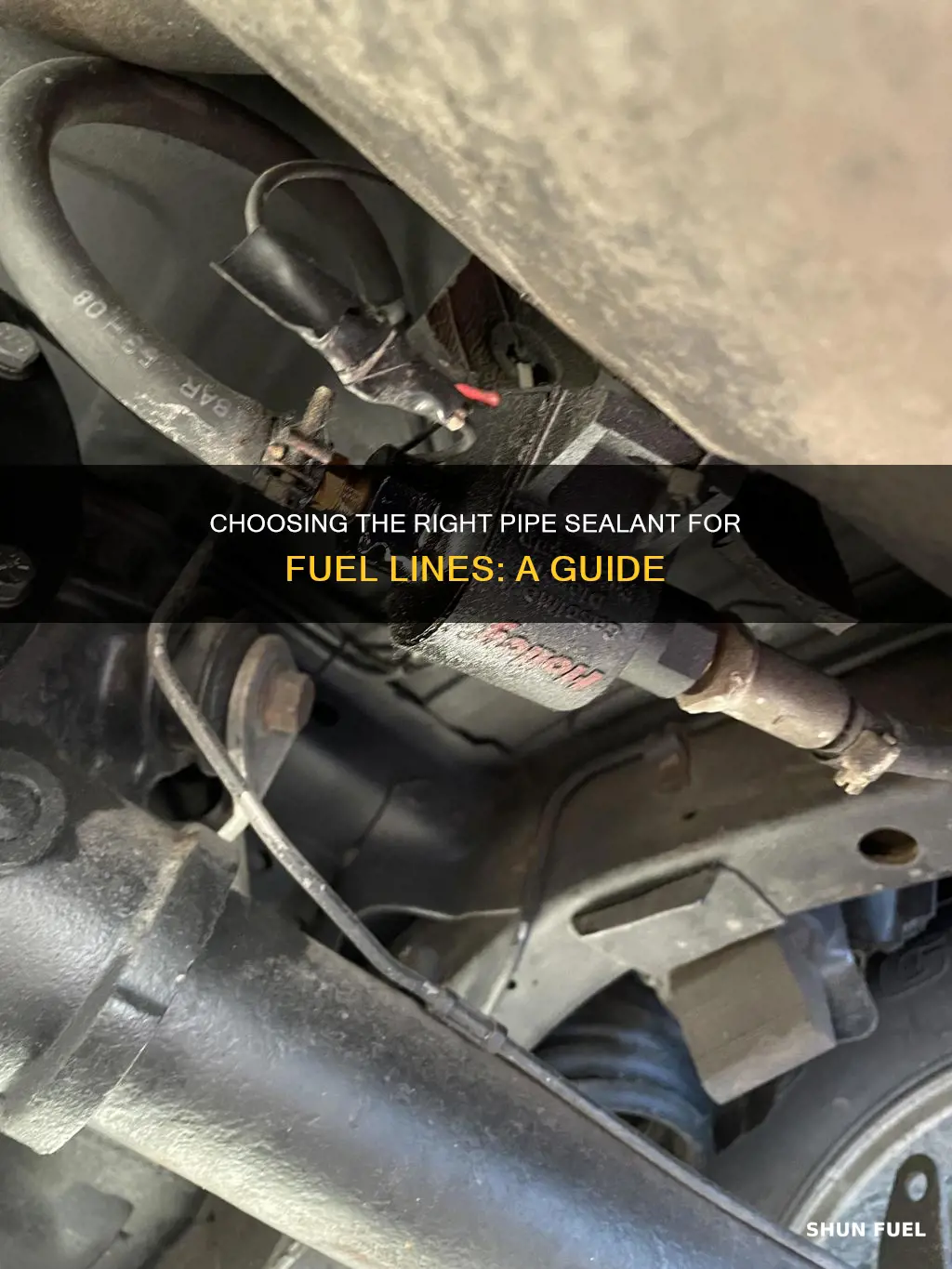
When it comes to maintaining your vehicle's fuel system, choosing the right pipe sealant is crucial. Fuel lines are susceptible to leaks and damage over time due to factors like heat, vibration, and chemical exposure. The right sealant can provide a robust and long-lasting solution to prevent fuel leaks and ensure your vehicle's engine runs efficiently. This guide will explore the various types of pipe sealants available for fuel lines, their advantages, and how to select the best one for your specific needs.
What You'll Learn
- Material Compatibility: Choose a sealant that is compatible with fuel and compatible with the pipe material
- Temperature Resistance: Select a sealant that can withstand fuel line temperatures without hardening or melting
- Flexibility: Opt for a flexible sealant that can accommodate pipe movement without cracking or breaking
- Vibration Resistance: Ensure the sealant can withstand engine vibrations without peeling or flaking
- Chemical Resistance: Pick a sealant resistant to fuel chemicals to prevent degradation and leaks
Material Compatibility: Choose a sealant that is compatible with fuel and compatible with the pipe material
When it comes to selecting a pipe sealant for fuel lines, material compatibility is a critical factor to consider. Fuel lines are designed to withstand the corrosive nature of gasoline, diesel, and other fuels, and the chosen sealant must be able to provide a reliable barrier without compromising the integrity of the pipe material. Incompatibility between the sealant and the fuel or the pipe can lead to degradation, leaks, and potential safety hazards.
The first step is to identify the type of fuel your system uses. Different fuels have varying chemical compositions, and some sealants may not be suitable for all types. For instance, gasoline-based sealants might not be ideal for diesel fuel lines due to the different chemical properties and potential for degradation. Research and select a sealant that is specifically formulated to be compatible with the fuel type in your vehicle.
Next, consider the material of the fuel lines. Common materials include rubber, plastic (such as PVC or ABS), and metal. Each material has unique properties and requires a sealant that can adhere and bond effectively without causing damage or distortion. For example, rubber fuel lines may require a sealant that is flexible and can accommodate movement, while plastic lines might need a sealant that is more rigid to prevent cracking.
A suitable sealant should be able to form a strong bond with the pipe material, ensuring that the fuel line remains intact and leak-free. Look for products that are specifically designed for the type of pipe material you have. Some manufacturers provide recommendations or even offer custom-made sealants for their specific fuel line systems. Following these guidelines ensures that the sealant will adhere properly and provide long-lasting protection.
Additionally, consider the environmental conditions your fuel lines will be exposed to. Temperature fluctuations, UV radiation, and other external factors can impact the performance of the sealant. Choose a product that is designed to withstand these conditions, ensuring its longevity and effectiveness. By carefully considering material compatibility, you can select a sealant that provides a secure and reliable solution for your fuel line needs.
Unleash Your Engine's Potential: Understanding the 8AM Fuel Line
You may want to see also
Temperature Resistance: Select a sealant that can withstand fuel line temperatures without hardening or melting
When it comes to choosing the right pipe sealant for fuel lines, temperature resistance is a critical factor that should not be overlooked. Fuel lines operate in demanding environments, often exposed to varying temperatures, and the sealant must be able to withstand these conditions without compromising its effectiveness. The primary concern is to ensure that the sealant does not harden or melt under the influence of heat, as this could lead to a loss of integrity and potential fuel leaks.
The temperature range of fuel lines can vary significantly, depending on the vehicle and its operating conditions. In some cases, fuel lines may experience extreme temperatures, especially in high-performance engines or vehicles used in harsh climates. Therefore, the chosen sealant should have a wide temperature resistance range, typically between -40°F and 300°F (-40°C and 150°C), to accommodate these varying conditions. This ensures that the sealant remains flexible and maintains its sealing properties even in the most challenging environments.
One effective approach to selecting a suitable sealant is to consider the materials used in its composition. Silicone-based sealants are known for their excellent temperature resistance, remaining pliable and effective even in extreme heat. They can withstand temperatures up to 500°F (260°C) without hardening or melting, making them ideal for fuel line applications. Additionally, silicone sealants are resistant to fuel degradation, ensuring that the sealant itself does not break down when exposed to fuel over time.
Another option to consider is epoxy-based sealants, which offer superior temperature resistance. These sealants typically have a higher melting point and can endure temperatures up to 400°F (204°C) without any significant changes in their properties. However, it is important to note that epoxy sealants may become brittle at very low temperatures, so a balanced temperature range is essential for optimal performance.
In summary, when selecting a pipe sealant for fuel lines, temperature resistance is a key consideration. The chosen sealant should be able to withstand the operating temperatures of the fuel lines without hardening or melting, ensuring the long-term integrity of the fuel system. By considering the temperature range and the material properties of the sealant, you can make an informed decision and choose the most suitable option for your specific application.
Wedeater Fuel Lines Reversed: A Recipe for Disaster?
You may want to see also
Flexibility: Opt for a flexible sealant that can accommodate pipe movement without cracking or breaking
When it comes to choosing the right pipe sealant for your fuel line, flexibility is a crucial factor to consider. Fuel lines are subject to constant movement and vibration, especially in the engine compartment, where they can experience a lot of stress. A flexible sealant is essential to ensure that the fuel line remains intact and functional over time.
Opting for a flexible sealant means selecting a material that can easily bend and stretch without compromising its structural integrity. This is particularly important in areas where the fuel line is exposed to engine movement, such as near the engine block or where it connects to other components. If the sealant is too rigid, it may crack or break, leading to potential fuel leaks and engine performance issues.
The key to achieving flexibility in a pipe sealant lies in the choice of materials. Silicone-based sealants are often preferred for their inherent flexibility. These sealants can withstand a wide range of temperatures and movements without becoming brittle or losing their sealing properties. Look for sealants that are specifically designed for automotive applications, as they are formulated to meet the unique demands of fuel lines.
Additionally, consider the application process. A flexible sealant should be easy to apply and spread evenly along the fuel line. It should also cure quickly, forming a strong bond that can withstand the rigors of the engine environment. Some sealants even come in convenient syringe-like applicators, making it easier to reach tight spaces and ensure complete coverage.
Remember, the goal is to find a sealant that can move with the fuel line, providing a reliable seal that endures over time. By choosing a flexible sealant, you are taking a proactive approach to maintaining the integrity of your fuel system, which is crucial for optimal engine performance and longevity.
Fram G3727 Inline Fuel Filter: Compatibility and Benefits
You may want to see also
Vibration Resistance: Ensure the sealant can withstand engine vibrations without peeling or flaking
When it comes to choosing a pipe sealant for fuel lines, one crucial aspect to consider is vibration resistance. Engine vibrations can be intense and relentless, and the fuel lines are no exception. These vibrations can cause the sealant to peel or flake off over time, leading to potential fuel leaks and other issues. Therefore, it is essential to select a sealant that can withstand the rigors of the engine environment.
The key to achieving vibration resistance lies in the sealant's composition and application method. Look for sealants that are specifically designed for high-vibration applications, such as those used in the automotive industry. These sealants often contain advanced polymers and additives that provide enhanced flexibility and durability. The sealant should be able to conform to the shape of the fuel line and withstand the repetitive motion and stress caused by engine vibrations.
During the application process, ensure that the sealant is applied evenly and smoothly along the fuel line. Any gaps or uneven layers can lead to areas of weakness where the sealant may fail under vibration. Take the time to clean the surface of the fuel line and remove any debris or contaminants that could interfere with the sealant's bond. Proper surface preparation is crucial for achieving optimal vibration resistance.
Additionally, consider the operating conditions of your vehicle. If you frequently drive through rough terrain or experience high-performance driving, the sealant's vibration resistance becomes even more critical. In such cases, you might want to consult with a professional mechanic or refer to the manufacturer's recommendations to choose the most suitable sealant for your specific needs.
By prioritizing vibration resistance, you can ensure that the sealant effectively seals the fuel line, preventing leaks and maintaining the integrity of your vehicle's fuel system. This is particularly important in high-performance or off-road vehicles where engine vibrations are more pronounced. Remember, the right sealant choice can make a significant difference in the long-term reliability and performance of your fuel system.
Understanding Snowmobile Fuel Lines: Inside the Gas Tank
You may want to see also
Chemical Resistance: Pick a sealant resistant to fuel chemicals to prevent degradation and leaks
When it comes to choosing the right pipe sealant for fuel lines, chemical resistance is a critical factor to consider. Fuel lines are exposed to a variety of chemicals, including gasoline, diesel, and other additives, which can cause degradation and potential leaks over time. Therefore, selecting a sealant that is resistant to these fuel chemicals is essential to ensure the long-term integrity and reliability of your fuel system.
The primary goal is to prevent the sealant itself from breaking down or dissolving when exposed to fuel chemicals. This degradation can lead to the sealant losing its ability to form a secure bond and seal the pipe, potentially resulting in fuel leaks and system malfunctions. To achieve this, look for sealants specifically designed to withstand the harsh environment of fuel systems. These sealants are typically formulated with high-performance polymers and additives that provide excellent chemical resistance.
One approach is to consider the type of fuel you are working with. Different fuels have varying compositions and additives, so a sealant that is resistant to one type of fuel may not be as effective for another. For example, gasoline-based fuels often contain detergents and antioxidants, while diesel may have different additives. Therefore, it is crucial to choose a sealant that has been tested and proven effective against the specific chemicals present in your fuel.
A good starting point is to research and compare various sealant options available in the market. Look for products that are specifically marketed as fuel-resistant or fuel-line sealants. These products are often designed with a unique formulation that ensures stability and resistance to fuel chemicals. Additionally, consider the temperature range and environmental conditions your fuel system will be exposed to, as this can further influence the choice of sealant.
In summary, when selecting a pipe sealant for fuel lines, chemical resistance is a key consideration. Opt for a sealant that is known for its ability to withstand the chemicals present in your fuel, ensuring long-term protection against degradation and potential leaks. By choosing the right sealant, you can maintain the integrity of your fuel system and avoid costly repairs and maintenance issues.
Understanding the Three Fuel Lines in an Engine: A Comprehensive Guide
You may want to see also
Frequently asked questions
For fuel lines, a high-temperature, silicone-based sealant is often recommended. These sealants are designed to withstand the extreme temperatures and pressures associated with fuel systems. They form a flexible, durable seal that can accommodate movement and vibrations, ensuring a reliable and long-lasting repair.
While general-purpose sealants can be used in a pinch, they are not ideal for fuel lines. Fuel systems require a sealant that can handle the specific challenges of fuel, including its volatile nature and the potential for corrosion. Specialized fuel line sealants are formulated to resist fuel degradation and provide a secure, long-lasting seal.
When selecting the amount of sealant, consider the length of the fuel line you need to seal. It's generally recommended to use enough sealant to create a continuous, even layer around the entire circumference of the pipe. A rule of thumb is to use a length of sealant that is approximately 1/4 to 1/2 inch longer than the pipe's diameter, ensuring complete coverage and a strong bond.