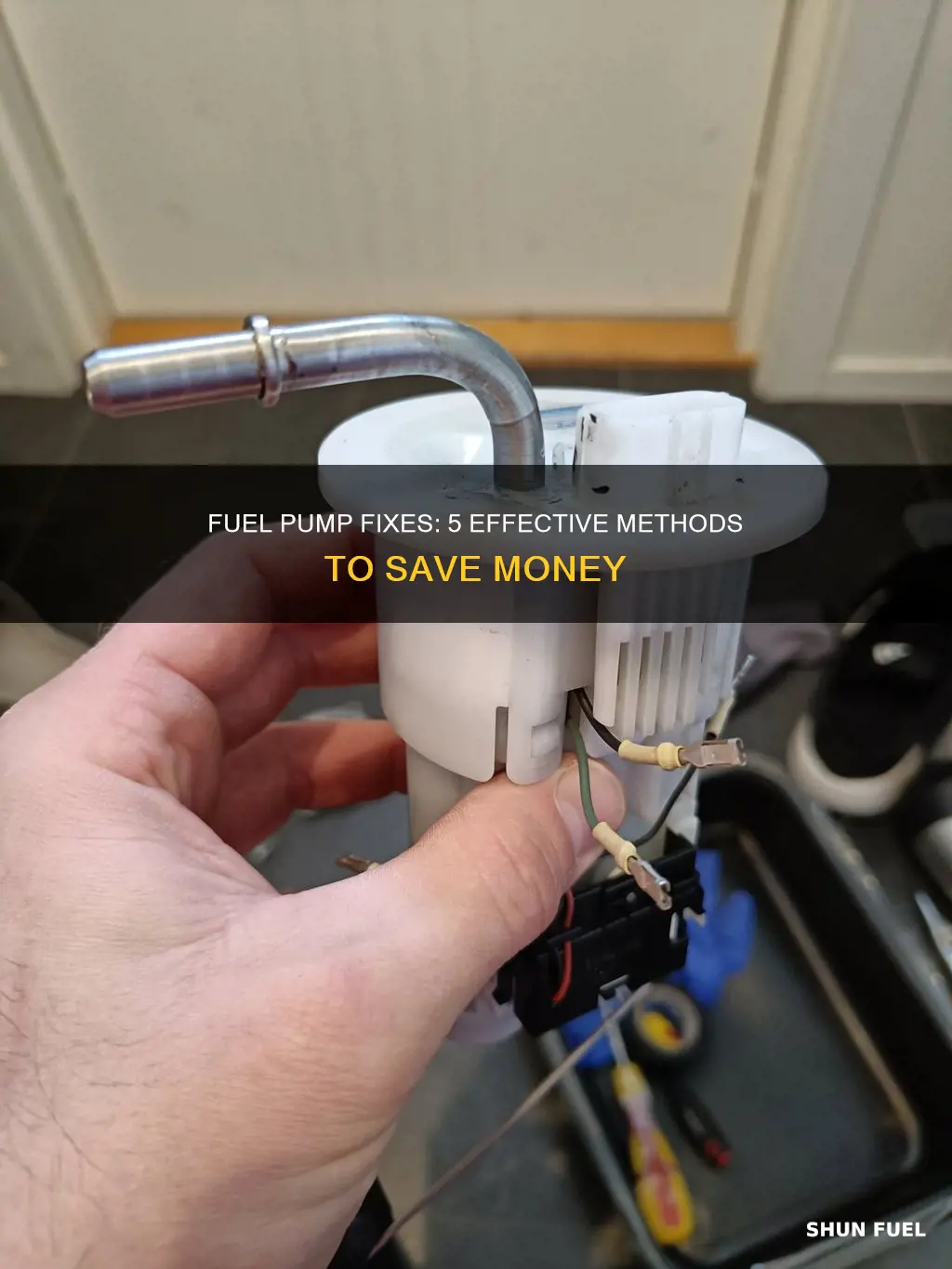
Fixing a fuel pump without replacing it can be a cost-effective solution for vehicle owners. This guide will provide a step-by-step approach to troubleshooting and repairing a faulty fuel pump. By following these instructions, you can potentially save money and extend the life of your vehicle's fuel system. The process involves identifying the issue, gathering the necessary tools and parts, and systematically addressing the problem to restore the pump's functionality. With patience and the right techniques, you can effectively resolve fuel pump issues and avoid an expensive replacement.
What You'll Learn
- Identify Issues: Check for fuel flow, listen for pump operation, and inspect for blockages
- Clean or Replace Filters: Ensure fuel pump and lines are free of debris and clogs
- Test Electrical Connections: Inspect wiring, fuses, and grounds for corrosion or damage
- Adjust Pressure: Calibrate fuel pressure regulator if pressure is too low or high
- Replace Pump Components: Replace worn-out parts like impellers or diaphragms
Identify Issues: Check for fuel flow, listen for pump operation, and inspect for blockages
When dealing with a fuel pump that needs repair without a full replacement, it's crucial to identify the specific issues to ensure an effective fix. Here's a step-by-step guide to help you pinpoint the problems:
Check for Fuel Flow: Start by ensuring that there is a steady supply of fuel reaching the pump. Inspect the fuel lines for any signs of damage, cracks, or leaks. If you notice any issues with the lines, it could indicate a problem with the fuel system that needs addressing before tackling the pump. Check the fuel filter as well; a clogged or dirty filter can restrict fuel flow, leading to pump issues. Replacing or cleaning the filter might be necessary to restore proper fuel delivery.
Listen for Pump Operation: The fuel pump should operate silently and consistently. If you hear any unusual noises, such as whining, groaning, or rattling, it could indicate a problem. Start by checking the pump's electrical connections. Loose or corroded connections can cause erratic behavior. Ensure all wires are securely attached and free from any signs of damage. If the pump still doesn't operate as expected, it might be faulty and require further investigation.
Inspect for Blockages: Blockages in the fuel system can prevent the pump from functioning correctly. Start by checking the fuel tank for any debris or sediment that might have accumulated. Use a fuel filter replacement tool to remove any built-up contaminants. If the tank is clean, move on to the lines. Inspect the fuel lines for any blockages or clogs, especially in the smaller lines that run from the tank to the pump. You might need to use a fuel line brush to clear any obstructions.
By following these steps, you can identify whether the issue lies with the fuel flow, pump operation, or blockages in the system. This targeted approach will help you make informed decisions about the necessary repairs, ensuring you fix the fuel pump effectively without unnecessary replacements.
Stihl 015 Fuel Filter Replacement: A Step-by-Step Guide
You may want to see also
Clean or Replace Filters: Ensure fuel pump and lines are free of debris and clogs
When dealing with a fuel pump that is not functioning optimally, one of the most common issues is the presence of debris and clogs within the system. This can be caused by a variety of factors, including old fuel, contaminated fuel, or simply the natural wear and tear of the fuel system over time. Cleaning or replacing filters is a crucial step in the process of fixing a fuel pump without resorting to a full replacement.
The first step is to inspect the fuel lines and pump for any visible signs of contamination or damage. Start by removing the fuel line from the fuel tank and examining it for any blockages or clogs. You can use a fuel line cleaner or a compressed air gun to blow out any debris or dirt that might be present. Ensure that you follow the manufacturer's instructions for the cleaner to avoid any potential damage to the fuel system. If you notice any significant buildup or damage, it might be necessary to replace the fuel line.
Next, focus on the fuel pump itself. Remove the pump from the vehicle and inspect it for any signs of debris or contamination. You can use a fine brush or a small tool to gently clean the pump's internal components, ensuring that you remove any dirt or grime. Pay close attention to the filter, as it is a critical component in keeping the fuel system clean. If the filter is clogged or dirty, replace it with a new one. This is a relatively simple process, often involving the removal of a few screws or clips to access the filter.
In addition to cleaning the fuel pump, it's essential to check and clean the fuel filter, which is typically located near the engine. This filter traps contaminants and ensures that only clean fuel reaches the pump. If the filter is clogged, it can restrict fuel flow, causing the pump to work harder and potentially leading to further issues. Replace the filter if it shows signs of wear or if it has been a while since the last replacement.
Remember, regular maintenance and cleaning of the fuel system can prevent many common issues. By ensuring that the fuel pump and lines are free of debris and clogs, you can often resolve performance problems without the need for a complete pump replacement. This approach is cost-effective and environmentally friendly, as it reduces the amount of waste generated by replacing parts unnecessarily.
Replacing Fuel Injector Wires in Your 06 Caravan
You may want to see also
Test Electrical Connections: Inspect wiring, fuses, and grounds for corrosion or damage
When dealing with a fuel pump that needs repair without a full replacement, it's crucial to start with a thorough inspection of the electrical connections. This process involves a systematic check of the wiring, fuses, and grounds to identify any potential issues that might be causing the pump's malfunction. Here's a step-by-step guide to help you through this process:
- Inspect the Wiring: Begin by carefully examining the wiring connected to the fuel pump. Look for any visible signs of damage, such as frayed or exposed wires, burn marks, or discolored insulation. Pay close attention to the points where wires connect to the pump and the vehicle's electrical system. Ensure that all connections are secure and free from any corrosion or oxidation. If you notice any damaged wires, it's essential to replace them with new ones of the correct gauge to ensure proper functionality.
- Check Fuses and Relay Modules: The next step is to inspect the fuses and relay modules associated with the fuel pump circuit. Locate the fuse box and identify the specific fuse that controls the fuel pump. Check if the fuse is intact and not blown. If the fuse is damaged, it might need to be replaced. Additionally, inspect the relay module, if present, for any signs of overheating or damage. Ensure that all connections within the relay module are clean and secure.
- Examine Grounds: Grounds are critical in electrical systems, and a poor ground connection can lead to various issues. Inspect all ground wires connected to the fuel pump for corrosion or damage. Clean any corroded terminals and ensure a solid connection. Sometimes, a simple cleaning and tightening of ground connections can resolve electrical problems.
- Use a Multimeter: For a more comprehensive test, use a multimeter to check the continuity and voltage of the wiring and connections. Set the multimeter to the appropriate range and test each wire for continuity. This will help identify any open circuits or damaged wires. Additionally, measure the voltage at various points in the circuit to ensure it matches the expected values.
- Look for Corrosion: Moisture and corrosion can be detrimental to electrical systems. Inspect the fuel pump and its surrounding areas for any signs of corrosion. This might include checking the pump's mounting area, wiring harnesses, and any nearby terminals. If corrosion is found, clean the affected areas with a suitable solvent and ensure proper drying before reinstalling or repairing.
By following these steps, you can systematically test and inspect the electrical connections related to the fuel pump. Identifying and addressing issues with wiring, fuses, and grounds can often resolve the problem without the need for a complete pump replacement. It's a practical approach to troubleshooting and can save time and resources.
Replacing Fuel Lines: 1998 Chevy Silverado Step-by-Step Guide
You may want to see also
Adjust Pressure: Calibrate fuel pressure regulator if pressure is too low or high
If you're experiencing issues with your fuel pump and are looking to avoid a full replacement, one of the key areas to focus on is the fuel pressure regulator. This component plays a critical role in ensuring the correct amount of fuel is delivered to the engine, and if it's not functioning optimally, it can lead to a variety of performance problems. Here's a step-by-step guide on how to adjust and calibrate the fuel pressure regulator to address low or high pressure issues.
Understanding the Fuel Pressure Regulator
The fuel pressure regulator is designed to maintain a consistent pressure within the fuel system. It regulates the flow of fuel from the tank to the engine, ensuring that the engine receives the precise amount required for optimal performance. Over time, this regulator can become dirty, clogged, or damaged, leading to pressure fluctuations.
Symptoms of Fuel Pressure Issues
Before you begin the calibration process, it's essential to identify the symptoms of a faulty fuel pressure regulator. Common signs include engine misfires, reduced power, rough idling, and poor fuel economy. If you notice any of these, it's a strong indicator that the fuel pressure regulator needs attention.
Tools and Materials Required
- Fuel pressure gauge
- Wrench set
- Cleaning solvent (for regulator)
- New o-rings (if required)
- Safety equipment (gloves, goggles)
Step-by-Step Calibration Process
- Safety First: Ensure the engine is cool and disconnected from the fuel source. Wear protective gear to avoid contact with fuel.
- Locate the Regulator: Identify the fuel pressure regulator, which is typically located near the engine's fuel rail. It might be a small, cylindrical component with an inlet and outlet.
- Check for Clogging: If the regulator is accessible, inspect it for any debris or fuel contamination. Use a cleaning solvent to remove any buildup, ensuring you don't damage the internal components.
- Adjust the Regulator: The regulator often has an adjustment screw or valve. Loosen the screw (if adjustable) and make small adjustments to increase or decrease pressure. Fine-tune the pressure until it matches the ideal range (usually specified in your vehicle's manual).
- Test the Pressure: Use the fuel pressure gauge to measure the pressure at the regulator's outlet. Ensure it falls within the recommended range.
- Secure Connections: Tighten all connections and ensure they are secure to prevent leaks.
Troubleshooting High Pressure
If the pressure is too high, you may need to adjust the regulator's spring tension or consider replacing it if it's severely damaged.
Troubleshooting Low Pressure
For low pressure, check the fuel pump's operation and ensure it's delivering sufficient fuel. If the pump is functioning correctly, the issue might be with the regulator's internal components, requiring adjustment or replacement.
Remember, this process requires precision and patience. If you're unsure, consult a professional mechanic to ensure the job is done safely and effectively.
Replacing the Fuel Line on your Stihl FS90R
You may want to see also
Replace Pump Components: Replace worn-out parts like impellers or diaphragms
If you're dealing with a fuel pump that's not working efficiently or making unusual noises, it might be possible to fix it without a full replacement. One common issue that can arise is worn-out pump components, such as the impeller or diaphragm. These parts play a crucial role in the pump's functionality, and replacing them can often resolve the problem. Here's a step-by-step guide on how to replace these components:
- Identify the Problematic Part: Start by carefully inspecting the fuel pump. Listen for any unusual sounds, such as whining or grinding, which could indicate a worn-out impeller or diaphragm. Check for any visible signs of damage, cracks, or excessive wear. The impeller is a rotating component that pushes fuel through the pump, and it can wear down over time. The diaphragm, on the other hand, is a flexible membrane that regulates fuel pressure. If either of these parts is damaged or worn, it may need to be replaced.
- Gather the Necessary Tools and Parts: Before you begin, ensure you have the required tools and replacement parts. You'll typically need a fuel pump disassembly kit, which includes specialized tools for removing the pump without causing damage. Additionally, source the replacement impeller and diaphragm for your specific pump model. It's essential to use genuine or high-quality aftermarket parts to ensure compatibility and optimal performance.
- Disassemble the Fuel Pump: Locate the fuel pump, which is usually positioned near the fuel tank or along the fuel line. Carefully drain any remaining fuel to avoid spills. Then, using the appropriate tools from your disassembly kit, carefully take apart the pump. This process may involve removing screws, clips, or brackets to access the internal components. Take note of the pump's orientation and the positions of various parts to ensure proper reassembly.
- Remove and Replace the Impeller or Diaphragm: With the pump disassembled, you can now access the worn-out component. Carefully remove the old impeller or diaphragm, being mindful of any delicate connections or seals. Inspect the replacement parts for any defects or damage during removal. Once the old parts are out, carefully insert the new impeller and secure it according to the manufacturer's instructions. Ensure that the diaphragm is properly seated and aligned.
- Reassemble and Test: Reassemble the fuel pump, making sure all components are correctly aligned and secured. Fill the pump with the appropriate fluid, typically engine oil or a specialized fuel pump cleaner. Then, reattach the pump to the fuel system and start the engine. Monitor the pump's performance and listen for any unusual noises. If the issue is resolved, you've successfully replaced the worn-out pump components.
By replacing the impeller or diaphragm, you can often restore the fuel pump's functionality without the need for a complete replacement. This process requires careful disassembly, identification of the faulty part, and precise reassembly. Always refer to the pump's manual or seek professional guidance if you're unsure about any step, as fuel system repairs can be complex and potentially dangerous if not handled correctly.
Replacing Your Fuel Pump: Getting Your Vehicle Started Again
You may want to see also
Frequently asked questions
Testing a fuel pump can be done through a few methods. Firstly, you can use a fuel pump tester, which is a handy tool that connects to the pump and measures its performance. This tester will indicate if the pump is drawing power and delivering fuel at the correct pressure. Alternatively, you can use a multimeter to test the pump's electrical connections and ensure it's receiving power. If the pump doesn't show any signs of life or fails these tests, it might be time to consider a replacement.
Clogged fuel pumps can be a common issue, but there are a few ways to address it without a full replacement. One method is to use a fuel line cleaner, which can be injected into the fuel system to dissolve any blockages. This process might require some patience as it can take time for the cleaner to work its way through the system. Another approach is to use a fuel pump flush, where you remove the pump and clean it with a suitable solvent. This process should be done with caution and might require professional tools and knowledge.
A noisy fuel pump often indicates a worn-out or damaged component. While it's not a permanent solution, you can try some temporary fixes. One option is to add a fuel system lubricant to the tank, which can help reduce friction and noise temporarily. However, this might not address the root cause of the noise. In most cases, replacing the fuel pump is the best long-term solution to eliminate the noise and ensure proper fuel delivery.