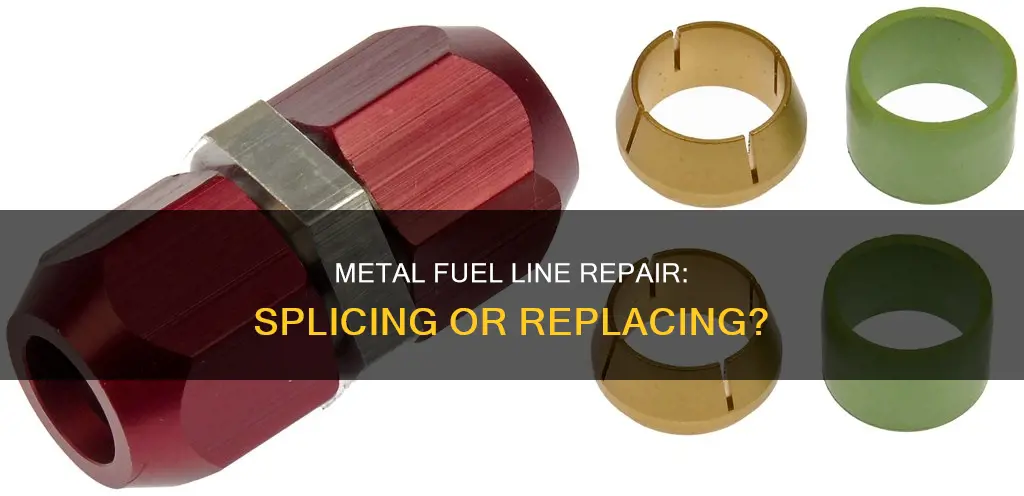
When it comes to repairing or modifying a vehicle's fuel system, one common question that arises is whether a metal fuel line can be spliced. This is a crucial consideration, as the integrity and safety of the fuel supply are paramount. Metal fuel lines are designed to withstand high pressure and temperatures, but splicing them requires careful attention to ensure a secure and reliable connection. In this discussion, we will explore the feasibility and best practices for splicing metal fuel lines, considering factors such as materials, techniques, and potential risks.
Characteristics | Values |
---|---|
Material Compatibility | Metal fuel lines are typically made of materials like steel, aluminum, or copper. When splicing, ensure the new section is compatible with the existing material to avoid corrosion or degradation. |
Temperature Resistance | Metal fuel lines should be able to withstand the temperatures of the fuel they carry. Splicing should not compromise this resistance. |
Pressure Handling | The spliced joint must be able to handle the pressure of the fuel system. This is crucial to prevent leaks and ensure safety. |
Flexibility | While metal is generally rigid, the splice should allow for some flexibility to accommodate movement in the vehicle. |
Corrosion Resistance | Depending on the environment, the splice should be resistant to corrosion to ensure long-term reliability. |
Cost | Splicing might be more expensive than replacing a section, but it can be a viable option in certain situations. |
Skill and Tools | Splicing requires specialized skills and tools to ensure a secure and reliable connection. |
Safety Regulations | Adhere to local and vehicle-specific safety regulations regarding fuel system modifications. |
Warranty and Guarantees | Check the manufacturer's warranty and guarantees for the original fuel lines and any potential splicing work. |
What You'll Learn
- Metal Fuel Line Materials: Common metals for fuel lines and their properties
- Splicing Techniques: Methods for joining metal fuel lines, including welding and crimping
- Safety Precautions: Steps to ensure safe splicing, like cleaning and testing
- Legal Regulations: Industry standards and laws regarding fuel line splicing
- Maintenance Tips: Best practices for maintaining spliced metal fuel lines
Metal Fuel Line Materials: Common metals for fuel lines and their properties
When it comes to metal fuel lines, several common metals are used, each with its own set of properties that make it suitable for different applications. Here's an overview of some of these materials:
Copper: Copper is an excellent choice for fuel lines due to its superior corrosion resistance. It is highly durable and can withstand the harsh conditions of fuel transport, including exposure to various chemicals and temperature fluctuations. Copper's ductility and ease of soldering make it easy to work with, allowing for efficient splicing and connections. This metal is commonly used in high-performance vehicles and racing applications where reliability and longevity are crucial.
Stainless Steel: This metal is renowned for its exceptional resistance to corrosion and oxidation, making it ideal for fuel lines that are exposed to harsh environments. Stainless steel fuel lines offer excellent durability and can handle high-pressure systems without compromising performance. Its non-magnetic properties are advantageous in applications where electromagnetic interference needs to be minimized. The material's strength and flexibility ensure a long-lasting solution for fuel transportation.
Aluminum: Lightweight and highly resistant to corrosion, aluminum is often used in fuel lines, especially for its ability to reduce the overall weight of the system. This is particularly beneficial in aircraft or high-performance automotive applications where weight savings are essential. Aluminum's natural resistance to fuel degradation and its ability to withstand high temperatures make it a popular choice for fuel systems.
Brass: Brass, an alloy of copper and zinc, offers a balance of strength and ductility. It is commonly used for fuel lines in marine environments due to its excellent resistance to saltwater corrosion. Brass is also known for its ease of soldering, making it a convenient choice for splicing and connecting fuel lines. Its non-magnetic and non-sparking properties add to its appeal, especially in sensitive applications.
Each of these metals has unique advantages, and the choice of material depends on the specific requirements of the fuel system, including environmental conditions, pressure, and temperature. Understanding the properties of these common metals is essential when considering splicing or repairing metal fuel lines.
K10 Fuel Line Size: 86 Chevy Truck Specs
You may want to see also
Splicing Techniques: Methods for joining metal fuel lines, including welding and crimping
Splicing metal fuel lines is a critical process in maintaining the integrity and safety of a vehicle's fuel system. When a fuel line is damaged or needs to be extended, splicing techniques are employed to ensure a secure and reliable connection. There are several methods to join metal fuel lines, each with its own advantages and applications.
One common splicing technique is welding. This method involves using a specialized welding torch to melt and fuse the ends of the metal fuel lines together. It requires precision and skill to ensure a strong bond. Before welding, the ends of the fuel lines should be prepared by cleaning and removing any oxidation or debris. This is crucial to prevent impurities from affecting the weld quality. The welder must also ensure that the lines are aligned properly to avoid any misalignment that could lead to leaks or reduced performance. Gas welding or electric arc welding can be used, with the choice depending on the specific requirements and the type of metal being used.
Another popular method is crimping, which uses a crimping tool to apply pressure to the fuel line ends, creating a mechanical connection. This technique is often preferred for its simplicity and ease of use. Crimping involves inserting the fuel line into a crimping sleeve, which is then compressed using the tool. The sleeve's internal threads must match the fuel line's diameter to ensure a tight seal. This method is particularly useful for temporary repairs or when working with flexible metal hoses. However, it may not be as durable as welding for high-pressure applications.
In some cases, a combination of welding and crimping might be employed. For instance, a welder might join two fuel lines using a weld, and then a crimping sleeve could be added to provide an additional layer of security at the splice point. This hybrid approach can offer both the strength of welding and the convenience of crimping.
When splicing metal fuel lines, it is essential to consider the specific requirements of the fuel system, including pressure ratings, temperature tolerances, and the type of fuel being transported. Proper preparation, skilled execution, and adherence to safety guidelines are key to ensuring a successful splice that will stand the test of time and provide reliable performance.
Honda CR-V '98 Fuel Line Cut-Off: Causes and Fixes
You may want to see also
Safety Precautions: Steps to ensure safe splicing, like cleaning and testing
When splicing metal fuel lines, it is crucial to prioritize safety to prevent potential hazards. Here are the essential steps to ensure a secure and reliable splice:
Cleaning the Lines: Begin by thoroughly cleaning both the existing fuel line and the area where the splice will be made. Remove any dirt, corrosion, or debris that could interfere with the splicing process. Use a suitable cleaning agent or solvent to ensure a clean and smooth surface. This step is vital as it prepares the metal for proper bonding and prevents any contaminants from affecting the splice's integrity.
Inspecting for Damage: Carefully inspect the fuel lines for any signs of damage, such as cracks, holes, or corrosion. If any damage is found, it is essential to replace the affected section instead of splicing it. Splicing a damaged line can lead to potential leaks and safety hazards. Ensure that the lines are in good condition before proceeding with the splicing process.
Testing for Leaks: Before and after the splicing process, perform leak tests to ensure the integrity of the fuel lines. Use a soapy water solution or a specialized leak detection kit to identify any potential leaks. Apply pressure to the lines and observe for any bubbles or leaks. This testing process helps identify weak points or potential failure areas, allowing for necessary adjustments or replacements before the splice is made.
Using Appropriate Splicing Techniques: When splicing the metal fuel lines, employ the correct techniques to ensure a secure connection. This may involve using specialized splicing kits or adapters designed for metal fuel lines. Follow the manufacturer's instructions and guidelines for the specific splicing method. Properly align the lines, ensure a tight fit, and secure the splice with the recommended fasteners or clamps.
Post-Splicing Inspection: After completing the splice, conduct a thorough inspection to verify its quality. Check for any signs of leakage, proper alignment, and secure fastening. Test the spliced section by running the fuel system and monitoring for any issues. This final inspection ensures that the splice is safe and functional, providing peace of mind and reliability for your fuel line system.
By following these safety precautions and steps, you can effectively splice metal fuel lines while minimizing the risk of accidents and ensuring the long-term performance of the fuel system.
Fuel Line Sizing for Optimal Performance: Lohler Lawnmower Guide
You may want to see also
Legal Regulations: Industry standards and laws regarding fuel line splicing
When it comes to splicing metal fuel lines, it's crucial to understand the legal and regulatory landscape to ensure compliance and safety. In many jurisdictions, there are specific industry standards and laws governing the modification or repair of fuel lines, especially in the automotive and industrial sectors. These regulations are in place to prevent accidents, ensure product reliability, and maintain environmental standards.
One of the primary considerations is the use of approved splicing methods and materials. Industry standards often dictate the types of adhesives, seals, and connectors that can be used for splicing. For instance, the Society of Automotive Engineers (SAE) and the American Petroleum Institute (API) provide guidelines for fuel line installation and repair, ensuring that the splicing process meets certain quality standards. These standards may include specific requirements for the type of adhesive used, the curing time, and the overall strength of the splice.
Local and national laws also play a significant role in regulating fuel line splicing. In some regions, there are strict regulations regarding the modification of vehicles, and any splicing or alteration must adhere to these rules. For example, in the United States, the National Highway Traffic Safety Administration (NHTSA) sets safety standards for vehicle modifications, including fuel line repairs. These regulations may specify the maximum allowable pressure drop across the splice, the required thickness of the splice material, and the need for additional protective measures.
Furthermore, environmental regulations might come into play when splicing fuel lines, especially in industrial settings. Laws governing the protection of the environment and the prevention of fuel leaks may require specific measures to ensure the splice does not compromise the integrity of the fuel system. This could include the use of leak-proof connections, the implementation of pressure relief mechanisms, and regular inspections to verify the splice's condition.
It is essential for professionals and DIY enthusiasts alike to stay informed about the latest industry standards and legal requirements. Consulting with local authorities, vehicle manufacturers, or industry experts can provide valuable insights into the specific regulations that apply to a particular region or application. By adhering to these legal and industry standards, individuals can ensure that any splicing or modification of metal fuel lines is safe, reliable, and in compliance with the law.
Thawing Frozen Diesel Fuel Lines: Quick Tips for Winter
You may want to see also
Maintenance Tips: Best practices for maintaining spliced metal fuel lines
When dealing with spliced metal fuel lines, it's crucial to follow best practices to ensure optimal performance and safety. Here are some essential maintenance tips to keep in mind:
Regular Inspections: Implement a routine inspection schedule for your spliced fuel lines. Visual inspections are a fundamental part of maintenance. Look for any signs of corrosion, rust, cracks, or damage along the line. Pay close attention to the splice area, as it can be more susceptible to issues. Check for any leaks or drips, even if they are minimal, as they could indicate a developing problem. Keep a record of your inspections to identify patterns or recurring issues over time.
Use of Appropriate Tools: When splicing or repairing metal fuel lines, utilize the right tools and techniques. Ensure that the splice is secure and properly sealed to prevent any fuel leakage. Common tools for splicing include pipe wrenches, pliers, and specialized splicing kits. It is essential to follow manufacturer guidelines or consult a professional to ensure the splice is done correctly. Properly tightened connections will help maintain the integrity of the fuel system.
Corrosion Prevention: Metal fuel lines are prone to corrosion, especially in environments with high moisture or salt content. To prevent corrosion, consider applying a suitable corrosion inhibitor or coating to the metal surface. This is particularly important in spliced areas, where the metal is more exposed. Regularly clean and inspect the lines to remove any corrosive substances or debris that may accumulate.
Fuel Quality and Filtration: Maintain high-quality fuel to minimize the risk of contamination, which can lead to issues with the fuel lines. Use fuel stabilizers and ensure that the fuel tank is properly vented and filtered. Regularly replace fuel filters to prevent debris and contaminants from entering the system, which could potentially damage the spliced fuel lines.
Professional Maintenance: For complex or large-scale splicing projects, it is advisable to seek professional assistance. Certified mechanics or fuel system specialists can provide expert advice and ensure the work is done safely and effectively. They can also offer valuable insights into specific maintenance requirements based on your vehicle's make and model.
By adhering to these maintenance tips, you can ensure the longevity and reliability of spliced metal fuel lines, minimizing the risk of fuel leaks, system failures, and potential safety hazards. Regular care and attention will contribute to a well-maintained fuel system.
Ford Fuel Line Removal: Tips for a Tool-Free Process
You may want to see also
Frequently asked questions
Yes, it is possible to splice a metal fuel line, but it requires careful preparation and the right materials to ensure a secure and reliable connection. Splicing should only be attempted by experienced professionals or those with a thorough understanding of the process to avoid potential leaks or damage.
Splicing a metal fuel line typically involves cleaning and preparing the ends of the lines, using a suitable primer or adhesive to ensure a good bond, and then using specialized connectors or welding techniques to join the lines together. It is crucial to follow manufacturer guidelines and industry standards to guarantee a safe and effective splice.
Absolutely! You will need specific tools like a fuel line cutter, deburr tools, and a fuel line crimping tool. Additionally, having the right type of metal fuel line connectors or welding equipment is essential. It is recommended to use materials and tools designed for fuel line splicing to ensure compatibility and avoid any potential problems.