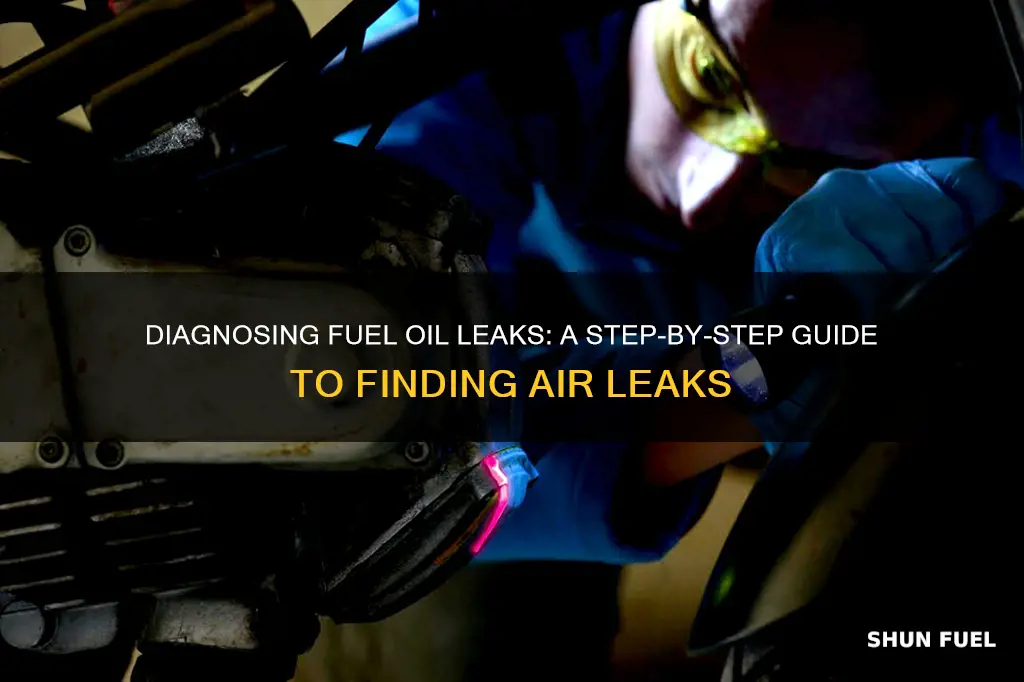
Locating an air leak in a fuel oil line can be a challenging task, but with the right approach, it's certainly achievable. This guide will provide a step-by-step process to help you identify and fix the issue. By following these instructions, you can ensure your fuel system operates efficiently and safely.
What You'll Learn
- Visual Inspection: Check for visible signs of damage, cracks, or disconnections in the fuel oil line
- Pressure Testing: Use a pressure gauge to identify leaks by monitoring pressure drops
- Fuel Flow Analysis: Measure fuel flow rates to detect abnormal leaks or blockages
- Ultrasonic Detection: Employ ultrasonic devices to identify leaks through sound wave detection
- Leak Detection Dyes: Apply specialized dyes to trace and pinpoint leaks in the fuel line
Visual Inspection: Check for visible signs of damage, cracks, or disconnections in the fuel oil line
A visual inspection is a crucial step in identifying air leaks in a fuel oil line. This method allows you to quickly assess the condition of the line and detect any potential issues. Here's a detailed guide on how to perform this inspection:
Start by locating the fuel oil line, which is typically a black or dark-colored hose connecting the fuel tank to the engine. Carefully examine the line for any visible signs of damage or deterioration. Look for cracks, cuts, or punctures along the length of the line. Even small tears or frays can lead to air leaks. Inspect the connections between the line and the fuel tank, as well as any fittings or valves along the route. Ensure that all connections are secure and tight. Over time, vibrations and temperature changes can cause connections to loosen, so it's essential to check and tighten them if necessary.
Pay close attention to areas where the line might be more susceptible to damage. These include bends, joints, and any points where the line passes over or under other components. In these areas, look for signs of wear, such as frayed insulation or exposed inner layers. If you notice any exposed fuel or air, it could indicate a potential leak. Additionally, check for any signs of corrosion or rust, especially if the line is made of metal. Corrosion can weaken the material and create cracks over time.
During your inspection, make sure to look for any visible bubbles or foam forming around the line. This could be a sign of air entering the fuel system. If you spot any bubbles, it's essential to investigate further, as air bubbles can indicate a leak or a problem with the fuel pump. Remember, the goal of this visual inspection is to identify any physical damage or disconnections that might allow air to enter the fuel line. If you find any issues, you can then proceed to more advanced diagnostic methods to pinpoint the exact location and cause of the air leak.
Mastering Ford Fuel Line Fitting: A Comprehensive Guide
You may want to see also
Pressure Testing: Use a pressure gauge to identify leaks by monitoring pressure drops
Pressure testing is a crucial method to identify air leaks in fuel oil lines, ensuring the system's efficiency and safety. This technique involves using a pressure gauge to measure and monitor the pressure within the fuel oil line. Here's a step-by-step guide on how to perform this test:
Preparation: Before starting, ensure you have the necessary tools, including a pressure gauge, a source of compressed air or nitrogen, and a clean, dry cloth. It is essential to disconnect the fuel oil line from the fuel source and the engine to create a sealed system for testing.
Step 1: Set Up the Pressure Gauge: Connect the pressure gauge to the fuel oil line, ensuring a secure and tight seal. The gauge should be positioned to measure the pressure at the point where the air leak is suspected. Calibrate the gauge to ensure accurate readings.
Step 2: Apply Pressure: Introduce compressed air or nitrogen into the fuel oil line to a predetermined pressure. The pressure should be set at a level that is slightly above the normal operating pressure of the system. This initial pressure reading will serve as a baseline.
Step 3: Monitor Pressure Drop: With the pressure applied, closely observe the pressure gauge. A trained professional should be present to monitor the readings. If an air leak exists, you will notice a rapid and consistent drop in pressure over time. The rate of pressure loss will indicate the severity of the leak.
Step 4: Identify Leaks: Leaks can be categorized as small, moderate, or severe based on the pressure drop rate. Small leaks may result in a gradual pressure decrease, while moderate and severe leaks will cause a more rapid drop. It is essential to document the pressure readings at regular intervals to track the leak's progress.
Step 5: Repair and Re-test: Once the leaks are identified, the appropriate repairs can be made. After addressing the issues, re-test the system using the same pressure testing procedure. This ensures that the repairs were successful and that the air leaks have been effectively resolved.
By following these steps, technicians can accurately locate and repair air leaks in fuel oil lines, maintaining the system's integrity and performance. Pressure testing is a reliable and non-invasive method to identify leaks, making it an essential tool in the maintenance and troubleshooting of fuel oil systems.
Freezing Fuel: The Impact of Water in Fuel Lines
You may want to see also
Fuel Flow Analysis: Measure fuel flow rates to detect abnormal leaks or blockages
Fuel flow analysis is a critical process in the maintenance and troubleshooting of fuel systems, especially in applications where fuel oil is used. This technique involves measuring the rate of fuel flow through a system to identify any leaks or blockages that might be occurring. By monitoring the fuel flow, technicians can quickly pinpoint issues that could lead to reduced performance, increased emissions, or even system failure.
The process begins with the installation of specialized flow meters at strategic points in the fuel system. These meters are designed to accurately measure the volume of fuel passing through them over a specific time period. The data collected from these meters provides a clear picture of the fuel's movement through the system. Technicians can then compare these measurements against expected flow rates to identify any deviations.
When conducting fuel flow analysis, it's essential to establish a baseline of normal operating conditions. This baseline is created by measuring fuel flow rates under various operating scenarios, such as idling, acceleration, and deceleration. By understanding the typical fuel flow patterns, technicians can more easily detect abnormal behavior. For instance, a sudden drop in fuel flow rate during acceleration could indicate a restriction or blockage in the fuel line.
In addition to measuring flow rates, technicians may also use pressure measurements to gain further insights. Fuel pressure can provide clues about the presence of air leaks or blockages. A drop in fuel pressure could suggest an air leak, as air is less dense than fuel and can enter the system through small openings. Conversely, an increase in pressure might indicate a blockage, as the fuel has to exert more force to pass through a restricted area.
By combining fuel flow analysis with pressure measurements, technicians can effectively diagnose a wide range of fuel system issues. This non-invasive method allows for the early detection of problems, enabling prompt repairs and minimizing potential damage to the system. Regular fuel flow analysis is an essential part of maintaining fuel efficiency, performance, and the overall longevity of the fuel system.
Quick Fix: Temporary Solutions for Fuel Line Leaks
You may want to see also
Ultrasonic Detection: Employ ultrasonic devices to identify leaks through sound wave detection
Ultrasonic detection is a highly effective method for identifying air leaks in fuel oil lines, offering a non-invasive and precise approach to troubleshooting. This technique utilizes ultrasonic devices, which emit high-frequency sound waves that can detect even the smallest leaks in the system. The process involves placing these devices along the fuel oil lines, where they send out sound pulses and listen for any deviations or disruptions in the sound waves. When an air leak occurs, it creates a unique acoustic signature that can be picked up by the ultrasonic sensor.
The devices are designed to detect the high-frequency sound waves that are typically inaudible to the human ear. When an air bubble or leak is present, it causes a change in the sound wave pattern, creating a distinct signal that can be analyzed. This method is particularly useful for locating leaks in hard-to-reach areas or where visual inspection is challenging. By moving the ultrasonic device along the line, technicians can map out the location of leaks, ensuring a comprehensive assessment of the system.
To employ this technique, technicians first need to select the appropriate ultrasonic device for the task. These devices come in various forms, including handheld probes, fixed sensors, or even robotic systems for automated inspection. Handheld probes offer portability and flexibility, allowing technicians to move them along the fuel oil lines. Fixed sensors, on the other hand, can be strategically placed at critical points to monitor the system continuously. The choice of device depends on the specific requirements of the fuel oil system and the accessibility of the areas to be inspected.
Once the devices are in place, the process involves transmitting sound waves through the fuel oil line and analyzing the received signals. Any deviations or changes in the sound wave patterns indicate the presence of air leaks. The ultrasonic devices can provide real-time data, allowing technicians to identify and pinpoint the exact location of the leak. This information is crucial for effective repair and ensures that the issue is addressed promptly to prevent potential damage or system failure.
Ultrasonic detection offers several advantages over traditional methods. It is a non-contact technique, eliminating the risk of damage to the fuel oil line during inspection. The high sensitivity of ultrasonic devices allows for the detection of very small leaks, ensuring that potential issues are caught early. Additionally, this method provides a detailed record of the leak's location, aiding in the development of targeted repair strategies. By combining ultrasonic detection with other diagnostic techniques, technicians can efficiently identify and resolve air leaks in fuel oil lines, ensuring optimal system performance and longevity.
F150 Fuel Line: Understanding Proper Ratings and Safety
You may want to see also
Leak Detection Dyes: Apply specialized dyes to trace and pinpoint leaks in the fuel line
Leak detection dyes are a powerful tool for identifying and pinpointing fuel line leaks, especially those that are difficult to detect with the naked eye. This method is particularly useful for fuel oil lines, as it can help you trace leaks in hard-to-reach areas or those that are not easily visible. Here's a step-by-step guide on how to use leak detection dyes effectively:
Preparation and Application:
- Start by ensuring that the fuel system is shut down and all fuel sources are disconnected. This is crucial for safety and to prevent any accidental fuel release.
- Purchase a leak detection dye kit, which typically includes the dye, a syringe or applicator, and instructions. These kits are designed specifically for fuel lines and are safe for use with various types of fuels.
- Carefully clean the fuel line section you suspect might have a leak. This step ensures that any existing contaminants or debris do not interfere with the dye's effectiveness.
- Apply the dye according to the manufacturer's instructions. Typically, a small amount of dye is injected into the fuel line using the provided syringe. The dye will mix with the fuel and become visible when a leak occurs.
Trace and Identify Leaks:
- After applying the dye, start the fuel system and observe the fuel's behavior. Leaks will be indicated by the presence of the dye, which will appear as a visible trail or stain.
- Follow the dye's path to locate the exact point of the leak. This might require some patience and careful observation, as the dye may take some time to become visible depending on the fuel's flow rate and the dye's properties.
- For hard-to-reach areas, you might need to temporarily access the fuel line by removing a section of the line or using a small camera to visualize the dye's path.
Safety and Cleanup:
- Always wear protective gear, such as gloves and goggles, when handling leak detection dyes to avoid any potential skin or eye irritation.
- If a leak is detected, immediately shut off the fuel supply and address the issue to prevent further fuel loss and potential safety hazards.
- After the leak is repaired, ensure that the dye is properly neutralized and any residual fuel is safely disposed of according to local regulations.
Using leak detection dyes is a non-invasive and effective method to identify fuel line leaks, especially in complex systems. It allows for precise leak location, ensuring that repairs can be made efficiently and safely. This technique is a valuable addition to any mechanic's or technician's toolkit for fuel system maintenance and troubleshooting.
Autozone's Fuel Line Offer: Push Lock or Not?
You may want to see also
Frequently asked questions
Air leaks in fuel oil lines can be tricky to detect, but there are a few methods you can try. One common sign is a hissing sound near the fuel tank or line, which indicates the presence of air. You can also use a soapy water solution to check for bubbles; if you see bubbles forming, it suggests an air leak. Additionally, monitoring the fuel pressure and flow rate can help identify issues.
To repair an air leak, you'll typically need a few basic tools. A fuel line repair kit is essential and includes items like a fuel line clamp, a fuel line coupler, and a fuel filter. You might also need a fuel pressure gauge to check and adjust the pressure. It's important to have a supply of replacement fuel lines or fittings if the damage is extensive.
Temporary fixes are possible for minor air leaks, but it's crucial to understand the limitations. You can use a temporary clamp or a piece of rubber to seal the leak, but this is only a short-term solution. For a more permanent repair, it's recommended to consult a professional mechanic who can ensure the job is done safely and effectively.
Regular maintenance is key to preventing air leaks. Inspect your fuel lines and connections periodically for any signs of damage, cracks, or corrosion. Keep the fuel tank and lines clean to prevent contamination, which can lead to leaks. Additionally, ensure that all fittings and connections are tight and secure.