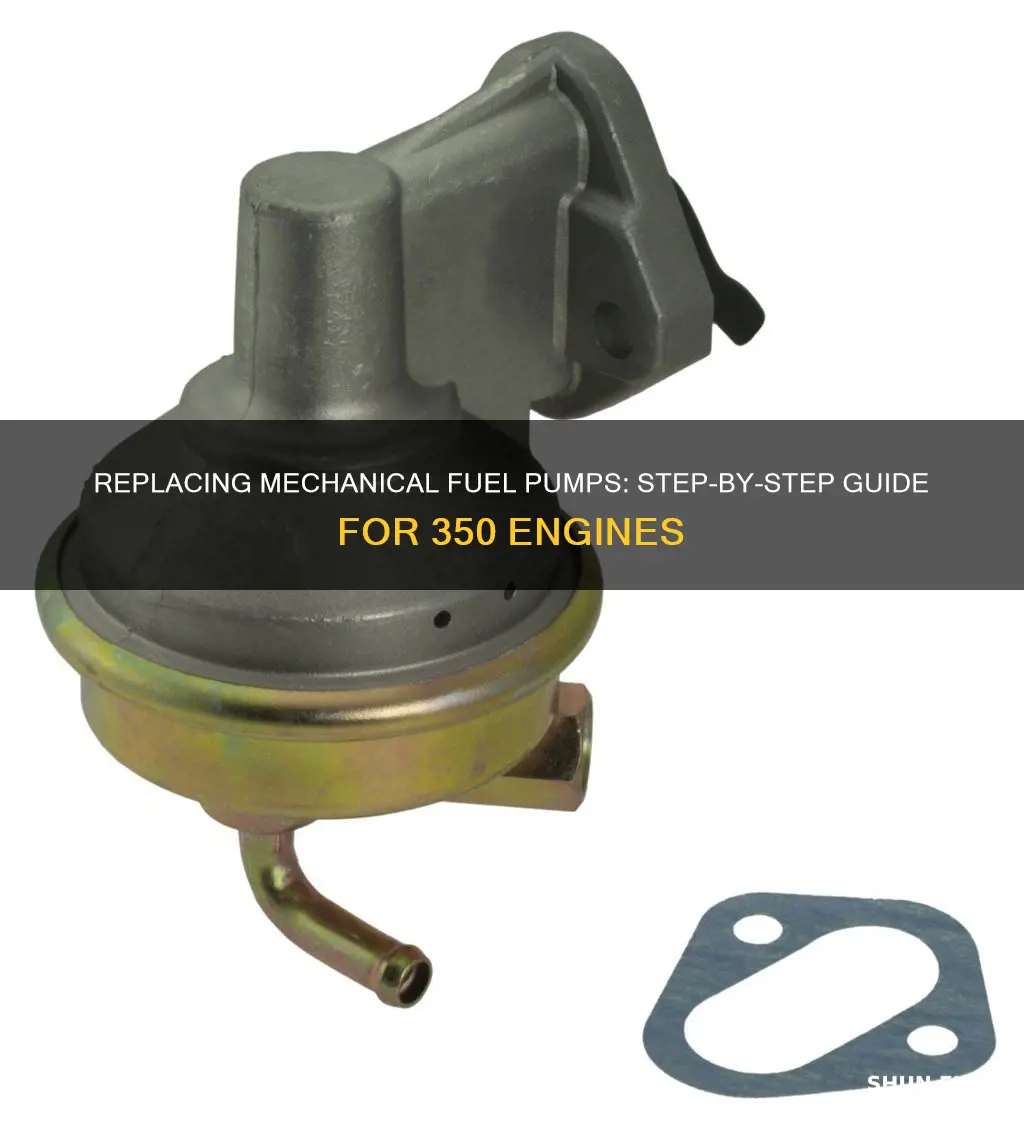
Replacing the mechanical fuel pump on a 350 engine is a complex job, but it can be done at home in about an hour or two. It is important to wear appropriate clothing and have the right tools, such as a ratchet wrench set, tubing, and a fire extinguisher. The process involves removing the old fuel pump by disconnecting the negative battery cable, fuel tank hose, and outlet line to the carburetor, as well as removing the attaching bolts and extracting the old pump. When installing the new pump, it is crucial to ensure the push rod is correctly installed and to attach the fuel lines and battery cable before starting the vehicle and checking for leaks.
What You'll Learn
Disconnect the negative battery cable
Disconnecting the negative battery cable is the first step in replacing a mechanical fuel pump. This is a crucial safety measure as it ensures that the power to the fuel pump is cut off before you start working. Here are some detailed instructions to guide you through the process:
Step 1: Prepare Your Workspace
Before you begin, make sure you have gathered all the necessary tools and turned off your vehicle. It is important to work in a well-ventilated area and avoid any open flames or sparks as you will be working around fuel and fuel vapors. Remember to dress appropriately as the task can be messy.
Step 2: Locate the Negative Battery Cable
The negative battery cable is usually black and is connected to the negative terminal of the battery, which is often marked with a "-" symbol. It is typically located on the driver's side of the vehicle, but this may vary depending on the car model.
Step 3: Disconnect the Cable
Once you have located the negative battery cable, you can proceed to disconnect it. Use a wrench or a ratchet to loosen the nut or bolt securing the cable to the battery terminal. Be careful not to drop the cable onto any metal parts of the car to avoid accidental electrical shorts.
Step 4: Secure the Cable
After disconnecting the cable, make sure to secure it safely away from the battery. You can use a cable tie or a piece of tape to hold it in place. This will prevent the cable from accidentally coming into contact with the battery during the fuel pump replacement process.
Step 5: Verify the Disconnection
To ensure that the negative battery cable is completely disconnected, you can use a multimeter to test for continuity between the cable and the battery terminal. Set the multimeter to measure resistance and touch one probe to the cable and the other to the terminal. If there is no continuity (infinite resistance), the cable is successfully disconnected.
Step 6: Proceed with Caution
Even with the negative battery cable disconnected, it is important to exercise caution. The fuel pump and lines may still contain fuel, so be prepared with a fire extinguisher and absorbents in case of spills or leaks. Always refer to your vehicle's repair manual for specific safety precautions and procedures.
By following these steps, you can safely disconnect the negative battery cable, ensuring a secure environment to proceed with the rest of the fuel pump replacement process. Remember to work carefully and methodically to avoid any potential hazards.
Replacing Fuel Pump on Cub Cadet: Step-by-Step Guide
You may want to see also
Remove the old fuel pump
To remove the old fuel pump, start by disconnecting the negative battery cable. Next, disconnect the fuel tank hose at the fuel pump and plug the hose with a bolt or wooden dowel to prevent fuel from flowing out. If your vehicle has one, also disconnect the vapor-return hose. Be sure to wipe up any spilled gas.
Disconnect the outlet line to the carburetor. Use a wrench on the fuel pump fitting and another on the line nut. Remove the two attaching bolts and extract the old fuel pump. Clean off any old gasket material from the mounting surface of the engine using a shop rag.
When removing the fuel pump, be aware that the push rod may fall or slide down behind the fuel pump backing plate. You can address this by putting the engine at top dead center 0 on the timing mark for #1 cylinder firing, which will put the fuel pump push rod at its most relaxed position with the least pressure on the pump lever. Alternatively, you can use a hacksaw blade to hold the pushrod up as you insert the mechanical pump arm.
Replacing the Fuel Pump in Your VE Commodore: Step-by-Step Guide
You may want to see also
Prepare and install the new fuel pump
Before you begin, ensure you are appropriately dressed for the task, as it can get messy. It is also important to work in a well-ventilated area and to avoid any activities that may cause sparks or safety hazards.
Once you have removed the old fuel pump, it is time to prepare and install the new one. Follow these steps:
- Apply a coat of gasket sealer to both sides of the new gasket.
- Put the attaching bolts through the new pump and slip the gasket over the bolts.
- Install the new pump on the engine, ensuring that the push rod is correctly installed in both the engine and the fuel pump. If needed, use some heavy grease to hold the push rod in place.
- Attach the fuel outlet line that runs to the carburetor. If it is difficult to connect, remove the other end of the line from the carburetor first. Connect the line to the fuel pump, and then reattach it to the carburetor. Use a wrench to tighten the line nut.
- Attach the fuel inlet hose from the gas tank and the vapor-return hose if your vehicle has one. Ensure all clamps are tightened.
- Reconnect the negative battery cable, start the vehicle, and check for any leaks. Ensure your work area is well-ventilated and free of any potential safety hazards.
Now that the new fuel pump is installed, you can inspect your work and ensure there are no leaks. Once you are satisfied, your vehicle is ready to go.
Replacing the Fuel Pump in Your 2010 Silverado: Step-by-Step Guide
You may want to see also
Attach the fuel outlet line
To attach the fuel outlet line, you will need to connect the line to the fuel pump. If you are finding it difficult to connect, you can remove the other end of the line from the carburettor. Once the line is connected to the fuel pump, reattach the other end to the carburettor. Use a wrench to hold the fuel pump fitting and tighten the line nut with another wrench.
When attaching the fuel outlet line, it is important to be aware of safety precautions. You will be working with fuel and fuel vapours, so ensure your workspace is well-ventilated. Do not smoke, use an open flame, or do anything that may cause sparks or present a safety hazard.
It is also important to dress appropriately when working with fuel. Wear clothes that cover your arms and legs, and consider using safety equipment such as gloves and eye protection.
Additionally, it is recommended to have a fire extinguisher rated for gasoline fires nearby in case of any accidents or spills. Always be cautious and careful when working with flammable liquids.
Once the fuel outlet line is securely attached, you can move on to the next step of reconnecting the battery ground cable and starting the vehicle to check for any leaks.
Replacing Fuel Pump in Trailblazer: Step-by-Step Guide
You may want to see also
Reconnect the battery ground cable
When reconnecting the battery ground cable, it is important to ensure that the connection is secure and well-maintained. Here are some detailed steps to follow for reconnecting the battery ground cable:
First, identify a suitable grounding location on the engine block. Look for a clean, paint-free metal surface or a designated grounding point. Some possible locations include an unused head bolt hole, the fuel pump cavity, or the alternator bracket. It is crucial to choose an area that is easily accessible and provides a direct connection to the battery ground cable.
Next, gather the necessary tools and materials. You will need a wire brush, sandpaper, antiseize or dielectric grease, a star washer, and a suitable bolt and nut for securing the connection. Ensure that the bolt size matches the selected grounding location.
Before making the connection, clean the grounding surface on the engine block. Use the wire brush and sandpaper to remove any paint, rust, or debris, creating a bright bare metal surface. This step ensures optimal conductivity and reduces the likelihood of corrosion.
Now, apply a small amount of antiseize or dielectric grease to the cleaned surface. This will enhance conductivity and provide additional protection against corrosion.
Place the star washer onto the bolt, followed by the battery ground cable eyelet or terminal. Secure the connection by tightening the bolt and nut assembly onto the chosen grounding location. Ensure that the connection is firm but be careful not to over-tighten, as this can damage the grounding surface.
Finally, inspect your work. Ensure that the battery ground cable is securely attached to the engine block and that there is good contact between the cable and the grounding surface. A poor connection can result in electrical issues and affect the performance of your vehicle.
By following these steps, you will help ensure that your battery ground cable is properly reconnected, providing a reliable electrical ground for your vehicle's systems.
Replacing Fuel Pump in Nissan Frontier: Step-by-Step Guide
You may want to see also