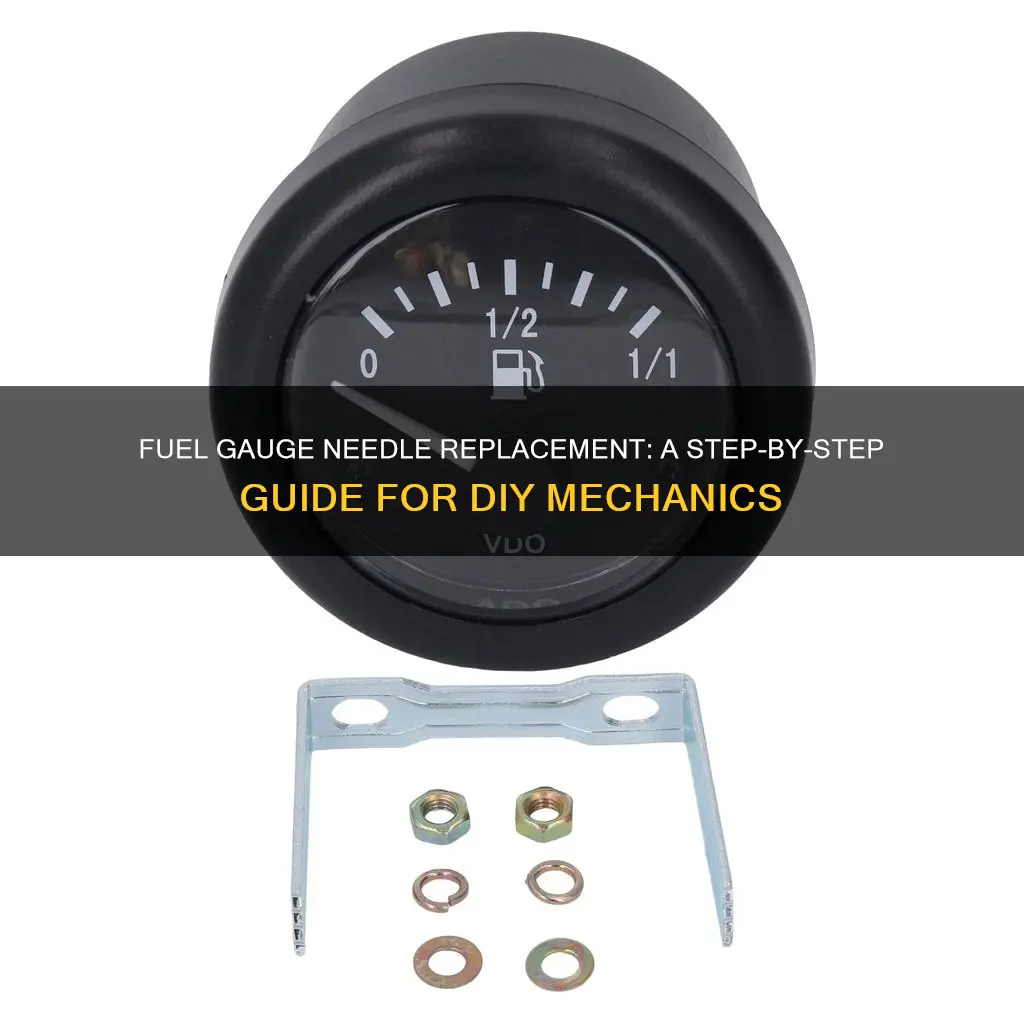
Replacing a fuel gauge needle is a relatively simple task that can be accomplished with basic automotive knowledge and tools. This guide will provide a step-by-step process to replace the fuel gauge needle in your vehicle, ensuring you have the necessary information to complete the job safely and effectively. By following these instructions, you can restore the functionality of your fuel gauge and ensure accurate fuel level readings.
What You'll Learn
- Fuel Gauge Basics: Understand gauge function, location, and wiring
- Needle Replacement: Remove old needle, install new one securely
- Wiring Connections: Identify and reconnect gauge wiring correctly
- Testing: Verify gauge accuracy post-replacement with a test tool
- Safety Precautions: Wear gloves, work in a well-ventilated area, and follow safety guidelines
Fuel Gauge Basics: Understand gauge function, location, and wiring
The fuel gauge is an essential component of your vehicle's dashboard, providing a visual indication of the fuel level in your tank. Understanding its function, location, and wiring is crucial for both maintenance and troubleshooting. Here's a breakdown to help you grasp the basics:
Function: The primary role of the fuel gauge is to inform the driver about the remaining fuel in the tank. It does this through a needle that moves along a scale, typically from 'empty' to 'full'. This gauge is designed to be a reliable indicator, ensuring you never run out of fuel unexpectedly. Modern vehicles often incorporate additional features, such as warning lights or digital displays, to provide more detailed information about fuel levels and potential issues.
Location: Fuel gauges are usually located in the center of the dashboard, often alongside other critical instruments like the speedometer and tachometer. Their placement is strategic to ensure easy visibility for the driver. The gauge is typically connected to the fuel tank via a series of hoses and wiring, allowing it to accurately measure the fuel level. In some vehicles, the fuel gauge may be integrated into the dashboard cluster, making it a seamless part of the overall design.
Wiring and Connections: The wiring for the fuel gauge is an intricate network of cables and connectors. It starts at the fuel tank, where sensors measure the fuel level and send this information to the gauge. The wiring harness typically includes a fuel level sensor, a sending unit, and a gauge wiring harness. The sending unit converts the fuel level into an electrical signal, which is then transmitted to the gauge via the wiring harness. Proper wiring is critical to ensure accurate readings and prevent issues like erratic behavior or complete failure of the gauge.
Understanding the fuel gauge's function, location, and wiring is the first step in maintaining and troubleshooting this vital component. If you encounter any issues with your fuel gauge, it's essential to inspect the wiring and connections, as loose or damaged wiring can lead to inaccurate readings. Additionally, regular maintenance, such as checking for corrosion or damage to the wiring, can help ensure the gauge operates reliably over the long term.
Replacing Powerstroke Fuel Injectors: A Step-by-Step Guide
You may want to see also
Needle Replacement: Remove old needle, install new one securely
To replace the fuel gauge needle, you'll need to carefully remove the old one and then install the new one securely. Here's a step-by-step guide to ensure a successful replacement:
Step 1: Gather the Necessary Tools and Materials
Before you begin, make sure you have the required tools and materials. You'll need a new fuel gauge needle, a small screwdriver (preferably a flathead), and possibly a fuel gauge replacement kit if your car model requires specific tools. It's also a good idea to have a bright flashlight or a headlamp to illuminate the dashboard area.
Step 2: Locate the Fuel Gauge Assembly
Locate the fuel gauge assembly, which is typically found on the driver's side of the dashboard. Carefully inspect the area around the gauge to identify the screws or clips that hold it in place. You may need to remove some trim panels or decorative covers to access the screws.
Step 3: Remove the Old Fuel Gauge Needle
Once you have access to the fuel gauge assembly, carefully remove the screws or clips and set them aside. Gently lift the gauge assembly to expose the old fuel gauge needle. You might need to use the screwdriver to pry the needle out, being careful not to damage the surrounding components. Take note of the position of the needle to ensure proper alignment when installing the new one.
Step 4: Prepare the New Fuel Gauge Needle
Take the new fuel gauge needle and ensure it is the correct size and type for your vehicle. Some vehicles may have different needle styles, so double-check compatibility. If your car has a specific fuel gauge replacement kit, follow the instructions provided with the kit to ensure a proper fit.
Step 5: Install the New Fuel Gauge Needle
Carefully align the new fuel gauge needle with the slot or opening in the gauge assembly. Press the needle firmly into place, ensuring it is securely attached. Double-check that the needle is straight and aligned with the gauge's markings. Replace any screws or clips you removed earlier to secure the gauge assembly back in place.
Step 6: Test and Adjust
After installing the new needle, turn on the ignition and test the fuel gauge. Ensure it is functioning correctly and displaying the fuel levels accurately. If necessary, make small adjustments to the needle's position using the screws or clips to fine-tune its alignment.
Remember, if you're unsure about any step or encounter any difficulties, it's best to consult a professional mechanic or refer to your vehicle's manual for specific instructions tailored to your car model.
Cadillac CTS Fuel Injector: DIY Replacement Guide
You may want to see also
Wiring Connections: Identify and reconnect gauge wiring correctly
When replacing the fuel gauge needle, one of the crucial steps is ensuring that the wiring connections are made correctly. This process requires careful attention to detail to avoid any issues with the gauge's functionality. Here's a step-by-step guide to help you with the wiring connections:
Locate the Gauge Wiring: Begin by locating the wiring harness that connects to the fuel gauge. This harness typically consists of several wires, each with a specific color-coded insulation. Identify the wires that are connected to the gauge and the corresponding wires in the harness. It's essential to match the correct wires to ensure proper functionality.
Prepare the New Gauge (if applicable): If you are installing a new fuel gauge, take this opportunity to double-check the wiring. Ensure that the new gauge has the correct wiring configuration and color-coded wires. This preparation will make the wiring process smoother.
Disconnect the Old Gauge (if replacing): If you are replacing the fuel gauge, carefully disconnect the wiring harness from the old gauge. Take note of the wire connections and their positions. Properly secure the old gauge to prevent any accidental disconnections during the replacement process.
Connect the Wires: Now, it's time to reconnect the wiring. Start by identifying the ground wire, which is usually black or brown. Connect this wire to the corresponding ground terminal on the new gauge (or the old one if you're reusing it). Next, locate the send wire, often colored white or yellow, and connect it to the send terminal. The send wire is responsible for transmitting the fuel level signal. Ensure a secure connection by tightening the wires firmly.
Test the Connections: After completing the wiring connections, it's crucial to test them. Turn on the vehicle's ignition and check if the fuel gauge functions correctly. Monitor the needle movement and ensure it responds accurately to the fuel level changes. If the gauge doesn't work as expected, double-check the wiring connections and ensure they are secure and properly aligned.
Remember, proper wiring connections are vital for the fuel gauge to function correctly. Take your time to identify and reconnect the wires accurately, and always test the gauge after making any wiring changes.
Replacing the Fuel Filter: A Step-by-Step Guide for Your 2007 Hyundai Tucson
You may want to see also
Testing: Verify gauge accuracy post-replacement with a test tool
After replacing the fuel gauge needle, it's crucial to verify its accuracy to ensure reliable operation. This testing process involves using a specialized test tool designed for fuel gauge calibration. Here's a step-by-step guide to ensure the new gauge is functioning correctly:
Step 1: Prepare the Test Equipment:
You'll need a fuel gauge test tool, which is a device specifically calibrated to simulate different fuel levels. This tool will allow you to set specific fuel levels and measure the gauge's response. Ensure the tool is properly charged and calibrated for accurate readings.
Step 2: Connect the Test Tool:
Carefully connect the test tool to the fuel gauge's wiring harness. This connection will allow the tool to communicate with the gauge and send simulated fuel level signals. Ensure all connections are secure to avoid any interference.
Step 3: Set Known Fuel Levels:
Using the test tool, set the fuel level to various known values, starting from empty and gradually increasing. For example, set it to 1/4, 1/2, 3/4, and full tank levels. It's important to cover a range of fuel levels to test the gauge's accuracy across different states.
Step 4: Observe Gauge Reading:
As you adjust the fuel level with the test tool, observe the gauge's response. The needle should move accordingly, indicating the simulated fuel levels accurately. Compare the gauge's reading with the known fuel levels you set.
Step 5: Record Results:
Make detailed notes of the fuel levels set and the corresponding gauge readings. Record any discrepancies or variations in the gauge's response. This documentation will help identify any potential issues with the replacement gauge.
Step 6: Repeat and Verify:
Repeat the testing process multiple times to ensure consistency. Perform the test at different temperatures and driving conditions to account for potential environmental factors that might affect gauge accuracy.
By following these steps and using a dedicated test tool, you can thoroughly verify the accuracy of the fuel gauge needle replacement. This testing process ensures the gauge functions correctly and provides reliable fuel level information, giving you peace of mind and accurate fuel management.
Replacing Fuel Filter: A Step-by-Step Guide for 1998 Buick Regal GS Owners
You may want to see also
Safety Precautions: Wear gloves, work in a well-ventilated area, and follow safety guidelines
When embarking on a project to replace a fuel gauge needle, prioritizing safety is paramount. One of the most critical precautions is to wear gloves throughout the process. This simple step acts as a barrier, protecting your hands from potential hazards such as sharp edges, hot surfaces, or any chemicals that might be involved in the repair. Gloves also provide a better grip, ensuring that you can handle tools and components with precision and control. Opt for gloves made from durable materials like leather or heavy-duty rubber to ensure they can withstand the demands of the task.
In addition to personal protective equipment, working in a well-ventilated area is essential. Many fuel gauge replacements involve handling small components and soldering, which can release fumes that may be harmful if inhaled. A well-ventilated workspace helps to disperse these fumes, reducing the risk of respiratory issues. If you're working in a confined space, consider using a portable air purifier or a fan to improve air circulation. Ensure that your work area is clean and organized to minimize the risk of accidents caused by tripping or mishandling tools.
Safety guidelines should be followed meticulously to ensure a secure and efficient repair. Before beginning, ensure that you have all the necessary tools and components ready to avoid any unnecessary handling of the car's interior. It is also advisable to disconnect the battery to prevent any accidental electrical shocks or short circuits. When soldering, use a fume extractor to capture and filter the harmful gases, and always work with the engine off and the car in a stationary position.
Furthermore, take the time to understand the specific procedures and potential risks associated with your vehicle's fuel gauge system. Consult the car's manual or online resources to gather detailed instructions tailored to your make and model. This knowledge will enable you to identify potential hazards and take appropriate measures to mitigate them. Remember, taking these safety precautions will not only protect you but also contribute to a successful and safe fuel gauge replacement.
In summary, replacing a fuel gauge needle requires a thoughtful approach to safety. By wearing gloves, working in a well-ventilated area, and adhering to safety guidelines, you can minimize the risks associated with the task. These simple yet effective measures will ensure a safer working environment and contribute to a successful repair, allowing you to get back on the road with confidence.
Replacing Your Fuel Door: A Step-by-Step Guide
You may want to see also
Frequently asked questions
Replacing the fuel gauge needle is a relatively simple process, but it requires some basic automotive knowledge and tools. Here's a step-by-step guide: First, locate the fuel gauge assembly, which is usually found on the dashboard. You might need to remove some dashboard trim panels to access it. Then, disconnect the electrical connections and carefully remove the old needle. Take note of the wiring harness and any retaining clips. Purchase a replacement needle that fits your car's make and model. Install the new needle by aligning it with the gauge housing and securing it with the provided clips or screws. Reconnect the electrical wires and ensure a secure connection. Test the gauge to ensure it functions correctly.
Yes, you can replace the needle without completely removing the fuel gauge. Start by disconnecting the electrical connections and identifying the retaining clips or screws that hold the needle in place. Carefully pry open the gauge housing to access the needle. Take note of the wiring and any additional fasteners. Remove the old needle and install the new one, ensuring it is aligned correctly. Secure the new needle and reconnect the wiring.
You will typically need a small screwdriver or a flat-head tool to pry open the gauge housing. Some cars may require a specialized tool for removing the retaining clips or screws. Have a set of screwdrivers, a flat-head screwdriver, and possibly a small pry bar handy. Additionally, ensure you have the replacement needle and any necessary wiring harnesses.
In some cases, you might be able to fix a broken needle instead of replacing it. If the needle is cracked or damaged but still functional, you can try cleaning and lubricating the needle and its housing. Ensure the gauge is properly calibrated and adjust the sensitivity if needed. However, if the needle is severely damaged or beyond repair, replacement is the best option.
Yes, several issues can lead to a malfunctioning fuel gauge needle. These include damaged or corroded wiring, faulty gauge sensors, or issues with the gauge's internal circuitry. In some cases, the needle may become stuck or unresponsive due to dirt or debris in the gauge housing. It's essential to inspect the wiring and gauge components for any signs of damage or corrosion before attempting any repairs or replacements.