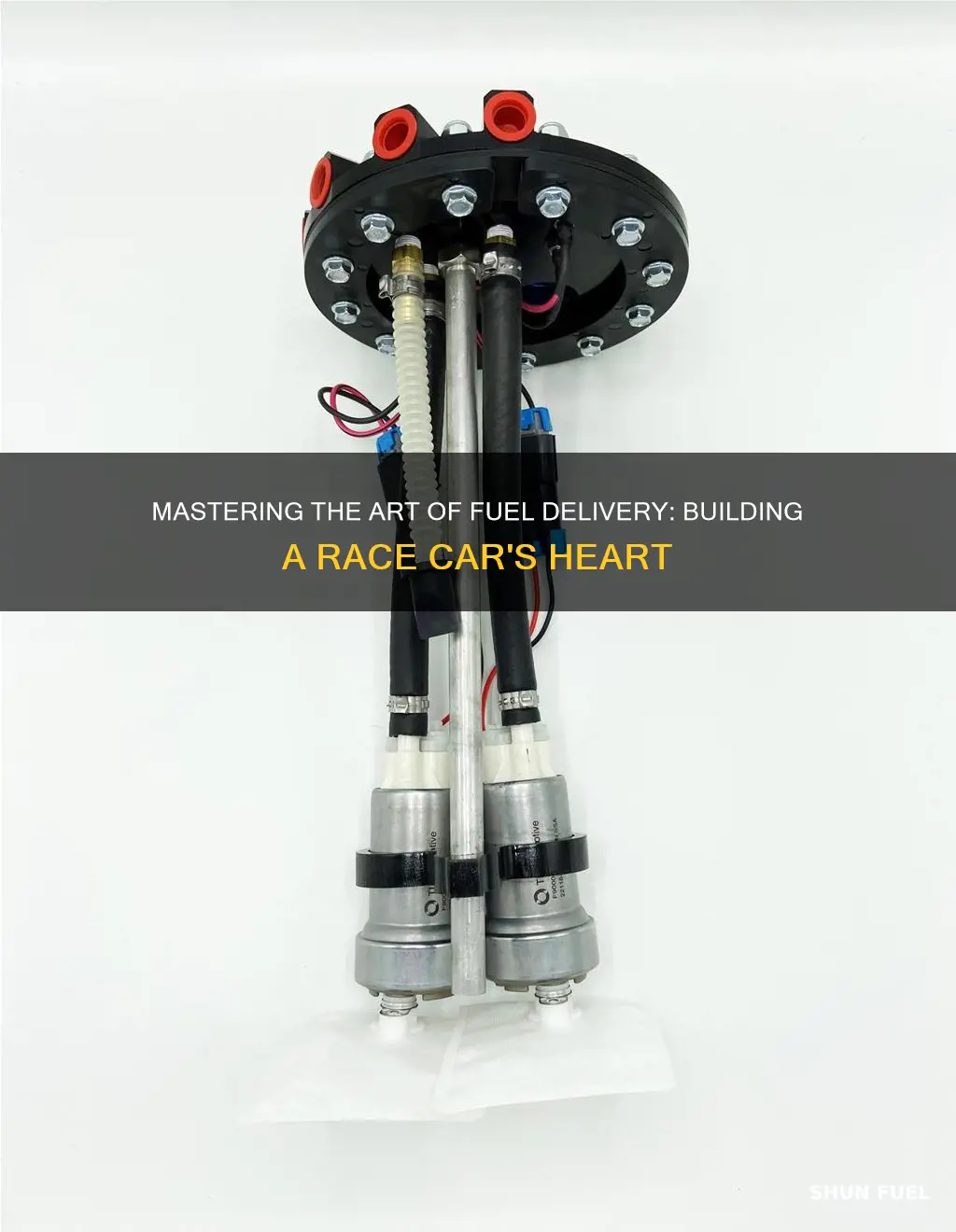
Building a race car fuel system is a complex but rewarding process that requires careful planning and execution. It involves selecting the right components, such as fuel tanks, pumps, lines, and injectors, and ensuring they are properly installed and configured to meet the specific demands of high-performance racing. This guide will provide a comprehensive overview of the key steps and considerations involved in designing and constructing an efficient and reliable fuel system for your race car, covering everything from material choices to system testing and optimization.
What You'll Learn
- Fuel Tank Selection: Choose a tank with high-pressure capacity and corrosion resistance
- Fuel Pump Installation: Install a high-flow pump with a suitable capacity for the engine
- Fuel Lines Routing: Route lines to ensure minimal pressure loss and no kinks
- Fuel Filters: Use multiple filters to protect the system from contaminants
- Fuel Injection System: Design an efficient injection system for precise fuel delivery
Fuel Tank Selection: Choose a tank with high-pressure capacity and corrosion resistance
When designing a fuel system for a race car, selecting the right fuel tank is a critical component that can significantly impact performance and safety. The fuel tank must be able to withstand the high pressures and demanding conditions of racing, ensuring reliable fuel supply while maintaining structural integrity. One of the primary considerations is the tank's pressure capacity. Race cars operate under extreme conditions, with rapid acceleration and deceleration, which subject the fuel system to rapid pressure fluctuations. A fuel tank with a high-pressure capacity is essential to handle these dynamic changes without compromising performance. High-pressure tanks are designed to maintain a consistent fuel supply, ensuring that the engine receives the required amount of fuel even during intense racing moments.
Corrosion resistance is another vital aspect of fuel tank selection. Racing environments are often harsh, with exposure to various chemicals, fuels, and extreme temperatures. Over time, these factors can lead to corrosion, compromising the tank's structural integrity and potentially causing fuel leaks. To prevent such issues, choose a fuel tank made from materials that offer excellent corrosion resistance. Common materials include high-density polyethylene (HDPE) and aluminum alloys, which are known for their ability to resist corrosion and maintain their structural properties in demanding conditions. These materials ensure the longevity of the fuel system and reduce the risk of fuel contamination, which could negatively impact engine performance.
The design and construction of the fuel tank also play a crucial role. A well-designed tank should have a robust structure with reinforced walls to withstand the forces exerted during racing. It should feature a smooth interior surface to minimize fuel sloshing and ensure an even distribution of fuel. Additionally, consider the placement of the tank. In race cars, the fuel tank's position can affect weight distribution and overall vehicle balance. A strategically placed tank can contribute to better handling and stability, allowing for precise control during high-speed maneuvers.
Furthermore, the fuel tank's capacity should be carefully evaluated based on the car's fuel requirements and race duration. A race car's fuel system must provide sufficient fuel for the entire race, considering factors like fuel consumption rates and refueling strategies. Selecting a tank with an appropriate capacity ensures that the driver can push the car to its limits without the fear of running out of fuel. In summary, when building a race car fuel system, the fuel tank's high-pressure capacity and corrosion resistance are non-negotiable. These factors directly influence the system's reliability, performance, and safety, making them essential considerations in the design process.
Butane's Potential: Could It Power Your Next Car Ride?
You may want to see also
Fuel Pump Installation: Install a high-flow pump with a suitable capacity for the engine
When building a race car fuel system, one of the critical components is the fuel pump, which ensures a consistent and efficient fuel supply to the engine. The installation process requires careful consideration to match the pump's capacity with the engine's demands for optimal performance.
The first step is to select a high-flow fuel pump that can handle the increased power and speed of a race car engine. High-flow pumps are designed to deliver a larger volume of fuel at higher pressures, which is essential for maximizing power output. Look for pumps with a flow rate that exceeds the engine's requirements, typically measured in gallons per minute (GPM). For high-performance engines, a flow rate of 10-15 GPM or more is often recommended.
Installation begins by locating the ideal position for the pump. It should be placed close to the fuel tank to minimize pressure loss and ensure a steady fuel supply. Mount the pump securely, using appropriate brackets or frames to support its weight and maintain alignment. Ensure the pump is easily accessible for maintenance and has adequate ventilation to prevent overheating.
Connect the fuel lines to the pump, using high-quality, flexible hoses with a suitable inner diameter to handle the increased fuel flow. The lines should be routed away from heat sources and sharp bends to prevent restrictions and ensure smooth fuel flow. Consider using a fuel filter and pressure regulator in the line to maintain optimal pressure and protect the engine from contaminants.
Finally, test the fuel pump installation thoroughly. Check for any leaks at the connections and ensure the pump operates within the specified voltage and current range. Monitor the fuel pressure using a gauge to verify it meets the engine's requirements. Proper installation and calibration of the fuel pump are crucial for achieving the desired engine performance and ensuring a reliable fuel supply during racing.
Flex Fuel: Can Your Car Handle the Switch?
You may want to see also
Fuel Lines Routing: Route lines to ensure minimal pressure loss and no kinks
When designing the fuel system for a race car, proper routing of fuel lines is crucial to maintaining optimal performance and ensuring the safety of the vehicle. The goal is to minimize pressure loss and eliminate any potential kinks or restrictions that could impact fuel flow. Here's a detailed guide on how to achieve this:
Understanding the Basics: Begin by familiarizing yourself with the different types of fuel lines available, such as steel, aluminum, or braided lines. Each material has unique properties, and the choice depends on factors like pressure requirements, temperature resistance, and flexibility. For high-performance applications, braided lines are often preferred for their ability to withstand extreme conditions.
Route Planning: Start by mapping out the fuel lines' path, considering the vehicle's layout and available space. The goal is to keep the lines as straight and short as possible, reducing the potential for pressure drops. Avoid sharp bends and kinks, as these can restrict fuel flow and cause unnecessary stress on the lines. Aim for a smooth, continuous path that integrates seamlessly with the vehicle's structure.
Minimizing Turns and Bends: When routing the fuel lines, strive for minimal turns and sharp angles. Each bend introduces friction and potential pressure loss. Consider using elbows and fittings with smooth, gradual curves to reduce these effects. For long runs, you might need to use flexible hoses, but ensure they are securely fastened to prevent movement-induced pressure drops.
Securing the Lines: Properly secure the fuel lines to prevent movement and potential damage. Use high-quality clamps or tie-downs that can withstand the forces generated during acceleration and deceleration. Avoid tight bends or kinks by ensuring the lines are not pinched or crushed. Regularly inspect the lines for any signs of wear or damage, especially in areas prone to vibration or heat.
Consideration of Fuel Flow: Keep in mind that fuel flow rate and pressure requirements vary depending on the engine's needs. Route the lines to accommodate the expected fuel flow, ensuring that the lines can handle the volume and pressure without introducing unnecessary restrictions. This might involve using larger-diameter lines or multiple lines in parallel to maintain optimal performance.
By following these guidelines, you can create a fuel system that delivers fuel efficiently and reliably to the engine, contributing to the overall performance and success of the race car. Proper routing is a critical aspect of building a high-performance fuel system, ensuring that every drop of fuel reaches the engine when needed.
Unleash the Power: Hydrogen Fuel for Cars Explained
You may want to see also
Fuel Filters: Use multiple filters to protect the system from contaminants
When it comes to building a race car fuel system, one of the most critical components to consider is the fuel filter system. The primary purpose of using multiple filters is to ensure the highest level of protection against contaminants, which can cause significant performance issues and even engine damage. Here's a detailed guide on why and how to implement this strategy:
Multiple filters are essential because a single filter might not be sufficient to handle the high-pressure, high-flow environment of a race car's fuel system. Contaminants such as water, dirt, and debris can enter the system through various points, including the fuel tank, lines, and injectors. These particles can cause blockages, leading to reduced fuel flow, poor engine performance, and potential damage to the fuel injectors. By using multiple filters, you create a layered defense system, ensuring that contaminants are caught at multiple stages, reducing the risk of system failure.
The first filter in the sequence should be a primary filter, often located near the fuel tank. This filter is designed to capture larger particles and debris, preventing them from entering the system. It is typically a high-capacity filter that can handle the volume of fuel flowing through the system. After the primary filter, a secondary filter can be installed closer to the engine. This filter is more precise and is designed to capture smaller contaminants, such as water droplets and fine particles. The secondary filter ensures that any remaining impurities are removed before the fuel reaches the injectors.
In some cases, a third filter might be added, especially in high-performance applications. This additional filter provides an extra layer of protection, ensuring that the fuel system is as clean as possible. It is particularly useful when dealing with fuels that have a higher risk of contamination, such as ethanol-blended fuels. By using multiple filters, you create a robust defense mechanism that can handle the demanding conditions of racing. This setup ensures that the fuel injectors receive clean, contaminant-free fuel, optimizing engine performance and reliability.
When implementing this strategy, it's crucial to choose the right filters for your specific application. Consider factors such as filter media, capacity, and flow rate to ensure they meet the requirements of your race car's fuel system. Regular maintenance, including filter replacement, is also vital to keep the system effective. By following this approach, you can build a robust and reliable fuel system, ensuring your race car performs at its best while minimizing the risk of fuel-related issues.
Honda's Fuel-Efficient Cars: Unlocking the Secret to Efficient Driving
You may want to see also
Fuel Injection System: Design an efficient injection system for precise fuel delivery
The fuel injection system is a critical component in the performance and efficiency of a race car's engine. Designing an efficient and precise fuel delivery system involves several key considerations to optimize power output and ensure reliable operation. Here's a detailed guide on how to approach this design process:
Understanding the Basics: Begin by familiarizing yourself with the fundamentals of fuel injection. This includes understanding the different types of fuel injection systems, such as port injection and direct injection. Port injection involves injecting fuel into the intake manifold, while direct injection delivers fuel directly into the combustion chamber. Each method has its advantages and is chosen based on the specific requirements of the engine and the desired performance characteristics.
Fuel Pump and Pressure Regulation: A high-performance fuel injection system relies on a robust fuel pump to deliver the required volume and pressure of fuel. The pump should be capable of providing a precise and consistent flow rate to ensure accurate fuel metering. Consider using a pump with a variable output control to adjust the fuel pressure according to engine load and speed. This allows for efficient fuel delivery during high-performance driving conditions. Additionally, incorporate a fuel pressure regulator to maintain optimal pressure, ensuring the engine receives the correct amount of fuel at all times.
Precision Fuel Injectors: The heart of the fuel injection system are the injectors themselves. Design the injector nozzles to deliver fuel with extreme precision. This involves calculating the nozzle orifice size, spray pattern, and fuel atomization to optimize combustion. High-performance injectors should provide a fine mist of fuel, ensuring complete combustion and minimizing fuel consumption. Consider using injectors with adjustable flow rates to fine-tune the fuel delivery for different engine speeds and loads.
Electronic Control Unit (ECU) and Sensor Integration: Efficient fuel injection requires a sophisticated ECU to manage the process. The ECU should be programmed to receive input from various sensors, such as engine temperature, speed, and load sensors. These sensors provide real-time data to the ECU, allowing for precise fuel mapping and adjustment. The ECU calculates the optimal fuel injection timing, rate, and duration, ensuring the engine receives the correct amount of fuel for optimal performance. Advanced ECUs can also incorporate learning capabilities, adapting to different driving conditions and engine characteristics.
Fuel Rail and Delivery System: Design a fuel rail system that ensures an even distribution of fuel to all cylinders. The fuel rail should have a high-pressure design to facilitate quick response times and efficient fuel delivery. Consider using a fuel filter and separator to maintain fuel quality and prevent contamination. Additionally, implement a fuel return system to recycle excess fuel, improving overall efficiency.
By carefully considering these design elements, you can create a fuel injection system that delivers precise fuel metering, optimizes combustion, and enhances the overall performance of a race car engine. This approach ensures efficient fuel usage, improved power output, and reliable operation, giving the vehicle a competitive edge on the track.
Hydrogen Fuel Cell Cars: A Guide to Filling Up
You may want to see also
Frequently asked questions
Race car fuel systems typically utilize lightweight and high-strength materials such as aluminum, carbon fiber, and specialized plastics. These materials offer excellent strength-to-weight ratios, ensuring the system can withstand high pressures and temperatures while keeping the overall weight low.
Selecting the appropriate fuel pump involves considering factors like desired fuel flow rate, system pressure requirements, and engine specifications. It's crucial to match the pump's capacity with the engine's demands. Consulting with experts or referring to manufacturer guidelines can help ensure the right pump is chosen for optimal performance.
A race car fuel system comprises several critical components, including the fuel tank, fuel lines, fuel filter, pump, and injectors or carburetor. Each component plays a vital role in delivering fuel efficiently and reliably to the engine. Proper installation and maintenance of these parts are essential for optimal performance.
Achieving a tight seal in the fuel system is crucial to prevent fuel leaks and maintain system integrity. This can be accomplished by using high-quality fuel lines with appropriate fittings, ensuring all connections are secure, and applying vacuum-forming techniques to create custom-fitted fuel tanks. Regular inspections and leak checks are also recommended.
To optimize fuel efficiency, consider factors such as fuel injection calibration, engine tuning, and aerodynamic improvements. Fine-tuning the fuel-air mixture, using advanced fuel management systems, and minimizing drag can all contribute to better fuel economy. Additionally, regular maintenance and keeping the fuel system clean are essential for optimal performance.