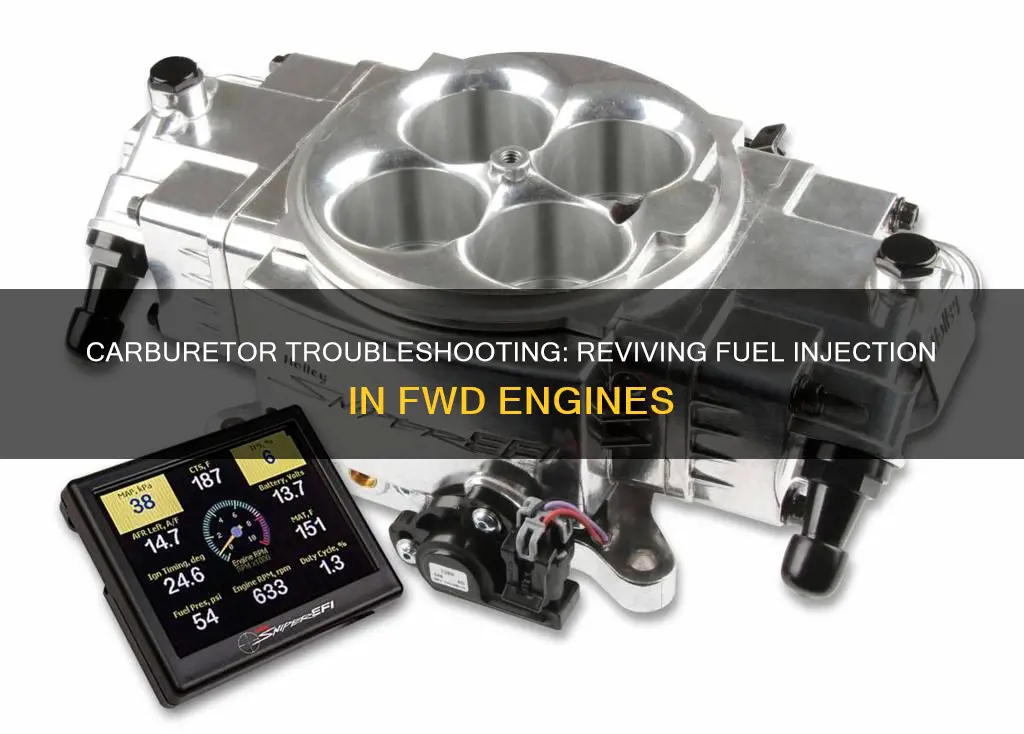
Carburation in a fuel-injected engine is a process that involves mixing air and fuel to create a combustible mixture, which is then ignited in the engine's cylinders. While modern vehicles often use fuel injection systems, which directly inject fuel into the engine's intake manifold or cylinders, some enthusiasts and racers may still want to manually adjust the fuel mixture for optimal performance. This guide will provide an overview of the steps involved in carburating a fuel-injected engine in a front-wheel-drive (FWD) car, including the necessary tools, safety precautions, and techniques to achieve the desired air-fuel ratio.
What You'll Learn
- Fuel Injection Basics: Understand the system, including injectors, pumps, and sensors
- Engine Calibration: Adjust fuel maps and timing for optimal performance
- Airflow Management: Ensure proper air intake and filtration for efficient combustion
- Fuel Pressure Regulation: Monitor and adjust pressure to match engine demands
- Diagnostics and Tuning: Use tools for troubleshooting and fine-tuning fuel injection
Fuel Injection Basics: Understand the system, including injectors, pumps, and sensors
Fuel injection is a sophisticated system that plays a crucial role in modern engines, offering precise control over the fuel-air mixture for optimal performance and efficiency. This technology has evolved from the traditional carburetor system, providing a more reliable and efficient way to deliver fuel to the engine. Here's an overview of the fuel injection system, focusing on its key components: injectors, pumps, and sensors.
Fuel Injectors: These are the heart of the fuel injection system. They are strategically positioned along the intake manifold or directly into the cylinders. When activated, the injectors spray a precise amount of fuel into the intake manifold or directly into the combustion chamber. This process ensures that the fuel is atomized and mixed with air, creating a homogeneous mixture that promotes efficient combustion. The injectors are designed to deliver fuel at high pressure, ensuring a quick and accurate injection process.
Fuel Pumps: The fuel pump is responsible for supplying fuel from the tank to the injectors at the required pressure. It is typically located near the engine and operates continuously to maintain a steady fuel supply. The pump's efficiency is crucial as it directly impacts the system's performance. Modern fuel pumps are designed to provide a consistent fuel flow, ensuring that the injectors receive the necessary pressure to deliver the correct amount of fuel.
Sensors: Sensors are integral to the fuel injection system, providing critical data to the engine's computer. These sensors monitor various parameters such as engine temperature, air intake, and exhaust gases. One of the key sensors is the Mass Airflow (MAF) sensor, which measures the amount of air entering the engine. This data is essential for the engine control unit (ECU) to calculate the correct fuel injection timing and quantity. Other sensors include the oxygen sensors, which monitor the exhaust gases to ensure optimal combustion, and the pressure sensors, which measure fuel pressure to ensure it meets the system's requirements.
The fuel injection system's complexity lies in its ability to precisely manage fuel delivery, ensuring optimal performance and fuel efficiency. It eliminates the need for manual adjustments, as the system automatically calculates and delivers the required fuel based on various engine conditions. This technology has revolutionized engine design, offering improved power, reduced emissions, and enhanced overall performance. Understanding the fuel injection system's components is essential for anyone looking to optimize their vehicle's performance and maintain it effectively.
Maximizing Your Car's Fuel Capacity: A Comprehensive Guide
You may want to see also
Engine Calibration: Adjust fuel maps and timing for optimal performance
Engine calibration is a crucial process when dealing with fuel-injected engines, especially in forward-wheel-drive (FWD) vehicles, as it ensures optimal performance, fuel efficiency, and longevity. The primary goal is to fine-tune the engine's fuel-air mixture and timing to match the specific requirements of the engine's operating conditions. This process involves adjusting the fuel maps and timing, which are essential parameters for a well-performing engine.
Fuel maps are essentially a set of instructions that dictate the amount of fuel to be injected into the engine's cylinders based on various engine operating conditions. These conditions include engine speed, load, and temperature. By calibrating these fuel maps, you can ensure that the engine receives the precise amount of fuel required for efficient combustion at any given moment. This is particularly important in FWD cars, where the engine's performance needs to be balanced with the front wheels' traction and grip.
Adjusting the fuel maps involves a series of steps. First, you'll need to access the engine's control unit (ECU), which is the brain of the engine. The ECU stores the current fuel maps and various sensor data. You can then use specialized software to modify these fuel maps. The process requires a deep understanding of the engine's mechanics and the impact of each adjustment. For instance, increasing the fuel injection rate at higher engine speeds can improve performance but may also lead to excessive emissions. Therefore, precise calibration is essential.
Timing is another critical aspect of engine calibration. It refers to the precise moment when the fuel is injected into the engine's cylinders relative to the piston's position. Proper timing ensures that the fuel ignites at the optimal moment, allowing for efficient combustion. In a fuel-injected engine, timing is often controlled by the ECU, which calculates the best injection timing based on engine speed, load, and other factors. Adjusting the timing can improve power output and responsiveness while also optimizing fuel consumption.
To adjust the timing, you'll need to access the ECU's timing settings. This process may vary depending on the vehicle's make and model. Generally, you'll use the vehicle's onboard diagnostic tool to communicate with the ECU and make adjustments. Fine-tuning the timing can significantly impact the engine's performance, especially during acceleration and high-load conditions. Proper timing ensures that the engine operates smoothly and efficiently, providing the driver with a responsive and powerful driving experience.
In summary, engine calibration is a detailed process that involves adjusting fuel maps and timing to optimize a fuel-injected engine's performance. It requires a thorough understanding of the engine's mechanics and the use of specialized tools and software. By carefully calibrating these parameters, you can ensure that the FWD car's engine operates at its peak, delivering improved performance, fuel efficiency, and overall driving experience.
Fuel Filter Maintenance: DIY Cleaning Tips for Car Owners
You may want to see also
Airflow Management: Ensure proper air intake and filtration for efficient combustion
In the context of optimizing a fuel-injected engine in a front-wheel-drive (FWD) car, airflow management is a critical aspect that directly impacts combustion efficiency. The primary goal is to ensure that the engine receives the right amount of air at the correct temperature and pressure to facilitate efficient combustion of the fuel. This involves a series of steps and considerations to fine-tune the air intake and filtration process.
The first step is to inspect and ensure the air intake system is free from any obstructions. This includes checking the air filter, which is a crucial component in the airflow management process. A clean and well-maintained air filter is essential to prevent dust, dirt, and other contaminants from entering the engine. Regularly replacing the air filter at recommended intervals is a simple yet effective way to maintain optimal airflow. Clogged filters can restrict air flow, leading to reduced engine performance and increased fuel consumption.
The next step is to verify the functionality of the air intake system's components. This includes checking the air dam, which is designed to direct airflow towards the air intake, and ensuring it is securely attached. Additionally, inspect the air box, which houses the air filter and directs air to the engine. Make sure there are no leaks or damage to the air box, as this can disrupt the airflow and negatively impact combustion.
To further optimize airflow, consider the use of an intake manifold or a cold air intake system. An intake manifold distributes air evenly to multiple cylinders, ensuring a consistent fuel-air mixture. Cold air intakes, on the other hand, draw in cooler air, which can improve engine performance by providing more oxygen for combustion. These modifications can enhance the engine's breathing capabilities, resulting in better power output and fuel efficiency.
Lastly, monitoring the engine's performance and adjusting the airflow management system accordingly is essential. This may involve fine-tuning the air-fuel mixture, which can be done through the engine's computer system or by using a fuel injection calculator. By ensuring proper airflow and filtration, you can achieve a well-balanced and efficient combustion process, ultimately improving the overall performance of the fuel-injected engine in your FWD car.
New Cars: Fuel Efficiency Myths Debunked
You may want to see also
Fuel Pressure Regulation: Monitor and adjust pressure to match engine demands
Fuel pressure regulation is a critical aspect of optimizing the performance of a fuel-injected engine, especially in forward-wheel-drive (FWD) vehicles. The primary goal is to ensure that the engine receives the precise amount of fuel required for efficient combustion at all operating conditions. This process involves monitoring the fuel pressure and making adjustments to meet the dynamic demands of the engine.
In a fuel-injected engine, the fuel pressure regulator plays a vital role in maintaining the correct pressure. It is typically located near the fuel pump and is designed to control the flow of fuel to the engine. The regulator's primary function is to maintain a consistent pressure regardless of engine load and speed. When the engine is idling or operating at low loads, the regulator reduces the pressure to ensure a steady flow of fuel for efficient combustion. As the engine demands increase, the regulator opens up, allowing higher pressure to supply the additional fuel required for power generation.
Monitoring fuel pressure is essential to ensure the engine operates within the optimal range. This can be achieved through various methods, including pressure sensors and fuel pressure gauges. These tools provide real-time feedback on the fuel pressure, allowing mechanics and engineers to identify any deviations from the desired range. Regular checks and adjustments are necessary to maintain the fuel pressure within the specified limits, ensuring the engine performs optimally and efficiently.
Adjusting the fuel pressure involves making fine-tuned modifications to the fuel pump or using adjustable pressure regulators. By carefully adjusting the pump's output or the regulator's settings, technicians can fine-tune the fuel pressure to match the engine's requirements. This process requires precision and a thorough understanding of the engine's characteristics and performance. Proper calibration ensures that the engine receives the correct amount of fuel, resulting in improved power output, better fuel economy, and reduced emissions.
In summary, fuel pressure regulation is a critical process in carburating a fuel-injected engine on a FWD car. It involves monitoring and adjusting the fuel pressure to match the engine's demands, ensuring optimal performance and efficiency. By understanding the fuel pressure's role and implementing precise adjustments, mechanics can fine-tune the engine's fuel delivery system, leading to enhanced overall engine functionality.
California's Hydrogen Fuel Cell Car Revolution: A Growing Trend
You may want to see also
Diagnostics and Tuning: Use tools for troubleshooting and fine-tuning fuel injection
When dealing with fuel-injected engines, especially those in front-wheel-drive (FWD) vehicles, diagnostics and tuning can be a complex process. However, with the right tools and knowledge, you can effectively troubleshoot and fine-tune the fuel injection system to optimize performance. Here's a guide on how to approach this task:
Understanding the Fuel Injection System: Begin by familiarizing yourself with the specific fuel injection setup in your FWD car. Different manufacturers use various types of fuel injection systems, such as sequential fuel injection or pump-line-nozzle (PLN) systems. Each system has unique characteristics and requires tailored diagnostic approaches. Research the system's design, components, and potential issues to identify the most relevant diagnostic tools and techniques.
Diagnostic Tools: Invest in a set of specialized tools for fuel injection diagnostics. These tools typically include fuel pressure gauges, fuel flow meters, and engine analyzers or scan tools. Fuel pressure gauges help measure the pressure of the fuel entering the engine, allowing you to identify issues like clogged lines or faulty pumps. Fuel flow meters measure the actual fuel flow rate, which can reveal problems with the injectors or the fuel pump. Engine analyzers or scan tools provide real-time data on engine parameters, enabling you to monitor fuel injection timing, air-fuel ratio, and other critical metrics.
Troubleshooting Steps: When troubleshooting, follow a systematic approach:
- Visual Inspection: Start with a thorough visual inspection of the fuel injection system. Check for any signs of damage, leaks, or contamination. Inspect the fuel lines, injectors, and related components for any visible issues.
- Fuel Pressure Check: Use the fuel pressure gauge to measure the pressure at different engine speeds. Compare the readings to the manufacturer's specifications. Low fuel pressure could indicate a faulty pump or clogged lines, while excessive pressure may suggest a malfunctioning pressure regulator.
- Injector Testing: With the engine off, use a multimeter to test the injectors' resistance. Each injector should have a specific resistance value at rest. Deviations from the expected range may indicate a faulty injector. Additionally, you can perform a leak-down test to check for injector leaks.
- Engine Data Analysis: Connect the engine analyzer or scan tool to the OBD-II port (if applicable) or use the manufacturer's diagnostic interface. Monitor the engine's performance data, including idle speed, air-fuel ratio, and fuel injection timing. Look for any abnormal readings or trends that could indicate system issues.
Fine-Tuning and Adjustments: Once you've identified potential problems, it's time to fine-tune the fuel injection system:
- Fuel Pressure Adjustment: If the fuel pressure is too low, consider adjusting the pressure regulator or replacing the fuel pump. Ensure you follow the manufacturer's guidelines for safe and accurate adjustments.
- Injector Calibration: Adjust the injector calibration to optimize fuel delivery. This may involve changing the fuel injection timing, spray angle, or other parameters. Fine-tuning the injectors can significantly impact engine performance and fuel efficiency.
- Air-Fuel Ratio Optimization: Use the engine analyzer to adjust the air-fuel ratio until it matches the manufacturer's specifications. A lean or rich mixture can lead to performance issues, so precise tuning is crucial.
Remember, proper training and experience are essential when working with fuel injection systems. Always refer to the vehicle's service manual and consult with experienced mechanics when performing diagnostics and tuning to ensure accuracy and safety.
Electric Cars: Fuel Savings or Just a Myth?
You may want to see also
Frequently asked questions
Carburetor conversion in a fuel-injected engine is not a common or recommended practice for FWD cars. These engines are designed to run efficiently with electronic fuel injection, which provides precise control over the fuel-air mixture. Attempting to add a carburetor can lead to performance issues, reduced fuel efficiency, and potential engine damage. It's best to leave the fuel injection system intact and focus on maintaining it for optimal performance.
While adding a carburetor might seem like a way to increase power, it is generally not beneficial for a fuel-injected engine. The electronic fuel injection system already provides the engine with the optimal fuel-air mixture for efficient combustion. A carburetor would introduce a simpler, less precise fuel delivery method, likely resulting in reduced power, poorer fuel economy, and increased emissions. It's recommended to stick with the factory-installed fuel injection system for the best performance.
Retrofitting a carburetor onto a fuel-injected engine can have several negative consequences. Firstly, it can lead to an improper air-fuel mixture, causing the engine to run rich, which may result in reduced performance, increased emissions, and potential engine damage. Secondly, the engine's computer controls are designed to work with fuel injection, and adding a carburetor can interfere with these controls, leading to erratic behavior. It's crucial to respect the original design and maintain the fuel injection system for the best and safest engine operation.