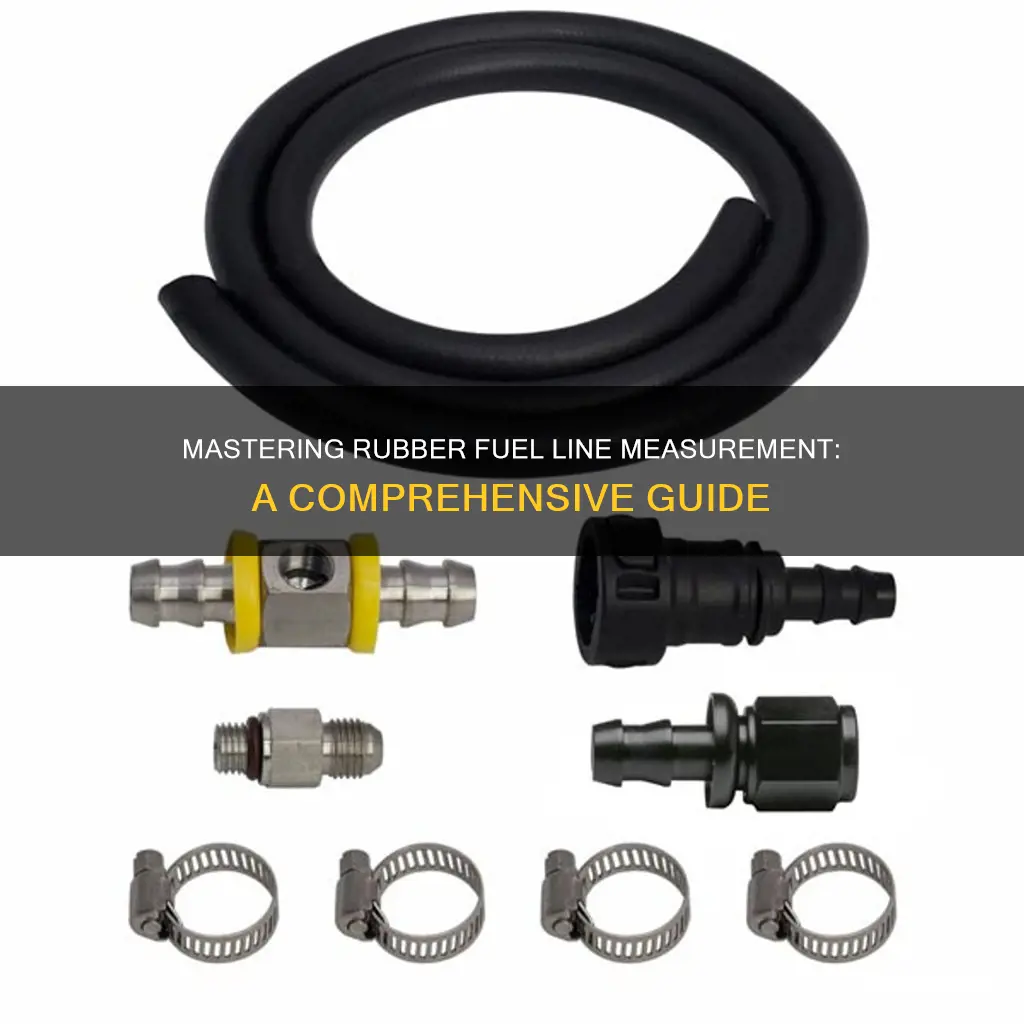
Measuring rubber fuel lines is a crucial process in the automotive industry, ensuring the correct fit and functionality of these components. Rubber fuel lines are essential for transferring fuel from the tank to the engine, and their precise measurement is vital for vehicle performance and safety. The measurement process involves assessing the length, diameter, and material properties of the fuel line to ensure it meets the required specifications. This involves using specialized tools and techniques, such as calipers, rulers, and material testing equipment, to accurately determine the dimensions and characteristics of the rubber fuel line. Understanding these measurements is key to selecting the appropriate fuel line for a vehicle, ensuring optimal fuel delivery and engine operation.
What You'll Learn
- Material Thickness: Rubber fuel line thickness is measured in inches or millimeters
- Inner Diameter: The inner diameter of the fuel line is crucial for flow rate
- Outer Diameter: The outer diameter determines the space it occupies in the engine bay
- Length: Fuel line length is measured in feet or meters for installation
- Flexibility: Rubber's flexibility is tested for durability and ease of installation
Material Thickness: Rubber fuel line thickness is measured in inches or millimeters
The thickness of rubber fuel lines is a critical aspect of their design and functionality, ensuring they can withstand the demands of fuel transportation in vehicles. This measurement is typically expressed in either inches or millimeters, depending on the regional standards and the manufacturer's preferences. Understanding the thickness measurement is essential for selecting the appropriate fuel line for a specific application.
In the imperial system, rubber fuel line thickness is commonly measured in inches. This measurement provides a clear indication of the line's wall thickness, which is crucial for its structural integrity. Thicker walls offer enhanced durability and resistance to fuel pressure, making them suitable for high-performance applications. For instance, a 3/16-inch thick rubber fuel line is a standard choice for most automotive uses, ensuring a balance between strength and flexibility.
On the other hand, the metric system utilizes millimeters as the unit of measurement for rubber fuel line thickness. This system is widely adopted in many countries and offers a precise way to specify the line's thickness. A 2.5 mm thick rubber fuel line, for example, indicates a robust construction capable of handling high-pressure fuel systems. Metric measurements provide a more detailed specification, allowing for a more tailored approach when selecting fuel lines for specialized applications.
When specifying rubber fuel lines, it is essential to consider both the overall diameter and the thickness. A larger diameter line with a thinner wall might not be as durable as a smaller diameter line with a thicker wall. Therefore, understanding the thickness measurement in either inches or millimeters is vital to ensure the fuel line meets the required performance standards.
In summary, the measurement of rubber fuel line thickness is a critical factor in its design and application. Whether expressed in inches or millimeters, this measurement directly influences the line's strength, flexibility, and ability to withstand fuel pressure. By considering these thickness specifications, engineers and enthusiasts can make informed decisions when selecting rubber fuel lines for various automotive and industrial purposes.
Catalyst Fuel Line Removal: A Step-by-Step Guide for 2006 Jeep Liberty Owners
You may want to see also
Inner Diameter: The inner diameter of the fuel line is crucial for flow rate
The inner diameter of a rubber fuel line is a critical factor in determining its performance and efficiency. This measurement is essential because it directly influences the flow rate of the fuel, which is a key consideration in engine operation. The flow rate refers to the volume of fuel that can pass through the line per unit of time, and it is directly proportional to the cross-sectional area of the fuel line.
When the inner diameter of the fuel line is increased, the cross-sectional area of the line also increases. This larger area allows for a greater volume of fuel to flow through the line, resulting in a higher flow rate. This is particularly important in high-performance engines or applications where precise fuel control is required. A larger inner diameter can ensure that the engine receives the necessary amount of fuel at the right time, optimizing power output and overall performance.
On the other hand, a smaller inner diameter will restrict the flow of fuel, leading to a reduced flow rate. This restriction can cause the engine to run lean, where there is an insufficient amount of fuel available for combustion, resulting in decreased power and potential performance issues. Therefore, it is crucial to select the appropriate inner diameter for the fuel line to match the engine's requirements.
Measuring the inner diameter accurately is essential to ensure the correct fuel line specifications are met. This measurement can be taken using a caliper, a precision measuring tool that can provide an accurate reading of the inner diameter. By inserting the caliper into the fuel line and measuring the distance between the inner walls, you can determine the inner diameter. This measurement should be taken at multiple points along the length of the fuel line to ensure consistency and account for any variations in the line's shape or thickness.
In summary, the inner diameter of a rubber fuel line plays a significant role in its ability to deliver fuel efficiently to an engine. A larger inner diameter allows for increased flow rate, ensuring optimal engine performance. Accurate measurement of the inner diameter is crucial to guarantee the correct specifications and functionality of the fuel line. By understanding the relationship between inner diameter and flow rate, engineers and enthusiasts can make informed decisions when selecting and installing fuel lines for various applications.
Fox Body Fuel Line Fixes: A Comprehensive Guide to Restoring Performance
You may want to see also
Outer Diameter: The outer diameter determines the space it occupies in the engine bay
The outer diameter of a rubber fuel line is a critical measurement that directly impacts its functionality and performance within an engine bay. This dimension is a key factor in determining the line's ability to fit within the available space and ensure proper installation. When measuring the outer diameter, it is essential to consider the following:
The engine bay of a vehicle is a confined space with limited dimensions. The outer diameter of the fuel line should be carefully assessed to ensure it can navigate through this area without causing any obstructions or interference. A line with an oversized diameter might not fit through certain passages, leading to installation challenges and potential damage to other components. Conversely, a line with a diameter that is too small may not provide sufficient space for the necessary connections and bends, compromising its functionality.
To measure the outer diameter, a precise tool such as a caliper or micrometer is required. These instruments allow for accurate measurements of the line's circumference at its widest point. It is crucial to measure multiple points along the length of the line to account for any variations in thickness or manufacturing tolerances. By taking these measurements, technicians can ensure that the fuel line's outer diameter meets the required specifications and can be installed securely.
In addition to the engine bay's dimensions, the outer diameter also influences the line's flexibility and bend radius. A larger diameter often corresponds to a more rigid line, which may require careful planning to avoid sharp bends that could lead to damage. On the other hand, a smaller diameter might offer better flexibility, allowing for easier routing around various engine components.
Understanding and accurately measuring the outer diameter of a rubber fuel line is essential for a successful installation. It ensures that the line fits seamlessly into the engine bay, operates efficiently, and maintains its integrity over time. By considering the available space and the line's dimensions, technicians can make informed decisions to optimize the fuel system's performance and reliability.
Mastering Fuel Line Replacement: A Guide to Poulan PP4218AVX Pro
You may want to see also
Length: Fuel line length is measured in feet or meters for installation
The length of a rubber fuel line is a critical factor in its installation and performance. When measuring the length, it is essential to ensure that the fuel line is long enough to reach the desired destination without being overly long, which could lead to unnecessary material waste and potential installation challenges. The measurement is typically done in feet or meters, providing a clear and standardized way to specify the required length.
During the installation process, the fuel line must be carefully routed to avoid any sharp bends or kinks, as these can compromise the integrity of the material. The length measurement ensures that the fuel line can be laid out efficiently, allowing for smooth and continuous flow of fuel from the source to the engine. This is particularly important in automotive applications, where the fuel line connects the fuel tank to the engine's fuel injection system.
Accurate length measurement is achieved through various methods. One common approach is to use a flexible measuring tape or a ruler, ensuring that the measurement is taken along the actual path the fuel line will take. This might involve temporarily marking or taping the route to ensure an accurate assessment. For longer fuel lines, especially in industrial or marine settings, specialized measuring tools or techniques may be employed to handle the extended length without compromising precision.
In some cases, the fuel line's length is determined by the specific requirements of the vehicle or equipment it will be installed in. This involves considering factors such as the distance between the fuel tank and the engine, any existing plumbing or wiring, and the need for additional length to allow for flexibility and movement during operation. Understanding these specific needs ensures that the fuel line is not only the correct length but also compatible with the overall design and functionality of the system.
Once the length is determined, it is essential to double-check the measurement to avoid any installation errors. This might involve comparing the measured length to the specifications provided by the manufacturer or consulting with experts in the field to ensure compliance with industry standards. Proper measurement and installation of the fuel line contribute to efficient fuel delivery, optimal engine performance, and overall system reliability.
Mastering Fuel Line Maintenance: The Ultimate Guide to Spring Lock Coupling Tools
You may want to see also
Flexibility: Rubber's flexibility is tested for durability and ease of installation
The flexibility of rubber fuel lines is a critical aspect of their performance and longevity. Rubber is a natural material that can be manipulated to varying degrees, and its flexibility is essential for its ability to withstand the rigors of the automotive environment. When it comes to fuel lines, flexibility is not just about bending without breaking; it's about ensuring the material can endure the constant expansion and contraction caused by temperature changes, engine vibrations, and the pressure of fuel flow.
To test the flexibility of rubber fuel lines, manufacturers employ various methods. One common approach is to subject the material to repeated bending and straightening cycles. This process, often referred to as a flex test, involves placing the fuel line through a series of bends and straightens at different angles and radii. The goal is to simulate the real-world conditions the fuel line will experience during the vehicle's operation. By doing so, engineers can assess the material's ability to recover its original shape after deformation, ensuring it remains intact and functional over time.
Another critical aspect of flexibility testing is evaluating the material's resistance to fatigue. This involves exposing the rubber fuel line to cyclic loading, where it is repeatedly bent and straightened under controlled conditions. The test measures the material's endurance and determines how many cycles it can withstand before showing signs of failure, such as cracking or permanent deformation. This fatigue testing is crucial because it helps predict the fuel line's long-term performance and ensures it can handle the repetitive stresses it will encounter during the vehicle's lifetime.
In addition to these physical tests, manufacturers also consider the ease of installation. A flexible rubber fuel line should be easy to route through the engine bay without kinking or becoming damaged during installation. This aspect is particularly important in tight spaces where the fuel line must navigate around various components. The flexibility of the material allows it to conform to the available space, ensuring a secure and reliable connection without the risk of damage.
The flexibility of rubber fuel lines is a result of the material's inherent properties and the manufacturing process. Rubber's natural elasticity, combined with additives and processing techniques, allows it to be manipulated into various forms while maintaining its structural integrity. This flexibility is further enhanced by the use of reinforcing materials, such as fibers, which provide additional strength and durability without compromising the material's pliability. By understanding and testing these properties, engineers can design fuel lines that are not only flexible but also highly reliable, ensuring optimal performance and longevity in automotive applications.
Unclipping the Ford Pink Fuel Line: A Step-by-Step Guide
You may want to see also
Frequently asked questions
The length of a rubber fuel line is typically measured in inches or centimeters. It is important to measure the line's length carefully, especially if it needs to be replaced or modified to fit a specific application. Measure the line's total length from one end to the other, ensuring you include any bends or loops.
Measuring rubber fuel lines can be done using basic tools. A flexible measuring tape or ruler is commonly used to get an accurate length measurement. For more precise measurements, a caliper can be employed to measure the thickness and diameter of the line, which is crucial for selecting the right replacement size.
Accurate measurements are vital when working with rubber fuel lines to ensure a proper fit and functionality. If the line is too short, it may not reach the intended destination, while an overly long line can lead to unnecessary material waste and potential performance issues. Precise measurements also help in avoiding leaks or damage during installation.
Yes, measuring a rubber fuel line while it's installed is possible, but it may require some disassembly. You can carefully remove any connected components to access the line and measure it. Alternatively, you can measure the line's length before installation to ensure it fits the vehicle's specifications.
If the rubber fuel line is damaged, it is best to replace it with a new one of the appropriate size and material. Measure the old line to determine the required length and diameter. When purchasing a replacement, ensure it meets the specifications for your vehicle's fuel system to maintain optimal performance and safety.