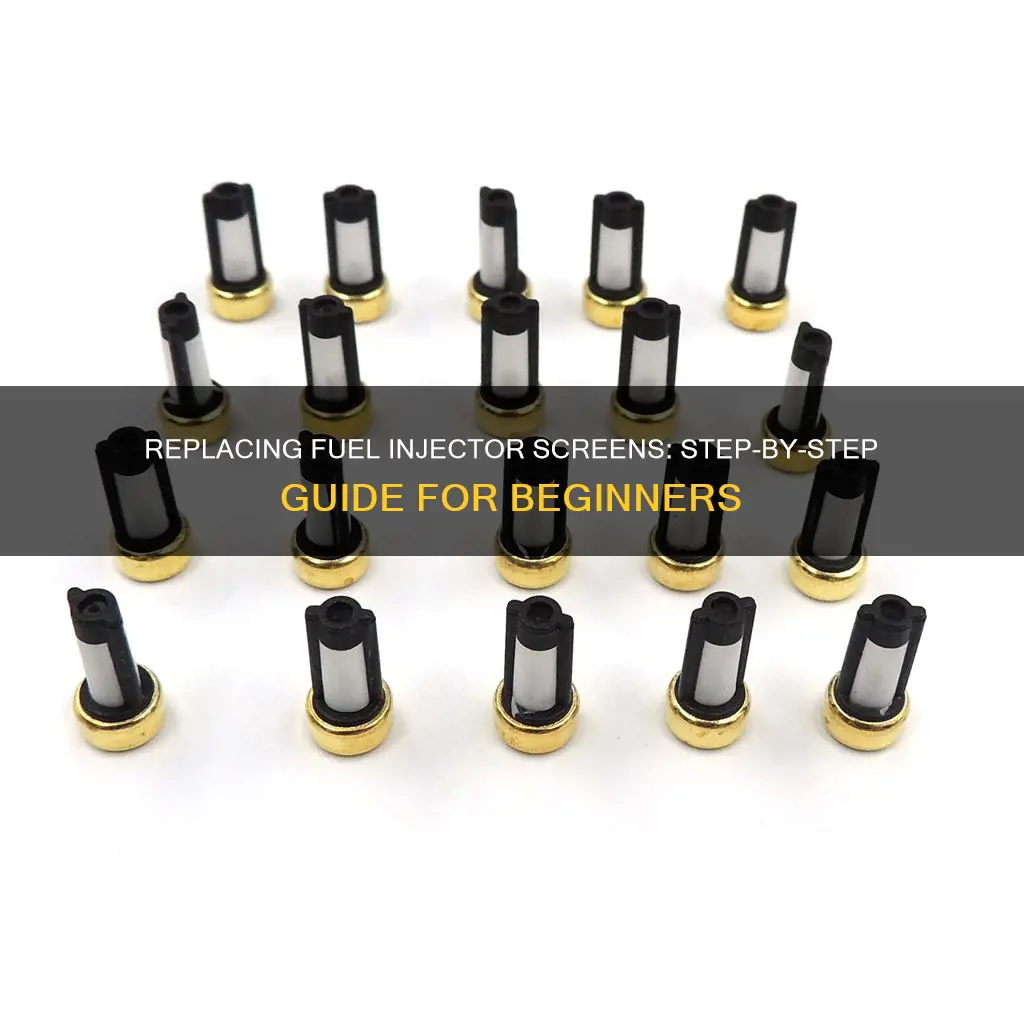
Fuel injectors are designed to deliver fuel into an engine's cylinders at precise moments and in the correct quantities to ensure optimal combustion. They are small electric valves that are fitted between the fuel rail and the intake manifold, combustion chamber, or throttle body (in older cars). While fuel injectors are designed to be incredibly long-lasting, there may come a time when one of them develops an issue that can only be solved by replacing it. This could be due to external leaks, clogged debris, or carbon deposits on the nozzle that can't be cleaned. Before replacing a fuel injector, it is important to disconnect the battery and let the engine cool completely. It is also crucial to wear safety glasses and gloves and have a fire extinguisher within reach.
What You'll Learn
Disconnect the electrical connector
Disconnecting the electrical connector from a fuel injector can be a tricky task, but it is doable with the right tools and techniques. Here is a step-by-step guide to help you through the process:
Step 1: Prepare Your Tools
Before beginning, ensure you have the necessary tools on hand. You will need a small flat-head screwdriver, a small pick or needle-nose pliers, and a dental pick or small sheet metal screw (optional). Having these tools ready will make the process smoother.
Step 2: Access the Fuel Injector
Locate the fuel injector and its electrical connector. In some cases, you may need to remove the fuel rail or other components for better access. This will give you more room to work on disconnecting the electrical connector.
Step 3: Understand the Connector Mechanism
The electrical connector is typically secured by a metal clip or a wire retainer. Observe how the clip or retainer is positioned and fastened. Some connectors have a release button, while others require manipulating the clip to release the connector. Understanding the mechanism will help you disconnect it effectively.
Step 4: Release the Connector
Now, it's time to disconnect the electrical connector. If there is a release button, simply press it to detach the connector. If there is a metal clip, use the small flat-head screwdriver to carefully pry or push it outwards. You may need to do this on both sides of the connector. Alternatively, if there is a wire retainer, squeeze the connector and the injector together while pulling them apart. In some cases, you can also push the wire clip in while pulling the connector upwards.
Step 5: Work Carefully
Throughout the process, be cautious and gentle to avoid damaging the electrical connector or any surrounding components. It is crucial to work with precision to prevent any accidental breakage. If you encounter resistance or if the connector seems stuck, double-check your technique and ensure you are using the correct tools.
Step 6: Seek Alternate Methods
If you are having difficulty, there may be alternate methods to disconnect the electrical connector. For example, some people suggest using a small pick or needle-nose pliers to carefully release the clip or retainer. Others have mentioned soldering as a possible solution. Always research and understand the potential risks and benefits of any alternative approach before proceeding.
Step 7: Reinstallation
When it comes time to reconnect the electrical connector, first ensure that the metal clip or retainer is in place. Then, simply push the connector back onto the injector until you hear a click, indicating that it is securely fastened.
Remember, always refer to your vehicle's service manual for specific instructions and safety precautions. Taking your time and working carefully will help ensure a successful and safe disconnection of the fuel injector's electrical connector.
The Future of Energy: Sustainable Alternatives to Fossil Fuels
You may want to see also
Remove the fuel rail mounting bolts
To remove the fuel rail mounting bolts, you will need to locate the bolts on the fuel rail. There are typically two or three mounting bolts that hold the fuel rail in place. Using a wrench or socket, loosen and remove the bolts. Be careful not to overtighten the bolts as they can snap. If the bolt snaps, you may need to drill it out or use a left-handed bit or needle-nose pliers to remove the broken piece.
Once the mounting bolts are removed, you can lift the fuel rail away from the injectors. Be careful not to damage the injectors or any other components. Place the fuel rail in a safe location, as you will need to access it later when installing the new fuel injector screen.
Before removing the fuel injector, it is important to relieve the fuel system pressure and disconnect the negative battery terminal. This will help prevent any accidental spills or injuries. It is also recommended to wear safety goggles and gloves during this process to protect your eyes and hands.
When you are ready to install the new fuel injector screen, simply reverse the removal process. Reattach the fuel rail using the mounting bolts and tighten them securely, but be careful not to overtighten. Reconnect the negative battery terminal and start the engine to check for any leaks.
It is important to note that working on fuel injectors can be dangerous if not done properly. If you are unsure about any part of the process, it is always best to consult a professional mechanic.
G Fuel: Healthy Energy Drink Alternative?
You may want to see also
Take out the retainer clip
To take out the retainer clip, you will need to carefully follow these steps to ensure you do not damage the fuel injector or the retainer clip. First, you will need to locate the retainer clip. It is important to note that there are two types of retainer clips: one for the fuel side of the injector and another for the electrical side. Make sure you identify the correct one.
Once you have located the retainer clip, use a suitable tool to gently pry it out. You can use a flat-head screwdriver or a similar tool to carefully lift the clip out of its housing. Be very careful not to apply too much force, as you may damage the clip or the injector. It is recommended to use a tool with a flat and thin edge to reduce the risk of damage.
After successfully removing the retainer clip, set it aside in a safe place to avoid misplacing or losing it. At this point, you can proceed with the next steps in replacing the fuel injector screen. Remember to work carefully and patiently to avoid any accidental damage to the components.
If you are installing a new retainer clip, ensure that it is securely in place before proceeding. A loose or improperly installed retainer clip can cause issues, so take your time and ensure it is correctly positioned and fastened. Additionally, it is always a good idea to refer to the manufacturer's instructions or seek guidance from a qualified mechanic if you are unsure about any steps in the process.
Replacing the MFI Fuel Pump in Your 1988 Ford F150
You may want to see also
Check the old fuel injector
To check the old fuel injector, you can start by locating the fuel injectors in your vehicle. These are usually found on the intake manifold, connected to one another with a fuel rail. Once you've located the injectors, you can use a long metal rod or screwdriver to listen for any clicking sounds, which indicate that the injector is functioning. This can be done by placing one end of the rod or screwdriver on the injector and bringing your ear close to the other end. It is important to be careful and keep your eyes open while leaning into the engine bay.
Another way to check the old fuel injector is to use a test light to check the voltage of the wires connected to the injector. First, locate the two wires going into each injector. One of these wires should be a 12-volt constant that is continuously receiving power. Then, use the test light to penetrate the rubber coating around each wire and see if the light turns on. If the test light turns on with one wire, the injector is receiving power. If neither wire makes the light turn on, there may be an issue with the power reaching the injector.
Additionally, you can perform a leak test by starting the engine and letting it idle for a few minutes. Shine a flashlight under the hood and look for any leaking gas or smell for gasoline. If you notice any leaks, the fuel injector may need to be replaced.
Finally, you can use an OBD2 scanner to check for any trouble codes or real-time data that indicates fuel injector issues. This method requires a compatible scanner and a vehicle equipped with an OBD2 port, typically found under the dashboard. By connecting the scanner and accessing the "Live Data" or "Data Stream" menu, you can monitor parameters such as fuel trim, injector pulse width, and cylinder misfire data to identify any deviations that signal injector problems.
Replacing Weed Eater Fuel Lines: A Step-by-Step Guide
You may want to see also
Lubricate the new injector's O-rings
Lubricating the new injector O-rings is a crucial step in the process of replacing a fuel injector screen. It is essential to never install the O-rings dry, as this can lead to potential issues. There are a variety of lubricants that can be used, each with its own advantages and considerations. Here is a detailed guide on how to effectively lubricate the new injector O-rings:
Firstly, it is important to select an appropriate lubricant. Common options include engine oil, grease, vaseline, silicone-based lubricants, and gasoline. It is recommended to refer to the manufacturer's service manual for specific recommendations. For example, some manuals suggest using fresh engine oil or dipping the O-rings in gasoline before installation. Silicone-based lubricants, such as dielectric grease or silicone spray, are often preferred by mechanics as they are safe to use near combustion chambers and will not react with the rubber O-rings. However, it is crucial to avoid using silicone near openings that lead to the combustion chambers, throttle body, injector openings, or vacuum ports, as it can damage the catalytic converter.
When lubricating the O-rings, it is important to apply a light coat or a small amount of the chosen lubricant. Excessive lubrication can lead to over-lubrication, which may cause dripping or other issues. For example, when using vaseline, it is crucial to use a small amount and ensure it is not overdone. This is because vaseline is a petroleum-based product, and while it can be effective, there is a risk of swelling and softening the rubber O-rings, leading to potential failure. Therefore, it is generally recommended to use silicone-based grease instead of vaseline for O-ring lubrication.
Additionally, it is worth noting that WD-40 can be useful for removing old O-rings. Its lubricating properties can help loosen and remove the old O-rings without causing damage. However, it should not be used as a lubricant for new O-rings, as it is not a long-lasting solution and may not provide sufficient lubrication.
In summary, when lubricating the new injector O-rings, it is essential to select an appropriate lubricant, apply it sparingly, and avoid over-lubrication. By following these steps and referring to the manufacturer's recommendations, you can effectively lubricate the new injector O-rings and ensure a smooth installation process.
Fuel Pump Replacement: When is the Right Time?
You may want to see also
Frequently asked questions
Use a dental pick, a small sheet metal screw, or a drywall screw to carefully pull out the screen. Be gentle to avoid damaging anything.
If your fuel injector screen is dirty, you should replace it. Dirty screens can cause issues like a rough idle, misfire, poor fuel efficiency, and trouble starting the engine.
Wear safety glasses and gloves, and avoid getting fuel on your skin. Have a fire extinguisher within reach and work in a well-ventilated area to avoid inhaling fumes.
You will need a dental pick or a small standard screwdriver. If you are replacing the entire fuel injector, you will also need a line wrench, shop towels, a small standard screwdriver or pick, and clean engine oil.