, especially in the presence of certain fuels. Copper, while durable, can react with some fuels, leading to the formation of copper salts, which can cause corrosion and, in severe cases, leaks. This is particularly relevant for fuels containing sulfur, as sulfur compounds can accelerate the corrosion process. Therefore, it is essential to choose the right type of copper and ensure it is compatible with the specific fuel being used.
For instance, brass, a copper alloy, is often preferred for fuel lines due to its improved corrosion resistance. It contains a higher zinc content, which forms a protective layer on the surface, preventing copper from coming into direct contact with the fuel. This makes brass a safer and more reliable option for fuel lines, especially in high-corrosion environments.
Additionally, the manufacturing process and the specific grade of copper used can also impact compatibility. Some copper alloys are designed to be more resistant to corrosion, making them ideal for fuel line applications. It is recommended to consult with material experts or refer to manufacturer guidelines to select the most suitable copper-based material for the task.
In summary, while copper can be an effective material for replacing rusted fuel lines, its compatibility with the fuel type is paramount. Proper selection and consideration of the fuel's properties will ensure a successful and safe replacement, preventing potential corrosion and leaks. Always prioritize material compatibility to maintain the integrity of the fuel system.
Replacing Fuel Pump in 2008 Ford F150: Step-by-Step Guide
You may want to see also
Pressure Rating: Copper lines must meet or exceed fuel line pressure requirements
When considering replacing a rusted fuel line with copper, it's crucial to prioritize safety and performance. One of the most critical factors to consider is the pressure rating of the copper fuel line. Copper lines used for fuel systems must meet or exceed the pressure requirements of the original fuel line to ensure optimal performance and prevent potential issues.
Fuel lines operate under varying pressure conditions, and the pressure can vary depending on the vehicle's engine specifications and operating conditions. It is essential to consult the vehicle's manual or manufacturer's guidelines to determine the specific pressure rating required for the fuel line. This information will help you select a copper fuel line with the appropriate pressure rating.
Copper fuel lines are known for their durability and flexibility, making them a suitable replacement for rusted lines. However, the pressure rating is a critical aspect that cannot be overlooked. Copper lines should be chosen based on their ability to withstand the maximum pressure the fuel system can exert. If the copper line's pressure rating is lower than the required specifications, it may not provide the necessary protection against fuel system failures or leaks.
To ensure a proper fit and reliable performance, it is recommended to use copper fuel lines that are specifically designed for automotive applications. These lines are engineered to meet or exceed industry standards and vehicle manufacturer requirements. By selecting a copper line with an appropriate pressure rating, you can ensure that the fuel system operates safely and efficiently.
In summary, when replacing a rusted fuel line with copper, always consider the pressure rating as a top priority. Copper fuel lines should be chosen based on their ability to meet or exceed the pressure requirements of the original line. This ensures the longevity and reliability of the fuel system, providing peace of mind for vehicle owners.
Replacing the Fuel Door: A Step-by-Step Guide for 2008 Colorado Owners
You may want to see also
Flexibility: Copper's flexibility ensures it can withstand engine vibrations and movement
The flexibility of copper is a crucial factor to consider when replacing a rusted fuel line. Copper's inherent pliability allows it to adapt to the various movements and vibrations experienced within an engine's environment. This is particularly important in the case of fuel lines, as they are subject to constant flexing and expansion due to engine operation.
When a fuel line is installed, it needs to be able to move with the engine block without kinking or breaking. Copper's flexibility ensures that the line can accommodate these movements, reducing the risk of damage or leaks. This is especially critical in high-performance engines or those with aggressive driving conditions, where vibrations and stress on the fuel system can be more intense.
The ability of copper to bend and twist without permanent deformation is a direct result of its unique crystal structure. Copper's atoms are arranged in a way that allows for easy sliding and rearrangement, providing the material with exceptional flexibility. This characteristic is essential for fuel lines, as it enables the line to navigate through engine compartments, around various components, and along the frame without compromising its integrity.
Furthermore, the flexibility of copper contributes to the overall longevity of the fuel system. By allowing the line to move freely, copper reduces the likelihood of stress-induced failures, such as cracks or punctures. This is particularly important in older vehicles or those with modified engines, where the fuel system may be more susceptible to vibrations and movement.
In summary, the flexibility of copper is a key advantage when replacing a rusted fuel line. Its ability to withstand engine vibrations and movement ensures a secure and reliable installation, minimizing the risk of damage and providing long-term durability. This property makes copper an ideal choice for fuel lines, offering both performance and protection in demanding automotive applications.
Replacing the Fuel Pump in Your Lexus IS300: Step-by-Step Guide
You may want to see also
Temperature Tolerance: Copper can handle fuel temperature fluctuations without degradation
When considering replacing a rusted fuel line, one of the critical factors to evaluate is the material's ability to withstand temperature variations, especially in the context of fuel systems. Copper, a metal known for its excellent thermal conductivity, offers a unique advantage in this regard. Unlike some other materials, copper can handle fuel temperature fluctuations without significant degradation, making it a reliable choice for fuel line replacements.
The temperature tolerance of copper is a result of its inherent material properties. Copper has a high thermal conductivity, which means it can efficiently transfer heat. In the context of a fuel line, this property ensures that the copper material can quickly dissipate heat generated by the fuel, preventing the fuel from overheating and maintaining its stability. This is particularly important in fuel systems where temperatures can vary widely, especially during engine operation.
Furthermore, copper's ability to withstand temperature changes is not limited to just heat dissipation. It also possesses excellent resistance to thermal expansion and contraction. This characteristic is crucial for fuel lines as it allows the copper to maintain its structural integrity even when exposed to rapid temperature fluctuations. Unlike materials that may crack or weaken under such conditions, copper can adapt to these changes without compromising its performance.
In the case of a rusted fuel line, replacing it with copper can provide long-term benefits. Rusted fuel lines often lead to fuel leaks and contamination, which can cause engine performance issues. Copper, being a durable material, ensures that the new fuel line can withstand the rigors of the fuel system, including temperature variations, without corroding or deteriorating over time. This makes it an ideal replacement option for maintaining a reliable and efficient fuel system.
In summary, copper's temperature tolerance is a significant advantage when considering its use for replacing rusted fuel lines. Its ability to handle fuel temperature fluctuations without degradation ensures the longevity and reliability of the fuel system. By choosing copper, you are selecting a material that can provide a robust and efficient solution for your fuel line replacement needs.
Fuel Pump Relay: When to Replace for Optimal Performance
You may want to see also
Installation Techniques: Proper crimping, soldering, and sealing methods are crucial for a successful replacement
When replacing a rusted fuel line with copper, proper installation techniques are essential to ensure a secure and leak-free connection. Here's a detailed guide on the key methods:
Crimping: This method involves using a specialized tool to create a mechanical connection between the copper line and a fitting. It's a reliable way to join copper tubing, especially for fuel lines. Start by ensuring the copper line and fitting are clean and free of any debris. Apply a thin layer of thread seal tape around the fitting's threads, then carefully insert the line into the fitting. Use the crimping tool to apply pressure and create a secure connection. The tool will compress the fitting onto the line, forming a tight bond. Make sure to follow the manufacturer's instructions for the specific tool and pressure required. Proper crimping ensures a strong, leak-resistant joint.
Soldering: Soldering is another effective technique for joining copper. It creates a strong, permanent bond between the copper line and fitting. Begin by cleaning the surfaces to be soldered, removing any oxidation. Use a flux to prevent oxidation during the soldering process. Heat the joint until the copper begins to turn a light brown color, indicating it's at the correct temperature for soldering. Apply the solder, ensuring it's free of any air bubbles. Use a soldering iron to melt the solder, allowing it to flow into the joint. Hold the iron for a few seconds to ensure a strong bond. After cooling, wipe away any excess solder with a damp cloth. This method provides a durable and long-lasting connection.
Sealing: Proper sealing is critical to prevent fuel leaks. After joining the copper line and fitting, use a high-quality sealant designed for fuel lines. Apply the sealant to the threads of the fitting and the surrounding area. Insert the line into the fitting, ensuring it's properly aligned. Tighten the fitting securely, but be careful not to overtighten, as this can damage the threads. The sealant will create a barrier that prevents fuel from leaking out and protects against future corrosion.
Remember, each step should be executed with precision and care. Take your time to ensure a flawless installation, as improper techniques can lead to leaks and potential safety hazards. Following these installation techniques will result in a successful replacement, providing a reliable and long-lasting solution for your fuel line.
Replacing Husqvarna 266 Chainsaw Fuel Tank Vent: Step-by-Step Guide
You may want to see also
Frequently asked questions
Yes, it is feasible to replace a rusted fuel line with copper, but it requires careful consideration and preparation. Copper is a good choice for fuel lines due to its durability and resistance to corrosion. However, it's important to ensure that the copper is properly prepared and installed to avoid any potential issues.
Copper offers several benefits for fuel lines. It is highly resistant to corrosion, which helps prevent rust and ensures the longevity of the fuel system. Copper is also known for its excellent thermal conductivity, allowing for efficient heat dissipation, and it has a relatively low coefficient of thermal expansion, making it less prone to cracking.
When replacing a rusted fuel line with copper, it's crucial to follow these steps: First, ensure the copper is properly cleaned and free of any oxide layer. Then, use a suitable primer or adhesive to secure the copper to the existing fuel line, providing a strong bond. Additionally, consider using a copper-specific fuel line connector to ensure a proper seal. Regular maintenance and inspections are also recommended to identify and address any potential issues early on.