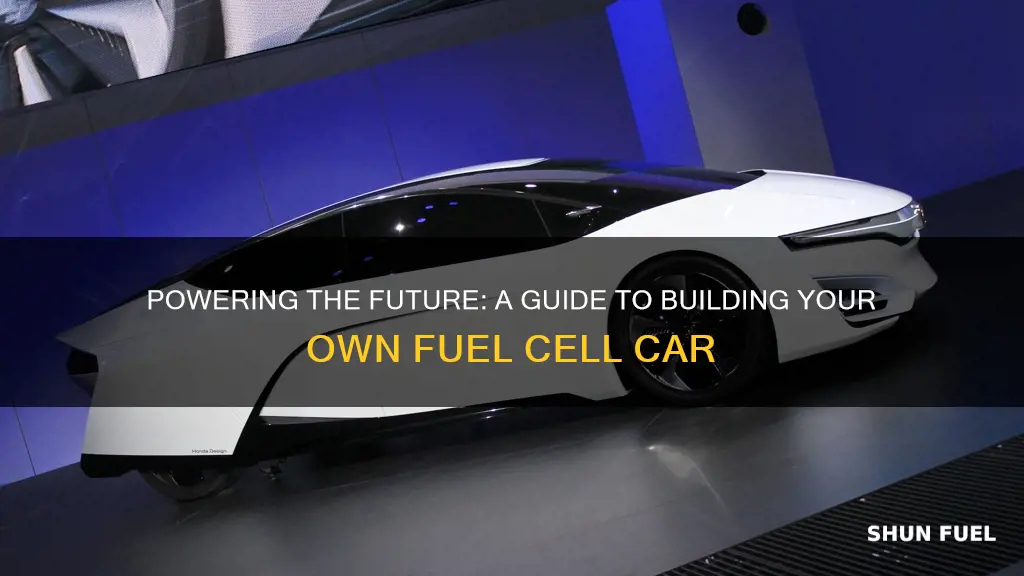
Building a fuel cell car is an innovative project that involves harnessing the power of hydrogen to generate electricity for propulsion. This process begins with the design and construction of a fuel cell stack, which is the heart of the vehicle, converting chemical energy from hydrogen and oxygen into electricity through an electrochemical reaction. The electricity then powers an electric motor, driving the car's wheels. Key components include a fuel cell, a hydrogen storage system, and an air supply system for oxygen. The construction requires expertise in engineering, materials science, and energy systems, as well as careful consideration of safety and efficiency to create a sustainable and efficient mode of transportation.
What You'll Learn
- Materials and Components: Select lightweight, durable materials for the car's structure and fuel cell components
- Fuel Cell Design: Engineer compact, efficient fuel cell stacks with optimized cooling and ventilation systems
- Energy Storage: Integrate advanced batteries to store excess energy and ensure stable power supply
- Power Management: Develop sophisticated control systems to manage power distribution and vehicle performance
- Safety and Efficiency: Implement safety measures and optimize energy efficiency for long-term sustainability
Materials and Components: Select lightweight, durable materials for the car's structure and fuel cell components
When building a fuel cell car, the choice of materials is critical to achieving a lightweight, efficient, and durable vehicle. The primary goal is to minimize weight while ensuring structural integrity and the longevity of the fuel cell components. Here's a detailed guide on the materials and components selection process:
Lightweight Materials for the Vehicle Structure:
- Carbon Fiber Composites: Carbon fiber-reinforced polymers (CFRP) are an excellent choice for the car's body and chassis. Carbon fiber offers exceptional strength-to-weight ratios, making it incredibly lightweight yet robust. It can withstand structural stresses while keeping the overall weight low.
- Aluminum Alloys: Aluminum is a traditional lightweight metal used in automotive engineering. Modern aluminum alloys provide excellent corrosion resistance and strength, making them suitable for body panels, engine components, and chassis structures.
- High-Strength Steel: While steel is heavier than some alternatives, advanced high-strength steel (AHSS) offers improved strength and durability. It can be used for critical structural elements, ensuring the vehicle's safety and stability without adding excessive weight.
- Composite Materials: Various composite materials, such as glass fiber-reinforced polymers, can be utilized for non-structural components like body panels and interior trim. These materials provide design flexibility and contribute to weight reduction.
Durable Materials for Fuel Cell Components:
- Fuel Cell Membrane: The membrane within a fuel cell is a critical component. It should be durable, corrosion-resistant, and capable of withstanding harsh chemical environments. Materials like perfluorinated sulfonic acid (PFSA) polymers are commonly used for their stability.
- Catalyst Support: Catalysts are essential for the electrochemical reactions in fuel cells. The support structure for catalysts should be durable and resistant to degradation. Ceramic materials or carbon-based composites are often employed for this purpose.
- Gas Diffusion Layers (GDL): GDLs facilitate the transport of gases in and out of the fuel cell. Materials like polypropylene or carbon-based composites with high permeability and mechanical strength are ideal for this application.
- Bipolar Plates: These plates separate the fuel and air channels in a fuel cell stack. They require materials with excellent thermal and chemical stability. Stainless steel or specialized alloys with added corrosion resistance are commonly used.
The design and selection of materials should consider factors like manufacturing processes, cost-effectiveness, and the overall environmental impact of the vehicle. Advanced manufacturing techniques, such as 3D printing or molding, can be employed to create complex structures and optimize material usage. Additionally, recycling and reusing materials can contribute to the sustainability of the fuel cell car project.
Understanding Fuel Injection: Can You DIY Your Car's Injection System?
You may want to see also
Fuel Cell Design: Engineer compact, efficient fuel cell stacks with optimized cooling and ventilation systems
Fuel cell technology is a key component in the development of efficient and environmentally friendly vehicles. When designing a fuel cell stack for a car, engineers must focus on creating a compact and highly efficient system while ensuring optimal cooling and ventilation to maintain performance and longevity. Here's an overview of the design process:
Compact Stack Design: The primary goal is to minimize the size and weight of the fuel cell stack while maximizing power output. This involves careful arrangement of the fuel cell components. Each fuel cell consists of a membrane electrode assembly (MEA) sandwiched between two gas diffusion layers (GDLs). The MEAs are typically made of a polymer electrolyte membrane (PEM) and catalysts. Engineers aim to stack these cells efficiently, ensuring proper alignment of the gas inlets and outlets. By optimizing the cell geometry and using advanced manufacturing techniques, such as micro-milling or laser cutting, it is possible to create a compact stack with reduced dimensions.
Cooling and Heat Management: Efficient cooling is critical to prevent overheating and maintain the performance of the fuel cell stack. The design should incorporate a robust cooling system that can handle the heat generated during the electrochemical reaction. One common approach is to use a liquid cooling system, where a coolant flows through channels within the stack, absorbing heat from the cells. The coolant can then be directed to a radiator or a heat exchanger to dissipate the heat. Alternatively, air cooling can be employed by designing the stack with fins or channels to increase the surface area, allowing for efficient heat transfer to the surrounding air. Proper heat management ensures stable operation and extends the lifespan of the fuel cell components.
Ventilation and Gas Management: Effective ventilation is essential to supply the required reactants (hydrogen and oxygen) to the fuel cells and expel the reaction byproducts. Engineers must design a ventilation system that ensures a consistent gas flow rate throughout the stack. This involves creating channels for gas distribution and collection, often with a precise geometry to maintain uniform gas pressure and flow. The ventilation system should also consider the removal of water vapor and carbon dioxide produced during the reaction to prevent backpressure and maintain optimal operating conditions.
Optimization and Testing: Fuel cell stack design requires extensive optimization and testing. Engineers use computational fluid dynamics (CFD) simulations to model the gas and coolant flow, ensuring efficient heat and mass transfer. Prototyping and laboratory testing are crucial to validate the design. This includes performance testing to measure power output, current density, and voltage under various conditions. Additionally, durability testing simulates real-world operating conditions to assess the stack's longevity and reliability. Through iterative design and testing, engineers can fine-tune the stack's dimensions, materials, and cooling/ventilation systems to achieve the desired efficiency and performance.
By focusing on compact design, efficient cooling, and optimized ventilation, engineers can create fuel cell stacks that power electric vehicles with high energy density and reliable performance. This approach contributes to the overall goal of developing sustainable transportation solutions.
Hydrogen Fuel Cells: The Green Revolution on the Road?
You may want to see also
Energy Storage: Integrate advanced batteries to store excess energy and ensure stable power supply
Energy storage is a critical component of any fuel cell vehicle, as it ensures a stable and reliable power supply, even when the fuel cell is not generating electricity. The primary goal is to store excess energy produced during periods of high generation and release it when needed, maintaining a consistent power output. This is particularly important for fuel cell cars, as they rely on a continuous supply of electricity to power their electric motors.
Advanced batteries, often lithium-ion, are the most commonly used energy storage systems in fuel cell vehicles. These batteries are designed to store a significant amount of energy efficiently and release it rapidly when required. The key to successful energy storage lies in the careful selection and integration of these batteries into the vehicle's electrical system.
When designing the energy storage system, engineers must consider several factors. Firstly, the battery capacity should be sufficient to store the excess energy generated during peak fuel cell operation. This excess energy can be used to charge the batteries, ensuring they are fully charged and ready for use. Secondly, the batteries should be able to discharge quickly and efficiently to meet the power demands of the vehicle, especially during acceleration or when additional power is required.
The integration process involves mounting the batteries in a way that ensures optimal weight distribution and easy access for maintenance. They are typically placed in the vehicle's underbody or rear compartment, where they can be protected from external elements. The batteries are connected to the fuel cell and electric motor through sophisticated wiring harnesses, ensuring efficient power transfer.
Additionally, advanced battery management systems (BMS) are employed to monitor and control the charging and discharging processes. The BMS regulates the flow of energy, prevents overcharging or over-discharging, and provides protection against short circuits and other potential issues. This system ensures the longevity and safety of the batteries, allowing for efficient energy storage and supply.
In summary, energy storage in fuel cell cars is a complex but essential process. By utilizing advanced batteries and sophisticated management systems, engineers can ensure a stable power supply, optimize energy usage, and contribute to the overall efficiency and performance of the vehicle. This technology is a key enabler for the widespread adoption of fuel cell vehicles, offering a sustainable and environmentally friendly transportation solution.
Wind-Powered Cars: A Sustainable Alternative to Fuel Cars?
You may want to see also
Power Management: Develop sophisticated control systems to manage power distribution and vehicle performance
Power management is a critical aspect of fuel cell vehicle design, as it directly influences the efficiency, performance, and overall driving experience. The primary goal is to create a sophisticated control system that optimizes power distribution between the fuel cell, electric motor, and various vehicle systems. This involves a complex interplay of sensors, microcontrollers, and software algorithms to ensure seamless and efficient operation.
At the heart of this system is the power electronics unit, which acts as the brain of the fuel cell car. It receives input from various sensors, including temperature sensors to monitor the fuel cell's operating conditions, current sensors to measure power flow, and speed sensors for vehicle dynamics. These sensors provide real-time data, allowing the control system to make informed decisions. The microcontroller, often a powerful embedded system, processes this data and executes control strategies. It calculates the required power output for the electric motor, adjusts fuel cell operation, and manages energy storage, ensuring the vehicle's performance meets the driver's needs.
One key challenge is balancing power generation and consumption. Fuel cells produce electricity, which powers the electric motor and other vehicle systems. The control system must manage this power distribution efficiently. During acceleration, more power is demanded, and the system should dynamically allocate power to the motor while ensuring the fuel cell operates within safe limits. When cruising, the system can optimize power usage, potentially recharging the fuel cell's storage system or powering auxiliary components. This dynamic power management is crucial for extending the vehicle's range and ensuring a smooth driving experience.
Advanced control algorithms play a vital role in this process. These algorithms can predict and respond to changes in power demand and supply. For instance, they can anticipate the driver's acceleration pattern and adjust power distribution accordingly. By learning from driving patterns, the system can also optimize energy usage, reducing waste and improving overall efficiency. Additionally, the control system should monitor and control the fuel cell's voltage and current to maintain optimal performance and prevent damage.
In summary, developing a sophisticated power management system is essential for fuel cell car success. It requires a deep understanding of power electronics, sensor integration, and control theory. The system must be capable of real-time decision-making, optimizing power distribution, and ensuring the vehicle's performance meets or exceeds that of conventional cars. With continuous advancements in control algorithms and hardware, fuel cell vehicles can become more efficient, reliable, and appealing to a wider range of consumers.
Optimize Engine Performance: A Guide to Cleaning Car Fuel Injectors
You may want to see also
Safety and Efficiency: Implement safety measures and optimize energy efficiency for long-term sustainability
When building a fuel cell car, safety and efficiency are paramount considerations to ensure the vehicle's long-term sustainability and performance. Here's a detailed guide on implementing safety measures and optimizing energy efficiency:
Safety Measures:
- Robust Fuel Cell Design: Construct the fuel cell with a focus on durability and safety. Use high-quality materials that can withstand extreme conditions, such as pressure vessels made from advanced composites or alloys. Ensure the fuel cell system is designed to handle potential overpressure situations and incorporate safety relief mechanisms to prevent damage or hazards.
- Advanced Monitoring Systems: Implement a comprehensive monitoring system to track various parameters in real-time. This includes fuel cell voltage, temperature, pressure, and hydrogen levels. Install sensors and control units that can detect anomalies, such as sudden pressure spikes or temperature deviations, and trigger appropriate responses, like automatic shutdown or warning signals to the driver.
- Fire and Explosion Prevention: Hydrogen fuel cells can pose fire and explosion risks if not managed properly. Install fire suppression systems, such as hydrogen-sensitive detectors and automated extinguishing mechanisms, to quickly respond to potential fires. Ensure proper ventilation and consider using fire-resistant materials in the fuel cell compartment.
- Driver Assistance and Warning Systems: Develop an intuitive driver interface with clear indicators and warnings. Provide visual and auditory alerts for critical issues, such as low hydrogen levels or system malfunctions. Implement advanced driver assistance systems (ADAS) to enhance safety, including lane-keeping assist, adaptive cruise control, and automatic emergency braking.
Energy Efficiency Optimization:
- Efficient Hydrogen Storage: Optimize hydrogen storage systems to maximize energy density and minimize weight. Explore advanced storage technologies like metal hydrides or carbon-based materials that offer higher storage capacities and faster refueling times. Ensure the storage system is designed to handle pressure and temperature variations safely.
- Power Management and Control: Develop an intelligent power management system to optimize energy distribution and usage. This system should dynamically adjust power output based on driving conditions and load demands. Implement regenerative braking systems to capture and reuse kinetic energy, improving overall efficiency.
- Lightweight Materials and Design: Utilize lightweight materials throughout the vehicle's structure to reduce mass and improve energy efficiency. Consider advanced alloys, carbon fiber composites, or even lightweight polymers for the body and components. Minimize unnecessary weight without compromising structural integrity.
- System Integration and Optimization: Integrate all fuel cell components, including the fuel cell stack, power electronics, and storage systems, to optimize overall efficiency. Minimize energy losses during power conversion and transmission. Regularly optimize the system through testing and simulation to identify areas for improvement.
By focusing on these safety and efficiency aspects, you can create a fuel cell car that is not only environmentally friendly but also reliable, safe, and highly efficient, making it a viable and sustainable transportation solution.
Fuel Injector Cleaner: Too Much of a Good Thing?
You may want to see also
Frequently asked questions
Building a fuel cell car involves several critical components. The primary one is the fuel cell stack, which is the heart of the vehicle, converting chemical energy from hydrogen and oxygen into electricity through an electrochemical reaction. This electricity powers the car's electric motor(s), which drive the wheels. Additionally, you'll need a hydrogen storage system, typically a high-pressure tank, to store the fuel, and a cooling and ventilation system to manage the temperature and humidity inside the fuel cell stack. Other essential parts include a fuel cell control system, an air supply system for the oxygen required in the reaction, and an exhaust system to manage the byproducts.
Sourcing materials and infrastructure for a fuel cell car project can be a complex task. You can start by identifying reputable fuel cell manufacturers and suppliers who can provide the required components, including the fuel cell stack, hydrogen storage tanks, and control systems. Many companies offer turn-key solutions, providing the necessary hardware and software integration. For hydrogen fuel, you may need to work with hydrogen producers or distributors to ensure a reliable supply. Additionally, building the necessary infrastructure, such as hydrogen refueling stations, might require collaboration with local governments and energy companies to establish the required infrastructure for hydrogen distribution and refueling.
Designing and constructing a fuel cell car presents several challenges and considerations. One significant challenge is optimizing the size and weight of the fuel cell stack to fit within the vehicle's structure while ensuring sufficient power output. Fuel cell efficiency and longevity are also critical factors, as they directly impact the vehicle's performance and range. Another consideration is the safety of hydrogen storage and handling, as it requires specialized knowledge and adherence to strict regulations. Additionally, the overall cost of the vehicle, including the fuel cell system and supporting infrastructure, is a major factor in making fuel cell cars a viable and competitive alternative to traditional internal combustion engines.