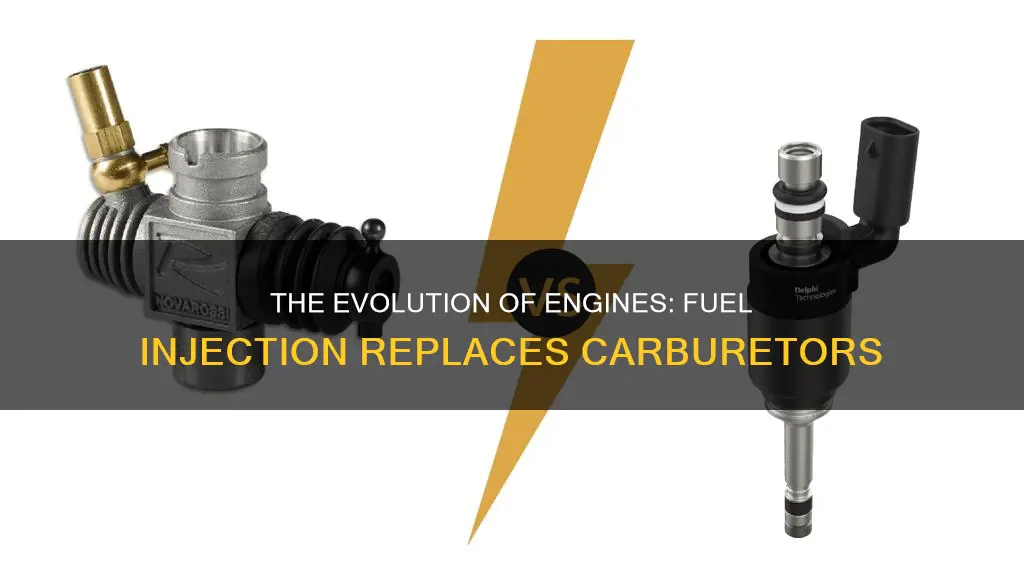
Fuel injection is a means of introducing fuel into an internal combustion engine, most commonly automotive engines, through a fuel injector. This process has been used since the 1950s, but it was in the 1990s that fuel injectors began to replace carburettors, which were the previous device used to supply fuel to the engine. Carburettors were phased out due to stricter emissions requirements and the need for more efficient fuel systems. Fuel injection systems are more precise and can be controlled by the engine control unit (ECU), which adjusts the air-to-fuel ratio in real time, allowing for more efficient combustion and power output while reducing emissions.
Characteristics | Values |
---|---|
Replaced Part | Carburetor |
Replaced By | Fuel Injector |
Replaced Part Function | Device that supplied fuel to the engine |
Replacement Part Function | Spraying pressurised fuel into the engine |
Replacement Process | Gradual, starting with throttle body fuel injection systems and moving to multi-port fuel injection |
Replacement Timeline | Gradual process since the 1950s, fully replacing carburetors by the early 1990s |
Reason for Replacement | Fuel injectors are more efficient, reliable, and better at meeting emissions and fuel efficiency standards |
What You'll Learn
Carburettors were replaced by throttle body fuel injection systems
Throttle body fuel injection systems were a near drop-in replacement for carburettors, which allowed automakers to avoid making drastic changes to their engine designs. These systems incorporated electrically controlled fuel injector valves into the throttle body.
The primary difference between carburettors and fuel injection systems is how they deliver fuel. Carburettors rely on suction created by intake air accelerated through a Venturi tube to draw fuel into the airstream. In contrast, fuel injection systems atomize the fuel through a small nozzle under high pressure.
The introduction of fuel injection systems to automobiles has been a significant factor in increasing engine power in recent years. Initially, the adoption of fuel injection was slow due to the inherent complexities of the system. However, computer integration revolutionized the design of this automotive subsystem, and intelligent computer controls have now made carburettors obsolete.
Modern automobiles must meet stringent emissions and fuel efficiency standards, and these have mostly been achieved through improvements in engine fuel entry systems. The emergence of computer-automated controls has enabled manufacturers to build smaller, more powerful engines by increasing the efficiency of the combustion process.
Replacing Fuel Sending Unit in a 2005 Trailblazer
You may want to see also
Carburettors couldn't meet stricter emissions requirements
Carburettors were unable to meet stricter emissions requirements for several reasons. Firstly, to meet these requirements, catalytic converters were introduced, which demanded very careful control of the air-to-fuel ratio. Carburettors were unable to achieve this control. Oxygen sensors monitor the amount of oxygen in the exhaust, and the engine control unit (ECU) uses this information to adjust the air-to-fuel ratio in real time. This is called closed-loop control, which was not feasible with carburettors.
Secondly, the inherent complexities of the fuel injection system meant that its introduction was initially slow. However, computer integration revolutionized the design of this automotive subsystem, and it has become the onboard controller of the fuel injection system itself. Intelligent computer controls for fuel-injection systems have effectively forced the carburettor into obsolescence. Computer-automated controls allow manufacturers to build smaller, more powerful engines by increasing the efficiency of the combustion process. Most of these advancements have come from the precise timing of the fuel entering the combustion chamber, as well as the timing of the ignition itself.
The introduction of fuel injection systems has also allowed for the precise control of the temporal and spatial placement of the fuel spray. This type of engine is called a stratified charge engine, where the aim is to have a pocket of rich fuel within a larger body of a weak air-fuel mixture, ensuring that the rich, easily ignitable area surrounds the spark at the point of ignition.
Finally, the introduction of the microcomputer age aided in the design and implementation of fuel injection systems. These systems could now be simulated in a virtual environment and then modified to run with new parameters in minutes, a process that would have taken weeks or months using traditional methods.
Replacing Kubota Fuel Gauge Sensor: Step-by-Step Guide
You may want to see also
Fuel injection systems are more efficient and reliable
The inherent complexities of fuel injection systems initially slowed their adoption. However, the integration of computer controls and automation has since improved the efficiency and reliability of the technology. Computer simulations and models have allowed manufacturers to design fuel injection systems that precisely control the temporal and spatial placement of the fuel spray during the combustion process. This has resulted in more efficient combustion and increased power output.
The use of computers and digital electronics in fuel injection systems has also allowed for more precise control of the timing and amount of fuel released, depending on the demands placed on the engine. This level of precision is not possible with carburetors. For example, Honda's VTEC (Variable Valve Timing and Lift Electronic Control) technology constantly monitors the demands placed on the engine and adjusts the fuel injection timing, intake valve open duration, and other relevant factors. This technology allows the engine to deliver ample low-rpm torque and high-rpm power without sacrificing either, resulting in improved functionality and efficiency.
The use of fuel injection systems has also contributed to meeting stricter emissions requirements. Catalytic converters, which require very careful control of the air-to-fuel ratio to be effective, were introduced to reduce emissions. The closed-loop control needed for this was not feasible to achieve with carburetors. Oxygen sensors in fuel injection systems monitor the amount of oxygen in the exhaust, and the engine control unit (ECU) uses this information to adjust the air-to-fuel ratio in real time, resulting in reduced emissions.
Fuel Filter Replacement: Signs You Need to Know
You may want to see also
Fuel injection systems are computer-controlled
The introduction of fuel injection to automobiles has been a significant factor in increasing engine power in recent years. Initially, the uptake of fuel injection was slow due to the inherent complexities of the system. However, computer integration revolutionised the design of this automotive subsystem, and it has become the onboard controller of the fuel injection system itself.
Modern automobiles must meet stringent emissions and fuel efficiency standards. These standards have mostly been achieved through improvements in the engine fuel entry systems. The desire to create powerful automobiles is a driving force in the advancement of engine technology.
Until the early 1970s, additional horsepower came from larger and more costly engines. This was due to the belief that burning more gasoline was the best way to increase power. However, by the 1970s, cities were blanketed in thick black smog, a byproduct of combustion. To combat this, the US government enacted regulations that raised minimum fuel efficiency requirements for automobiles.
With the emergence of computer-automated controls, auto manufacturers found that it was possible to build smaller engines with power to spare by increasing the efficiency of the combustion process. Most of these advancements have come from the precise timing of the fuel entering the combustion chamber, as well as the timing of the ignition itself.
Fuel injection works on a commonly known principle: it is much easier to burn smaller twigs and leaves (i.e., misted gasoline) than it is to burn a large log (a large droplet from standard intake valves). There is a practical and optimal limit to the size of the mist particles—about 10 micrometres (about half the width of a human hair).
The introduction of the microcomputer age removed the hurdle in the design and implementation of fuel injection systems. The systems could now be simulated in a virtual stroke in a computer and then modified to run with new parameters in minutes. This process would have taken weeks or months using traditional industrial practices.
Digital logic, and more specifically micro-controllers (small computers), also revolutionised the actual implementation of fuel injection systems. Previously, the delivery mechanism of fuel was mechanical and generated from the injector forcing gasoline through a comb filter, producing a relatively inconsistent mist. However, with the advent of modern processing technology, the timing of one or even several separate injectors can be precisely controlled in each piston. In addition, the timing and amount of fuel released can be varied depending on the demands placed on the engine by the driver.
Replacing the Fuel Pump in Your 1986 Buick Electra
You may want to see also
Fuel injection systems are more precise
The primary difference between carburetion and fuel injection is that fuel injection atomizes the fuel through a small nozzle under high pressure, while carburetion relies on suction created by intake air accelerated through a Venturi tube to draw fuel into the airstream. The suction method of carburetors is less precise than the atomization of fuel injection.
Single-point fuel injection systems, also known as throttle-body injection, feature a common fuel injector for all the cylinders in the combustion chamber of the engine. This is the oldest and simplest form of the fuel injection system. While it has an edge over the carburetor, it has a slight disadvantage: since it uses a single injector, it disturbs the performance of an engine at high RPMs and causes rough ride quality as the required fuel supply isn't fulfilled. Moreover, a small fraction of fuel gets condensed outside the intake manifold of the cylinders, causing fuel wastage.
Multi-point fuel injection, or port injection, is more precise than single-point injection. In multi-point fuel injection technology, every cylinder in the combustion chamber of the engine is given an injector at the front of their inlet valves (outside the intake port). Every injector sprays fuel at the same time, and each cylinder gets a more precise volume of fuel, with less possibility of fuel condensation outside the intake manifold. While multi-point injection has the advantage of lower fuel wastage compared to single-point injection, since the fuel is sprayed at the same time in all the cylinders, it doesn't get properly synced with the rotation of all the pistons. This results in the fuel idling in the engine and port for as long as 150 milliseconds. Nonetheless, from a performance perspective, multi-point injection functions much better than single-point injection.
The sequential fuel injection system is the most effective and efficient of all the fuel injection systems currently available. It eliminates the disadvantage of multi-point injection, where fuel is sprayed at the same time in all cylinders. In a sequential fuel injection system, the fuel injectors function with respect to the cylinders they are connected to. Every injector injects fuel only when the intake valve of the cylinder opens. It remains idle for the rest of the steps. An ECU monitors the movement of cylinders and triggers the injectors only when required.
Direct fuel injection is also very precise. In this system, the injector is placed inside the cylinder to directly inject the fuel, bypassing the intake valve or manifold. While this type of fuel injection system is usually seen in diesel engines, it has a significant space in petrol engines as well, where it's known as GDI (gasoline direct injection). In direct fuel injection, all the fuel is directly injected into the cylinder, which produces maximum fuel economy. In diesel engines, direct fuel injection has been used since the 1920s, whereas in petrol engines, it's been used since around World War II.
Replacing the Fuel Pump on Your Kawasaki 250F
You may want to see also
Frequently asked questions
Carburetors were replaced by fuel injection.
Fuel injection is the introduction of fuel into an internal combustion engine, usually an automotive engine, by means of a fuel injector. Fuel injection atomizes the fuel through a small nozzle under high pressure.
Carburetors were gradually replaced by fuel injection from the 1950s onwards. By the early 1990s, fuel injection had largely replaced carburetors.