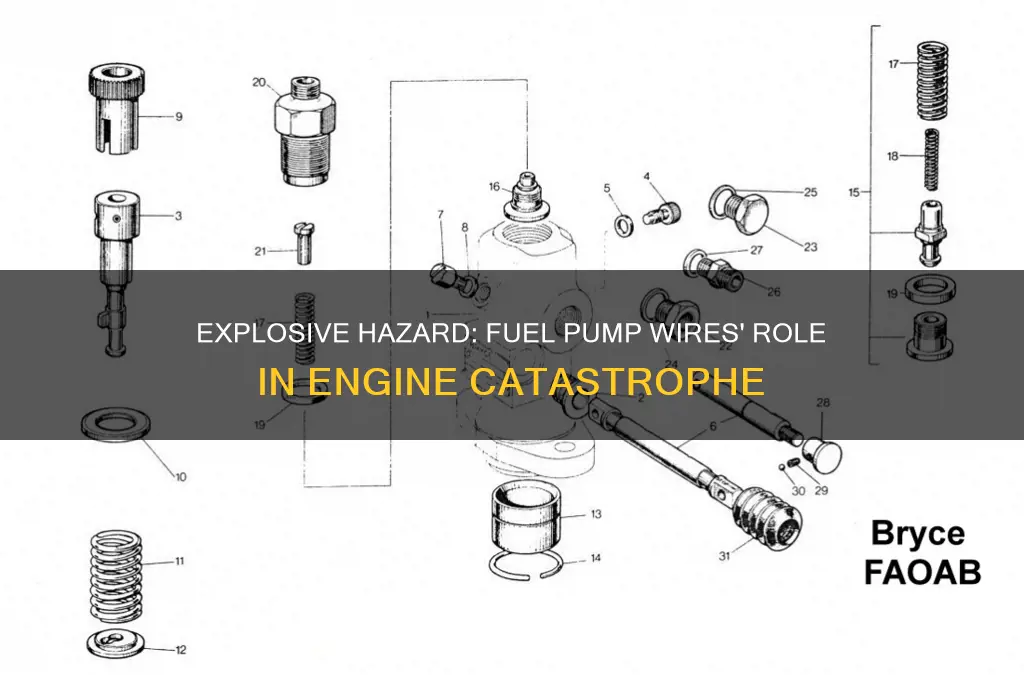
A replaced fuel pump with frayed wires can pose a significant safety hazard and potentially lead to an explosion. When a fuel pump is damaged or malfunctions, it may not be able to handle the pressure and flow rate of the fuel, leading to a buildup of pressure and potential overheating. Additionally, frayed wires can cause electrical shorts, which can lead to sparks and ignite the fuel vapor in the engine compartment. This scenario highlights the importance of proper installation and maintenance of fuel pump systems to prevent such dangerous situations.
Characteristics | Values |
---|---|
Potential Cause | Yes, a replaced fuel pump with damaged or frayed wires can potentially cause an explosion. |
Risk Factors | - Faulty wiring connections - Short circuits - Spark from damaged wires - Accumulation of flammable fuel vapor |
Prevention | - Ensure proper wiring installation and maintenance - Regularly inspect fuel pump wiring for damage - Use high-quality wires and connectors - Keep the fuel tank and pump area well-ventilated |
Symptoms | - Engine misfires - Reduced power or performance - Strange noises from the fuel system - Smell of burning plastic or fuel |
Safety Measures | - Consult a professional mechanic for diagnosis and repair - Avoid starting the engine if there's a suspected issue - Ensure proper ventilation during repairs |
What You'll Learn
- Fuel Pump Design: Different designs may have varying susceptibility to wire damage
- Wire Quality: Low-quality wires can crack or melt under pressure
- Fuel Type: Some fuels may corrode or damage wires more easily
- Environmental Factors: Extreme temperatures or moisture can accelerate wire degradation
- Maintenance: Regular inspections can prevent wire damage and potential explosions
Fuel Pump Design: Different designs may have varying susceptibility to wire damage
The design of a fuel pump plays a crucial role in determining its resistance to potential issues arising from damaged wires. Different fuel pump designs incorporate unique features and components that can either mitigate or exacerbate the impact of wire damage. For instance, some pumps utilize a robust wiring harness with multiple protective layers, ensuring that even if a few wires are compromised, the overall system remains functional. This design philosophy prioritizes reliability and safety, making it less susceptible to catastrophic failures due to wire damage.
In contrast, other fuel pump designs may lack such comprehensive wire protection. Older or more basic pump models might have a simpler wiring configuration, making them more vulnerable to wire damage. If a single wire is damaged, it could potentially disrupt the entire fuel supply, leading to engine stalls or even posing a safety hazard during operation. Therefore, understanding the specific design characteristics of a fuel pump is essential for predicting its behavior in the event of wire damage.
One critical aspect of fuel pump design is the material and construction of the wires themselves. High-quality wires with improved insulation and shielding can better withstand the harsh environment within the fuel tank, reducing the likelihood of damage from corrosion, heat, or mechanical stress. Pumps equipped with such wires are less likely to experience wire breakage or short circuits, which could lead to dangerous situations.
Additionally, the layout and routing of wires within the fuel pump assembly are vital considerations. Some designs employ a more intricate wiring pattern, ensuring that wires are protected by surrounding components and less likely to come into contact with sharp edges or hot surfaces. This thoughtful wiring arrangement can significantly reduce the risk of wire damage and subsequent failures.
Engineers and designers must carefully evaluate these factors when creating fuel pump systems to ensure optimal performance and safety. By considering the unique characteristics of different pump designs, they can develop solutions that minimize the chances of wire damage and its potential consequences. This attention to detail is essential in the automotive industry, where the reliability and safety of fuel systems are of utmost importance.
Replacing a Chainsaw Fuel Line: A Step-by-Step Guide
You may want to see also
Wire Quality: Low-quality wires can crack or melt under pressure
Low-quality wires, often overlooked, can be a significant source of concern when it comes to vehicle safety, especially in the context of a replaced fuel pump. The integrity of the wiring harness is crucial, as it ensures the safe and efficient operation of various vehicle systems, including the fuel pump. When a fuel pump is installed, the wiring harness plays a critical role in delivering the necessary power and signals to the pump.
The primary issue with low-quality wires is their susceptibility to cracking and melting under pressure. Over time, wires can degrade due to various factors such as exposure to heat, chemicals, and mechanical stress. When a fuel pump is replaced, the existing wiring may not meet the required standards, leading to potential hazards. If the wires are brittle or have a poor insulation material, they can crack or melt when subjected to the high pressure and heat generated by the fuel pump's operation. This can result in a short circuit, which may cause the pump to malfunction or even fail, potentially leading to a dangerous situation.
The consequences of using low-quality wires can be severe. A cracked or melted wire can lead to a loss of power to the fuel pump, causing it to stop functioning. This can result in reduced engine performance, stalling, or even a complete breakdown of the vehicle. In extreme cases, a short circuit can trigger a fire hazard, especially if the wires are located in close proximity to flammable materials. It is essential to ensure that the wiring harness used for the fuel pump replacement meets the manufacturer's specifications and is of high quality to prevent such risks.
To mitigate these risks, it is recommended to use high-quality wires with robust insulation and a suitable thickness to withstand the demands of the fuel pump. Regular inspections of the wiring harness should also be conducted to identify any signs of wear and tear, especially in areas prone to heat and mechanical stress. By prioritizing wire quality, vehicle owners can ensure the safety and reliability of their fuel pump systems, reducing the chances of explosions or other hazardous incidents.
In summary, the quality of wires is a critical aspect of vehicle maintenance, particularly when dealing with fuel pump replacements. Low-quality wires can crack or melt under pressure, leading to potential explosions or other dangerous situations. By choosing high-quality materials and conducting regular inspections, vehicle owners can minimize the risks associated with wiring harnesses and ensure the safe operation of their vehicles.
The Future of Energy: Solar, Wind, and Fossil Fuels
You may want to see also
Fuel Type: Some fuels may corrode or damage wires more easily
When it comes to fuel systems, the type of fuel used can significantly impact the longevity and performance of the wiring and components, especially when dealing with a replaced fuel pump. Some fuels are more corrosive and can cause damage to wires and electrical connections more easily than others. This is an important consideration for vehicle owners and mechanics alike, as it can lead to potential safety hazards and performance issues.
For instance, ethanol-blended fuels, which are becoming increasingly common, can be particularly corrosive to certain types of wiring materials. Ethanol has a higher water content and can attract moisture, leading to increased electrical resistance and potential short circuits. Over time, this can result in wire degradation, corrosion, and even complete wire failure. This is especially critical in fuel pump wiring, as a failure could lead to fuel starvation, causing the engine to stall or even fail to start.
On the other hand, some fuels, like pure gasoline, may not be as corrosive but can still cause issues. Gasoline can contain additives and impurities that can lead to wire degradation over time. These additives can cause the insulation on wires to break down, exposing the conductive core and leading to electrical shorts or open circuits. This can result in erratic engine behavior, such as stalling or difficulty starting, and may even cause damage to the fuel pump itself.
To mitigate these issues, it is essential to use the correct type of fuel recommended by the vehicle manufacturer. Additionally, regular maintenance and inspections of the fuel system, including the wiring, are crucial. This includes checking for any signs of corrosion, frayed or exposed wires, and ensuring that all connections are secure and free from damage.
In summary, the type of fuel used in a vehicle can significantly impact the performance and safety of the fuel system, particularly when a fuel pump has been replaced. Ethanol-blended fuels and certain gasoline blends can be corrosive and cause wire damage, while all fuels can lead to insulation breakdown. Vehicle owners and mechanics should be aware of these potential issues and take appropriate measures to ensure the fuel system's reliability and safety.
Replacing Fuel Injectors in 2005 Expeditions: Step-by-Step Guide
You may want to see also
Environmental Factors: Extreme temperatures or moisture can accelerate wire degradation
Extreme environmental conditions can significantly impact the performance and longevity of electrical wires, including those used in fuel pump systems. When it comes to the potential explosion of a fuel pump with damaged wires, understanding the role of environmental factors is crucial.
In regions with extreme temperatures, whether hot or cold, the wires connecting the fuel pump can be particularly vulnerable. High temperatures can cause the insulation around the wires to degrade, leading to exposure of the conductive core. This exposure increases the risk of short circuits, as the wires may come into contact with other components or nearby metal surfaces. Over time, this can result in sparks, which, in the presence of fuel vapor, could ignite and potentially cause an explosion. Similarly, in cold environments, the wires may become brittle, and the insulation can crack, again leading to potential short circuits and the risk of fire or explosion.
Moisture is another critical environmental factor. Water intrusion into the fuel pump system can be detrimental. When wires are exposed to moisture, especially in humid conditions, the water can seep into the insulation, causing it to swell and weaken. This process, known as hydrolysis, can lead to the breakdown of the wire's insulation, leaving the conductive material exposed. As a result, the wires may become susceptible to corrosion, which can further accelerate the degradation process. Corroded wires are more likely to cause electrical issues, including sparks and potential ignition of fuel vapor, posing a serious safety hazard.
To mitigate these risks, it is essential to ensure that fuel pump systems are designed and installed with appropriate environmental considerations. This includes using wires with robust insulation that can withstand the expected temperature and moisture ranges. Additionally, regular maintenance and inspections can help identify and address any issues related to wire degradation, ensuring the safety and reliability of the fuel pump system.
In summary, environmental factors such as extreme temperatures and moisture play a significant role in the degradation of wires, which can lead to potential explosions in fuel pump systems. Understanding and addressing these factors are vital in maintaining the safety and performance of such systems.
Replacing Fuel Pump in Chevy S10: Step-by-Step Guide
You may want to see also
Maintenance: Regular inspections can prevent wire damage and potential explosions
Regular maintenance and inspections are crucial when it comes to preventing potential hazards associated with fuel pump wiring. One of the primary concerns is the possibility of wire damage, which can lead to serious consequences, including explosions. Fuel pumps, especially those that have been replaced, can be susceptible to various issues, and the wiring is no exception. Over time, wires can degrade due to factors such as heat, vibration, and exposure to fuel contaminants. This degradation can result in frayed or damaged wires, which may seem like a minor issue at first but can quickly escalate into a major problem.
The potential for explosion arises when damaged wires come into contact with fuel, creating a spark. Fuel is a highly flammable substance, and any spark or ignition source can lead to a dangerous fire or explosion. This is particularly true for fuel pumps, as they are designed to deliver fuel to the engine, and any disruption in the wiring can cause an unexpected surge of fuel, creating a hazardous situation. Therefore, it is essential to identify and address wire damage promptly.
To prevent such incidents, regular inspections are recommended. During these inspections, technicians should carefully examine the fuel pump wiring for any signs of wear and tear, damage, or corrosion. Look for frayed or exposed wires, discolored insulation, or any signs of heat damage. It is also important to check for proper connections and ensure that all wiring is securely attached to the fuel pump and the vehicle's electrical system. Any issues found should be addressed immediately to prevent further deterioration.
In addition to visual inspections, it is beneficial to use specialized tools and techniques to assess wire integrity. Insulation resistance testing and wire continuity checks can help identify damaged or compromised wires. These tests can reveal issues that may not be immediately apparent, ensuring that potential hazards are caught early. Regular maintenance also includes keeping the fuel system clean and free of contaminants, as fuel-borne contaminants can accelerate wire degradation.
By implementing a proactive maintenance routine, including regular inspections and testing, the risk of wire damage and potential explosions can be significantly reduced. This is especially important for vehicles with older fuel pump systems or those that have undergone recent replacements. Taking these preventative measures ensures the safety and reliability of the vehicle's fuel system, providing peace of mind to drivers and reducing the likelihood of costly and dangerous incidents.
Replacing the Fuel Filter in Your 2006 Range Rover Sport
You may want to see also
Frequently asked questions
Yes, a fuel pump with damaged or frayed wires can be a potential fire hazard and may lead to an explosion. When the pump is powered, the electrical current can arc through the air, creating a spark that ignites the volatile fuel vapor in the system. This is especially dangerous if the pump is located near the engine or in an enclosed space.
A failing fuel pump may exhibit several symptoms, including engine stalling or difficulty starting, reduced engine performance, and unusual noises from the fuel system. If you notice any of these issues, it's essential to inspect the pump for any visible damage or wear.
Regular maintenance and inspections can help prevent such incidents. Ensure that all wiring connections are secure and free from corrosion. Keep the fuel tank and lines clean and free from debris. It's also recommended to use high-quality fuel pump modules and wires to minimize the risk of electrical issues.
Temporary fixes should be avoided as they may not ensure a safe operation. It's best to replace the damaged wire or pump entirely to eliminate the risk of a potential explosion. Attempting to repair the wire might lead to further complications and compromise the safety of the vehicle.
Yes, certain fuel types, especially those with higher ethanol content, can be more susceptible to pump-related problems. Ethanol can dissolve the rubber components of the fuel system, leading to potential pump failure and increased fire risks. It is advisable to use fuel stabilizers or consult the vehicle manufacturer's guidelines for fuel recommendations.