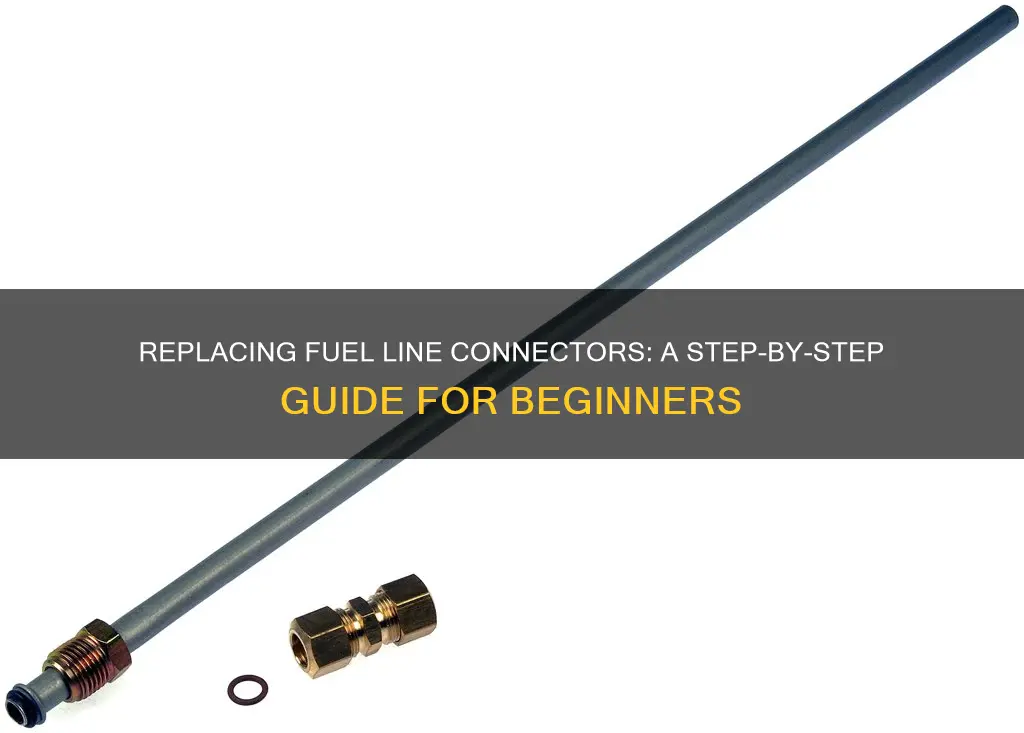
Replacing a fuel line connector can be a challenging task, especially when dealing with different types of connectors and fuel line materials. The process involves disconnecting the fuel line, repairing or replacing the connector, and reinstalling the fuel line. It is crucial to take safety precautions when working with fuel lines to prevent leaks and potential fires. Some common tools and techniques used in this process include the use of nylon repair tools, tubing cutters, boiling water to soften nylon lines, and various types of clamps and fittings.
Characteristics | Values |
---|---|
Tools | Wood screw, wire cutters, small hacksaw, utility knife, tubing cutter, tubing bender, pliers, screwdriver, jack, jack stands, ramps, Phillips screwdriver, 7mm socket/wrench, heat gun, hair dryer, silicone spray, lubricant, caulking gun, single-edge razor blade, flaring tool clamp, band saw, drill, vise, hammer, pliers, needle-nose pliers, razor knife, fuel injection clamps, heat gun, tubing pliers, release tool, bolt, string, pot, stove, wire cutters or clamping device, hose clamp, car jack, jack stands, ramps, push-type connector, push-and-lock style connector, pinch-type connector, spring-style retainer fitting, horseshoe-type fitting, horseshoe clip, barbed splice, barbed union, compression fitting, ferrule, perforated cap, centre section, compression fitting, safety latch, safety line, black ring, fuel injection clamps, nylon repair tool, gun, nylon-tubing cutter, spring lock, special tool |
Materials | Teflon, rubber, metal, plastic, silicone spray, hydraulic jack oil, lubricant, light lubricant, rubber hose, nylon, wood, rubber tubing, fuel, fuel injection clamps, high-temperature tube, heat-shrink tube, ETFE tubing, braided line, fuel-grade hose, barbed union, hose clamps, rubber patch, plumbing epoxy, race tape, compression coupling, brass splice, rubber line, jubilee patch, nitrile glove, soda can, shoelace, hose, fuel line, fuel filter, fuel pump, compression fitting, ferrule, screw, block, rubber tubing, compression fitting, centre section, cap, ferrule, nylon fuel line, fuel line connector, boiling water, nylon replacement lines, fuel pump hanger, AN-6 feed, return lines, braided fuel line, barbed fitting, barbed splice, quick-connect barrel connectors, rubber fuel line, hose clamps, barbed connectors, compression type fitting, brass compression fitting, nylon safety clips, spring lock, horseshoe clip, horseshoe-type fitting, barbed connectors, quick-connect barrel connectors, <co: |
What You'll Learn
Identify the type of connector
To identify the type of connector in your fuel line, you'll need to inspect the current setup and take note of certain characteristics. Here's a guide to help you identify the type of connector:
Material
First, identify the material of your fuel line. Most cars are equipped with metal lines, typically made from stainless steel, aluminum, or coated steel tubes. Metal lines are known for their durability. Alternatively, some vehicles may have rubber fuel lines, which are easier to install but may degrade over time. Other options include nylon tubing or braided hose, which is rubber hose reinforced with a braided stainless steel or nylon exterior.
Fitting Type
Next, determine the type of fitting used in your fuel line. Fittings are the connectors that join different sections of the fuel line together. Common types of fittings include Adapter Fittings (also called Standard or Union Fittings), Port Fittings, and Pipe Fittings. Adapter Fittings are often used to connect fuel lines to components like fuel pumps, regulators, or filters. Port Fittings conform to specific standards, such as military standards, and provide a reliable seal. Pipe Fittings, on the other hand, use tapered threads and require sealing compounds or Teflon tape to prevent leakage.
Thread Type
When identifying the connector type, pay attention to the thread type used in the fittings. There are two main types of threads: straight thread and tapered thread. Straight threads run parallel to each other, and Port Fittings or Adapter Fittings with straight threads require an O-ring Boss Seal technique to prevent leakage. Tapered threads, also known as pipe threads, have a slight angle (typically 2°) that allows the threads to interfere and seal off. Tapered threads do not use O-rings but rely on compounds or Teflon tape for sealing.
Hose and Tubing Size
Finally, identify the size of the hose or tubing used in your fuel line. This is important when sourcing replacement connectors or fittings. The size is typically designated by its outer diameter (OD) and is measured in inches or millimetres. For example, a 3/8" hose or tubing has an outer diameter of 3/8 inches.
By considering these factors, you can identify the type of connector in your fuel line and make informed decisions when replacing or repairing your fuel system.
Replacing Fuel Injectors in a CBR600RR: A Step-by-Step Guide
You may want to see also
Disconnect the fuel line
Disconnecting a fuel line can be a tricky process and may require a fuel line disconnect tool. The first step is to identify the type of fuel line connector in your vehicle. Some common types include quick-connect, push-on, and barbed fittings. Here is a step-by-step guide to help you safely disconnect the fuel line:
Step 1: Prepare the Work Area
Before beginning any work on the fuel system, it is crucial to take necessary safety precautions. Ensure the engine is turned off and the fuel supply is disconnected to prevent any accidental ignition. Place a suitable container under the fuel line to catch any spilled fuel. Wear protective gear, such as gloves and eye protection, to shield yourself from fuel and debris.
Step 2: Relieve Fuel System Pressure
Release the pressure in the fuel system by relieving the pressure in the fuel rail. This can be done by removing the fuel pump fuse or relay and then cranking the engine for a few seconds. Make sure to re-install the fuse or relay after releasing the pressure.
Step 3: Loosen the Fuel Line Connector
Locate the fuel line connector and identify the type of connection. For quick-connect fittings, you may need a fuel line disconnect tool, which can be purchased or rented from auto parts stores. Place a rag or towel around the connector to catch any spilled fuel. Carefully insert the disconnect tool and release the locking mechanism by pushing or twisting, depending on the tool's design.
For push-on connectors, you may not need a specialized tool. Instead, use a pair of pliers to gently squeeze the tabs on the connector and pull the fuel line away from the fitting. Be cautious not to damage the tabs during this process.
If your vehicle has barbed fittings, you will need to cut the fuel line to disconnect it. Use a tubing cutter or a single-edge razor blade to make a clean cut as close to the fitting as possible. Be mindful not to damage any surrounding components.
Step 4: Remove the Fuel Line
Once the connector is loosened, carefully pull the fuel line away from the fitting. If the line is stubborn, use a gentle rocking motion to loosen it further. Be cautious not to kink or damage the fuel line during removal.
Step 5: Contain Spilled Fuel and Clean the Area
Use an appropriate container to collect any spilled fuel and dispose of it safely. Clean the work area, ensuring that all fuel residue is removed. Do not leave any fuel-soaked rags unattended, as they pose a fire hazard.
Disconnecting a fuel line is a delicate task that requires attention to safety and precision. Always refer to your vehicle's repair manual for specific instructions and take the necessary precautions to avoid any potential hazards.
Replacing Fuel Injectors: Ford 302 Step-by-Step Guide
You may want to see also
Cut the line
Cutting a fuel line is a risky procedure and should be done with caution. Before cutting, ensure you have the right tools to get a clean cut without creating sparks, which could be dangerous. A hacksaw blade, tubing cutter, or small pipe cutter are good options. It is also important to work outside or in a well-ventilated area.
When cutting the line, be sure to leave enough room for the tubing to rotate 360 degrees if using a pipe cutter. If there is not enough space to use a pipe cutter, an alternative method is to use a hacksaw blade with electrical tape wrapped around one end for a secure grip. This will help you avoid getting cut.
If you are cutting a high-pressure metal fuel line, a mini plumbing pipe cutter or a Dremel with a cutting disc can be used, but be cautious of sparks. It is recommended to do this work outside the car and to keep a fire extinguisher nearby as a precaution.
Another method for cutting fuel lines involves using a caulking gun and a line clamp from a brake line flaring kit. First, make a clean cut on the tubing, then insert the end of the tubing through the caulking gun. Clamp the tubing tightly in the flaring tool, leaving only enough tubing sticking out to fit onto the fitting. Next, add lubricant to the fitting and move the plunger forward in the gun until there is just enough room for the fitting. Align the fitting with the tubing and begin to squeeze the handle of the caulking gun. Watch closely, as it only takes a few clicks to seat the fitting fully.
Remember to always exercise caution when working with fuel lines and take the necessary precautions to ensure your safety.
Fuel Injectors: Replace or Repair? The Pros and Cons
You may want to see also
Soften the line with hot water
Softening a fuel line with hot water is a great way to make it more pliable and easier to work with. Here's a step-by-step guide on how to do it effectively:
First, boil some water and pour it into an insulated mug or container. You want to ensure that the water is very hot, as this will help soften the line more effectively. Be careful not to burn yourself during this process. Next, take the fuel line and dip the hose end into the hot water. Allow it to sit for a few minutes, regularly checking to see if it has softened enough. You should aim for a consistency that is pliable but not too soft, as you don't want it to lose its shape.
While the line is softening in the hot water, you can prepare the fitting by loosening the clamp screws. There's no need to remove them entirely, just loosen them enough to make the process smoother. Once the line is soft enough, carefully remove it from the hot water. It's now time to quickly fit the line onto the connector. Be mindful of the time here, as the line will start to harden again as it cools down. Use your hands or a suitable tool to guide the line onto the connector, ensuring a snug fit.
If you're having trouble getting the line onto the connector, you can try dipping just the end of the line into hot water for a few seconds to soften it again. Alternatively, you can apply some WD or motor oil to the connector to help ease the process. It's important to work quickly and efficiently during this process to take advantage of the softened state of the line. Once the line is in place, allow it to cool and harden, forming a secure connection.
This method is a great way to make working with fuel lines easier and can be a real time-saver. Just remember to exercise caution when working with hot water and fuel lines to avoid any accidents or injuries.
Replacing the Fuel Pump in Your 1998 Honda Civic
You may want to see also
Insert the new connector
To insert the new connector, you must first prepare the fuel line. Cut the line with a utility knife, ensuring that the final length remains the same as the old line. Then, boil a pot of water and submerge the end of the fuel line for a few minutes until the nylon becomes soft.
Now, you can insert the new connector. Place a small amount of oil on the tapered connector and position it at the end of the fuel line. Use a tool to squeeze the blocks of the repair kit together, pushing the connector into the line. Ensure that the connector is fully seated on all three steps of the line.
If you are repairing a metal fuel line, you will need a compression fitting. Place one perforated cap on the original line with the threads facing out, then install the ferrule (ring) over the line in front of the cap. Push the original fuel line with the ferrule and cap into the centre section of the connector, and thread the cap onto the centre section. Keep pressure on the fuel line while tightening the cap.
Finally, turn the key in the ignition and check for any leaks.
Replacing Fuel Injectors in Your Classic 1984 Merc
You may want to see also