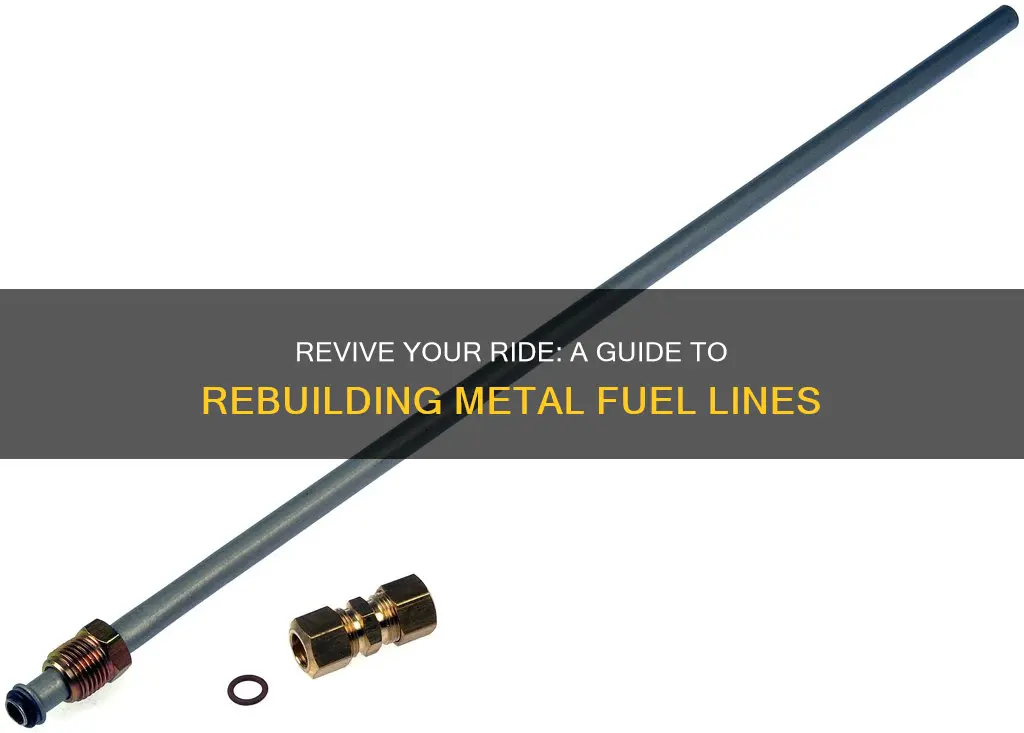
Rebuilding a metal fuel line is a crucial task for ensuring the safe and efficient operation of a vehicle's fuel system. This process involves replacing damaged or worn-out components to restore the line's integrity and prevent potential fuel leaks or system failures. The procedure typically includes removing the old fuel line, inspecting and replacing any corroded or damaged sections, and reinstalling the new line with secure fittings and connections. Proper tools, safety equipment, and a systematic approach are essential to ensure a successful rebuild, allowing the vehicle to operate reliably and efficiently.
What You'll Learn
- Prepare Tools and Materials: Gather necessary tools, safety gear, and replacement metal fuel lines
- Inspect and Prepare the Line: Check for damage, clean the line, and ensure it's straight and secure
- Cut and Fit the New Line: Measure and cut the new line, then attach it securely to the engine
- Test for Leaks: Use a pressure gauge to check for leaks and ensure a tight connection
- Final Adjustments and Safety Checks: Verify the fuel line's functionality and stability before driving
Prepare Tools and Materials: Gather necessary tools, safety gear, and replacement metal fuel lines
Before you begin the process of rebuilding a metal fuel line, it's crucial to gather all the necessary tools, safety equipment, and replacement parts. This preparation will ensure a smooth and efficient repair process. Here's a step-by-step guide on what you need to do:
Tools and Equipment:
- Start by making a list of the tools required for the job. You will need a set of basic hand tools such as screwdrivers, pliers, an adjustable wrench, and a fuel line cutter. For more intricate work, consider a tube bender and a fuel line crimping tool. These specialized tools will help you bend and secure the metal fuel line effectively.
- A good set of safety gloves and safety goggles is essential to protect your hands and eyes from any potential hazards during the repair.
- Additionally, you might want to have a fuel line inspection camera to visualize the condition of the existing fuel line and identify any issues.
Safety Gear:
- Personal protective equipment (PPE) is a priority. Ensure you have a pair of heat-resistant gloves to handle any soldering or welding that might be required.
- Safety goggles or a face shield will protect your eyes from sparks, debris, or any potential fuel leaks.
- Consider wearing a respirator mask to avoid inhaling any harmful fumes during the repair process.
Replacement Parts:
- Obtain a replacement metal fuel line that is compatible with your vehicle's specifications. Ensure it is the correct size, length, and material to match the original fuel line.
- Along with the fuel line, you might need new fittings and connectors to ensure a proper seal and secure connection.
- It's advisable to have a spare set of these fittings in case any are damaged during the installation process.
By gathering these tools, safety gear, and replacement parts beforehand, you'll be well-prepared to tackle the task of rebuilding the metal fuel line. This organized approach will make the repair process more efficient and less stressful, ensuring you have everything readily available when you start the actual rebuilding process.
Understanding NBR Fuel Line: A Comprehensive Guide
You may want to see also
Inspect and Prepare the Line: Check for damage, clean the line, and ensure it's straight and secure
When inspecting and preparing a metal fuel line for rebuilding, it's crucial to follow a systematic approach to ensure a thorough assessment and effective preparation. Begin by visually examining the fuel line for any signs of damage, such as cracks, corrosion, or bends. Look for areas where the metal may have weakened or become compromised due to age, heat, or previous repairs. Pay close attention to the connections and fittings, as these are common points of failure. Check for any leaks or signs of moisture, as these could indicate internal damage or potential issues.
Cleaning the fuel line is an essential step to ensure a fresh start. Start by removing any visible debris or dirt from the exterior of the line. Use a soft-bristled brush or a specialized fuel line cleaner to gently scrub the surface, removing any built-up grime. For more stubborn deposits, consider using a fuel line cleaner that can dissolve and remove internal contaminants. Ensure that you follow the manufacturer's instructions for the cleaning product to avoid any potential damage to the metal. Rinse the line thoroughly to eliminate any residue and allow it to dry completely before proceeding.
Straightening the fuel line is critical to its proper function. Inspect the line for any kinks or bends that may have occurred during installation or previous repairs. Gently straighten the line using pliers or a fuel line straightener, being careful not to apply excessive force that could cause damage. Ensure that the line is straight and aligned, especially at the points where it connects to other components. This step is vital to prevent restrictions in fuel flow and potential engine performance issues.
Security and stability are key considerations. Check that the fuel line is securely attached to the fuel tank and engine with appropriate clamps or fittings. Ensure that all connections are tight and free from any looseness that could lead to leaks or disconnections. Inspect the clamps for any signs of wear or damage, and replace them if necessary. Verify that the line is not pinched or caught between other components, as this could restrict flow and cause issues. Properly securing the fuel line ensures its longevity and the overall reliability of the fuel system.
By thoroughly inspecting and preparing the metal fuel line, you lay the foundation for a successful rebuild. This process involves a careful assessment of damage, thorough cleaning, and ensuring the line is straight and securely installed. Each step is crucial to guarantee optimal performance and safety in the fuel system.
Mastering the Art of Painting Rubber Fuel Line Hose
You may want to see also
Cut and Fit the New Line: Measure and cut the new line, then attach it securely to the engine
Before you begin the process of cutting and fitting the new metal fuel line, it's crucial to ensure you have the right measurements and tools. Start by carefully measuring the length of the old fuel line and making a note of it. This will help you determine the exact length of the new line required. Using a metal shears or a similar cutting tool, carefully cut the new fuel line to the precise length. It's important to be accurate here to ensure a proper fit.
Once you have the new line cut to size, it's time to attach it to the engine. Locate the fuel line fittings and connectors that will be used to join the new line to the existing system. Clean the fittings and ensure they are free of any debris or old fuel residue. Apply a suitable fuel line adhesive or sealant to the interior of the fittings, following the manufacturer's instructions. Slide the new fuel line into the fittings, ensuring it is aligned correctly. Tighten the fittings securely using the appropriate tools, being careful not to overtighten and risk damage.
When attaching the new line, it's essential to maintain a secure and tight connection. Use fuel line clamps or fittings designed for the specific fuel line material. Tighten the clamps or fittings firmly, ensuring they are snug against the fuel line and engine components. Check for any leaks by applying a small amount of fuel to the connection and observing if there are any drips. If there are any leaks, tighten the connection further or consider replacing the fitting.
After attaching the new fuel line, it's a good practice to test the system. Start the engine and listen for any unusual noises, especially hissing or roaring sounds, which could indicate a leak. Check the fuel gauge and ensure the engine runs smoothly without any fuel-related issues. If everything functions as expected, you've successfully cut and fitted the new metal fuel line. Remember, proper maintenance and regular inspections of the fuel system are essential to ensure optimal engine performance and longevity.
Ford Fuel Line Clip Removal: A Step-by-Step Guide
You may want to see also
Test for Leaks: Use a pressure gauge to check for leaks and ensure a tight connection
When rebuilding a metal fuel line, it's crucial to ensure that all connections are secure and leak-free. One of the most effective methods to achieve this is by using a pressure gauge to test for leaks. This process involves applying pressure to the system and monitoring for any signs of leakage. Here's a step-by-step guide on how to perform this test:
Step 1: Prepare the Tools and Materials
Before you begin, ensure you have the necessary tools and materials. You'll need a pressure gauge, preferably a mechanical or dial-type gauge with a range suitable for the fuel line's pressure. Additionally, have some fuel or a fuel-like substance ready for the test. It's also a good idea to wear protective gear, such as gloves and safety goggles, to safeguard against any potential fuel splashes.
Step 2: Attach the Pressure Gauge
Locate the connection points where the fuel line joins other components, such as the fuel tank, pump, or engine. Carefully attach the pressure gauge to one of these connections. Ensure a tight and secure connection to avoid any potential leaks around the gauge itself.
Step 3: Apply Pressure
With the gauge attached, slowly open the fuel line's valve or connection to allow fuel to flow into the system. If you're using a pump, activate it to create pressure. The goal is to reach a predetermined pressure, which can be found in your vehicle's manual or a reliable source for your specific fuel line. Apply pressure gradually to avoid sudden spikes that could damage the system.
Step 4: Observe for Leaks
Now, carefully observe the system for any signs of leakage. Check for fuel dripping from connections, hissing sounds, or any other indicators of a potential leak. Pay close attention to the gauge's reading as well. A steady reading indicates a tight connection, while any fluctuations or drops in pressure could suggest a leak.
Step 5: Adjust and Secure Connections
If you detect any leaks, it's essential to address them immediately. Tighten connections, ensure proper alignment, and consider using thread seal tape or pipe dope on threads to enhance their sealing properties. If the leak persists, you may need to replace the affected section of the fuel line or seek professional assistance.
Step 6: Repeat the Process
After making any necessary adjustments, reattach the pressure gauge and repeat the pressure application and leak-checking process. This ensures that the issue has been resolved and provides an opportunity to verify the system's integrity.
By following these steps and using a pressure gauge, you can effectively test for leaks and ensure that your metal fuel line is rebuilt to the highest standards of safety and functionality. Remember, proper testing is crucial to prevent potential fuel-related issues and maintain the overall health of your vehicle's fuel system.
Cold Weather's Impact: Why Diesel Gels in Fuel Lines
You may want to see also
Final Adjustments and Safety Checks: Verify the fuel line's functionality and stability before driving
After completing the initial steps of rebuilding the metal fuel line, it's crucial to perform final adjustments and safety checks to ensure the system is reliable and secure. This process involves verifying the functionality and stability of the fuel lines to prevent any potential issues while driving. Here's a detailed guide on how to approach these final checks:
Inspect for Leaks: Start by checking for any signs of fuel leaks. Turn on the car's engine and listen for any hissing or dripping sounds around the fuel lines. You can also use a soapy water solution to carefully inspect the lines for bubbles, indicating a leak. Ensure that all connections are tight and secure, as loose fittings can lead to fuel escaping into the wrong areas.
Test the Fuel Pressure: Check the fuel pressure to ensure it meets the manufacturer's specifications. You can use a fuel pressure gauge to measure the pressure at the fuel rail or injectors. Low fuel pressure might indicate a restricted line or a problem with the fuel pump. Adjust the pressure regulator or consider replacing the fuel pump if necessary.
Stability and Vibration: Drive the vehicle at varying speeds and pay close attention to the fuel lines. They should remain stable and secure, with no excessive movement or vibration. Check for any rattling or loose connections that might occur during acceleration or deceleration. Ensure that the fuel lines are properly supported and routed to avoid damage from vibrations.
Final Functionality Check: Before driving, start the engine and let it idle for a few minutes. Observe the fuel gauge and ensure it reads the correct fuel level. Check for any unusual noises, such as hissing or roaring, which could indicate air bubbles or fuel line issues. Start the car and drive it for a short distance, monitoring the performance and fuel consumption. The vehicle should respond normally, indicating that the fuel lines are functioning correctly.
Documentation and Record-Keeping: Document the entire rebuilding process, including any parts replaced or adjusted. Keep a record of the fuel line's performance and stability after these final checks. This documentation can be useful for future reference, especially if any issues arise, allowing for quicker identification and resolution.
By following these final adjustments and safety checks, you can ensure that the metal fuel line is rebuilt to a high standard, providing a safe and efficient fuel supply to the engine. It is essential to take the time for these checks to prevent potential hazards on the road.
Fuel Line Cleaning: A Step-by-Step Guide for Your Lawn Mower
You may want to see also
Frequently asked questions
Metal fuel lines can corrode, crack, or develop leaks due to factors like age, exposure to fuel contaminants, temperature fluctuations, and mechanical damage.
Look for signs like fuel leaks, engine misfires, reduced performance, or strange noises. If you notice any of these issues, it's best to inspect the fuel line for damage.
Rebuilding a metal fuel line can be a complex task and often requires specialized tools and knowledge. It's recommended to consult a professional mechanic or automotive specialist to ensure a proper repair.
You'll typically need a fuel line cutter, crimping tools, new fuel line (compatible with your vehicle's specifications), fuel line connectors, and possibly a fuel line inspection camera for visual assessment.
Absolutely! Always work on a level surface, wear protective gear, and ensure proper ventilation. Before starting any repair, turn off the fuel supply and drain the system to avoid fuel spills and potential hazards.