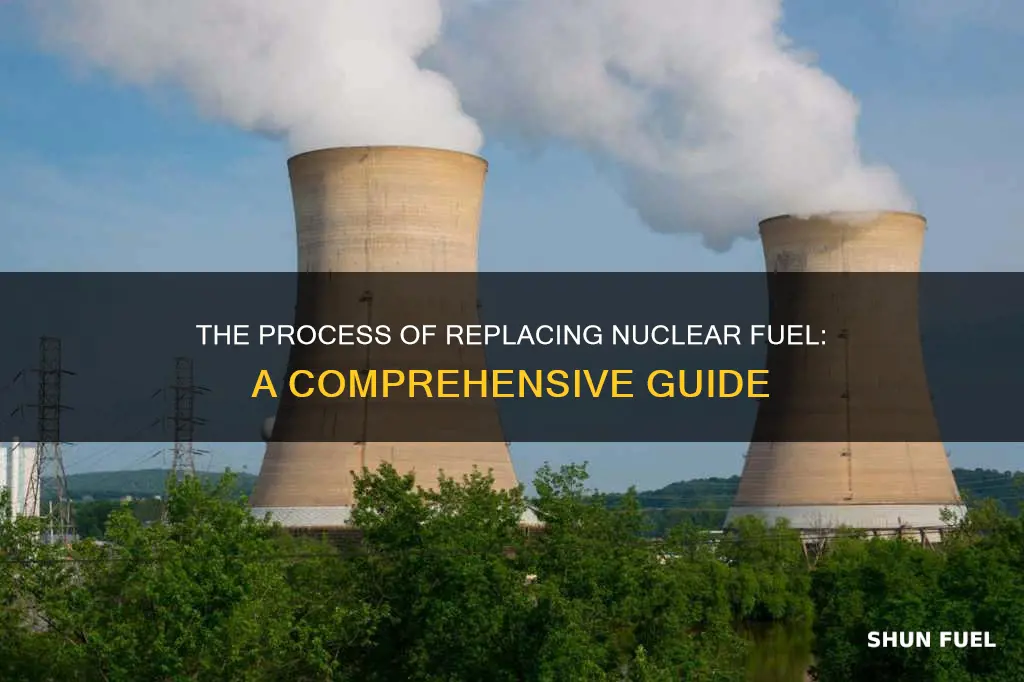
The process of replacing nuclear fuel in reactors is a critical aspect of nuclear power generation. It involves carefully removing the used fuel, which has undergone a series of chemical and physical changes during operation, and replacing it with fresh fuel. This replacement is necessary to sustain the nuclear reaction and maintain the reactor's power output. The procedure requires specialized equipment and trained personnel to handle the radioactive materials safely. Understanding the methods and challenges of fuel replacement is essential for ensuring the efficient and safe operation of nuclear power plants.
What You'll Learn
- Fuel Assembly: Replacing fuel rods in a controlled manner during operation
- Refueling Window: Optimizing reactor downtime for efficient fuel exchange
- Automation: Using robotic systems to handle and replace fuel elements
- Safety Protocols: Strict procedures to ensure safe fuel replacement
- Waste Management: Proper disposal of used fuel and spent fuel handling
Fuel Assembly: Replacing fuel rods in a controlled manner during operation
The process of replacing nuclear fuel rods in a controlled manner is a critical aspect of maintaining the safe and efficient operation of a nuclear power plant. This procedure is carefully planned and executed to ensure the safety of the plant's personnel and the environment, as well as to optimize the plant's performance. Here's an overview of the steps involved:
Fuel Assembly and Design: Before the replacement process begins, the fuel assembly design is crucial. Each fuel assembly is a carefully engineered structure that houses the fuel rods. These assemblies are designed to allow for the controlled removal and insertion of fuel rods while maintaining the structural integrity of the assembly. The design includes features like guide tubes and support plates to ensure proper alignment and stability during the replacement process.
Pre-Replacement Preparation: Prior to the replacement, a comprehensive set of preparations is undertaken. This includes a detailed inspection of the fuel assembly to identify any defects or issues with the existing fuel rods. Specialized tools and equipment are prepared, such as fuel rod handling tools and replacement fuel rods, ensuring they meet the required specifications. The plant's control room is also set up to monitor the process and adjust parameters as needed.
Controlled Removal of Fuel Rods: The replacement process starts with the careful removal of fuel rods. This is typically done in a controlled manner to prevent any release of radioactive material. Specialized tools are used to grip and remove the fuel rods, ensuring they are handled with precision. The removed fuel rods are then placed in a designated storage area, where they are cooled and monitored to ensure the safety of the handling process.
Insertion of New Fuel Rods: Once the old fuel rods are removed, the new ones are carefully inserted into the fuel assembly. This step requires precision and control to ensure proper alignment and seating of the new fuel rods. Specialized equipment, such as fuel rod positioning devices, is used to guide the rods into their correct positions. The new fuel rods are then secured, and the assembly is prepared for further processing.
Post-Replacement Procedures: After the fuel rods are replaced, a series of checks and tests are conducted. This includes verifying the proper functioning of the fuel assembly, monitoring radiation levels, and ensuring that all safety protocols have been adhered to. The replaced fuel rods are also analyzed to assess their performance and determine if any further adjustments are required. This comprehensive approach ensures that the fuel assembly is ready for continued operation while maintaining the highest safety standards.
The replacement of fuel rods in a controlled manner is a complex but essential process in nuclear power generation. It requires meticulous planning, specialized equipment, and highly trained personnel to ensure the safety and efficiency of the plant's operation. This procedure contributes to the overall reliability and longevity of nuclear power systems.
Chevy Van Fuel Filter Replacement: A Step-by-Step Guide
You may want to see also
Refueling Window: Optimizing reactor downtime for efficient fuel exchange
The process of refueling a nuclear reactor is a carefully planned and executed procedure, and the timing of this operation is critical to the overall efficiency and safety of the plant. The 'refueling window' refers to the specific period during which the reactor is shut down for the purpose of replacing spent fuel and inserting new fuel assemblies. This downtime is a unique opportunity to optimize the fuel exchange process, ensuring that the reactor can operate at peak performance once again.
During the refueling window, the reactor core is completely inaccessible to the primary system, allowing for the safe removal and insertion of fuel components. This period is typically planned well in advance, considering the reactor's operational schedule and the availability of skilled personnel. The goal is to minimize the duration of the shutdown, as prolonged outages can impact the plant's overall availability and efficiency.
Efficient fuel exchange begins with a comprehensive assessment of the reactor's current fuel inventory. This includes analyzing the burn-up levels of the existing fuel, determining the amount of fuel remaining, and identifying any fuel that has reached the end of its operational life. Advanced instrumentation and control systems play a vital role here, providing real-time data on fuel performance and enabling precise calculations.
Once the assessment is complete, the refueling process can commence. Skilled operators carefully remove the spent fuel assemblies, ensuring they are handled and transported safely to storage or reprocessing facilities. Simultaneously, new fuel assemblies are prepared and positioned within the core, following a precise sequence to maintain the reactor's stability and power distribution. This delicate dance of fuel exchange requires meticulous planning and execution to avoid any potential safety hazards.
The timing of the refueling window is crucial. It should be scheduled when the reactor is not in operation, allowing for a controlled environment during the fuel exchange. Additionally, the window should be long enough to accommodate the complex procedures without rushing, ensuring that all fuel is successfully replaced and the reactor is prepared for its next operational cycle. Optimizing this downtime is essential to maintaining the reactor's performance and overall reliability.
Replacing the Fuel Pump in Your Scion IQ: A Step-by-Step Guide
You may want to see also
Automation: Using robotic systems to handle and replace fuel elements
The process of replacing nuclear fuel in a reactor is a critical and delicate operation, and automation plays a crucial role in ensuring safety and efficiency. One of the key aspects of automating this task is the use of robotic systems designed to handle and replace fuel elements with precision and minimal human intervention. These robotic systems are engineered to navigate the challenging environment inside the reactor, where extreme conditions such as high radiation and intense heat exist.
Robotic arms, equipped with specialized grippers and tools, are at the heart of this automation process. These arms are designed to reach into the reactor vessel, locate the spent fuel elements, and carefully extract them. The precision required is immense, as the fuel elements are typically the size of a small car and must be handled without damage. Robotic systems use advanced sensors and computer vision to identify the correct fuel elements and ensure a secure grip. Once grasped, the robotic arm carefully transports the spent fuel to a storage area or a dedicated cooling pool for temporary storage.
The replacement process begins with the insertion of new fuel elements. Robotic systems are programmed to follow a precise sequence of movements, ensuring that the new fuel elements are positioned correctly within the reactor core. This involves precise alignment and secure fastening of the fuel elements to the core structure. Automation ensures that the process is consistent and reduces the risk of human error, which could potentially lead to fuel damage or incorrect placement.
Furthermore, robotic systems can be integrated with advanced imaging and monitoring technologies. These systems can provide real-time feedback on the status of the fuel elements, allowing operators to make informed decisions. For instance, robotic arms can be equipped with cameras to inspect the fuel elements for any signs of damage or degradation, ensuring that only healthy fuel is used. This level of automation and inspection contributes to the overall safety and reliability of the nuclear power plant.
In summary, automation, particularly the use of robotic systems, is a vital component in the replacement of nuclear fuel. These systems enable precise handling, transportation, and insertion of fuel elements, all while operating in a highly controlled and safe manner. By minimizing human intervention, automation reduces the potential for errors and enhances the overall efficiency of the fuel replacement process, ultimately contributing to the smooth operation of nuclear power plants.
Replacing the Fuel Level Sensor in a 5th Gen 4Runner
You may want to see also
Safety Protocols: Strict procedures to ensure safe fuel replacement
The process of replacing nuclear fuel in a reactor is a complex and highly regulated procedure, primarily due to the inherent risks associated with handling radioactive materials. Safety protocols are designed to minimize the potential for human error and ensure the well-being of both the personnel involved and the environment. Here are some of the critical safety measures implemented during fuel replacement:
Training and Qualification: All personnel involved in the fuel replacement process undergo rigorous training. This includes understanding the reactor's design, the specific fuel assembly layout, and the procedures for handling and replacing fuel. Technicians and engineers must be qualified to perform their tasks, ensuring they can identify potential hazards and implement safety protocols effectively. Regular refresher courses and simulations are conducted to keep their skills sharp and up-to-date.
Remote Handling Systems: To minimize direct exposure to radiation, remote handling systems are employed. These systems allow operators to manipulate the fuel assemblies from a distance, using specialized tools and robotic arms. This setup ensures that workers are not in close proximity to the highly radioactive fuel, reducing the risk of radiation exposure and potential health issues.
Containment and Shielding: The reactor and its surroundings are designed with robust containment systems to prevent the release of radioactive materials. During fuel replacement, the reactor is typically shut down, and the core is shielded to maintain a safe environment. This includes using heavy materials like lead and concrete to block radiation and ensure the safety of the personnel and the surrounding area.
Strict Access Control: Access to the reactor site is highly controlled and restricted. Only authorized personnel are granted entry, and they must adhere to specific protocols. This includes wearing appropriate personal protective equipment (PPE) and following decontamination procedures to prevent the spread of contamination outside the facility.
Emergency Response Planning: Comprehensive emergency response plans are in place to address potential accidents or incidents during fuel replacement. These plans outline the steps to be taken in various scenarios, including radiation leaks, equipment failures, or fires. Regular drills and simulations are conducted to ensure that the response teams are prepared and can react swiftly and effectively.
Quality Assurance and Inspection: Every step of the fuel replacement process is meticulously monitored and inspected. Quality assurance protocols are in place to verify the integrity of the fuel, the accuracy of the replacement, and the overall safety of the procedure. This includes visual inspections, radiation surveys, and comprehensive documentation to ensure compliance with safety standards.
These strict safety protocols are essential to maintaining the integrity of the nuclear fuel replacement process, ensuring the protection of workers, the environment, and the public. The procedures are designed to be robust and adaptable, allowing for the swift identification and mitigation of any potential risks.
Renewable Revolution: Wind and Solar's Future as Fossil Fuel Alternatives
You may want to see also
Waste Management: Proper disposal of used fuel and spent fuel handling
The proper management and disposal of used nuclear fuel and spent fuel is a critical aspect of nuclear power plant operations, ensuring the safety of the environment and public health. When nuclear fuel is used in reactors, it undergoes a series of chemical and physical changes, leading to the generation of various radioactive byproducts. These byproducts remain radioactive and can pose significant risks if not handled and disposed of correctly.
Used fuel, also known as spent fuel, is highly radioactive and contains a variety of fission products, including heavy metals and volatile elements. The handling and disposal process involves several stages. Firstly, the spent fuel is removed from the reactor core and placed in a water-filled pool, known as a spent fuel pool, for cooling and temporary storage. This pool provides a safe environment to allow the fuel to decay and reduce its radioactivity over time. During this period, the fuel continues to emit heat, and the water serves as a heat sink, preventing overheating and potential damage to the fuel pellets and cladding.
After a certain period, typically several years, the spent fuel is transferred from the pool to a dry storage facility. This can be done in various ways, including using specialized containers or casks designed to safely transport and store the fuel. Dry storage systems provide a secure and long-term solution, allowing for the continued decay of the fuel and the reduction of its radioactivity. These facilities are designed to withstand natural disasters and external threats, ensuring the safety of the surrounding environment and population.
The next step in waste management is the eventual disposal of the spent fuel. This is a complex process and a subject of ongoing research and debate. One proposed method is geological disposal, where the spent fuel is placed in a deep geological repository. These repositories are designed to isolate the fuel from the environment, utilizing natural barriers such as rock layers and groundwater to prevent any potential release of radioactive materials. The site selection and design of these repositories require rigorous scientific and engineering analysis to ensure long-term stability and safety.
Another approach is to reprocess the spent fuel, extracting valuable materials and reducing the volume of high-level waste. Reprocessing allows for the recovery of plutonium and minor actinides, which can be recycled back into new fuel, reducing the overall waste volume. However, reprocessing also presents technical and safety challenges, and it is not a widely adopted practice due to concerns over proliferation and technical complexity.
In summary, the proper disposal of used nuclear fuel and spent fuel handling is a comprehensive process that involves cooling, storage, and eventual disposal or reprocessing. Each step requires careful planning, advanced technologies, and a deep understanding of nuclear physics and chemistry to ensure the safety and environmental protection. Effective waste management is crucial for the sustainable development of nuclear power and the responsible utilization of nuclear energy.
Replacing the Fuel Pump in Your 2002 Mercedes S430: Step-by-Step Guide
You may want to see also
Frequently asked questions
The replacement of nuclear fuel in a reactor is a critical process that occurs regularly during the operation of a nuclear power plant. The frequency of fuel replacement depends on various factors, including the type of reactor, the fuel design, and the specific operating conditions. Typically, fuel assemblies are replaced every 12 to 18 months.
Replacing nuclear fuel involves a series of steps. First, the spent fuel, which has reached the end of its useful life, is removed from the reactor core. This is done carefully to ensure the safety of the plant and its personnel. The spent fuel is then transported to a spent fuel pool, where it is cooled and stored temporarily. During this time, the fuel continues to release heat, and the pool provides a safe environment for this decay heat to dissipate. Once the fuel has cooled sufficiently, it can be prepared for long-term storage or disposal.
The replacement of nuclear fuel is typically carried out by trained personnel, often referred to as fuel handlers or maintenance technicians. These individuals are highly skilled and undergo rigorous training to ensure they can perform the task safely and efficiently. Safety measures are in place throughout the process, including radiation monitoring, personal protective equipment, and strict protocols to minimize exposure to radiation. The plant's control room continuously monitors the reactor's parameters, and emergency procedures are in effect to handle any potential issues during fuel replacement.
While fuel replacement is a well-established procedure, it does come with certain challenges and risks. One of the primary concerns is the handling of highly radioactive materials, which requires specialized equipment and trained personnel. Additionally, the process must be carefully timed to avoid disrupting the reactor's operation and to ensure the plant's stability. There is also a risk of human error, which is mitigated through comprehensive training, multiple-check systems, and strict adherence to operating procedures. Regular maintenance and testing of equipment further contribute to the safety of the fuel replacement process.