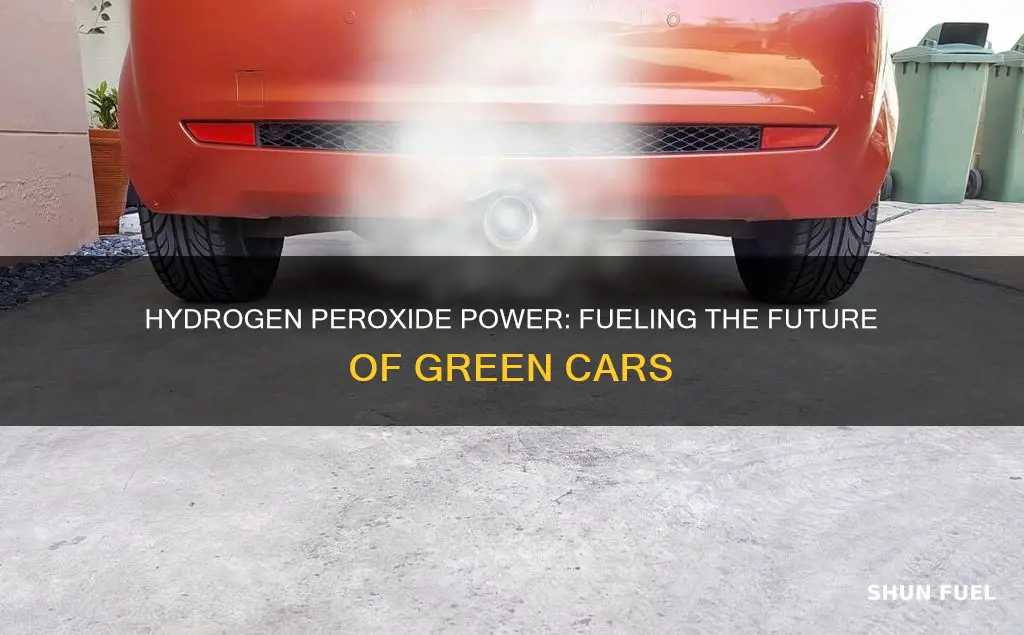
Hydrogen peroxide cars are an innovative concept in the automotive industry, utilizing the powerful oxidizer hydrogen peroxide as a fuel source. To power these vehicles, a complex process is required to extract energy from the chemical reaction between hydrogen peroxide and a catalyst, typically a metal such as platinum. This reaction produces water, oxygen, and a significant amount of energy, which can be harnessed to drive the car's engine. The challenge lies in developing efficient and safe systems to manage the high-pressure and highly reactive nature of hydrogen peroxide, ensuring a sustainable and practical alternative to traditional combustion engines.
What You'll Learn
- Hydrogen Peroxide Production: Extract and purify hydrogen peroxide from various sources
- Fuel Cell Design: Engineer efficient fuel cells for peroxide-based vehicles
- Storage and Handling: Develop safe methods for storing and transporting hydrogen peroxide
- Engine Optimization: Modify engines to utilize hydrogen peroxide as a power source
- Safety Protocols: Establish guidelines for safe operation and maintenance of peroxide cars
Hydrogen Peroxide Production: Extract and purify hydrogen peroxide from various sources
The process of extracting and purifying hydrogen peroxide from various sources is a fascinating and crucial aspect of producing a fuel for cars. Here's an overview of the methods involved:
Source Identification: The first step is to identify suitable sources of hydrogen peroxide. This can be achieved through natural processes or industrial production. One common natural source is the decomposition of certain organic compounds, such as the breakdown of plant materials or even some bacteria. For industrial-scale production, various methods are employed, including the electrolysis of dilute sulfuric acid or the oxidation of isopropanol.
Extraction Techniques: Depending on the source, different extraction methods can be applied. For instance, if you're working with natural materials, you might use distillation or extraction with organic solvents to separate hydrogen peroxide from other compounds. In industrial settings, large-scale distillation columns are often used to separate hydrogen peroxide from the reaction mixture. This process involves heating the mixture to vaporize the hydrogen peroxide, which is then condensed and collected.
Purification Process: Purification is critical to ensure the hydrogen peroxide is of high quality and safe for use as a fuel. One common purification technique is crystallization, where the hydrogen peroxide is dissolved in a solvent and then cooled to encourage the formation of crystals. These crystals can then be filtered and dried to obtain pure hydrogen peroxide. Another method is absorption, where impurities are removed by passing the hydrogen peroxide through a suitable adsorbent material.
Quality Control: After purification, rigorous testing and analysis are essential. This includes checking the concentration of hydrogen peroxide using titration or refractometry. Impurity levels should be measured to ensure they meet the required standards. Additionally, the physical and chemical properties of the purified hydrogen peroxide, such as its boiling point and stability, should be evaluated to guarantee its effectiveness as a fuel.
By following these steps, it is possible to produce high-quality hydrogen peroxide for use in alternative fuel applications, including the innovative concept of hydrogen peroxide-powered cars. This process requires careful planning, the right equipment, and a deep understanding of chemical processes to ensure safety and efficiency.
Biofuels: The Sustainable Alternative for Your Car's Engine
You may want to see also
Fuel Cell Design: Engineer efficient fuel cells for peroxide-based vehicles
The design of fuel cells for peroxide-based vehicles is a specialized field that requires a deep understanding of electrochemistry and materials science. These fuel cells must efficiently convert the chemical energy of hydrogen peroxide into electrical power while ensuring safety and reliability. Here's an overview of the key considerations and steps in engineering efficient fuel cells for such vehicles:
- Electrolyte Selection: The heart of a fuel cell is the electrolyte, which facilitates the movement of ions between the anode and cathode. For peroxide-based fuel cells, a suitable electrolyte must be chosen to withstand the corrosive nature of hydrogen peroxide. Common choices include alkaline electrolytes like potassium hydroxide (KOH) or alkaline earth metal salts, which provide a stable environment for the electrochemical reactions.
- Catalysts and Anode Design: Catalysts play a critical role in facilitating the oxidation of hydrogen peroxide at the anode. Platinum (Pt) is often used as a catalyst due to its high activity and stability. The anode design should promote efficient mass transfer of hydrogen peroxide and electrons. A porous structure with a high surface area can enhance the contact between the catalyst and the reactants, improving overall performance.
- Cathode Configuration: At the cathode, oxygen from the air is reduced to form water. A catalyst like platinum or a platinum-based alloy can be used here as well. The cathode design should ensure good gas diffusion and proper water management to prevent flooding, which can hinder performance.
- Membrane Technology: A proton-conducting membrane is essential to separate the anode and cathode compartments while allowing protons to pass through. The choice of membrane material is crucial. Polymers like perfluorinated sulfonic acid (PFSA) or sulfonated polyetheretherketone (SPEEK) are commonly used due to their proton conductivity and chemical stability.
- System Integration and Optimization: Efficient fuel cell design also involves integrating various components, including pumps, sensors, and control systems. Engineers must ensure proper heat management to prevent overheating, as hydrogen peroxide decomposition can release significant heat. Additionally, optimizing the fuel cell's geometry and flow rates can maximize energy output and minimize losses.
- Safety and Reliability: Given the potential hazards associated with hydrogen peroxide, safety is paramount. Engineers must implement measures to prevent accidental release or overheating. This includes using pressure-relief mechanisms, implementing leak detection systems, and designing robust seals. Regular maintenance and monitoring can further ensure the long-term reliability of peroxide-based fuel cell vehicles.
In summary, engineering fuel cells for peroxide-based vehicles demands a meticulous approach, combining electrochemical understanding with materials science expertise. The design process involves selecting appropriate electrolytes, catalysts, and membranes while ensuring system integration and safety. This specialized fuel cell technology has the potential to power vehicles with high energy efficiency and unique performance characteristics.
Unveiling the Power: Fuel Injection in NASCAR Cup Cars
You may want to see also
Storage and Handling: Develop safe methods for storing and transporting hydrogen peroxide
The safe storage and transportation of hydrogen peroxide, a potent and reactive chemical, are critical aspects of its use in alternative fuel systems for vehicles. Here are some detailed guidelines for handling this substance:
Storage:
- Temperature Control: Hydrogen peroxide is sensitive to temperature changes. Store it in a cool, dry environment, preferably at temperatures between 32°F and 95°F (0°C and 35°C). Avoid exposure to direct sunlight and extreme heat sources.
- Ventilation and Containment: Always store hydrogen peroxide in a well-ventilated area. Use appropriate containers made of compatible materials like glass or certain plastics. Ensure the containers are tightly sealed to prevent evaporation and potential contamination.
- Segregation: Keep hydrogen peroxide away from flammable materials, oxidizing agents, and substances that may react violently with it. It is highly reactive and can initiate combustion when mixed with certain chemicals.
- Labeling and Documentation: Clearly label all containers with the chemical name, concentration, and any relevant hazards. Maintain detailed records of storage locations, quantities, and dates to ensure proper inventory management and emergency response planning.
Transportation:
- Secure Packaging: When transporting hydrogen peroxide, use specialized containers designed for chemical transportation. These containers should be made of materials resistant to corrosion and capable of withstanding pressure. Ensure the containers are properly sealed and secured to prevent leaks.
- Handling and Loading: Train personnel in safe handling procedures. This includes wearing appropriate personal protective equipment (PPE) and following established protocols for loading and unloading. Minimize the risk of contamination by using clean equipment and ensuring proper ventilation during transportation.
- Transportation Vehicles: Choose vehicles designed to handle hazardous materials. Ensure they are equipped with safety features such as spill containment kits, emergency response equipment, and communication systems. Regularly inspect and maintain the vehicles to guarantee safe transportation.
- Regulatory Compliance: Adhere to local, state, and federal regulations regarding the transportation of hazardous chemicals. Obtain necessary permits and ensure compliance with packaging and labeling requirements. Provide transportation companies with detailed information about the chemical to facilitate safe handling.
Implementing these storage and handling practices is essential to minimize risks associated with hydrogen peroxide. Proper training, regular inspections, and adherence to safety protocols will contribute to a secure environment for both the fuel and those who work with it.
A Beginner's Guide to Filling Up Your Car's Tank
You may want to see also
Engine Optimization: Modify engines to utilize hydrogen peroxide as a power source
The concept of using hydrogen peroxide as a power source for vehicles is an intriguing one, and optimizing engines to run on this chemical can lead to some innovative and efficient transportation methods. Here's a detailed guide on engine modification to achieve this:
Engine Design and Modification:
To begin, the engine's design must be tailored to accommodate hydrogen peroxide as a fuel source. This involves significant changes to the combustion chamber and the overall engine architecture. The engine should be designed to handle the unique properties of hydrogen peroxide, which is a highly oxidizing agent. The combustion process needs to be carefully controlled to ensure efficient burning without the risk of explosion. One approach is to use a modified piston engine with a specially designed combustion chamber that promotes rapid and controlled combustion. The chamber could be designed with a unique shape and material to facilitate the mixing and burning of hydrogen peroxide.
Fuel Injection System:
A precise and efficient fuel injection system is crucial. Hydrogen peroxide's chemical properties require a carefully calibrated injection process. The system should deliver the peroxide in a controlled manner, ensuring it mixes thoroughly with air before entering the combustion chamber. This might involve using high-pressure injectors and advanced fuel pumps to manage the flow rate accurately. The injection timing and quantity must be optimized to achieve the desired power output while maintaining stability.
Ignition System:
The ignition process is critical for hydrogen peroxide engines. Traditional spark plugs may not be suitable due to the highly oxidizing nature of the fuel. Instead, consider using a homogeneous charge compression ignition (HCCI) system or a direct injection method with a precise ignition timing system. This ensures that the hydrogen peroxide is ignited efficiently without the risk of premature combustion or engine knock.
Engine Materials and Cooling:
Engine components, especially those in direct contact with hydrogen peroxide, should be carefully selected to withstand its corrosive nature. Materials like stainless steel or specialized alloys might be required for engine blocks, cylinders, and valves. Additionally, efficient cooling systems are essential to manage the heat generated during combustion. Proper heat dissipation will prevent overheating and ensure the engine operates within safe temperature limits.
Performance and Efficiency:
Optimizing the engine's performance involves fine-tuning various parameters. This includes adjusting the compression ratio, optimizing the air-fuel mixture, and fine-tuning the engine's timing. The goal is to achieve a balance between power output and efficiency. Proper engine management systems can help monitor and control the combustion process, ensuring the engine operates optimally under different load conditions.
By implementing these modifications and optimizations, it is possible to create a functional and efficient engine that utilizes hydrogen peroxide as a power source. This technology could potentially offer a unique and environmentally friendly transportation solution, especially for specialized applications where traditional fuels may not be feasible.
Manual Cars: Fuel Efficiency Myth or Reality?
You may want to see also
Safety Protocols: Establish guidelines for safe operation and maintenance of peroxide cars
Safety is paramount when dealing with hydrogen peroxide-powered vehicles, and establishing comprehensive guidelines is essential to ensure the well-being of both operators and the environment. Here are some critical safety protocols to consider:
Training and Certification: Prior to operating a hydrogen peroxide car, all drivers should undergo rigorous training. This training should cover the unique properties of hydrogen peroxide, its potential hazards, and the specific maintenance procedures required. Operators should be certified and provided with a comprehensive manual outlining safe operating procedures. Regular refresher courses can help keep drivers updated on any new safety measures or changes in regulations.
Fuel Handling and Storage: Hydrogen peroxide fuel requires careful handling and storage. All fuel containers must be made of compatible materials to prevent corrosion and ensure the stability of the fuel. The storage area should be well-ventilated, cool, and dry, with proper ventilation systems to mitigate any potential gas leaks. It is crucial to implement strict protocols for fuel transfer, including the use of approved pumps and containers to minimize the risk of spillage or contamination.
Maintenance and Inspection: Regular maintenance is vital to the safe operation of peroxide cars. A comprehensive inspection protocol should be developed, covering all critical components, including the fuel system, engine, and electrical wiring. Maintenance technicians should be trained to identify potential issues, such as fuel leaks, pressure buildup, or electrical faults. All maintenance activities should be documented, and a record-keeping system should be established to track the history of each vehicle, ensuring that any identified problems are promptly addressed.
Emergency Response and Containment: In the event of an accident or malfunction, a well-defined emergency response plan is essential. This plan should include procedures for containing and neutralizing hydrogen peroxide spills, as well as protocols for evacuation and medical assistance. All personnel should be trained in these procedures, and emergency response teams should be readily available. Regular drills and simulations can help ensure that everyone is prepared for potential hazardous situations.
Environmental Considerations: Hydrogen peroxide cars should be operated with a deep understanding of their environmental impact. Guidelines should emphasize the importance of proper waste disposal, including the safe handling and treatment of used fuel and waste materials. Operators should be encouraged to explore sustainable practices, such as recycling or reusing certain components, to minimize the overall environmental footprint of the vehicle.
Can a Car Run with a Bad Fuel Filter? Uncovering the Truth
You may want to see also
Frequently asked questions
Hydrogen peroxide cars typically use a mixture of hydrogen peroxide and an oxidizer, often sulfuric acid or potassium nitrate, as their fuel source. This combination creates a powerful reaction, providing the necessary energy for the vehicle's operation.
The fuel mixture is carefully proportioned to ensure a controlled reaction. When ignited, the hydrogen peroxide decomposes, releasing oxygen and generating a rapid expansion of gases. This expansion drives the engine, similar to how gasoline or diesel engines work, but with a unique chemical process.
Absolutely, safety is crucial. Hydrogen peroxide and its mixtures are highly corrosive and can be hazardous if not handled properly. Proper ventilation is essential during fueling and operation, and all personnel should be trained in safety protocols to minimize risks associated with this powerful fuel source.