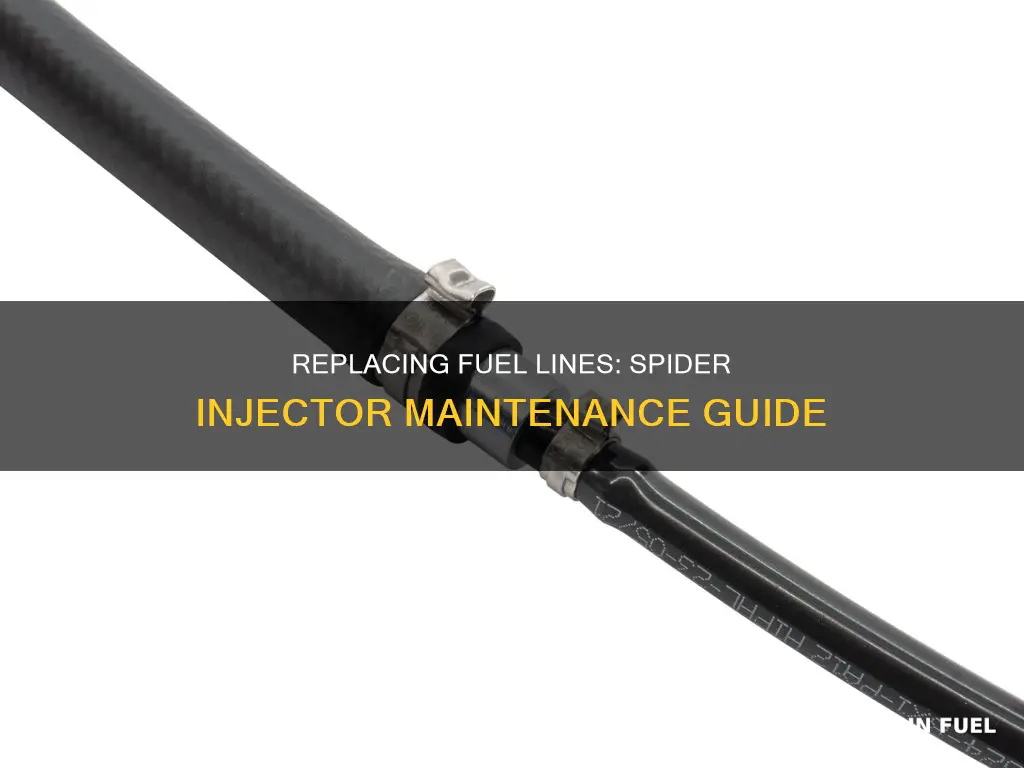
Replacing the fuel lines on a spider injector is a complex task that requires careful attention to detail and a good understanding of engine mechanics. Online forums suggest that it can take anywhere from one to nine hours to complete the job, depending on skill level and experience. It is also important to have the right tools, such as a line wrench for removing the fuel rail, and to take safety precautions when working with fuel systems. Before beginning the replacement, it is recommended to consult a step-by-step guide or video tutorial to familiarise oneself with the process.
What You'll Learn
Check for leaks and faulty O-rings
When checking for leaks and faulty O-rings, it is important to take precautions to prevent any health and safety risks. Do not smoke while performing the work, and park your vehicle outside to prevent the accumulation of dangerous fumes. If your clothes become fuel-soaked, change them immediately, and wash any contacted skin with mild soap and plenty of fresh water.
To begin, raise the vehicle and support it on jack stands. Using a flashlight, carefully trace the fuel lines from the tank to the engine, looking for any signs of leaks. Keep an eye out for spots with an accumulation of dust and road grime, wet spots or streaks, and clean spots where the fuel may have washed away all the grime. If you notice any dripping, follow the structural component to discover the source of the leak. Remember that gravity and wind pressure can affect the path of travel, so the fuel may be running along a series of members before dripping out.
If you are unable to locate the leak through a visual inspection, there are specialised products that can help. These products contain a dye that is added to the fuel and will glow under fluorescent or ultraviolet light. Run the engine to leak some of the treated fuel, then perform another visual inspection with a handheld light. Alternatively, you can use a leak detector, which has a probe that can be inserted into areas that aren't readily visible.
If you suspect that the O-rings are faulty, you will need to inspect them. Fuel injector O-rings are small, circular seals typically made from nitrile or Viton, placed between the fuel injector and the fuel rail. Over time, these O-rings can become brittle, hard, and cracked, leading to fuel leaks and engine problems. Check that the O-rings are in place and inspect them for any signs of damage or wear. If they appear compromised, they will need to be replaced.
When selecting replacement O-rings, it is important to choose the right material for your specific fuel type and operating conditions. Viton O-rings, for example, offer excellent resistance to a wide range of chemicals and have a broad temperature tolerance, making them ideal for high-temperature environments. On the other hand, Nitrile O-rings are more cost-effective and provide good resistance to oils and some fuels but may falter in extreme temperatures.
Lawn Mower Fuel Filter: Replacing and Troubleshooting Guide
You may want to see also
Clean, lubricate, and replace O-rings
To clean, lubricate, and replace O-rings on a spider injector, follow these steps:
Firstly, it is important to gather the necessary materials and take the following preparatory steps: ensure you are working in a well-ventilated area and wear appropriate safety gear, including gloves and eye protection. Disconnect the battery to prevent electrical shocks while working on the fuel system. Locate the fuel injectors on your engine—they are typically mounted on the intake manifold. Before removing the injector, clean the area around it using a clean cloth and a degreaser to prevent dirt and debris from contaminating the O-rings.
Now, gently remove the fuel injector from the manifold, being careful not to damage the injector or its wiring. Inspect the O-rings for any signs of damage, such as cracks, tears, or excessive wear. If the O-rings are damaged, you should replace them. Clean the O-rings and lubricate them with a fuel-compatible lubricant. You can use a clean cloth or a small brush to apply a thin layer of lubricant to both sides of each O-ring. Reinstall the injector, ensuring that the O-rings are properly seated, and reconnect the battery.
To maintain your fuel injector O-rings, you should periodically inspect them for signs of wear or damage, keep your fuel system clean by using a fuel system cleaner, and use high-quality fuel to minimise the buildup of deposits. If you notice any issues with the O-rings, such as fuel leaks, rough idling, decreased fuel efficiency, or a decrease in engine power, replace them as soon as possible.
When choosing a lubricant, opt for a reputable brand of silicone-based lubricant that is specifically designed for fuel systems. Avoid using WD-40, motor oil, or silicone grease, as these can be unsuitable or even cause damage.
Fuel Injection: The Evolution Beyond Carburetors
You may want to see also
Tools required: deep socket, wrenches, screwdriver, pliers, gloves, light
Replacing the fuel lines on a spider injector can be a challenging task, but with the right tools and precautions, it can be accomplished safely and effectively. Here is a detailed guide on the tools required for the job:
Deep Socket: A deep socket, preferably a deep 10mm socket, is essential for reaching and manipulating the bolts and fittings in tight and confined spaces around the spider injector.
Wrenches: An assortment of wrenches, including both metric and standard sizes, will be needed to loosen and tighten various connections and fittings associated with the fuel lines and spider injector.
Screwdriver: A flat-tip or flat-blade screwdriver is useful for prying, lifting, and adjusting various components during the disassembly and reassembly process.
Pliers: Needle-nose pliers or long-nose pliers are handy for grasping and manipulating small objects, wires, or hoses. They can also assist in reaching tight spaces.
Gloves: Fuel-resistant gloves are crucial for protecting your hands from fuel exposure and ensuring a safe working environment.
Light: A good light source, such as a flashlight or a well-lit workspace, is essential for illuminating the engine bay and undercarriage of the vehicle, allowing you to see clearly during the replacement process.
In addition to these tools, it is important to have a fire extinguisher nearby as a safety precaution when working with the fuel system. Before beginning any work, always disconnect the battery to prevent electrical short circuits or sparks that could ignite fuel vapors.
Algae Biofuels: The Green Alternative to Fossil Fuels
You may want to see also
Disconnect fuel lines and AC compressor
Disconnecting the fuel lines and AC compressor is a complex task that requires careful attention to detail. Here is a step-by-step guide to help you through the process:
Locate the AC compressor and fuel lines
The AC compressor is typically located at the front of the engine, along with the other belt-driven accessories. Identify the fuel lines that need to be disconnected; these will be connected to the spider injector.
Prepare the necessary tools and safety equipment
Before beginning any work, ensure you have the correct tools and safety equipment. This includes wearing protective gloves and safety glasses. You will also need a socket or wrench, a ratchet, and possibly a screwdriver.
Locate and adjust the serpentine belt tensioner
Find the serpentine belt tensioner; if you are having trouble locating it, refer to the belt routing diagram or vehicle repair manual. Use the socket or wrench to rotate the tensioner and slide it away from the belt. The direction you rotate it will depend on your vehicle and belt routing. Some tensioners have a square hole for a ratchet, rather than a bolt head.
Remove the belt from the pulleys
Hold the tensioner away from the belt and carefully slide the belt off the pulleys.
Disconnect the electrical connectors
Disconnect the electrical connectors from the compressor. These should pull out easily.
Disconnect the pressure hoses
Using a ratchet or wrench, disconnect the pressure hoses from the compressor. Be sure to plug the hoses to prevent system contamination.
Remove the compressor mounting bolts
With a ratchet or wrench, remove the bolts that secure the compressor in place.
Remove the compressor
The compressor may be heavy, so carefully tug it out of its housing.
Prepare the new compressor
Compare the new compressor to the old one to ensure they are the same. Remove the dust caps and add the recommended lubricant (usually around 1/2 ounce of PAG oil, but check your vehicle's specifications). Some compressors come with oil already installed, so check the instructions.
Replace the pressure line O-rings
Use a small screwdriver or pick to remove the O-rings from the AC pressure lines, and replace them with new ones. These may come with the new compressor, or you can purchase them from an auto parts store.
At this stage, the AC compressor has been successfully disconnected, and you can now install the new compressor by following the above steps in reverse.
As for the fuel lines, there are various types of fuel line connectors, and the process for disconnecting them will depend on the type you have:
- Push-type connector: Push-type connectors may have a push point on both sides, requiring you to push from both directions to release. Others may have a push point on only one side; simply push it down and pull it off.
- Push-and-lock style connector: Push this type of connector onto the fitting, then push the locking tab through. To remove, release the safety latch and push the connector back through.
- Pinch-type connector: This type has retainers on each side; pinch these together to disconnect.
- Spring-style retainer fitting: To remove, pull back on the black ring (the release tool) and then pull the fitting off.
- Hose and clamp-style fitting: Typically used for emissions lines. Use pliers to pinch the clamp together, slide it back, and then pull the line off.
- Horseshoe-type fitting: Held onto the fitting with a clip. Use a screwdriver to pull the horseshoe up and out.
By following these steps, you can successfully disconnect the fuel lines and AC compressor, allowing you to replace the spider injector and complete necessary maintenance or repairs.
Replacing the Fuel Pump in a 2000 Yukon: Step-by-Step Guide
You may want to see also
Re-install fuel lines
To re-install the fuel lines, first thread the fuel lines by hand until you cannot get them to go any further. Then, push the fuel lines into the spider and install the clamp and nuts. Lightly oil the metal tubes before installing.
Start the bolt into the lower intake for the line bracket and thread it almost all the way down, but still a little loose. Tighten the fuel lines by hand using a crow's foot. Tighten the bracket and then finish tightening the fuel line with the crow's foot and ratchet.
Make sure you firmly lock the poppet nozzles into place. Also, ensure that the poppet nozzles are properly seated to reduce the risk of fire or injury.
Replacing the Fuel Tank Vent Valve in a 2007 Tahoe
You may want to see also
Frequently asked questions
To replace the fuel lines on a spider injector, you will need to remove the old lines, clean the area, and then install the new lines. You may also need to replace the O-rings and apply lubricant to ensure a tight seal.
Replacing a spider injector typically takes between 1 and 6 hours, depending on your level of expertise and the tools you have available.
Some common issues with spider injectors include leaks, clogged or stuck valves, and idle issues after replacement.