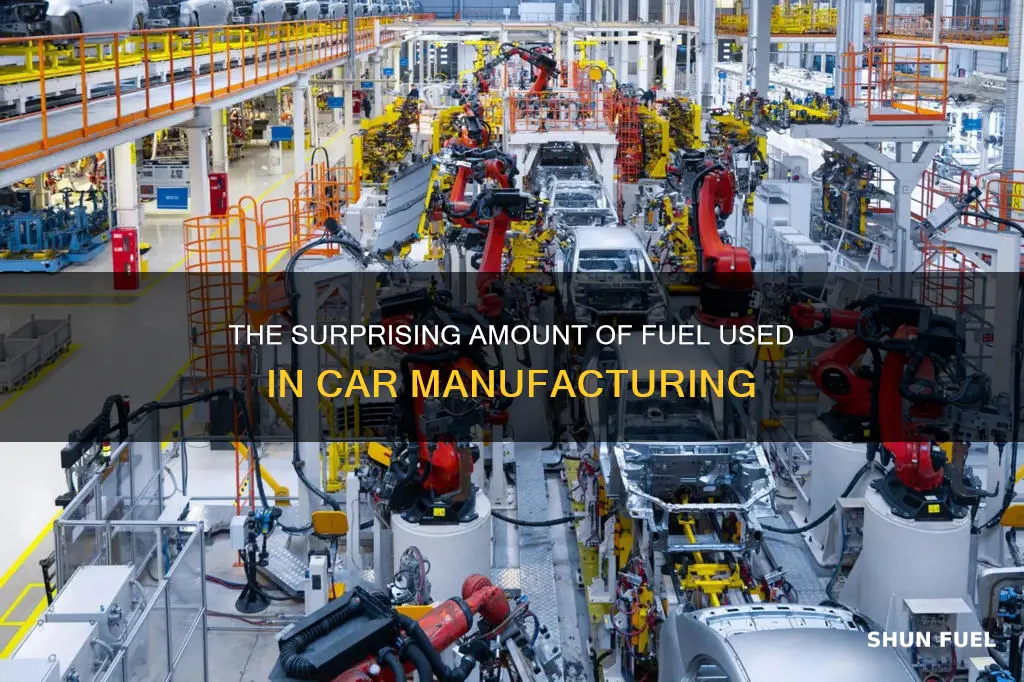
Building a car requires significant amounts of fuel, which is a critical component in the manufacturing process. The exact amount of fuel used can vary depending on the type of vehicle, its size, and the materials used in its construction. Generally, the production of a car involves the use of various fuels, including gasoline, diesel, and even biofuels, which are derived from renewable sources. Understanding the fuel consumption during the manufacturing phase is essential for optimizing the efficiency of the production process and reducing the environmental impact of the automotive industry.
What You'll Learn
- Fuel Efficiency Standards: Regulations dictate the fuel efficiency of vehicles, impacting their fuel consumption
- Engine Design: The design of the engine directly affects fuel usage, with more efficient designs reducing consumption
- Vehicle Weight: Lighter vehicles require less fuel to accelerate and maintain speed, improving efficiency
- Aerodynamics: Smooth vehicle shapes reduce drag, leading to lower fuel consumption over longer distances
- Fuel Injection Systems: Advanced fuel injection technology optimizes fuel-air mixture, enhancing engine performance and fuel economy
Fuel Efficiency Standards: Regulations dictate the fuel efficiency of vehicles, impacting their fuel consumption
The concept of fuel efficiency standards is a crucial aspect of the automotive industry, aiming to reduce the environmental impact of vehicles and promote sustainable transportation. These regulations are designed to ensure that cars meet specific fuel economy targets, which directly influence their fuel consumption and overall efficiency. By setting these standards, governments and regulatory bodies aim to encourage manufacturers to produce vehicles that are more environmentally friendly and cost-effective for consumers.
Fuel efficiency standards typically specify the maximum amount of fuel a vehicle can consume over a certain distance, often measured in miles per gallon (mpg) or liters per 100 kilometers (l/100 km). These regulations vary across different regions and countries, with some areas having more stringent requirements. For instance, the United States has implemented Corporate Average Fuel Economy (CAFE) standards, which set targets for the entire vehicle fleet of a manufacturer. These standards have evolved over time, pushing carmakers to develop more efficient engines and improve overall vehicle design.
The impact of these regulations is significant, as they directly affect the way vehicles are engineered and produced. Manufacturers are compelled to invest in research and development to meet the specified fuel efficiency targets. This often involves employing advanced technologies such as direct fuel injection, turbocharging, and hybrid systems. As a result, modern vehicles are becoming more efficient, burning less fuel for the same level of performance, and reducing the overall environmental footprint of the automotive industry.
One of the key benefits of fuel efficiency standards is the potential for reduced fuel consumption and lower operating costs for vehicle owners. Cars that meet or exceed these standards are likely to have better fuel economy, allowing drivers to travel longer distances with less fuel. This not only saves money but also reduces the amount of fuel extracted from the ground, which has a positive environmental impact. Additionally, improved fuel efficiency can contribute to lower carbon emissions, addressing the global challenge of climate change.
In summary, fuel efficiency standards play a vital role in shaping the automotive industry and its environmental performance. These regulations drive innovation, forcing manufacturers to create more efficient vehicles. As a result, consumers benefit from reduced fuel consumption, lower costs, and a smaller environmental impact. The continuous evolution of these standards is essential to ensure that the automotive sector remains aligned with global sustainability goals and contributes to a greener future.
Understanding Your Car's Fuel Efficiency: A Comprehensive Guide
You may want to see also
Engine Design: The design of the engine directly affects fuel usage, with more efficient designs reducing consumption
The engine is the heart of a car, and its design plays a crucial role in determining fuel efficiency. Modern engines have evolved significantly over the years, with engineers constantly striving to optimize performance while minimizing fuel consumption. Engine design encompasses various components, including the cylinder layout, combustion chamber geometry, and the overall architecture of the powerplant.
One key aspect of engine design is the arrangement of cylinders. In-line engines, where cylinders are arranged in a straight line, are common in many vehicles. This layout offers excellent balance and compactness, allowing for efficient packaging within the car's body. However, V-shaped engines, with cylinders arranged in two banks forming a 'V' shape, are also prevalent. This design provides better weight distribution and can contribute to improved fuel efficiency due to its compact and lightweight nature.
The combustion chamber, where the fuel-air mixture is ignited, is another critical element. Designers aim to create chambers with optimal dimensions and shape to ensure complete combustion. This involves careful consideration of the chamber's volume, the placement of spark plugs, and the design of the intake and exhaust ports. Efficient combustion results in better fuel-to-energy conversion, leading to reduced fuel consumption.
Engineers also focus on minimizing friction and optimizing airflow to enhance efficiency. This includes designing low-friction engine components, such as piston rings and cylinder liners, to reduce internal friction. Additionally, advanced engine architectures, like the use of turbochargers or superchargers, can improve power output while maintaining fuel efficiency. These forced induction systems provide a boost of air and fuel, enabling the engine to produce more power without significantly increasing fuel usage.
Furthermore, the integration of electronic controls and sensors in modern engines allows for precise fuel management. Engine control units (ECUs) monitor various parameters and adjust fuel injection accordingly, ensuring optimal fuel-air mixture ratios. This level of control contributes to improved fuel efficiency and reduced emissions, as the engine operates closer to its ideal performance point.
In summary, engine design is a complex process that significantly impacts a car's fuel consumption. By optimizing cylinder layout, combustion chamber geometry, and incorporating advanced technologies, engineers can create engines that deliver excellent performance while minimizing fuel usage. These design considerations are vital in the pursuit of more efficient and environmentally friendly vehicles.
Monthly Car Fuel Costs: A Breakdown
You may want to see also
Vehicle Weight: Lighter vehicles require less fuel to accelerate and maintain speed, improving efficiency
The weight of a vehicle plays a significant role in its fuel efficiency and overall performance. Lighter cars inherently require less energy to accelerate and maintain a steady speed, which directly translates to reduced fuel consumption. This concept is based on the fundamental principle of physics, where the force required to move an object is directly proportional to its mass. In simpler terms, a lighter vehicle needs less power to overcome inertia and move forward, resulting in improved fuel economy.
When a car's weight is reduced, its engine doesn't have to work as hard to get the vehicle moving. This is especially noticeable during acceleration, where a lighter car can quickly gain speed with less fuel expenditure. As a result, drivers can experience better performance and responsiveness, especially in city driving conditions where frequent stops and starts are common. The reduced weight also contributes to better handling and a more agile driving experience, further enhancing the overall efficiency of the vehicle.
The impact of vehicle weight on fuel efficiency is particularly evident when comparing different car models. Heavier vehicles, often those with robust engines and ample interior space, tend to consume more fuel, especially during the initial stages of acceleration. This is because they have to overcome their own weight and the additional mass of passengers and cargo. In contrast, lighter cars, such as compact or subcompact models, can achieve better fuel economy due to their reduced weight, making them more economical for daily use.
Furthermore, the design and materials used in a vehicle's construction can significantly influence its weight. Modern automotive engineers are constantly exploring innovative ways to reduce vehicle weight without compromising safety and structural integrity. This includes the use of lightweight materials like aluminum, high-strength steel, and carbon fiber composites. By incorporating these materials, manufacturers can create lighter vehicles that still offer excellent performance and durability, ultimately leading to improved fuel efficiency.
In summary, vehicle weight is a critical factor in determining fuel efficiency. Lighter cars require less fuel to accelerate and maintain speed, resulting in improved overall efficiency. This not only benefits drivers with better performance and responsiveness but also contributes to reduced fuel consumption, making lighter vehicles more environmentally friendly and cost-effective in the long run. Understanding the relationship between weight and fuel efficiency can guide consumers in making informed decisions when choosing their next vehicle.
Understanding Fuel Requirements: Do New Cars Need Premium Gas?
You may want to see also
Aerodynamics: Smooth vehicle shapes reduce drag, leading to lower fuel consumption over longer distances
The concept of aerodynamics is a crucial factor in reducing fuel consumption and improving the overall efficiency of a vehicle. When a car is designed with a focus on aerodynamics, its shape and structure are optimized to minimize drag, which is the force that opposes the motion of the vehicle as it moves through the air. This is particularly important for cars, as they are often designed with a focus on speed and performance, which can lead to higher drag coefficients and increased fuel usage.
A well-designed aerodynamic vehicle has a sleek and streamlined body, often with a low-slung profile. This design reduces the frontal area exposed to the wind, which is a significant contributor to drag. By minimizing the frontal area, the car can cut through the air more efficiently, reducing the force that opposes its motion. This is achieved through careful consideration of the vehicle's shape, including the roof, windows, and even the shape of the headlights and taillights.
The impact of aerodynamics on fuel efficiency is substantial. When a car encounters air resistance, it must exert more power to overcome this drag, resulting in increased fuel consumption. By reducing drag, aerodynamic improvements can lead to a significant decrease in fuel usage. For example, a study by the US Department of Energy found that aerodynamic improvements can reduce fuel consumption by up to 10% for passenger cars and even more for larger vehicles like SUVs and trucks. This translates to substantial savings at the pump and a reduced environmental impact.
One effective way to enhance aerodynamics is through the use of smooth, curved surfaces. Traditional boxy car shapes create more drag due to the sharp edges and abrupt changes in direction of the airflow. In contrast, a more aerodynamic design features smooth, flowing lines that guide the air around the vehicle. This is often achieved through advanced manufacturing techniques, such as using computer-aided design (CAD) to create precise, optimized shapes.
Additionally, the placement and design of exterior components play a vital role in aerodynamics. For instance, the positioning of the front grille and the location of the windshield can significantly impact airflow. A well-designed grille can direct air efficiently, reducing drag, while a properly positioned windshield can minimize the impact of air pressure on the vehicle's front end. These small details, when combined with a sleek overall shape, contribute to a more aerodynamic vehicle, resulting in improved fuel efficiency and reduced environmental emissions.
Electric Car Charging: Fuel Usage and Efficiency
You may want to see also
Fuel Injection Systems: Advanced fuel injection technology optimizes fuel-air mixture, enhancing engine performance and fuel economy
Fuel injection systems have revolutionized the way engines operate, offering a more efficient and powerful method of fuel delivery compared to traditional carburetor systems. Advanced fuel injection technology plays a crucial role in optimizing the fuel-air mixture, which is essential for maximizing engine performance and improving fuel economy. This innovative system has become a cornerstone in modern automotive engineering, ensuring that vehicles run smoothly and efficiently.
At its core, the fuel injection system delivers precise amounts of fuel to the engine's cylinders, ensuring a balanced and efficient combustion process. Unlike older carburetor systems, which relied on a mechanical process to mix fuel and air, fuel injection uses electronic sensors and actuators to control the fuel flow. This electronic control unit (ECU) monitors various engine parameters, such as temperature, speed, and load, to calculate the exact amount of fuel required for optimal combustion. By doing so, it ensures that the fuel-air mixture is perfectly calibrated, leading to improved performance and reduced emissions.
The advanced technology behind fuel injection systems offers several advantages. Firstly, it allows for a more precise control of the fuel-air mixture, resulting in a more efficient combustion process. This precision means that the engine can extract more power from the fuel, leading to increased horsepower and torque. Additionally, the optimized mixture promotes better fuel economy, as the engine requires less fuel to achieve the same performance, thus reducing fuel consumption and costs for vehicle owners.
One of the key benefits of fuel injection is its ability to adapt to different driving conditions. The ECU can quickly adjust the fuel-air mixture based on real-time data, ensuring that the engine performs optimally in various scenarios. For instance, during high-speed cruising, the system can deliver a leaner mixture to improve fuel efficiency, while under heavy load or during acceleration, it can provide a richer mixture to meet the engine's increased power demands. This adaptability contributes to a smoother and more responsive driving experience.
Furthermore, fuel injection systems have contributed to significant advancements in engine technology. The use of electronic sensors and actuators allows for the implementation of advanced features like knock sensing, which detects and prevents engine knock, and cylinder deactivation, which optimizes fuel usage during low-load conditions. These technologies not only enhance engine performance but also contribute to better fuel economy and reduced environmental impact.
In summary, advanced fuel injection technology is a game-changer in the automotive industry, offering a sophisticated solution to optimize fuel-air mixtures. By providing precise control over fuel delivery, it enhances engine performance, improves fuel economy, and ensures a more responsive driving experience. As engine technology continues to evolve, fuel injection systems will undoubtedly play a pivotal role in shaping the future of efficient and powerful vehicles.
Haddad Toyota Fuel Tank: Sold Cars, Now a Legacy
You may want to see also
Frequently asked questions
The amount of fuel used in the manufacturing process of a car can vary significantly depending on several factors. On average, it is estimated that the production of a vehicle, including the assembly of various components, can consume around 1,000 to 2,000 liters (264 to 528 gallons) of fuel. However, this figure can be influenced by the type of vehicle, its size, engine capacity, and the specific manufacturing processes employed.
No, the fuel usage in car manufacturing is not limited to the production phase. The entire lifecycle of a vehicle, from raw material extraction to end-of-life disposal, contributes to fuel consumption. This includes the energy used for mining and refining materials, transportation of components, and the overall assembly process. Additionally, the energy required for the transportation of the finished vehicle to dealerships and the subsequent sale also plays a role.
Absolutely. Different components of a car have varying fuel requirements during manufacturing. For instance, the production of an engine typically demands more fuel compared to the manufacturing of the body or interior. The complexity and precision required in engine manufacturing, along with the use of specialized machinery, contribute to higher fuel consumption. Similarly, the production of advanced electronic systems and safety features may also increase the overall fuel usage.
The fuel consumption in the manufacturing of cars has environmental implications. The burning of fossil fuels releases greenhouse gases, contributing to climate change. Additionally, the extraction and processing of raw materials can lead to habitat destruction and pollution. It is essential to consider the environmental impact of the entire lifecycle of a vehicle, including the energy-intensive manufacturing process, to promote sustainable practices in the automotive industry.