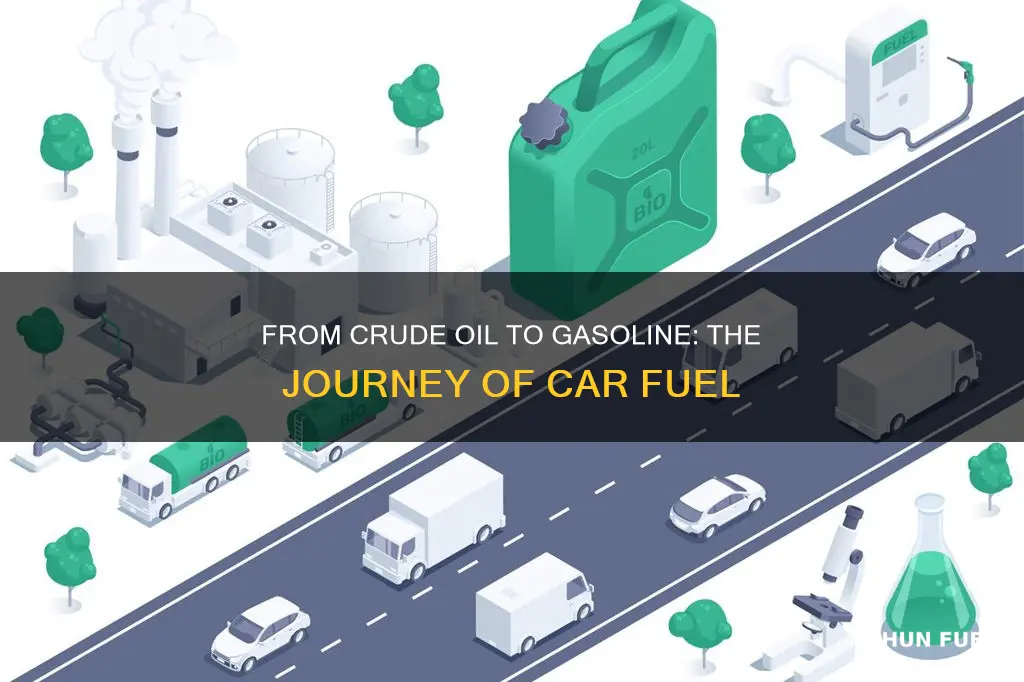
The process of creating car fuel, also known as gasoline or diesel, involves a complex series of steps that transform crude oil into a usable energy source. It begins with the extraction of crude oil from the earth, which is then transported to refineries. At the refinery, the crude oil undergoes a process called fractional distillation, where it is heated and separated into various components based on their boiling points. These components are then further processed through a series of chemical reactions and refining techniques to produce the final fuel products, including gasoline and diesel. This intricate process involves multiple stages of purification, blending, and treatment to ensure the fuel meets the required standards for combustion and performance in vehicles.
What You'll Learn
- Crude Oil Extraction: Drilling and pumping crude oil from underground reservoirs
- Refining Process: Crude oil is transformed into usable fuel through distillation and chemical processes
- Catalysts and Additives: Essential compounds added to enhance fuel performance and reduce emissions
- Fuel Distribution: Transportation and storage of refined fuel to gas stations
- Emissions Control: Strict regulations and technologies to minimize harmful emissions from vehicle exhaust
Crude Oil Extraction: Drilling and pumping crude oil from underground reservoirs
The process of extracting crude oil from the earth begins with drilling, a complex and precise operation. Drilling rigs, often massive structures, are used to create a wellbore, a narrow hole extending deep into the Earth's crust. This borehole serves as the pathway to access the oil-bearing formations. The choice of drilling method depends on various factors, including the type of reservoir, its depth, and the geological characteristics of the area. Vertical drilling is common for shallow reservoirs, while horizontal drilling is employed for deeper and more complex structures to maximize oil recovery.
Once the wellbore is drilled, it must be completed to ensure the safe and efficient extraction of crude oil. This involves several steps. First, the borehole is lined with a steel casing to provide structural integrity and prevent collapse. This casing is carefully positioned to follow the path of the wellbore. Next, a cementing process is carried out to fill the space between the casing and the borehole wall, creating a solid and impermeable barrier. This step is crucial to prevent the contamination of groundwater and ensure the safety of the drilling operation.
After the well has been completed, the drilling rig moves to the pumping stage. Here, a large pump, often located on the surface, is used to inject a high-pressure fluid, typically a mixture of water and chemicals, down the wellbore. This fluid, known as a 'flush,' serves multiple purposes. It helps to break up the rock formations, a process called 'frac-watering,' which creates small cracks and pores in the rock, providing a pathway for the oil to flow. The flush also carries away any oil and gas that has been released during the process, allowing it to be captured and collected.
The high-pressure fluid is then released, and the pressure created forces the crude oil to flow back up the wellbore. This natural flow is carefully monitored, and the rate of oil production is controlled by adjusting the pressure and flow rate of the flush. As the oil rises, it is separated from the water and other impurities through a process called 'oil production.' This separation is crucial to ensure that only pure crude oil is collected, which is then stored in large tanks or sent directly to the refining process.
Drilling and pumping operations are carefully managed to minimize environmental impact and ensure the safety of the surrounding areas. Modern drilling rigs are equipped with advanced technology to monitor pressure, temperature, and flow rates, allowing operators to make real-time adjustments and optimize the extraction process. Additionally, stringent safety protocols are in place to prevent oil spills and protect ecosystems during the entire crude oil extraction process.
Low Fuel: The Surprising Reason Your Car Won't Start
You may want to see also
Refining Process: Crude oil is transformed into usable fuel through distillation and chemical processes
The process of transforming crude oil into the fuel that powers our vehicles is a complex and fascinating journey through the world of refining. This intricate process begins with the extraction of crude oil from the earth, a raw material that holds the potential to power our modern lives. Once extracted, crude oil is a dark, viscous liquid that requires extensive processing to become a usable fuel source.
The initial step in refining crude oil is distillation, a process that takes advantage of the different boiling points of various hydrocarbons present in the oil. In a distillation column, the crude oil is heated, and as it vaporizes, the different components separate based on their unique boiling points. Lighter hydrocarbons, such as gasoline, have lower boiling points and vaporize at lower temperatures, while heavier hydrocarbons, like diesel and kerosene, have higher boiling points and require more heat to vaporize. This separation is crucial as it allows for the production of various fuel products.
After distillation, the refined products are further processed through chemical processes to enhance their quality and performance. One common process is catalytic cracking, where heavy hydrocarbons are broken down into lighter, more valuable fractions. This is achieved by exposing the hydrocarbons to a catalyst, typically a zeolite mineral, which provides an alternative reaction pathway for breaking down large molecules. The catalyst speeds up the cracking process, allowing for the production of high-octane gasoline and other valuable petroleum products.
Another essential chemical process is hydrotreating, which is used to remove impurities and improve the quality of the fuel. This process involves treating the refined products with hydrogen gas in the presence of a catalyst. The hydrogen helps to break down sulfur compounds and other impurities, reducing the fuel's sulfur content. Lower sulfur levels are crucial as they help minimize the emission of harmful pollutants when the fuel is burned in vehicle engines.
The refining process also includes various other treatments and upgrades to ensure the final fuel products meet the required standards. These processes may include desulfurization, which further reduces sulfur levels, and the addition of octane boosters to enhance engine performance. Through these intricate chemical and physical processes, crude oil is transformed into a diverse range of fuels, each tailored to specific applications, ensuring that our vehicles can run efficiently and with reduced environmental impact.
E15 Fuel: Is It Safe for Your Car?
You may want to see also
Catalysts and Additives: Essential compounds added to enhance fuel performance and reduce emissions
Catalysts and additives play a crucial role in modern fuel production, ensuring that the combustion process is efficient, environmentally friendly, and meets the stringent standards set by regulatory bodies. These compounds are carefully selected and incorporated into the fuel formulation to optimize performance and minimize the release of harmful pollutants.
One of the primary functions of catalysts in fuel is to facilitate the combustion process. Catalysts are substances that accelerate chemical reactions without being consumed in the process. In the context of fuel, catalysts are designed to lower the activation energy required for the combustion of hydrocarbons present in the fuel. This results in a more complete and rapid burning of the fuel, leading to improved engine performance and reduced emissions. For instance, platinum and palladium catalysts are commonly used in catalytic converters to convert harmful exhaust gases like carbon monoxide (CO) and nitrogen oxides (NOx) into less harmful substances such as carbon dioxide (CO2) and nitrogen gas (N2).
Additives, on the other hand, are compounds added to the fuel in small quantities to modify its properties and performance. These can include detergents, antioxidants, and lubricants. Detergents, for example, are added to gasoline to clean the fuel injectors and intake valves, ensuring that the engine operates efficiently. They help to prevent the formation of deposits and keep the engine components clean, thus improving overall performance and longevity. Antioxidants are added to both gasoline and diesel to prevent the oxidation of the fuel, which can lead to the formation of gum and varnish in the fuel system. This ensures that the fuel remains stable and performs optimally over a wide range of temperatures and storage conditions.
In diesel fuel, lubricity additives are crucial. These compounds reduce internal friction within the fuel, ensuring smoother operation of the engine's injection system. This results in improved power output and reduced wear on engine components. Additionally, lubricity additives help to prevent the coking of fuel injectors, which can lead to increased fuel consumption and reduced engine performance.
The use of catalysts and additives is a critical aspect of modern fuel production, allowing for the development of cleaner, more efficient, and environmentally conscious fuels. These compounds work in harmony to optimize the combustion process, reduce emissions, and ensure that the fuel meets the highest performance standards. As technology advances, the development of new catalysts and additives will continue to play a pivotal role in shaping the future of the automotive industry and its environmental impact.
Navigating the Road: When Your Fuel Gauge Acts Up
You may want to see also
Fuel Distribution: Transportation and storage of refined fuel to gas stations
The process of fuel distribution involves a complex network of transportation and storage systems to ensure that the refined fuel reaches gas stations efficiently and safely. Once the crude oil has been processed and refined into various fuel products, such as gasoline, diesel, and jet fuel, the real challenge begins: getting these products to the end consumer.
Transportation of refined fuel is primarily done via specialized trucks and pipelines. Large-scale pipeline networks are an efficient and cost-effective method for moving fuel over long distances. These pipelines are designed to handle high-pressure fuel and are often buried underground, ensuring a secure and continuous supply. Pipeline transportation is especially useful for moving large volumes of fuel, such as when supplying a region with multiple gas stations. Trucks, on the other hand, are versatile and can navigate roads that pipelines cannot, making them ideal for reaching remote areas or providing localized fuel supply. Specialized fuel tankers and tank trucks are designed to carry fuel safely and efficiently, often with advanced safety features to prevent leaks and spills.
The transportation process requires careful planning and coordination. Fuel distributors must consider factors such as the distance between refineries and gas stations, traffic conditions, and the capacity of the transportation vehicles. Optimizing routes and scheduling deliveries to minimize travel time and fuel consumption is crucial. Additionally, temperature control is essential during transportation, especially for sensitive fuels like gasoline, which can degrade at higher temperatures. Specialized cooling systems and insulated tanks are used to maintain the fuel's quality and stability.
Storage of refined fuel is another critical aspect of the distribution process. Fuel terminals or storage facilities are strategically located to serve as intermediate hubs for fuel distribution. These terminals have large storage tanks that can hold millions of gallons of fuel, providing a buffer between production and consumption. The storage facilities are designed with safety in mind, incorporating measures to prevent fires, explosions, and environmental contamination. Advanced monitoring systems are used to track fuel levels, temperature, and pressure, ensuring that the fuel remains stable and safe.
The storage and transportation processes are highly regulated to meet environmental and safety standards. Fuel distributors must adhere to strict guidelines and regulations set by government agencies to ensure the safe handling and distribution of fuel. This includes proper labeling, documentation, and emergency response planning. By following these protocols, the fuel distribution industry aims to minimize risks and ensure a reliable supply of energy to power our vehicles and aircraft.
Diesel Fuel's Impact on Car Finish: A Deep Dive
You may want to see also
Emissions Control: Strict regulations and technologies to minimize harmful emissions from vehicle exhaust
Emissions control is a critical aspect of modern vehicle design, aiming to minimize the release of harmful substances into the atmosphere. Over the years, strict regulations and innovative technologies have been implemented to combat the environmental impact of vehicle exhaust. These measures are essential to address the growing concerns regarding air pollution and its detrimental effects on human health and the environment.
One of the primary focuses of emissions control is to reduce the release of pollutants such as carbon monoxide (CO), nitrogen oxides (NOx), and particulate matter (PM). These substances are known to contribute significantly to air pollution and have adverse effects on both the environment and human well-being. To combat this, vehicle manufacturers have adopted various strategies.
Strict regulations play a pivotal role in emissions control. Governments worldwide have set emission standards that vehicles must adhere to. These standards define the maximum allowable levels of pollutants that can be emitted from a vehicle's exhaust system. For instance, the United States Environmental Protection Agency (EPA) has implemented the Corporate Average Fuel Economy (CAFE) standards, which include emissions limits for vehicles. Similarly, the European Union's Euro emissions standards categorize vehicles based on their pollutant emissions, ensuring that only low-emission vehicles are sold in the market. These regulations provide a framework for manufacturers to design and produce vehicles that meet specific environmental criteria.
To achieve these stringent emission standards, vehicle manufacturers employ a range of technologies. One of the most common technologies is the catalytic converter, which is designed to reduce harmful emissions. This device converts toxic gases, such as carbon monoxide and nitrogen oxides, into less harmful substances like carbon dioxide and nitrogen gas. Catalytic converters use a catalyst, typically made of platinum, palladium, or rhodium, to facilitate these chemical reactions. Modern vehicles are also equipped with advanced engine control units (ECUs) that optimize fuel injection and combustion processes, ensuring that engines operate efficiently and produce fewer emissions.
Additionally, advancements in exhaust systems have contributed significantly to emissions control. Modern exhaust systems are designed to capture and filter particulate matter, preventing it from being released into the atmosphere. These systems use filters or particulate matter traps to collect and remove solid particles, such as soot and ash, from the exhaust stream. Furthermore, the development of selective catalytic reduction (SCR) systems has been instrumental in reducing nitrogen oxide emissions. SCR systems inject a solution of urea (a liquid or solid compound) into the exhaust stream, where it reacts with nitrogen oxides to form harmless nitrogen and water vapor.
In summary, emissions control is a multifaceted approach that combines strict regulations and advanced technologies. By implementing these measures, vehicle manufacturers aim to minimize the environmental impact of vehicles and promote cleaner air. The continuous development and refinement of emissions control technologies are essential to meeting the ever-tightening emission standards and ensuring a more sustainable future for transportation.
Exploring Alcohol as an Alternative Car Fuel: Feasibility and Implications
You may want to see also
Frequently asked questions
The process of creating car fuel, typically gasoline or diesel, involves several steps. It starts with the refining of crude oil, which is extracted from the earth. Crude oil is a complex mixture of various hydrocarbons and other organic compounds. Through a process called fractional distillation, the oil is heated and separated into different components based on their boiling points. These components are then further processed to create the final fuel products.
Gasoline production involves a process called catalytic cracking. In this process, the heavy hydrocarbons from crude oil are heated to high temperatures in the presence of a catalyst, typically zeolites or metal oxides. This cracking process breaks down large hydrocarbon molecules into smaller ones, producing a range of lighter, more volatile hydrocarbons that form the basis of gasoline. Additional refining steps, such as reforming and blending, are used to adjust the fuel's properties and meet quality standards.
A refinery is a crucial facility in the fuel-making process. It is responsible for taking the crude oil and transforming it into various petroleum products, including gasoline, diesel, jet fuel, and other petrochemicals. Refineries use a combination of physical separation processes, such as distillation and solvent extraction, to separate the different components of crude oil. These components are then further processed through chemical reactions and purification techniques to produce the desired fuel products.
Yes, there are alternative fuels for cars, such as diesel, liquefied petroleum gas (LPG), and biofuels. Diesel is produced through a similar refining process as gasoline, but it involves different distillation cuts and cracking processes. LPG, or propane, is a byproduct of natural gas processing and is separated during the refining of crude oil. Biofuels, on the other hand, are made from renewable biomass sources like plant oils, animal fats, or even waste materials. These feedstocks are processed through various methods, including transesterification, to produce fuel suitable for combustion in internal combustion engines.
Refineries employ various quality control measures to ensure the fuel meets the required standards. This includes rigorous testing and analysis of the fuel at different stages of production. Samples are taken and tested for parameters such as octane rating, sulfur content, and the presence of impurities. Refineries also use advanced purification techniques, like hydrotreating and desulfurization, to remove unwanted contaminants and ensure the fuel's stability and performance.