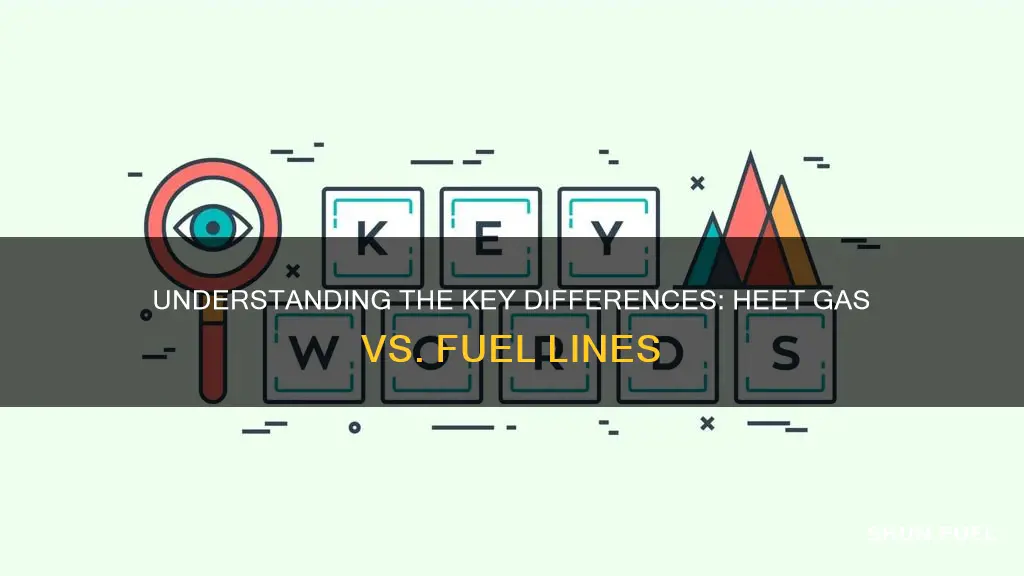
The terms heated gas line and fuel line are often used in discussions about vehicle systems, particularly in the context of engines. While both are crucial for the operation of an engine, they serve distinct purposes. A heated gas line, also known as a heated intake manifold, is a component in some engines that preheats the air-fuel mixture before it enters the combustion chamber. This process improves engine performance and efficiency by ensuring the fuel burns more effectively. On the other hand, a fuel line is a pipeline or conduit that transports fuel from the fuel tank to the engine's fuel injectors or carburetor. The fuel line ensures a steady and controlled supply of fuel to the engine, allowing for precise fuel injection or mixing with air for combustion. Understanding the difference between these two lines is essential for maintaining and optimizing engine performance.
Characteristics | Values |
---|---|
Definition | A heated gas line is a pipe or conduit used to transport natural gas or propane at high temperatures, often for heating or cooking purposes. A fuel line, on the other hand, is a smaller diameter pipe used to deliver liquid or gaseous fuel to an engine or appliance. |
Material | Heated gas lines are typically made of materials like steel, copper, or plastic (PVC) that can withstand high temperatures and corrosion resistance. Fuel lines are often made of materials like rubber, plastic, or metal, depending on the application and fuel type. |
Temperature Rating | Heated gas lines are designed to handle high temperatures, often up to 1000°F or more, to ensure the gas remains in a gaseous state. Fuel lines may have different temperature ratings depending on the fuel and application, but they are generally not designed for extremely high temperatures. |
Pressure Rating | Gas lines, especially those for natural gas, often have higher pressure ratings to handle the force of the gas flow. Fuel lines may have varying pressure ratings depending on the engine or appliance they serve. |
Application | Heated gas lines are commonly used in residential and commercial settings for heating, cooking, and water heating. Fuel lines are used in engines, generators, and various industrial applications to supply fuel to the combustion chamber. |
Flexibility | Gas lines, especially those made of flexible materials, can be more flexible and easier to route compared to fuel lines, which may be stiffer due to the nature of the fuel they carry. |
Safety Considerations | Both heated gas lines and fuel lines require careful installation and maintenance to prevent leaks and ensure safety. Heated gas lines need to be properly insulated and vented, while fuel lines must be protected from damage and have appropriate fittings to prevent fuel leaks. |
What You'll Learn
- Definition: Heated gas lines carry hot gases, while fuel lines transport liquid or gaseous fuel
- Temperature: Gas lines are heated to maintain pressure, whereas fuel lines are not
- Flow Rate: Gas lines often have higher flow rates compared to fuel lines
- Materials: Different materials are used for each, considering heat resistance
- Applications: Heated gas lines are used in ovens, while fuel lines are found in engines
Definition: Heated gas lines carry hot gases, while fuel lines transport liquid or gaseous fuel
Heated gas lines and fuel lines are essential components in various industrial and mechanical systems, each serving distinct purposes. As the name suggests, heated gas lines are designed to transport gases that have been heated to a specific temperature, ensuring they remain in a gaseous state. These lines are commonly used in applications where the gas needs to be maintained at a certain temperature, such as in industrial processes, power generation, or even in some heating systems. The primary function of heated gas lines is to provide a controlled environment for the gas, preventing it from cooling down and potentially condensing, which could lead to various operational issues.
On the other hand, fuel lines are responsible for the transportation of either liquid or gaseous fuel, which is a critical component in many combustion processes. These lines are typically used to supply fuel to engines, furnaces, or any system that requires a continuous and controlled supply of energy. Fuel lines are designed to handle the specific characteristics of the fuel they carry, whether it's a liquid like gasoline or diesel, or a gaseous fuel such as natural gas or propane. The key difference lies in the state of the substance being transported; heated gas lines are specifically for gases, while fuel lines accommodate both liquids and gases, depending on the application.
In industrial settings, heated gas lines are often used in processes like natural gas processing, where the gas needs to be heated to remove impurities and maintain its purity. This ensures efficient combustion and optimal performance in power generation plants. In contrast, fuel lines are prevalent in automotive applications, where they supply gasoline or diesel to the engine, or in residential settings, where they provide natural gas for heating and cooking. The design and construction of these lines must consider factors such as pressure, temperature, and compatibility with the fuel to ensure safe and efficient operation.
The materials used for these lines are also distinct. Heated gas lines are often made of materials that can withstand high temperatures and corrosion, such as stainless steel or specialized alloys. Fuel lines, on the other hand, may use materials like rubber, plastic, or metal, depending on the fuel type and system requirements. The choice of material is crucial to prevent any adverse reactions between the line material and the fuel, which could lead to contamination or performance issues.
In summary, the primary distinction between heated gas lines and fuel lines lies in their purpose and the state of the substance they transport. Heated gas lines are specialized for carrying hot gases, ensuring they remain in a gaseous state, while fuel lines are versatile, accommodating both liquid and gaseous fuels. Understanding these differences is essential for engineers and technicians to select the appropriate lines for specific applications, ensuring efficient and safe operation in various industries.
Understanding Fuel Pickup Lines for Outboard Motors: A Comprehensive Guide
You may want to see also
Temperature: Gas lines are heated to maintain pressure, whereas fuel lines are not
Gas lines and fuel lines are essential components in various systems, particularly in the context of heating and transportation. One significant difference between these two types of lines is their temperature management and the role it plays in their functionality.
Gas lines, often associated with natural gas or propane, are designed to transport fuel at elevated temperatures to maintain pressure. This is a critical aspect of their operation, especially in heating systems. When gas is heated, it expands, and this expansion is used to create pressure, which is then utilized to power engines or heat homes and buildings. For instance, in a residential setting, a gas line might supply natural gas to a furnace, where it is ignited to produce heat. The gas line itself is typically insulated to prevent excessive heat loss, ensuring that the gas remains at an optimal temperature to sustain the required pressure. This heated state is necessary to overcome the natural tendency of gas to cool and contract, which would reduce its pressure and, consequently, its effectiveness.
On the other hand, fuel lines, such as those used in automotive applications, do not require the same level of temperature control. Fuel lines are responsible for delivering gasoline, diesel, or other fuels to the engine. These lines are generally not heated because the fuel itself is not under high pressure, and heating it could lead to unnecessary energy consumption and potential safety hazards. Instead, fuel lines are often insulated to prevent fuel from cooling and thickening, which could cause blockages or reduced flow. The primary concern with fuel lines is ensuring a consistent and smooth flow of fuel to the engine, rather than maintaining a specific temperature.
The temperature management of gas lines is a safety and efficiency consideration. Heated gas lines prevent the gas from condensing, which could lead to reduced pressure and performance. This is particularly important in industrial settings where large volumes of gas are used, and any drop in pressure could have significant operational implications. In contrast, fuel lines in vehicles are designed to handle the fuel's natural temperature variations, ensuring that the fuel remains in a liquid state and can be effectively injected into the engine.
In summary, the temperature of gas lines is a critical factor in their design and operation, as it directly impacts pressure maintenance. Fuel lines, while requiring careful insulation, do not need to be heated to the same extent, allowing for more flexibility in their construction and use. Understanding these temperature-related differences is essential for optimizing the performance and safety of various systems that rely on gas and fuel lines.
Unraveling the Mystery: 1971 Jeep Fuel Line Fitting Secrets
You may want to see also
Flow Rate: Gas lines often have higher flow rates compared to fuel lines
Gas lines and fuel lines are essential components in automotive and industrial systems, each serving a unique purpose. When it comes to the flow rate, or the volume of fluid or gas that passes through a line per unit of time, there is a notable difference between these two types of lines. Gas lines are designed to handle higher flow rates compared to fuel lines. This is primarily due to the nature of the substances they carry and the requirements of the systems they serve.
In the context of automotive applications, gas lines are typically used to deliver fuel to the engine's intake system. Gasoline, as a volatile and highly flammable substance, requires precise and rapid delivery to ensure efficient combustion. The higher flow rate in gas lines allows for a quick and continuous supply of fuel, enabling the engine to operate optimally. This is crucial for maintaining engine performance, especially during acceleration and high-load conditions.
On the other hand, fuel lines are responsible for transporting a less volatile fuel, such as diesel or kerosene, to the engine. While fuel still needs to be delivered efficiently, the flow rate requirements are generally lower compared to gas lines. Fuel lines are designed to provide a steady and controlled flow of fuel, ensuring that the engine receives the necessary amount without wastage or excessive pressure. This balance is essential to maintain engine efficiency and longevity.
The difference in flow rate is also influenced by the physical properties of the substances. Gasoline, being a lighter and more compressible fluid, can flow more rapidly through a line without excessive pressure. In contrast, diesel or kerosene, being heavier and less compressible, may require a more gradual flow rate to prevent issues like fuel atomization and engine misfires.
In summary, the higher flow rate in gas lines is a critical aspect of their design, ensuring that the engine receives the volatile fuel required for efficient operation. This distinction in flow rate management highlights the importance of understanding the unique characteristics of different substances and their respective systems when designing and maintaining automotive or industrial infrastructure.
Understanding Fuel Line Flush: A Comprehensive Guide
You may want to see also
Materials: Different materials are used for each, considering heat resistance
When it comes to the materials used for hot gas lines and fuel lines, heat resistance is a critical factor to consider. These lines are designed to withstand high temperatures and pressures, especially in automotive and industrial applications. The choice of material depends on the specific requirements of the system, including the operating temperature, pressure, and the type of fluid being transported.
For hot gas lines, materials such as stainless steel, Inconel, and Monel are commonly used. These alloys offer excellent heat resistance and can handle the extreme temperatures associated with hot gases, such as those produced by a combustion engine. Stainless steel, for instance, is known for its corrosion resistance and ability to maintain its structural integrity at elevated temperatures. Inconel, a nickel-chromium alloy, provides superior heat resistance and is often used in high-temperature environments. Monel, a copper-nickel alloy, is another suitable option due to its excellent heat and corrosion resistance.
On the other hand, fuel lines typically operate at lower temperatures compared to hot gas lines. Materials like high-density polyethylene (HDPE), polyurethane, and rubber are often chosen for fuel lines. HDPE is a popular choice due to its flexibility, chemical resistance, and ability to withstand a wide range of temperatures. Polyurethane is another durable material that offers flexibility and resistance to abrasion, making it suitable for fuel lines that need to navigate through tight spaces. Rubber, a traditional material, is also used for its flexibility and ability to absorb vibrations, ensuring a secure and reliable connection.
The selection of materials for these lines is crucial to ensure the safety and efficiency of the system. Heat-resistant materials prevent degradation, corrosion, and potential failures, especially in high-temperature environments. Additionally, the flexibility and durability of the chosen materials contribute to the overall performance and longevity of the fuel and hot gas systems. It is essential to consider the specific operating conditions and choose materials that can withstand the demands of the application.
Understanding Rubber Fuel Line Sizes for CJ7s
You may want to see also
Applications: Heated gas lines are used in ovens, while fuel lines are found in engines
Heated gas lines and fuel lines are both essential components in various applications, but they serve distinct purposes and are used in different systems. Understanding their applications can help in maintaining and troubleshooting these systems effectively.
Heated Gas Lines in Ovens:
Heated gas lines are commonly used in cooking appliances, particularly in ovens. These lines are designed to carry a combustible gas, such as natural gas or propane, from the fuel source to the oven's burners. The key feature of heated gas lines is their ability to maintain a consistent temperature, ensuring that the gas remains in a gaseous state and burns efficiently. In ovens, heated gas lines are crucial for precise temperature control, allowing for even cooking and baking. The heat generated by the gas combustion process is used to heat the oven's interior, providing the necessary heat for cooking food. This application requires careful design to ensure the gas is properly mixed with air, ignited, and burned safely and efficiently.
Fuel Lines in Engines:
On the other hand, fuel lines are an integral part of internal combustion engines. These lines are responsible for transporting fuel from the fuel tank to the engine's carburetor or fuel injection system. In engines, fuel lines must handle high-pressure fuel, which is typically in a liquid or gaseous state, depending on the engine's design. The primary function of fuel lines is to ensure a continuous and controlled supply of fuel to the engine's cylinders for combustion. This application demands fuel lines that are durable and capable of withstanding the high pressure and temperature changes that occur during engine operation. Proper fuel line installation and maintenance are critical to prevent fuel leaks and ensure optimal engine performance.
In summary, heated gas lines are specifically designed for oven applications, where they provide a controlled supply of combustible gas for efficient heating. In contrast, fuel lines are engineered for engines, managing the high-pressure fuel required for combustion. Both systems require careful consideration of materials and design to ensure safe and efficient operation in their respective applications. Understanding these differences is essential for anyone working with or maintaining these systems.
Unveiling the Material Mystery: What Fuels Clear Fuel Lines?
You may want to see also
Frequently asked questions
The main distinction lies in their purpose and the type of fuel they carry. A heater gas line is specifically designed to transport natural gas or propane, which is commonly used for heating homes, water, and cooking. On the other hand, a fuel line is typically associated with liquid fuels, such as gasoline or diesel, used for powering vehicles or machinery.
While it is technically possible to use a heater gas line for fuel, it is not recommended. Heater gas lines are not designed to handle the pressure and volatility of liquid fuels, which can lead to safety hazards and potential damage to the system. It's essential to use the appropriate fuel line for the specific fuel type to ensure safety and optimal performance.
Identifying the correct fuel line involves understanding your vehicle's fuel system and the type of fuel it uses. Gasoline vehicles typically have fuel lines made of rubber or plastic, while diesel engines may use steel fuel lines. Consulting your vehicle's manual or seeking professional advice can help determine the appropriate fuel line for your specific make and model.
Absolutely. Heater gas lines should be handled with care due to the potential risks associated with natural gas or propane. It is crucial to ensure proper ventilation, avoid sparks or open flames, and follow safety protocols when working with these lines. Regular maintenance and inspections by qualified professionals are recommended to prevent leaks and ensure safe operation.
Converting a fuel line to a heater gas line or vice versa is not a straightforward process and may require significant modifications to the fuel system. It is generally not recommended unless performed by experienced professionals who can ensure the conversion meets safety standards and regulations. It's best to consult with experts in the field to make such changes safely and effectively.