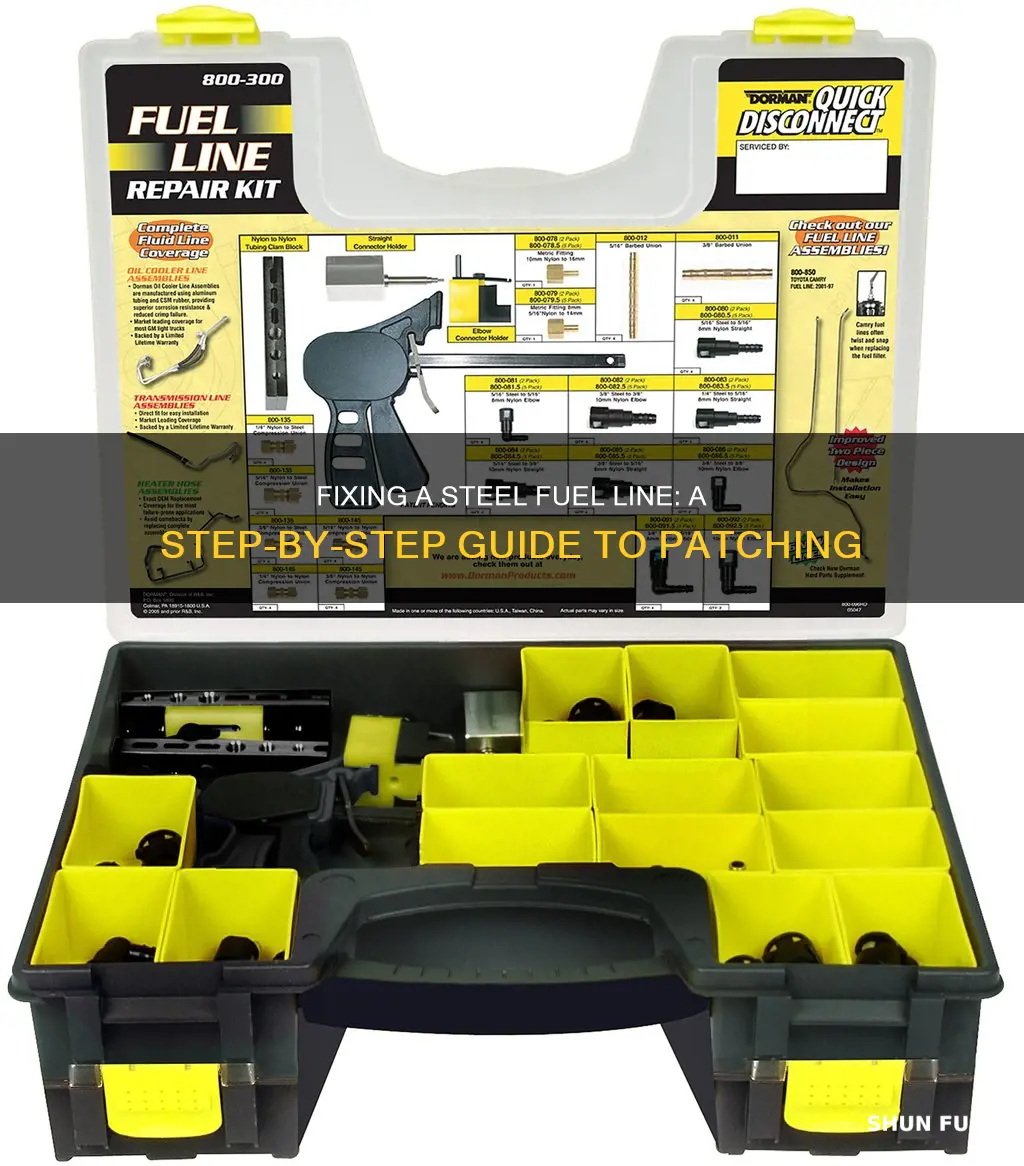
Patching a steel fuel line is a crucial task for maintaining the integrity of your vehicle's fuel system. Whether you're dealing with a small puncture or a larger tear, it's essential to follow a systematic approach to ensure a secure and reliable repair. This guide will provide a step-by-step process, including the necessary tools and materials, to help you effectively patch a steel fuel line, ensuring your vehicle's performance and safety.
What You'll Learn
- Prepare the Tools: Gather necessary tools like a fuel line repair kit, cutting torch, and flux
- Cut and Prepare: Carefully cut the damaged line and clean the ends
- Prepare the Patch: Apply flux to the pipe ends and insert the patch
- Solder or Weld: Use a soldering iron or torch to secure the patch
- Test and Inspect: Check for leaks and ensure the connection is secure
Prepare the Tools: Gather necessary tools like a fuel line repair kit, cutting torch, and flux
Before you begin the process of repairing a steel fuel line, it's crucial to gather the necessary tools and materials to ensure a successful and safe fix. Here's a step-by-step guide on preparing your toolkit:
Fuel Line Repair Kit: This kit is specifically designed for fuel line repairs and should include all the essential components you need. Look for a kit that provides a range of sizes to accommodate different fuel line diameters. It typically consists of various types of fittings, such as compression fittings, quick-connect fittings, or clamp-style fittings, along with the corresponding gaskets or seals. Ensure the kit includes the appropriate fittings for your fuel line's specifications.
Cutting Torch: A cutting torch is an indispensable tool for this task. It allows you to precisely cut the damaged section of the fuel line. Opt for a torch with adjustable flame settings to control the heat and ensure clean, straight cuts. When choosing a torch, consider the power and portability that suit your needs. A butane or propane-powered torch with a fine tip is ideal for working in tight spaces and making delicate cuts.
Flux: Flux is a crucial component in the repair process as it helps to create a strong bond between the new fitting and the fuel line. It is applied to the cut ends of the fuel line and the fitting before assembly. Look for a flux suitable for steel surfaces, as it should be compatible with the material of your fuel line. Ensure you have enough flux to cover the entire cut area and any additional areas where connections will be made.
Additionally, consider having a set of pliers, a wire brush, and a safety gear like gloves and goggles readily available. These tools will aid in preparing the fuel line, removing any debris, and ensuring a secure connection. By gathering these items, you'll be well-prepared to tackle the fuel line repair with the right equipment at hand.
Unraveling the Mystery: Chainsaw Fuel Lines Explained
You may want to see also
Cut and Prepare: Carefully cut the damaged line and clean the ends
When dealing with a damaged steel fuel line, the first step is to carefully assess the situation and prepare the necessary tools and materials. Start by gathering a sharp, clean pair of cutting shears or a utility knife specifically designed for cutting metal. Ensure the blade is in good condition to make precise cuts. Additionally, have a pair of pliers or a pair of metal-cutting gloves to assist with the cutting process.
Locate the damaged section of the fuel line and identify the point where it needs to be cut. Mark the spot with a permanent marker or a piece of tape to ensure you cut at the right location. It's crucial to cut the line at a 90-degree angle to ensure a secure connection later. Use the marked spot as a guide to make a clean, straight cut. Apply gentle pressure to the shears or knife, taking care not to apply excessive force that might distort the cut.
Once the damaged section is cut, it's essential to clean the ends of the fuel line. Use a wire brush or a small wire brush attachment on a power tool to remove any debris, rust, or old fuel residue from the cut ends. This step ensures a clean and smooth surface for the patch to adhere to. Be thorough in your cleaning, ensuring no contaminants remain.
After cleaning, inspect the cut ends for any remaining damage or imperfections. If there are any sharp edges or burrs, carefully file them down using a small file or a sandpaper block. This step is crucial to prevent the patch from catching or snagging on the fuel line during installation. Ensure the ends are smooth and free of any debris before proceeding.
With the cut and cleaned ends prepared, you're now ready for the next step, which is to apply the patch or repair material. This process will be detailed in the subsequent steps of the guide.
Honda Civic Fuel Line Location: A Comprehensive Guide
You may want to see also
Prepare the Patch: Apply flux to the pipe ends and insert the patch
Before you begin the patching process, it's crucial to ensure that the fuel line is clean and free of any debris or contaminants. Start by disconnecting the fuel line from the source and the receiving component. Use appropriate tools to carefully separate the line without causing any damage to the surrounding components. Once disconnected, inspect the interior of the fuel line for any signs of corrosion, pitting, or damage. This step is essential to identify the exact location and extent of the issue.
Next, you'll need to prepare the pipe ends for the patch. Apply a generous amount of flux to both ends of the fuel line. Flux is a chemical compound that helps to remove oxidation and create a clean surface for the patch to adhere to. Ensure that the flux is evenly distributed and covers the entire area where the patch will be inserted. Allow the flux to act according to the manufacturer's instructions, which may involve waiting for a specific duration to ensure optimal results.
While the flux is setting, take this time to prepare the patch. A steel patch, also known as a sleeve or wrap, is typically made of a compatible steel alloy. Measure and cut the patch to fit the damaged section of the fuel line, ensuring it is slightly longer than the affected area. The patch should be wider than the fuel line to provide a secure grip. Prepare the patch by cleaning it with a solvent to remove any oils or contaminants, ensuring a clean surface for bonding.
Once the flux has set, it's time to insert the patch. Carefully align the patch over the prepared pipe ends, ensuring it is centered and properly positioned. Apply pressure evenly along the length of the patch to ensure a tight fit. You can use a tool like a mallet or a dedicated patch-installing tool to help with this process. The goal is to create a secure bond between the patch and the fuel line, so take your time and apply the necessary force without causing any damage.
After inserting the patch, inspect the connection to ensure it is secure and properly aligned. Test the fuel line by reconnecting it to the source and receiving component, and then slowly filling the line with fuel. Check for any leaks around the patch area, and if none are found, you've successfully patched the steel fuel line. This method provides a reliable and long-lasting solution, ensuring the fuel line's integrity and functionality.
Dodge Cummins Fuel Line Removal: A Step-by-Step Guide
You may want to see also
Solder or Weld: Use a soldering iron or torch to secure the patch
When dealing with a damaged steel fuel line, one of the most effective methods to ensure a secure and long-lasting repair is by using a soldering or welding technique. This process involves heating the patch or replacement section to a precise temperature, allowing it to melt and bond with the surrounding metal. Here's a step-by-step guide on how to achieve this:
Preparation: Begin by ensuring you have the necessary tools and materials. You'll need a soldering iron or a gas-powered torch, flux (a cleaning agent to remove oxidation), a suitable solder or welding rod, and a pair of heat-resistant gloves for protection. Clean the damaged area of the fuel line thoroughly to remove any dirt or corrosion.
Applying Flux: Flux is a crucial step as it prepares the metal surface by removing any oxide layer that might interfere with the bonding process. Apply a small amount of flux to the area where the patch will be placed. This step ensures a strong and reliable connection.
Heating and Soldering/Welding: Now, for the application of heat. If using a soldering iron, hold it at a steady angle against the patch, applying heat for a few seconds until the metal begins to glow. Then, quickly add the solder, ensuring it melts and forms a bead. For welding, light the torch and adjust the flame to a controlled heat, then carefully place the patch over the damaged section and apply the flame. Keep the heat source in contact with the metal for a sufficient duration to melt the patch and create a strong bond.
Cooling and Inspection: After the patch is secured, allow the area to cool slowly. Rapid cooling can cause stress on the bond. Inspect the repair to ensure there are no visible gaps or imperfections. If necessary, reheat and reapply solder or welding to achieve a perfect fit.
Remember, this method requires precision and practice to master. It is essential to follow safety guidelines when using heat sources and to ensure proper ventilation in your workspace. With patience and attention to detail, you can effectively patch a steel fuel line using soldering or welding techniques.
Maximizing Fuel Line Lifespan: Expert Tips for Long-Lasting Performance
You may want to see also
Test and Inspect: Check for leaks and ensure the connection is secure
When it comes to repairing a steel fuel line, thorough testing and inspection are crucial to ensure the integrity and safety of the system. After patching the line, the first step is to check for any potential leaks. Start by applying a small amount of fuel or a suitable leak detection fluid along the patched area. This can be done by carefully injecting the fluid at various points, including the connection where the patch was applied. The fluid will help identify any cracks or imperfections in the patch or the original line. Look for any signs of fuel escaping, which could indicate a leak. If a leak is detected, it's essential to address it immediately.
To ensure a secure connection, inspect the patched area for any visible damage or debris. Use a bright flashlight or a mirror to examine the connection closely. Check for any sharp edges or rough surfaces that might cause the patch to come loose over time. Smooth out any rough spots and ensure that the patch is properly aligned and seated. Tighten the connections securely, but be careful not to overtighten, as this can cause damage. Use the appropriate tools and torque specifications provided by the manufacturer to achieve a secure yet gentle hold.
After ensuring the connections are tight, perform a visual inspection of the entire fuel line system. Look for any signs of corrosion, rust, or damage along the length of the line. Corrosion can weaken the steel and compromise the integrity of the patch. If any issues are found, consider replacing the affected section of the fuel line. Additionally, check for any signs of fuel contamination, such as water accumulation or debris buildup, which can lead to engine problems.
It is also recommended to test the fuel line's pressure and flow. Use a fuel pressure gauge to check for any abnormalities in pressure. Ensure that the fuel flows smoothly through the line without any restrictions. If the pressure or flow is inconsistent, it may indicate a problem with the patch or the surrounding components. Address any issues found during this test to guarantee optimal performance.
Remember, proper testing and inspection are vital to the success of the repair. By following these steps, you can ensure that the patched steel fuel line is secure, leak-free, and ready to function reliably. Always refer to the manufacturer's guidelines and safety instructions when working with fuel lines to ensure a safe and effective repair process.
Fuel Line Leaks: Causes and Solutions for Your Car's Gas Crisis
You may want to see also
Frequently asked questions
Patching a steel fuel line requires a careful approach to ensure a secure and reliable repair. Start by cleaning the damaged area to remove any dirt or debris. Then, use a fuel line repair kit specifically designed for steel lines. These kits typically include a primer, a repair sleeve, and a cement compound. Apply the primer to the affected area, let it dry, and then insert the repair sleeve over the damaged section. Secure it with the provided cement, following the manufacturer's instructions. Finally, wipe away any excess cement and allow the repair to cure according to the kit's guidelines.
While it's not recommended for long-term use, a temporary fix can provide short-term relief. Clean the fuel line and use a piece of rubber or vinyl tubing that is slightly larger in diameter than the damaged area. Secure it in place with mechanical clips or tape. However, this is a temporary solution and should be replaced as soon as possible to avoid potential fuel leaks and further damage.
Absolutely, safety is crucial when dealing with fuel lines. Always wear protective gear, including gloves and safety goggles, to prevent any potential injuries. Ensure you work in a well-ventilated area and avoid sparks or open flames as fuel is highly flammable. It's essential to identify the fuel source and shut it off before starting the repair process. Additionally, be cautious when using any tools or cutting equipment to avoid accidental punctures.