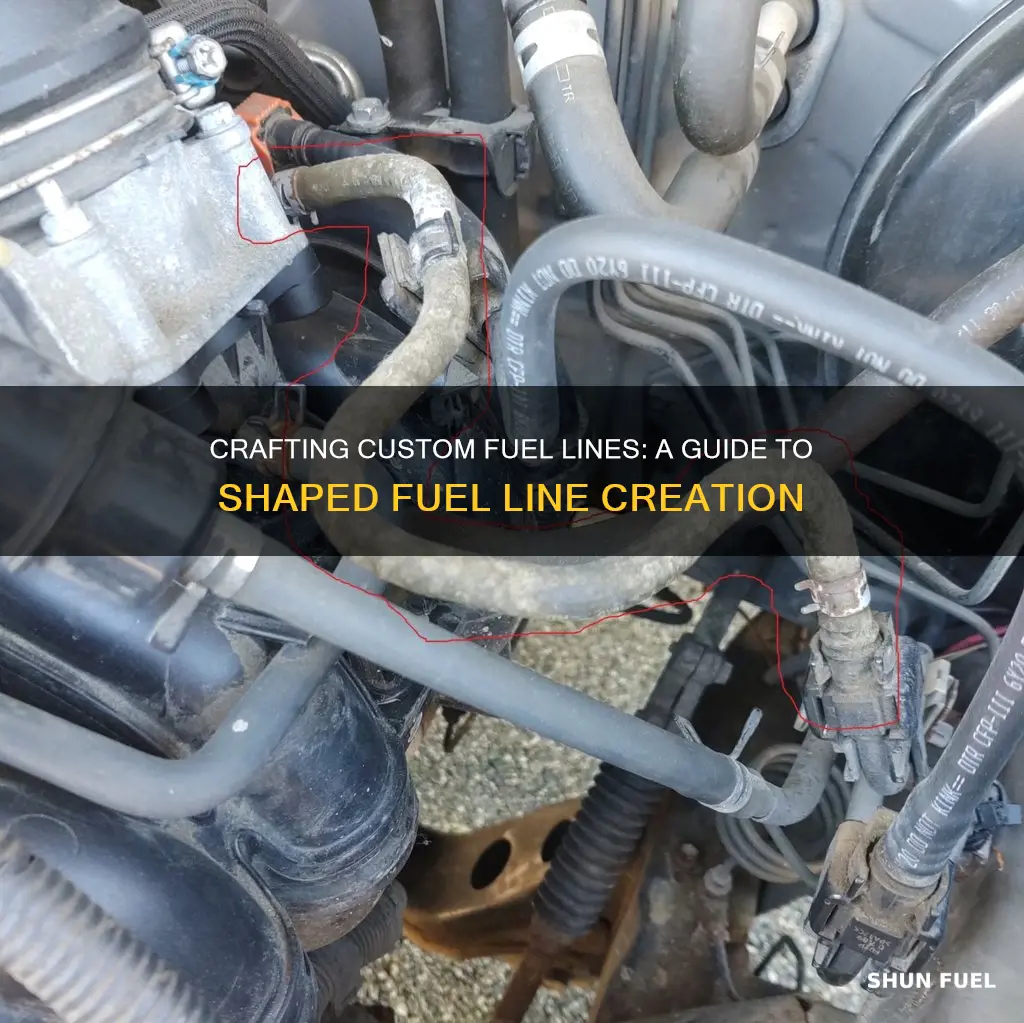
Creating a shaped fuel line is a precise process that requires careful planning and execution. It involves shaping a flexible tube to fit a specific route, often with tight bends and turns, to deliver fuel from a source to an engine or other fuel-consuming device. This task demands attention to detail, as the line must be able to withstand pressure, temperature changes, and potential vibrations while maintaining a secure and efficient connection. The process typically includes selecting the appropriate material, considering the fuel's properties, and ensuring the line is properly sealed and supported to prevent leaks and ensure optimal performance.
What You'll Learn
- Design and Measure: Determine the shape, measure the length, and mark the fuel line
- Prepare Materials: Gather fuel line, fittings, and tools. Ensure compatibility and safety
- Cut and Bend: Use sharp tools to cut and carefully bend the line to shape
- Connect Fittings: Attach fittings securely, ensuring tight seals and proper alignment
- Test and Adjust: Check for leaks, adjust as needed, and ensure optimal performance
Design and Measure: Determine the shape, measure the length, and mark the fuel line
To create a shaped fuel line, the first crucial step is the design and measurement phase. This process involves careful consideration of the desired shape and precise measurements to ensure a well-crafted final product. Here's a detailed guide on how to approach this stage:
Determining the Shape: Begin by envisioning the shape you want your fuel line to take. Consider the purpose and functionality of the line. For example, you might need a curved line for a specific engine component or a straight line for connecting two points. Sketching or visualizing the shape will help you communicate your design effectively. Remember, the shape should be practical and efficient, allowing for easy installation and optimal fuel flow.
Measuring the Length: Accurate measurements are essential to ensure the fuel line fits perfectly. Start by identifying the distance between the two points where the fuel line will be connected. Use a flexible measuring tape or a ruler to measure the length accurately. Take note of any specific requirements, such as the need for extra length to allow for bends or adjustments. Precision is key here to avoid any unnecessary adjustments during the manufacturing process.
Marking the Fuel Line: Once you have the shape and length determined, it's time to mark the fuel line. Use a permanent marker or a specialized fuel line marker to indicate the cut points. Mark the starting and ending points of the line, as well as any bends or turns. Clearly label the sections to ensure that the manufacturing process is straightforward. Consider creating a template or a diagram to guide the cutting and shaping process, especially if you're working with a team.
When marking, ensure that the fuel line material is not damaged. Some materials may require special care, such as avoiding sharp marks that could compromise the line's integrity. Take your time to ensure accuracy, as any mistakes at this stage could lead to costly errors later.
By following these design and measurement steps, you'll have a clear roadmap for creating a shaped fuel line that meets your specific requirements. This initial phase sets the foundation for the rest of the project, ensuring a well-executed and functional fuel line.
Chrysler 300 Fuel Line Routing: A Comprehensive Guide
You may want to see also
Prepare Materials: Gather fuel line, fittings, and tools. Ensure compatibility and safety
When preparing to create a shaped fuel line, the first step is to gather all the necessary materials and tools. This includes the fuel line itself, which is the primary component that will be shaped. It's crucial to choose a fuel line made from high-quality, flexible material that can withstand the demands of the application. Ensure that the length and diameter of the fuel line are suitable for your specific project, considering the distance it needs to cover and the flow rate required. Along with the fuel line, you'll need various fittings to connect and manipulate the line as needed. These fittings should be compatible with the fuel line material and designed for the fuel type you are working with. Common fittings include elbows, tees, reducers, and couplings. Each fitting should be selected based on the desired angle, size, and functionality.
In addition to the fuel line and fittings, you'll require a range of tools to facilitate the shaping process. These tools may include a fuel line cutter or a pair of sharp scissors or knives for precise cuts, ensuring a clean and safe connection. You might also need a fuel line crimping tool or a similar device to secure fittings and create a tight seal. Other essential tools could be a fuel line clamp or tie-down, which will be used to hold the line in place and maintain its shape. It is important to inspect and ensure the compatibility of all these tools with the chosen fuel line and fittings to guarantee a successful and safe installation.
Safety should always be a top priority when working with fuel lines. Before beginning the shaping process, verify that all materials and tools are suitable for the fuel type and application. Different fuels may require specific materials and fittings to prevent leaks and ensure compatibility. For instance, some fuels might require a particular type of fitting or material to avoid corrosion or contamination. Always refer to the manufacturer's guidelines and recommendations for the chosen fuel line and fittings to ensure you are using the correct and safe components.
When gathering your materials, it is beneficial to have a variety of sizes and types of fittings to accommodate different shaping requirements. Consider the angles and bends you need to create and select fittings accordingly. Having extra fuel line and fittings on hand can be advantageous for making adjustments or creating backups during the shaping process. Additionally, ensure that all tools are in good working condition to avoid any potential hazards or mistakes due to malfunctioning equipment.
By carefully preparing and gathering the necessary materials and tools, you set the foundation for a successful and safe shaped fuel line project. This initial step is crucial to ensure that you have everything required to complete the task efficiently and effectively, while also prioritizing safety throughout the entire process.
BMW X5 E53 Fuel Line Connection: A Step-by-Step Guide
You may want to see also
Cut and Bend: Use sharp tools to cut and carefully bend the line to shape
When it comes to shaping a fuel line, the process of cutting and bending is crucial to ensure a precise and secure fit. This step requires a steady hand and the right tools to avoid any damage to the fuel line or the surrounding components. Here's a detailed guide on how to achieve this:
Tools and Materials:
Start by gathering the necessary tools: sharp scissors or a utility knife, a pair of pliers, and a fuel line bending tool (optional but recommended for easier bending). Ensure you have the right size and type of fuel line for your specific application.
Cutting the Fuel Line:
- Lay out the fuel line on a flat surface and measure the desired length. Mark the cut line with a permanent marker or a piece of tape to guide your cut.
- Using sharp scissors or a utility knife, carefully cut along the marked line. Precision is key here; a clean cut will ensure a better finish and reduce the risk of any sharp edges causing damage.
- If the cut is not straight, use a file or sandpaper to smooth the edges, creating a neat and even surface.
Bending the Fuel Line:
- Now, it's time to shape the fuel line. Decide on the desired curvature or angle, keeping in mind the space available and the function of the line.
- Hold the fuel line at the bend point and use the pliers to apply gentle pressure and create a bend. For tighter bends, you might need to use the bending tool to get a precise shape.
- Take your time with each bend, ensuring the line remains intact and doesn't kink or twist. Practice and patience are essential here.
- If you need to make multiple bends, repeat the process, ensuring each bend is in the correct direction to achieve the desired shape.
Safety and Precision:
- Always work in a well-ventilated area when handling fuel lines to avoid inhaling any fumes.
- Take your time with each cut and bend, as rushing can lead to mistakes.
- Double-check your measurements and angles before finalizing each cut and bend to ensure the overall design is correct.
By following these steps, you can create a shaped fuel line that fits perfectly into your intended application, ensuring a safe and efficient fuel delivery system. Remember, practice makes perfect, and with the right tools and patience, you'll be able to master the art of shaping fuel lines.
Fixing a Fuel Line: A Step-by-Step Guide for Your 2002 Ford Taurus
You may want to see also
Connect Fittings: Attach fittings securely, ensuring tight seals and proper alignment
When connecting fittings to create a shaped fuel line, it's crucial to prioritize security and functionality. Here's a step-by-step guide to ensure a robust and reliable connection:
Prepare the Fittings: Begin by ensuring you have the appropriate fittings for your specific fuel line application. Consider the material compatibility and the required pressure rating. Clean the fittings thoroughly to remove any debris or contaminants that could interfere with the connection.
Apply Thread Sealant: If the fittings have threads, apply a generous amount of thread sealant (also known as pipe compound) to the male threads. This step is essential to create a tight seal and prevent fuel leaks. Allow the sealant to dry slightly before proceeding.
Connect the Fittings: Take one fitting and align it with the corresponding end of the fuel line. Start threading the fitting onto the fuel line, ensuring it is straight and secure. Use a wrench or spanner to tighten the fitting firmly, but be careful not to overtighten, as this can damage the threads or fuel line. The connection should be snug, with no visible gaps.
Check for Leaks: After tightening, inspect the connection for any signs of leakage. Apply a small amount of fuel to the connection and observe if any fuel drips or seeps out. If you notice any leaks, tighten the fitting further or reapply thread sealant. Ensure that all connections are tight and secure.
Proper Alignment: Maintain proper alignment of the fittings to avoid any potential issues. The fittings should be straight and not bent or twisted, as this can lead to fuel line damage or reduced performance. Use a straightedge or a ruler to verify the alignment, especially when connecting multiple fittings to create the desired shape.
Testing and Inspection: Once all fittings are connected, test the fuel line for any pressure drops or leaks. Use a pressure gauge to check for any abnormalities. Inspect the entire length of the fuel line for any visible damage or loose connections. This thorough inspection ensures the safety and efficiency of your shaped fuel line system.
Rally Racing Rules: Fuel Lines Allowed or Forbidden?
You may want to see also
Test and Adjust: Check for leaks, adjust as needed, and ensure optimal performance
When you've crafted your shaped fuel line, it's crucial to thoroughly test and adjust it to ensure optimal performance and safety. The first step is to check for any leaks. Start by applying a small amount of fuel to the line and observing if there are any signs of leakage. You can use a soapy water solution or a specialized fuel leak detector to make this process easier. If you notice any bubbles forming or a sudden drop in pressure, it indicates a potential leak. In such cases, carefully inspect the connections and joints, tightening any loose fittings and replacing any damaged components. Ensure that all connections are secure and free from corrosion.
After confirming that there are no leaks, it's time to adjust the line's shape and positioning. Consider the vehicle's engine requirements and the optimal fuel flow path. You might need to modify the line's route to accommodate engine components or ensure it doesn't interfere with other parts. Use flexible fuel line materials that can be bent and shaped without compromising integrity. Take note of any tight spaces or angles that might affect the line's performance, and make the necessary adjustments.
Performance testing is the next critical step. Start the engine and monitor its behavior, checking for any unusual noises or vibrations that could indicate issues with the fuel line. Ensure that the engine idles smoothly and responds promptly to acceleration and deceleration commands. Pay attention to fuel consumption and engine performance metrics to ensure they meet or exceed the manufacturer's specifications. If you notice any deviations, you may need to make further adjustments.
Adjustments might include fine-tuning the fuel line's length or positioning to optimize fuel delivery. This could involve slightly altering the line's angle or using different mounting techniques. It's important to strike a balance between a secure fit and allowing for engine movement during operation. Regularly check the fuel line's condition during these adjustments to ensure it remains intact and free from damage.
Finally, maintain a record of all the adjustments made and the corresponding performance outcomes. This documentation will be invaluable for future reference, helping you quickly identify and rectify any issues. By following this systematic approach, you can ensure that your shaped fuel line is not only functional but also safe and efficient, contributing to the overall performance of your vehicle.
Mastering Fuel Return: A Step-by-Step Guide to Adding a Line
You may want to see also
Frequently asked questions
The choice of material depends on the specific application and environmental factors. For fuel lines, commonly used materials include stainless steel, brass, or fuel-resistant rubber hoses. Stainless steel is durable and suitable for high-temperature environments, while brass offers good corrosion resistance. Rubber hoses are flexible and often used for their cost-effectiveness.
To achieve a secure connection, you should use appropriate fittings and ensure a tight seal. For metal fuel lines, use compression fittings or quick-connect couplings designed for fuel applications. For rubber hoses, ensure a proper fit and consider using a fuel-resistant adhesive or tape to reinforce the connection. Regularly inspect and replace connections to prevent leaks.
While it is possible to bend fuel lines to some extent, it should be done with caution. Fuel lines are designed to withstand pressure and temperature changes, but excessive bending can compromise their integrity. A common technique is to use a fuel line bender, which allows you to create smooth, consistent bends. It's important to follow the manufacturer's guidelines for the specific fuel line material and to avoid sharp bends that could lead to stress points.