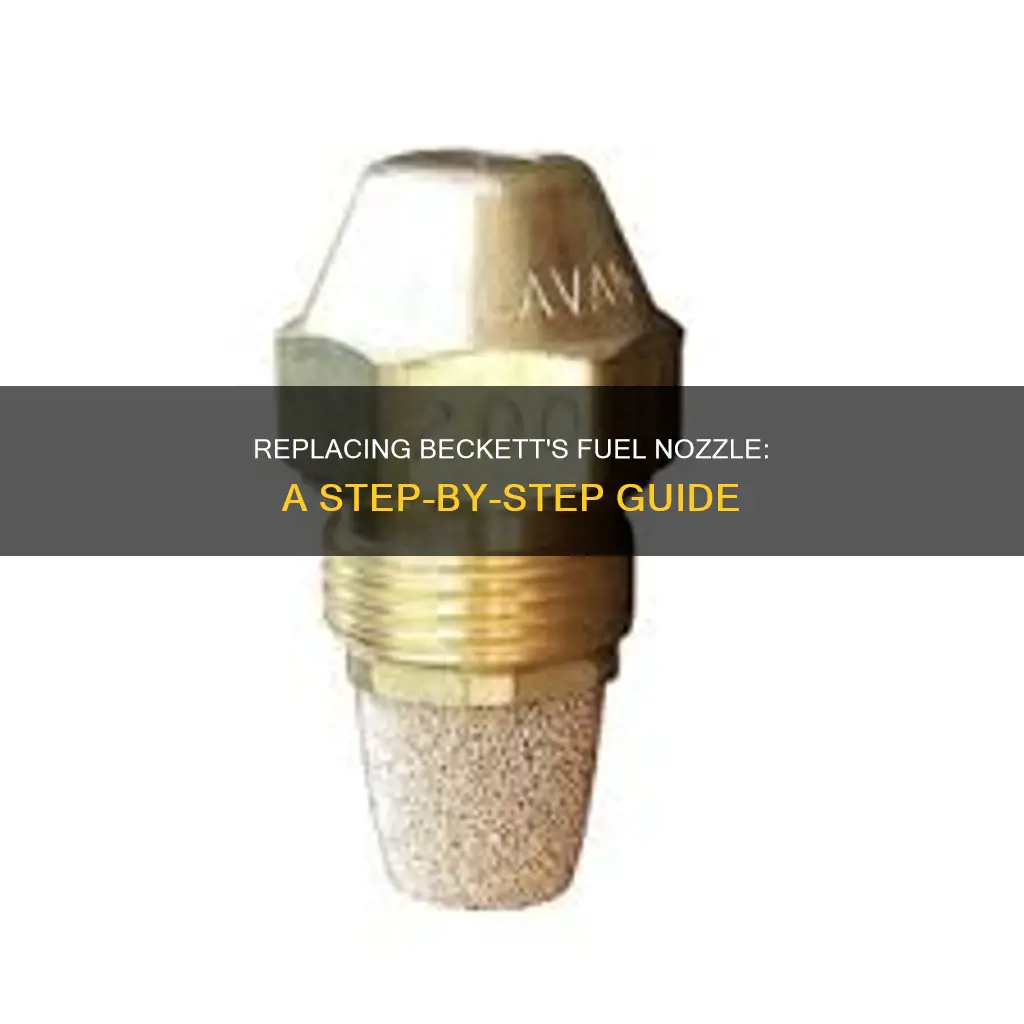
Replacing the fuel nozzle on a Beckett burner can be a little tricky. To replace the nozzle, you'll need to loosen the small oil line connecting to the drawer assembly, as the nozzle is at the end of this. Then, reach into the drawer assembly and pull it out. It's important to note that the nozzle orifice and strainer are vulnerable to damage, so care must be taken when installing the nozzle. Additionally, the nozzle adapter should be inspected and replaced if there are deep grooves from previous nozzles, as this can cause leaks.
Characteristics | Values |
---|---|
When to replace the fuel nozzle | When there is a blockage, a leak, or damage to the inside of the heater |
How to replace the fuel nozzle | Loosen the small oil line connecting to the drawer assembly, then reach in to drawer assembly and pull to the right, then up and out |
Where to buy a new fuel nozzle | Plumbing supply store |
What You'll Learn
How to identify the correct nozzle for your Beckett burner
When identifying the correct nozzle for your Beckett burner, there are several factors to consider. Firstly, it is important to refer to the manufacturer's specifications for the burner, which can usually be found on a sticker or data tag on the burner itself or in the instruction manual. This will provide information on the acceptable nozzle size range, spray angle, and spray pattern type recommended for your specific burner model.
The nozzle size, also known as the metering rate or firing rate, is typically expressed in gallons per hour (GPH) and indicates the capacity of the burner to deliver heating oil. It is important to select a nozzle with the correct size to ensure proper burner operation.
The spray angle of the nozzle should also match the shape and length of the combustion chamber. A narrower spray angle, such as 30° to 60°, is typically used with a longer and deeper combustion chamber, while a wider spray angle, such as 70° to 90°, is used with a shorter or smaller combustion chamber to prevent flame impingement on the chamber walls.
In addition to the spray angle, the spray pattern type of the nozzle should also be considered. The two most common spray pattern types are hollow cone (Type A) and solid cone (Type B). The hollow cone pattern has a hollow core with fewer droplets, while the solid cone pattern has a more uniform distribution of droplets throughout the spray. The correct spray pattern type will depend on the air flow pattern of the burner and the manufacturer's recommendations.
When selecting a replacement nozzle, it is generally best to choose one with the same size, spray angle, and spray pattern as the original nozzle. However, in some cases, substitutions may be made, such as changing from a hollow cone to a solid cone pattern or vice versa, as long as the other parameters remain the same. It is important to refer to the manufacturer's specifications and guidelines when making any substitutions.
Finally, it is important to ensure that the nozzle is properly installed and adjusted. This includes making sure the fuel supplied to the nozzle is clean and free of air, setting the pump pressure correctly, and protecting the nozzle orifice and strainer from dirt or scratches.
Replacing the Fuel System in Your '06 Malibu
You may want to see also
How to remove the old nozzle
Removing the old nozzle from your Beckett burner is a simple process, but it requires careful handling to avoid damage. Here is a step-by-step guide on how to remove the old nozzle:
- Turn off the burner and allow it to cool down: Before beginning any work on your burner, ensure that it is turned off and given sufficient time to cool down. This step is crucial for safety reasons and to prevent any damage from working on a hot burner.
- Locate the ignition transformer: The ignition transformer is usually hinged and facing you. It may be necessary to remove any screws or loosen slide brackets at the back to access it.
- Loosen or remove the screws holding the ignition transformer in place: By loosening or removing these screws, you will be able to swing open the ignition transformer towards you, providing access to the underlying components.
- Locate the small oil line connecting to the drawer assembly: The nozzle is located at the end of this oil line, which connects to the drawer assembly.
- Loosen the small oil line: Use the appropriate tool to loosen the connection between the small oil line and the drawer assembly. This will allow you to access the nozzle for removal.
- Reach into the drawer assembly and carefully pull the nozzle out: Grip the nozzle firmly but gently to avoid damage and pull it out to the right, then up and out of the drawer assembly.
- Inspect the nozzle and surrounding components: Once the nozzle is removed, take the opportunity to inspect it and the surrounding components for any signs of damage, wear, or debris buildup. This will help you determine if any additional cleaning or maintenance is needed.
- Clean the area: If there is any debris or residue buildup, use a suitable cleaning solution and a soft cloth or brush to clean the area. Ensure that you do not leave any residue or cleaning solution behind, as it could affect the performance of your burner.
- Prepare the new nozzle for installation: Refer to the instructions that came with your new nozzle to ensure that you have the correct replacement and that it is properly prepared for installation.
Remember to work carefully and methodically when performing these steps to avoid any damage to your burner or its components. If you encounter any issues or complications, it is recommended to consult a professional technician for assistance.
The Right Time to Replace Your Fuel Filter
You may want to see also
How to install the new nozzle
Before installing the new nozzle, it is important to ensure that the fuel supplied to it is clean and free of air. Check the pump pressure and set it to the correct value, which is typically between 100 and 150 PSIG for domestic applications. When installing the nozzle, use extreme care to protect the nozzle orifice and strainer, as any dirt or scratches will impact its function.
Inspect the nozzle adapter for any deep grooves or scratches from previous nozzles, and replace it if necessary. Do not overtighten the nozzle, as this can cut grooves into the adapter and cause leaks.
When replacing the nozzle, it is recommended to bring the old one to a plumbing supply store to ensure you get the correct replacement. Nozzles have three important settings: the degree of spray, type of spray, and the amount of fuel per hour. Using the wrong nozzle can impact the spray pattern and cause damage to the inside of the heater.
The installation process for a new nozzle is as follows:
- Pour clean oil into the nozzle adapter while blocking the rear nozzle tube fitting.
- Install the new nozzle securely, but do not overtighten.
- Insert the assembly into the burner.
- Connect the pump discharge connector tube.
Additional Considerations
- Make sure the burner is installed with a downward pitch to prevent oil from running back and dripping onto the floor.
- If you are using a Beckett burner, it will have a built-in air vent plug inserted into the nozzle tube to prevent air entrapment.
- To prevent afterdrip, line an old refractory with a modern cerafelt or ceramic chamber liner to reduce radiation and lower "soak" temperatures.
- Wrap a sleeve of cerafelt around the last few inches of the air tube to reduce nozzle temperatures.
- Ensure the burner is level to maintain the built-in downward pitch.
- Apply a high-temperature silicone rubber to the air tube/burner chassis junction to prevent oil from escaping.
Troubleshooting
If you encounter issues with the burner not firing, check the following:
- Ensure the eye is set correctly and not blocked.
- Verify that the transformer is making strong contact.
- Adjust the electrodes and bleed the line if necessary.
Best Marine Fuel Lines: Which Brand Replaces Better?
You may want to see also
How to prevent afterdrip
Afterdrip is a common issue with burners. To prevent afterdrip, you can try the following:
- Ensure the burner is installed with a downward pitch so that any afterdrip will run into the chamber and burn away during the next cycle.
- Check for a leaking pump shaft seal, dripping nozzle line, poor nozzle pattern, or impingement.
- Check for air in the oil lines or oil hitting the flame cone and running out.
- Use a high-temperature silicone rubber, such as 732 RTV Silastic by Dow Corning, on the air tube/burner chassis junction to prevent oil from finding an escape route.
- Make sure the burner is level and the appliance mounting plate is true to prevent oil from migrating uphill.
- Check the pump shut-off valve, as a defective one can cause afterdrip.
- Ensure oil supply lines are properly installed according to the pump manufacturer's specifications to prevent air from getting trapped in the nozzle line or adapter.
- When changing the nozzle, pour clean oil into the nozzle adapter while holding your thumb over the rear nozzle tube fitting. Install the nozzle securely without over-tightening, then insert the assembly into the burner and connect the pump discharge connector tube.
- Line an old refractory with a modern cerafelt or ceramic chamber liner to reduce radiation and lower the temperature rise that causes oil expansion and afterdrip.
- Wrap a sleeve of cerafelt around the last few inches of the air tube up to the combustion head to reduce nozzle temperatures and afterdrip.
- Ensure the nozzle orifice and strainer are protected during installation, as dirt or scratches can impact performance.
- Inspect the nozzle adapter before installing the nozzle, replacing it if there are deep grooves that could cause leaks.
- Do not over-torque the nozzle when tightening to avoid cutting grooves into the adapter, which can cause leaks.
Craftsman Weedwacker: Replacing the Fuel Line
You may want to see also
How to ensure the correct pump pressure
Ensuring the correct pump pressure is crucial for optimal performance and safety when using a Beckett fuel nozzle. Here are some detailed instructions to help you achieve and maintain the correct pump pressure:
Understand the Recommended Pump Pressure Range:
Before adjusting the pump pressure, it is essential to know the recommended pressure range for your specific Beckett fuel nozzle. For domestic applications, the pump pressure is typically set within the range of 100 PSIG to 150 PSIG. However, it's important to refer to the manufacturer's specifications for your particular model.
Install a Reliable Pressure Gauge:
To accurately measure the pump pressure, install a reliable pressure gauge in the nozzle discharge port of the fuel unit. Choose a gauge with an appropriate pressure range, such as 0-150 PSI, to ensure accurate readings. Ensure that all threaded joints are adequately sealed and tight to prevent leaks.
Test and Adjust the Pump Pressure:
Start the burner and let it run through a complete cycle. When the burner locks out, observe the pressure gauge. The pressure should drop from the operating level to approximately 20% less but remain substantially above 0 PSIG. If the pressure fails to stabilize and slowly drops to 0 PSIG, check the gauge fittings for any leaks. If no leaks are found, you may need to replace the pump.
Prevent Air Entrapment:
Air trapped in the nozzle line or adapter can cause afterdrip issues. To prevent this, ensure that the oil supply lines are properly installed according to the pump manufacturer's specifications. Use good-quality flare fittings, but keep their number to a minimum. If you suspect a leak, perform a thorough pressure or vacuum test on the piping. Leak-free oil lines will ensure clear and bubble-free oil delivery to the nozzle.
Maintain Clean and Air-Free Fuel:
It is crucial to supply the nozzle with clean and air-free fuel. Check the oil supply lines for any signs of froth or minute bubbles, either at the nozzle discharge tube or the bleed port. Additionally, always protect the nozzle orifice and strainer during installation, as a dirty or scratched orifice will affect the nozzle's performance.
Regularly Service the Pump Strainer:
Routine maintenance of the pump strainer is essential. Remove the pump cover and clean the strainer using a brush and clean fuel oil or kerosene. Replace the cover gasket with a new one, and ensure that the four cover screws are tightened evenly.
By following these detailed instructions, you can ensure that your Beckett fuel nozzle operates at the correct pump pressure, providing efficient and safe performance.
Replacing Fuel Lines in Your 2008 GMC Acadia
You may want to see also
Frequently asked questions
If your burner is experiencing afterdrip, a blocked nozzle could be the cause. Other signs include a burner that won't fire, a poor spray pattern, or damage to the inside of your heater.
Refer to the appliance manufacturer's nozzle specifications and burner manufacturer's recommendations. Make sure to set up the combustion with properly maintained test instruments.
First, consult your burner's manual and gather the necessary tools and parts. You may need to loosen screws, remove oil lines, and detach the nozzle assembly. Clean the nozzle area and install the new nozzle securely, without over-tightening.
Yes, it is important to protect the nozzle orifice and strainer during installation. Avoid over-tightening the nozzle to prevent damage to the adapter and leaks. Ensure the pump pressure is set correctly and use a combustion analyzer to fine-tune the burner after the replacement.