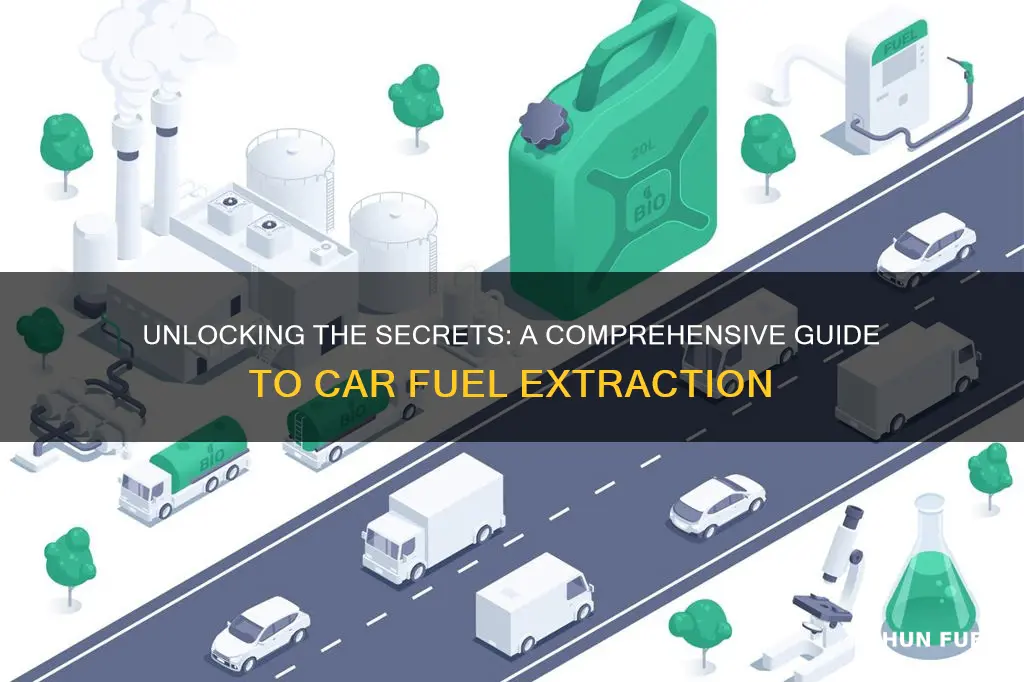
Extracting fuel from a car is a complex process that involves various components and systems. It begins with the engine, where the fuel is injected into the combustion chamber and ignited to power the vehicle. However, the process of extracting fuel goes beyond the engine itself. It involves the fuel system, which includes the fuel tank, fuel pump, and fuel lines, all working together to deliver the necessary fuel to the engine. Understanding how these components interact and function is crucial to optimizing fuel efficiency and ensuring the car's performance. This guide will explore the different methods and techniques used to extract fuel from a car, providing insights into the intricate relationship between the engine, fuel system, and the overall vehicle operation.
What You'll Learn
- Engine Oil: Filter and Reuse for Optimal Performance
- Ethanol Production: Fermentation Process for Biofuel Creation
- Biodiesel Synthesis: Transesterification for Vegetable Oil Conversion
- Gasoline Refining: Crude Oil Distillation for Fuel Purification
- Hydrogen Extraction: Electrolysis for Clean Energy Generation
Engine Oil: Filter and Reuse for Optimal Performance
Engine oil is a vital component of a car's engine, and proper maintenance, including regular oil changes and filtration, is essential for optimal performance and longevity. While it might seem counterintuitive to reuse engine oil, it is a common practice that can save costs and benefit the environment. Here's a guide on how to filter and reuse engine oil for optimal performance:
Understanding Engine Oil and Its Role: Engine oil serves multiple purposes in a car's engine. It lubricates the moving parts, reducing friction and preventing metal-to-metal contact, which can cause wear and tear. Additionally, oil acts as a coolant, absorbing heat generated during engine operation and preventing overheating. It also captures and removes contaminants, such as dirt, metal particles, and combustion byproducts, ensuring that the engine remains clean and operates efficiently.
The Importance of Oil Filtration: Over time, engine oil breaks down and becomes contaminated with various impurities. This degradation can lead to reduced performance and increased engine wear. That's where oil filtration comes into play. An oil filter is designed to trap contaminants and ensure that clean oil circulates throughout the engine. Regularly replacing the oil filter as part of routine maintenance is crucial to maintaining the health of the engine.
Steps to Filter and Reuse Engine Oil: Reusing engine oil can be a cost-effective and environmentally friendly approach, but it requires proper filtration. Here's a simplified process:
- Oil Change Preparation: Before reusing oil, ensure you have the necessary tools, including an oil filter, a new oil filter gasket, and a container for collecting the used oil. Park the car on a level surface and allow the engine to cool down.
- Drain the Old Oil: Locate the oil drain plug, typically found underneath the engine. Place a drain pan or container beneath the plug to catch the used oil. Carefully remove the plug and allow the oil to drain. Be cautious as the oil may still be hot.
- Replace the Oil Filter: Remove the old oil filter and inspect it for any signs of damage or excessive contamination. Clean the mounting surface on the engine block. Insert the new oil filter, ensuring it is torqued to the manufacturer's specifications.
- Refill with New Oil: Add the recommended amount and type of engine oil specified by the vehicle's manual. Start the engine and check for any leaks. Let it run for a few minutes to ensure proper distribution of the new oil.
- Reusing the Oil: After a successful oil change, the filtered and reused oil can be added back to the engine. However, it's important to note that reusing oil multiple times may lead to a loss of performance and protection benefits. For optimal results, consider reusing oil for a limited number of changes or for specific applications.
Benefits of Reusing Engine Oil: Reusing engine oil can result in cost savings, as it eliminates the need for frequent oil changes. It also reduces waste and contributes to environmental conservation. Additionally, reusing oil can help maintain the engine's performance and extend its lifespan, especially when combined with regular oil filter replacements.
Remember, while reusing engine oil can be beneficial, it should be done responsibly and in accordance with manufacturer guidelines. Proper filtration and regular maintenance will ensure that the reused oil continues to provide the necessary protection and performance.
Exploring the Size of Car Hydrogen Fuel Cells: A Comprehensive Guide
You may want to see also
Ethanol Production: Fermentation Process for Biofuel Creation
The process of ethanol production, a key component in the creation of biofuels, primarily involves a fermentation process that utilizes microorganisms to break down carbohydrates and convert them into ethanol. This method is an eco-friendly alternative to traditional fossil fuels, offering a renewable energy source with a lower environmental impact. Here's an overview of the fermentation process for ethanol production:
Feedstock Preparation: The first step is to select and prepare the raw materials, commonly known as feedstock, which will be used in the fermentation process. This feedstock can include various agricultural products such as corn, wheat, sugar cane, or even cellulosic materials like wood chips and straw. The feedstock is typically ground or processed to break down the complex carbohydrates into simpler sugars, making them accessible to the microorganisms for fermentation.
Enzymatic Conversion: Enzymes play a crucial role in this stage. Amylase enzymes are added to the feedstock to catalyze the breakdown of starches into maltose, a disaccharide. This process is essential as it converts the complex carbohydrate structure into a form that can be easily fermented. The maltose is then further broken down into glucose, a simple sugar, through the action of glucoamylase. This enzymatic conversion ensures that the microorganisms have the necessary substrate for ethanol production.
Fermentation: This is the core step in ethanol production. Yeast, a type of microorganism, is added to the feedstock containing glucose. Yeast ferments the glucose, producing ethanol and carbon dioxide as byproducts. The fermentation process can be carried out in large tanks or bioreactors, where the temperature, pH, and oxygen levels are carefully controlled to optimize the yeast's activity. The duration of fermentation varies but typically ranges from a few days to a week. During this time, the yeast consumes the glucose and secretes ethanol, which accumulates in the fermentation broth.
Ethanol Recovery: After the fermentation process, the ethanol needs to be separated from the remaining solids and water. This is achieved through distillation, where the fermentation broth is heated to vaporize the ethanol, which is then condensed back into a liquid form. The ethanol-rich fraction is collected, and the remaining solids, known as stillage, can be further processed to extract other valuable byproducts, such as animal feed or bio-based chemicals.
Purification and Quality Control: The recovered ethanol undergoes purification processes to meet the required standards for fuel usage. This may involve additional distillation steps or the use of absorption columns to remove impurities and water. Quality control measures are essential to ensure the ethanol meets the necessary specifications for its intended use, whether as a biofuel additive or a standalone fuel source.
Ethanol production through fermentation is a sustainable and renewable process, contributing to the development of a bio-based economy. It offers a promising solution to the environmental challenges associated with conventional fuel sources, providing a cleaner and more sustainable alternative for the transportation sector.
Can You Fuel a Car While It's Running? Unlocking the Mystery
You may want to see also
Biodiesel Synthesis: Transesterification for Vegetable Oil Conversion
Biodiesel synthesis through transesterification is a process that converts vegetable oils or animal fats into a usable fuel for diesel engines. This method is an eco-friendly alternative to traditional fossil fuels, offering a renewable and sustainable energy source. The process involves a chemical reaction where the oil is reacted with an alcohol, typically methanol, in the presence of a catalyst, usually sodium hydroxide (NaOH) or potassium hydroxide (KOH).
The key to this process is the transesterification reaction, which is a nucleophilic substitution reaction. In this reaction, the hydroxyl group (-OH) of the alcohol attacks the triglyceride molecule, breaking it down into three components: biodiesel, glycerol, and soap. The soap, or more accurately, the fatty acid methyl ester (FAME), is a byproduct that can be recycled or disposed of safely. The reaction can be represented by the following equation:
Vegetable Oil + Methanol + Catalyst → Biodiesel + Glycerol + Soap
This process is carried out in a reactor, often a stirred tank reactor, where the temperature and pressure are carefully controlled. The reaction is exothermic, meaning it releases heat, so proper temperature control is essential to prevent side reactions and ensure a high yield of biodiesel. The reaction mixture is then separated into three phases: an organic phase containing the biodiesel, an aqueous phase containing the glycerol and soap, and a residual oil phase.
After the reaction, the biodiesel must be washed to remove any traces of soap and water. This is typically done by washing the biodiesel with water to separate the aqueous phase from the organic phase. The biodiesel is then ready for use, and the glycerol can be further processed or used as a feedstock for other industries. This process not only provides a renewable fuel source but also offers a way to recycle waste vegetable oils, reducing environmental impact and promoting sustainability.
Are Flex Fuel Cars Reliable? Unlocking Robustness and Durability
You may want to see also
Gasoline Refining: Crude Oil Distillation for Fuel Purification
The process of refining crude oil into gasoline involves a complex series of steps, primarily centered around distillation. This method is a cornerstone of the petroleum industry, allowing for the separation of crude oil into various usable products, including gasoline, diesel, and other hydrocarbons. Here's an overview of how gasoline is refined through crude oil distillation:
- Crude Oil Transportation and Arrival at the Refinery: Crude oil is extracted from the earth and transported to refineries via pipelines or tankers. Upon arrival, the crude oil is carefully stored in large tanks to ensure it remains stable and ready for processing.
- Initial Processing and Sediment Removal: Before distillation, the crude oil undergoes initial treatment. This includes removing sediments and heavier impurities through processes like settling and filtration. This step ensures that the oil is free from solid particles and water, which could interfere with the distillation process.
- Distillation Column (Fractional Distillation): The heart of the gasoline refining process is the distillation column, often referred to as a fractional distillation column. Here's how it works: The crude oil is heated to a specific temperature, causing it to vaporize. The vapor then enters the distillation column, where it is separated into different fractions based on their boiling points. These fractions include:
- Gasoline Range: This fraction, which becomes gasoline, has a relatively low boiling point. It is collected and further processed to meet the required specifications.
- Kerosene and Diesel: These fractions have higher boiling points and are collected separately. Kerosene is used for heating and jet fuel, while diesel is a crucial component for powering vehicles and machinery.
- Lighter and Heavier Fractions: The distillation process also separates lighter hydrocarbons, such as ethylene and propylene, which are valuable for the chemical industry. Heavier fractions, like asphaltenes, are not suitable for fuel and are often used for other industrial purposes.
Refining Gasoline: The gasoline fraction is then subjected to further refining processes to enhance its quality and performance. This includes:
- Reformulation: Gasoline is reformulated to improve its octane rating, which is a measure of its resistance to engine knock. This is achieved by adding blending agents and reforming processes.
- Treating and Purification: Various treatments are applied to remove impurities, such as sulfur and nitrogen compounds, to meet environmental standards and ensure the fuel's stability.
- Blending and Storage: Finally, the refined gasoline is blended with other additives, such as antioxidants and detergents, and stored in large tanks before being distributed to gas stations.
Quality Control and Distribution: Throughout the refining process, rigorous quality control measures are implemented to ensure the gasoline meets or exceeds industry standards. Once refined, the gasoline is transported to distribution centers and then to gas stations, where it is sold to consumers for their vehicles.
This distillation process is a critical step in the transformation of crude oil into a usable fuel source, providing the energy needed to power vehicles and various industrial applications. It showcases the intricate and precise nature of modern petroleum refining.
Mitsubishi's Fuel Efficiency: Unlocking the Secrets of Efficient Driving
You may want to see also
Hydrogen Extraction: Electrolysis for Clean Energy Generation
The process of extracting hydrogen for clean energy generation through electrolysis is a promising method to produce fuel for vehicles, offering a sustainable alternative to traditional gasoline or diesel. Electrolysis involves using electricity to split water molecules (H2O) into hydrogen (H2) and oxygen (O2) gases. This technology is a key component in the development of hydrogen fuel cell vehicles, which produce electricity through a chemical reaction between hydrogen and oxygen, emitting only water as a byproduct.
To begin the electrolysis process, you would need an electrolyzer, a device designed to facilitate the splitting of water. The electrolyzer consists of an anode and a cathode separated by an electrolyte, typically a liquid or a solid polymer. When an electric current is applied, water molecules in the electrolyte gain energy and dissociate into hydrogen and oxygen ions. The hydrogen gas is then collected and stored for use as fuel.
The efficiency of hydrogen extraction through electrolysis is a critical factor in its feasibility. Modern electrolyzers can achieve efficiencies of around 65-70%, meaning that for every 100 units of electrical energy input, approximately 65-70 units of hydrogen energy output are produced. This efficiency is continually improving with technological advancements.
Electrolysis can be powered by renewable energy sources such as solar or wind power, making the entire process clean and sustainable. When electricity is generated from these sources, it is fed into the electrolyzer, driving the water-splitting reaction. This approach ensures that the hydrogen produced is 'green' or 'renewable', as it does not contribute to greenhouse gas emissions.
In summary, hydrogen extraction via electrolysis is a viable method for generating clean energy for vehicles. It involves the use of an electrolyzer to split water into hydrogen and oxygen, with the hydrogen being collected as a fuel source. With increasing efficiency and the potential to utilize renewable energy, this technology is a significant step towards a more sustainable and environmentally friendly transportation system.
Top Fuel Funny Car Body Price: A Breakdown
You may want to see also
Frequently asked questions
Fuel extraction from a car is not a typical or recommended practice. It is essential to understand that fuel systems are designed to be refueled through the fuel tank and should not be tampered with. Attempting to extract fuel manually can be dangerous and may void your vehicle's warranty. It is best to consult a professional mechanic or use a fuel transfer pump designed for safe and legal fuel removal.
No, it is not advisable to remove fuel manually. Car fuel tanks are designed to hold a specific amount of fuel, and removing it without proper equipment can lead to fuel contamination, engine performance issues, and potential safety hazards. Always use appropriate tools and methods recommended by the vehicle manufacturer.
Transferring fuel between vehicles should be done with caution and proper safety measures. Here's a general process: Ensure both cars are parked on a level surface, engage the parking brake, and use a fuel transfer pump designed for automotive use. Connect the pump's suction and discharge hoses to the respective fuel tanks, ensuring a secure fit. Start the transfer process slowly to avoid excessive pressure and potential spillage. Monitor the transfer and ensure the fuel is transferred to the receiving tank.
Using a household pump for fuel extraction is not recommended and can be dangerous. Automotive fuel systems operate under specific pressure and temperature conditions, and using non-automotive pumps may lead to fuel contamination, engine damage, or safety risks. Always use equipment designed for the task and follow manufacturer guidelines.
It is good practice to regularly check your car's fuel level to ensure you don't run out of fuel unexpectedly. Most modern vehicles have a fuel gauge that provides an accurate reading of the remaining fuel. It is recommended to check the fuel level at least once a month and before long trips to ensure you have sufficient fuel for your journey.