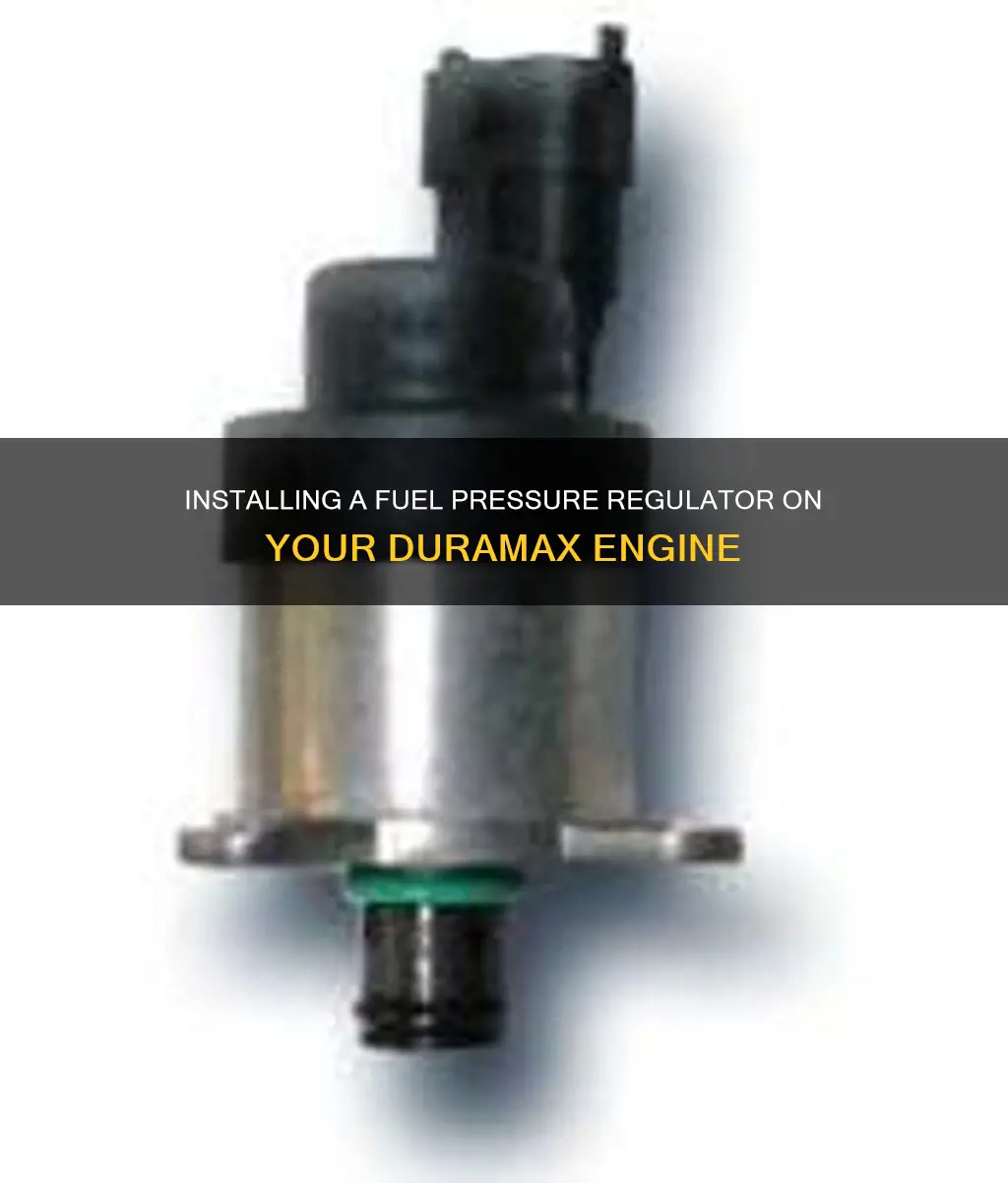
Installing a fuel pressure regulator on a Duramax engine can be a challenging task, but with the right tools and guidance, it is certainly achievable. The process involves disconnecting sensors, removing and replacing various engine components, and ensuring that the work area is clean and free of debris. It is important to note that different models of Duramax engines may have slight variations in the installation process, so it is always recommended to refer to a repair manual specific to your vehicle. Additionally, working with fuel system components can be dangerous, so proper safety precautions should be taken at all times.
Characteristics | Values |
---|---|
Difficulty level | Not all that bad, but time-consuming |
Required tools | T25 TORX, 3-inch Torx bit and a 1/4 wrench, DeWalt 6-inch Torx T25 bit, 10mm, 15mm, pliers, zip ties, rags, corks, air compressor tip, 8mm wrench, 1/4" open wrench, screwdriver bit extension, long screwdriver, 13mm socket, 10mm socket, 3/8" socket swivel adapter, 3/8" extension, 1/4" breaker-bar, needle-nose pliers, magnet wand, etc. |
Parts to remove | Sensors, air intake pipe, drive belt, water outlet tube, main harness electrical connectors, etc. |
Parts to disconnect | A/C compressor clutch electrical connector, A/C cut-out switch electrical connector, etc. |
What You'll Learn
Disconnect sensors and remove bolts to access the fuel pressure regulator
Disconnecting sensors and removing bolts is a crucial step in accessing and replacing the fuel pressure regulator in your Duramax engine. Here's a detailed guide on how to go about it:
Disconnecting Sensors:
- Start by removing the air intake pipe.
- Disconnect the air conditioning (A/C) compressor clutch electrical connector.
- Disconnect the A/C cut-out switch electrical connector.
- Disconnect both main harness electrical connectors.
- Disconnect the engine coolant temperature (ECT) sensor electrical connector.
- Disconnect the barometric pressure (BARO) sensor electrical connector.
- Disconnect the glow plug relay electrical connectors.
- Disconnect the fuel rail temperature sensor electrical connector.
- Disconnect the left front and rear fuel injector electrical connectors.
- Disconnect the fuel pressure regulator electrical connector.
- Disconnect the oil level sensor harness electrical connector.
Removing Bolts:
- Remove the drive belt by loosening the tensioner with a breaker bar.
- Remove the A/C compressor bolts. You can move the compressor aside with the hoses still attached.
- Remove the water outlet tube bolts.
- Remove the main harness electrical connector to bracket bolts.
- Using a T25 TORX®, remove the three fuel pressure regulator screws.
It is important to clean the area around the fuel pressure regulator and high-pressure injection pump with solvent and blow it dry with compressed air before beginning the removal process. This will help prevent debris from falling into the engine. Additionally, some people find it helpful to use a small piece of paper towel over the T25 bit to keep the screws from falling.
Once the sensors are disconnected and the bolts removed, you will be able to access and replace the fuel pressure regulator. Remember to work carefully and consult a mechanic or a detailed guide if you are unsure about any steps.
Best Fuel Options for 2700 PSI Pressure Washers
You may want to see also
Clean the area and use compressed air to dry it
Before removing the fuel pressure regulator, it is important to clean the regulator and the high-pressure injection pump thoroughly with a suitable solvent. This will ensure that any dirt or debris is removed from the components before they are worked on.
Once cleaned, the regulator and pump should be thoroughly dried with compressed air. This will ensure that no solvent or moisture remains on the components, which could cause issues during the installation process or affect the performance of the fuel system.
It is important to note that compressed air should not be used to remove debris while the fuel pressure regulator is removed, as this could cause dirt or debris to enter the fuel system. Instead, a clean rag should be used to collect excess fuel, and the engine should be bumped over to flush out any remaining debris.
High-Performance BMW 335i: Choosing the Right Fuel Pump
You may want to see also
Remove and replace the fuel pressure regulator
To remove and replace the fuel pressure regulator on a Duramax engine, follow these steps:
Removal:
- Disconnect the negative feed from the batteries.
- Using a 1/2" breaker bar, remove the belt from the pulleys by placing the bar into the square socket on the belt tensioner. Push it towards the passenger side and lift it off the AC compressor unit.
- Remove the air intake. Loosen the three hose clamps to do this.
- Disconnect the two connectors on the AC unit.
- Take out the four bolts that mount the AC unit to the engine. Move the AC unit out of the way by flipping it towards the passenger side battery.
- Using a sharp object, open the clip that holds the wire harness together.
- Remove the red bolt from the thermostat housing and set the bracket aside.
- Take out the two bolts that hold the metal piping to the engine.
- Using a 13mm socket, remove the four bolts at the front.
- Loosen the hose clamp on the coolant pipe.
- Insert a straight pick into the hose end and move it around the circumference of the pipe to break the connection.
- Pull the hose off the pipe and wedge it against the brake cylinder and the fuse box.
- Lift the pipe off the engine and flip it towards the turbo.
- Disconnect the sensor on the manifold to access a 10mm bolt.
- Using a swivel socket and/or a 10mm wrench, remove the three bolts on the inlet horn.
- Disconnect the FPR connector.
- Using pliers, remove the two fuel line clamps.
- Remove the three bolts from the FPR/CP3.
Installation:
- Use a dab of weatherstrip and gasket sealer on the bolt so you can place it in the lower hole.
- Once the sealer dries, you can pick it out or leave it in so you can pull the "plug" out if needed in the future.
- Reassemble everything in reverse order of removal.
- You may need to tune the FPR if you installed a non-LB7 version.
Note: It is recommended to spray some penetrating oil on the bolts before removal and to clean the bolt heads so that your bit seats completely and you don't strip them out.
Cleaning Fuel Pump Pressure: Tips and Tricks
You may want to see also
Reassemble the engine components in reverse order
To reassemble the engine components in reverse order, follow these steps:
- Reinstall the fuel pressure regulator electrical connector.
- Reconnect the left rear fuel injector electrical connector.
- Reconnect the left front fuel injector electrical connector.
- Reconnect the fuel rail temperature sensor electrical connector.
- Reconnect the glow plug relay electrical connectors.
- Reconnect the barometric pressure (BARO) sensor electrical connector.
- Reconnect the engine coolant temperature (ECT) sensor electrical connector.
- Reinstall the main harness electrical connector to the bracket.
- Reinstall the main harness electrical connector bracket bolts.
- Reinstall the water outlet tube.
- Reinstall the drive belt.
- Reconnect the air conditioning (A/C) compressor clutch electrical connector.
- Reinstall the air intake pipe.
- Reinstall the injection pump inlet hose to the fuel feed distribution (leak-off) block.
- Reposition the positive crankcase ventilation (PCV) hose to both valve covers.
- Reinstall the oil level sensor harness electrical connector.
- Reinstall the third fuel pressure regulator screw using a T25 TORX®.
- Reinstall the remaining two fuel pressure regulator screws.
- Reinstall the A/C compressor bolts.
- Reinstall the air intake pipe.
- Reconnect the air conditioning (A/C) compressor clutch electrical connector.
- Reinstall the drive belt.
- Reconnect the engine coolant temperature (ECT) sensor electrical connector.
- Reconnect the barometric pressure (BARO) sensor electrical connector.
- Reconnect the glow plug relay electrical connectors.
- Reconnect the left front fuel injector electrical connector.
- Reconnect the left rear fuel injector electrical connector.
- Reconnect the fuel rail temperature sensor electrical connector.
- Reinstall the fuel pressure regulator.
- Thoroughly clean the fuel pressure regulator and high-pressure injection pump with a suitable solvent.
- Blow-dry the regulator and pump using compressed air.
- Reinstall the injection pump inlet hose to the fuel feed distribution (leak-off) block.
- Reposition the positive crankcase ventilation (PCV) hose to both valve covers.
- Reinstall the oil level sensor harness electrical connector.
- Reinstall the A/C cut-out switch electrical connector.
- Reinstall the air intake pipe.
Fuel Pressure Maintenance for 2000 Civic HX
You may want to see also
Tuning may be required after installation
> I did not do the tuning myself but I'm just going to include a simple step for those with EFIlive access. I had mine done by Ryan's Diesel Service in Waukesha, Wisconsin. So this means that the following step is untested and I acquired it from Dieselplace.com.
>
> will a lbz regulator work in an 2003 lb7? - Page 3 - Diesel Place : Chevrolet and GMC Diesel Truck Forums ok, i have tested these numbers a little and i am very comfortable sharing them. I used 2 sheets of paper and worked out the numbers to be within specs. I basicly took the sections of an LMM Regulator and worked myu formula to find out how many mm3 equaled 1 mv ..... I left the bottom at 400 as that was the minimum number shown on both scales .... I currently have no surging anywhere, smooth clean idle, no unneccessary clacking .... 1 thing to remember... the purpose of the LBZ or LMM regulator is to increase flow ... i am not sure if this table will allow you to increase flow. My numbers are basicly matched to a LB7 regulator. With that in mind it' pretty much flowing the same as an LB7 at any desired area. To bypass this it may be advisable to only adjust the top sections with my numbers .... and leave the stock lb7 in line towards the bottom. By doing this, you will be flowing more fuel through. It's basicly the lower the number, the more fuel ... this is just my ramblings ... take it for what it's worth..... B1010 1550 1505 1460 1421 1395 1382 1369 1356 1344 1331 1318 1305 1292 1194 1109 1025 874 644 400 Stock LMM Table -1830 1700 0 1550 1115 1500 2230 1450 3570 1400 11390 1300 19420 1200 28890 1100 38430 1000 51720 700 53210 400 Stock LB7 Table 0 1500 1000 1351 2000 1279 3000 1236 4000 1194 5000 1157 6000 1120 7000 1088 8000 1056 9000 1020 10000 1000 11000 993 12000 986 20000 930 28000 878 36000 826 44000 770 52000 601 60000 400
If you installed an LBZ FPR on your LB7, you will need to tune your truck. This can be done with EFIlive access. Below is a simple step for those with EFIlive access.
> ok, i have tested these numbers a little and i am very comfortable sharing them. I used 2 sheets of paper and worked out the numbers to be within specs. I basicly took the sections of an LMM Regulator and worked myu formula to find out how many mm3 equaled 1 mv ..... I left the bottom at 400 as that was the minimum number shown on both scales .... I currently have no surging anywhere, smooth clean idle, no unneccessary clacking .... 1 thing to remember... the purpose of the LBZ or LMM regulator is to increase flow ... i am not sure if this table will allow you to increase flow. My numbers are basicly matched to a LB7 regulator. With that in mind it' pretty much flowing the same as an LB7 at any desired area. To bypass this it may be advisable to only adjust the top sections with my numbers .... and leave the stock lb7 in line towards the bottom. By doing this, you will be flowing more fuel through. It's basicly the lower the number, the more fuel ... this is just my ramblings ... take it for what it's worth..... B1010 1550 1505 1460 1421 1395 1382 1369 1356 1344 1331 1318 1305 1292 1194 1109 1025 874 644 400 Stock LMM Table -1830 1700 0 1550 1115 1500 2230 1450 3570 1400 11390 1300 19420 1200 28890 1100 38430 1000 51720 700 53210 400 Stock LB7 Table 0 1500 1000 1351 2000 1279 3000 1236 4000 1194 5000 1157 6000 1120 7000 1088 8000 1056 9000 1020 10000 1000 11000 993 12000 986 20000 930 28000 878 36000 826 44000 770 52000 601 60000 400
Fuel Pump Pressure: 67 Mustang Maintenance Guide
You may want to see also
Frequently asked questions
You will need a T25 Torx screwdriver bit, a 1/4-inch wrench, a 1/2-inch breaker bar, a 15mm socket, a 10mm socket, a 13mm socket, a 3/8-inch socket swivel adapter, a 3/8-inch extension, and a long screwdriver.
Loosen the three hose clamps and then twist and pull the assembly from the engine side.
Disconnect the two electrical connectors and then remove the four bolts that mount it to the engine. Move the A/C compressor out of the way.
Open the clip that holds the wire harness and then remove the red bolt from the thermostat housing. Remove the two bolts that hold the metal piping to the engine, and then the four bolts on the coolant pipe. Loosen the hose clamp and then remove the hose.
Disconnect the sensor on the manifold and then use a swivel socket and/or a 10mm wrench to remove the three bolts on the inlet horn.