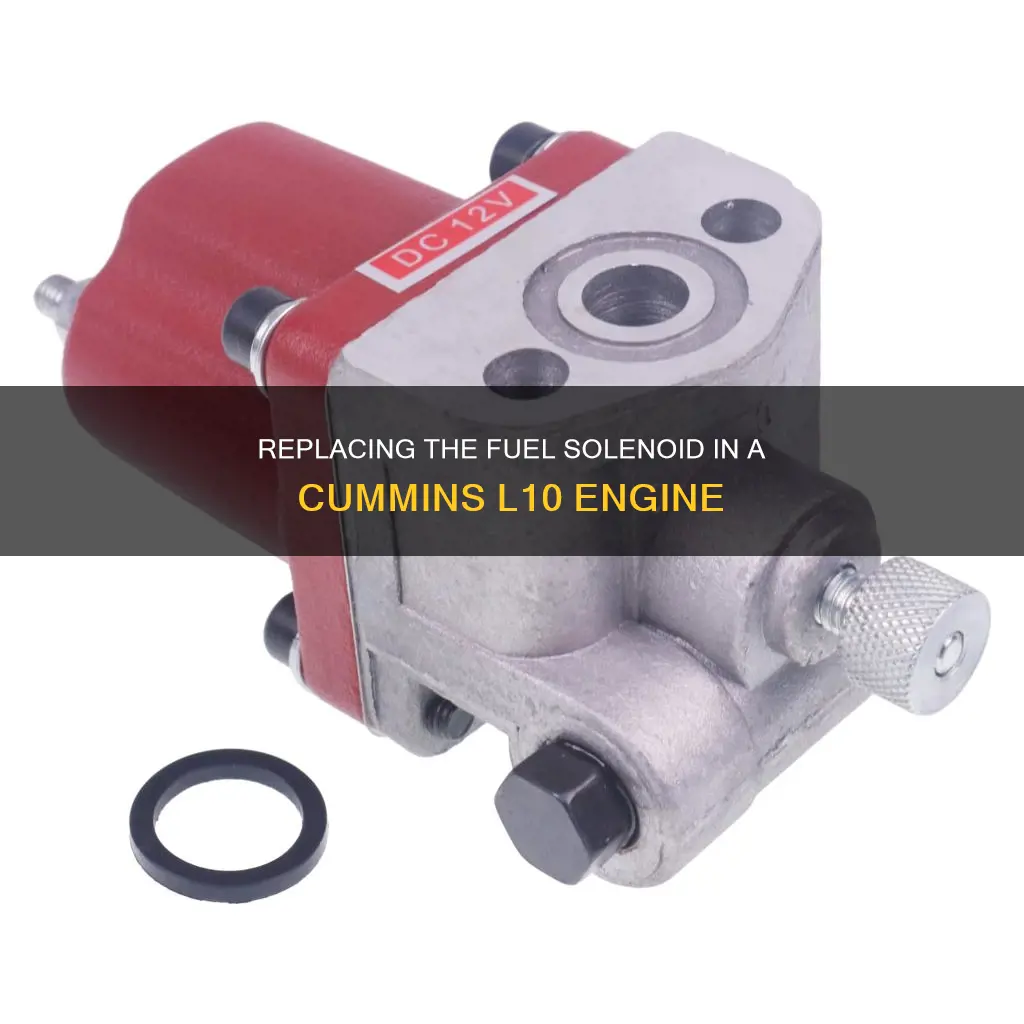
The Cummins L10 engine is a popular choice for heavy-duty trucks and machinery, but like any machine, it can experience problems with its fuel solenoid. A faulty fuel solenoid can cause issues with starting and shutting down the engine, which can be a major inconvenience and even a safety hazard. Troubleshooting and replacing the fuel solenoid is a complex process that requires mechanical knowledge and expertise. It involves checking for voltage at the solenoid, testing the magnetic pull, inspecting wiring and fuses, and even adjusting fuel flow settings. In some cases, the issue may lie elsewhere, such as with the return restriction or the fuel pump.
Characteristics | Values |
---|---|
Engine | Cummins L10 |
Problem | Engine won't shut off |
Solution | Verify 12 volts to shutdown solenoid; disconnect wire from solenoid; check for return restriction or pump problem |
Possible Cause | Return restriction or pump problem |
What You'll Learn
Troubleshooting a faulty solenoid
Step 1: Check Voltage and Wiring
First, verify that your shutdown solenoid is receiving the correct voltage. For a Cummins L10 engine, ensure there is 12 volts reaching the solenoid. Also, check that there is no voltage present at the solenoid when the ignition is turned off. Inspect the wiring for any signs of damage or corrosion, as this could be causing the issue.
Step 2: Disconnect the Wire
Try disconnecting the wire from the solenoid. If the engine shuts down after this, then the issue may lie elsewhere, such as a return restriction or an internal pump problem.
Step 3: Inspect the Fuel System
Check for any return fuel restriction that could be causing a buildup of pressure on the return side of the fuel system. This can lead to the engine not shutting down completely. Inspect fuel lines, filters, and the pump for any issues. Ensure there is good pressure going into the head and that the fuel filter is not draining excessively when starting.
Step 4: Check the Solenoid Valve
The solenoid valve may be stuck in either the open or closed position. When closed, it prevents fuel from reaching the engine, leading to starting issues and stalling. If it remains open, the engine may run uncontrollably or lead to fuel wastage. Disconnect the solenoid and test it with a battery to see if the plunger moves as it should.
Step 5: Test the Solenoid
Test the solenoid by connecting it directly to a power source. If it does not function properly or shows signs of malfunction, it will need to be replaced.
Step 6: Clean and Inspect
Clean the solenoid and the surrounding area to remove any dirt, debris, or corrosion that could be causing the issue. Ensure all connections are tight and secure. Check the plunger for any obstructions, and inspect the rubber boot for any damage.
Step 7: Check for Fuel Leaks
Inspect the solenoid area for any visible fuel leaks. Leaks can be caused by a damaged or malfunctioning solenoid that is not sealing correctly. Pipe tape, dirt, or hard water deposits could be the culprits, so clean and tighten all components to prevent future leaks.
Step 8: Address Other Potential Issues
If the above steps do not resolve the issue, there may be other factors at play, such as incorrect voltage, poor connections, mechanical wear and tear, or overheating. It is recommended to have a professional inspect and replace the solenoid if necessary to ensure the safe and reliable operation of your Cummins L10 engine.
Replacing Fuel Pump in Lexus GX470: Step-by-Step Guide
You may want to see also
Checking for power to the solenoid
To check for power to the solenoid, you can use a multimeter to test the solenoid valve. This will help you determine whether the solenoid is receiving power and working properly.
Firstly, ensure safety by turning off any power to the solenoid and disconnecting it from the circuit. Locate the solenoid and its two terminals. Set your multimeter to the appropriate measurement mode—for a basic check of solenoid valves, the resistance measurement mode is typically used. Choose an appropriate resistance range, usually in the range of 1KΩ or 10KΩ.
Now, connect one probe of the multimeter to one end of the solenoid coil and the other probe to the other end. If the solenoid is functioning properly, you should see a stable resistance value on your multimeter, typically between a few hundred to a few thousand ohms, depending on the solenoid size.
If the resistance value is infinite or close to zero, it indicates a problem with the solenoid coil, and further checks or replacement may be required.
Additionally, you can perform a dynamic test by simulating the actual working conditions of the solenoid valve. This involves applying air pressure instead of oil pressure and repeatedly turning the solenoid valve on and off to observe the airflow at the oil drain port. If the airflow always exists, it means the valve is not sealed properly. If there is no airflow, the solenoid valve is blocked.
Another test is to check the voltage of the solenoid valve to ensure it can work at its rated voltage. First, confirm the equipment's AC voltage specification according to the solenoid valve's manual. Then, connect the multimeter probes to the terminals of the solenoid valve. If the solenoid is working properly, the voltage displayed on the multimeter should match the rated voltage of the solenoid valve.
If the solenoid is not receiving power, there may be an issue with the wiring, fuses, or circuit breakers. Check for any signs of corrosion or damage in the wiring and fuses, and ensure that the circuit breaker has not tripped.
Corvette Fuel Pressure Regulator: Replacing the 91 Model
You may want to see also
Disconnecting the solenoid wire
Before you begin, ensure you have the necessary tools, such as a voltage tester, and safety equipment, including gloves and eye protection. It is also important to work in a well-ventilated area to avoid inhaling any fumes.
Step 1: Locate the fuel solenoid. It is usually found near the engine and is often labelled or marked.
Step 2: Identify the solenoid wire. This is the wire that connects the solenoid to the electrical system of the engine. It is typically colour-coded or labelled for easy identification.
Step 3: Using the appropriate tool, carefully disconnect the wire from the solenoid. You may need to loosen any clamps or fasteners that secure the wire in place. Be gentle to avoid damaging the wire or the solenoid.
Step 4: Once the wire is disconnected, place it away from the solenoid to avoid accidental reconnection. You can use wire ties or tape to secure the wire in a safe location.
Step 5: Check the voltage at the solenoid. Use a voltage tester to verify that there is no voltage present at the solenoid terminal. This step is crucial to ensure that the circuit is inactive before proceeding with further repairs or replacements.
Step 6: If the voltage tester indicates the presence of voltage, re-check your work to ensure that the wire is properly disconnected. If voltage persists, there may be an issue with the wiring or the electrical system.
Step 7: If no voltage is detected, you can proceed with further troubleshooting steps or replace the fuel solenoid as needed. Ensure that you refer to a qualified mechanic or a repair manual for specific instructions on replacing the solenoid.
Remember, working with an engine's electrical system requires caution. Always prioritize your safety and follow standard procedures to avoid any accidents or mishaps. If you are unsure about any steps, consult a professional mechanic for guidance.
Replacing the Fuel Pump in a 2002 Oldsmobile Silhouette
You may want to see also
Identifying a return restriction
A return restriction is a potential issue that can occur in the fuel system of an engine, specifically in the fuel shut-off solenoid valve. This issue can lead to the engine not shutting off properly. Here are some detailed instructions on identifying a return restriction:
Understanding the Fuel Shut-Off Solenoid
Before identifying a return restriction, it is essential to understand the function of the fuel shut-off solenoid. This component plays a crucial role in remotely shutting off the fuel supply to the engine. It consists of a valve body and a solenoid assembly attached to a valve stem. When energised, the solenoid creates an electromagnetic field that moves the plunger, allowing fuel to pass through the valve and reach the engine. Conversely, when deactivated, the valve spring pulls the poppet valve back, shutting off the fuel flow.
Signs of a Return Restriction
A return restriction can exhibit several signs, including:
- Engine shutdown issues: If the engine shuts down unexpectedly while running, it could be due to a loss of electromagnetic force in the solenoid, disrupting the fuel flow.
- Fuel supply interruption: A return restriction can cause a blockage in the fuel return line, preventing fuel from flowing back to the tank. This can lead to fuel supply issues and engine performance problems.
- Fuel leakage: In some cases, a return restriction may cause fuel to leak from the solenoid or other components in the fuel system.
- Engine performance issues: A return restriction can affect the fuel supply to the engine, resulting in rough idling, uneven acceleration, or power loss during operation.
Troubleshooting Steps
To identify a return restriction, follow these steps:
- Check voltage: Ensure that there is no voltage at the solenoid with the ignition turned off. This can be done using a multimeter.
- Disconnect the wire: Try disconnecting the wire from the solenoid. If the engine still doesn't shut down, the issue could be a return restriction or an internal pump problem.
- Inspect the fuel system: Carefully examine the fuel lines, including the return line, for any signs of blockage or restriction. Look for debris, corrosion, or damage that could be causing the restriction.
- Test the solenoid: Connect the solenoid to a power source and observe its function. If the plunger does not move as expected, the solenoid may be faulty or stuck.
- Check for leaks: Inspect the solenoid and surrounding components for any signs of fuel leakage. Leaks can be a result of a return restriction or a faulty solenoid.
- Verify fuel flow: Disconnect the fuel line from the solenoid and observe the fuel flow. If the flow is weak or non-existent, it could indicate a restriction in the fuel return line.
Replacing Fuel Lines on WeedEater SST25CE Trimmer: A Step-by-Step Guide
You may want to see also
Checking for a pump problem
If you're experiencing issues with your Cummins L10 engine, one potential problem area is the fuel pump. Here are some detailed steps to help you check for and troubleshoot any pump-related issues:
Step 1: Verify Voltage to the Shutdown Solenoid:
Start by checking if your Cummins L10 engine is receiving the correct voltage. Ensure that you have 12 volts reaching your shutdown solenoid. It's also important to verify that there is no voltage present at the solenoid when the ignition is turned off.
Step 2: Disconnect the Wire from the Solenoid:
Try disconnecting the wire that connects to the solenoid. If the engine shuts down after this step, your issue is likely related to a return restriction or an internal pump problem.
Step 3: Check for Return Fuel Restriction:
If the engine doesn't shut down after disconnecting the wire, the next step is to check for a return fuel restriction. This issue can cause a buildup of pressure on the return side of the fuel system, leading to potential pump problems.
Step 4: Inspect the Fuel Lines:
Examine the fuel lines for any signs of damage or blockage. Ensure that there is good pressure going into the engine head. If the fuel lines appear clear, the issue may lie elsewhere.
Step 5: Check the Fuel Shut-Off Solenoid:
The fuel shut-off solenoid is a critical component that controls the flow of fuel. Make sure this solenoid is functioning correctly and that it receives a constant supply of 12 volts when the ignition is on. If there is no power to the solenoid, you may need to replace it or check for wiring issues.
Step 6: Test the Manual Bypass:
Some Cummins L10 engines have a manual bypass screw near the solenoid on the top rear of the pump. Try turning this screw to bypass the valve and see if the engine starts. If it does, you may have a problem with the solenoid or its associated wiring.
Step 7: Check the Injector Seals:
If your engine continues to run even with the manual bypass screw turned, you might have leaking injector seals. This can cause the engine to keep running even when you attempt to shut it down.
Step 8: Verify the Presence of the Dished Spring Washer:
Under the shut-off solenoid, there should be a dished spring washer. Ensure that this washer is present and properly positioned, as its absence can affect the fuel shut-off function.
Step 9: Inspect the Solenoid Coil:
If you've had the coil off the solenoid for any reason, inspect the end where the wire connects. Verify the voltage marked on the solenoid (12V or 24V) to ensure it matches your vehicle's electrical system.
Step 10: Check for Wiring Issues:
If you continue to experience issues, there could be a problem with the wiring to the solenoid. Check the wires for any signs of damage or corrosion, especially at the fuse block in the cab. Ensure that the wires are securely connected and have intact insulation.
Remember to refer to a qualified mechanic or Cummins expert for further advice and guidance if you're uncomfortable performing these checks or if you suspect a more serious issue with your engine.
Replacing a 93 Ford E-150 Fuel Filter: Step-by-Step Guide
You may want to see also
Frequently asked questions
First, verify that you have 12 volts going to your shutdown solenoid and that there is no voltage at the solenoid when the IGN is off. Try disconnecting the wire from the solenoid and see if the engine will shut down. If not, you could have a return restriction or a pump problem.
If your engine won't shut off, even after replacing the fuel solenoid, there may be an issue with voltage or wiring.
There could be a return restriction causing a buildup of pressure on the return side, or there could be a problem with the pump.
The shutdown solenoid is controlled by the key and allows the engine to shut off when the key is turned off. The fuel solenoid controls the flow of fuel to the engine and can be manually operated with a screw.
Some common issues include wiring problems, voltage issues, and a weak or corroded terminal in the fuse block.