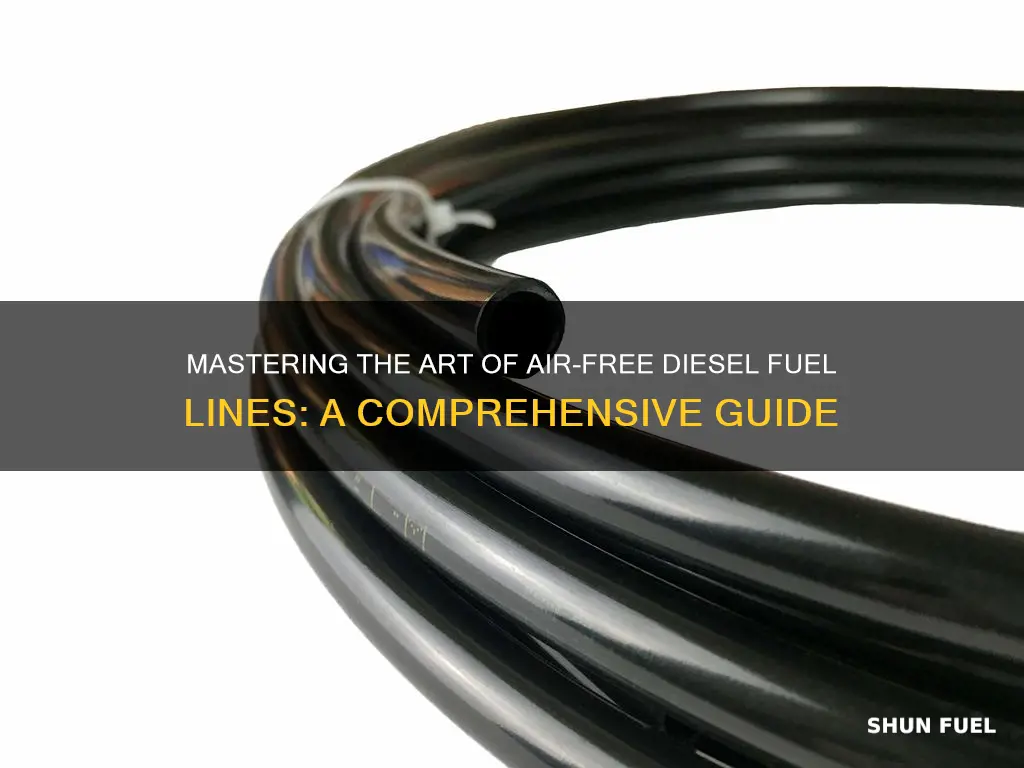
If you're experiencing issues with your diesel fuel system, you might need to know how to remove air from the fuel line. Air bubbles in the fuel can lead to poor engine performance, so it's crucial to address this issue promptly. This guide will provide you with a step-by-step process to safely and effectively eliminate air from your diesel fuel line, ensuring your vehicle runs smoothly.
What You'll Learn
- Bleeding the System: Use a bleed valve to release air bubbles from the fuel line
- Vacuum Pump: Employ a vacuum pump to extract air and ensure fuel purity
- Fuel Filter: Regularly clean or replace filters to prevent air entry
- Pressure Relief: Install pressure relief valves to vent excess air pressure
- Fuel Tank Venting: Ensure proper venting of the fuel tank to maintain atmospheric pressure
Bleeding the System: Use a bleed valve to release air bubbles from the fuel line
To remove air bubbles from a diesel fuel line, a process known as bleeding the system is often recommended. This method involves using a bleed valve, which is typically located near the fuel tank or the engine. Here's a step-by-step guide on how to perform this task:
Locate the bleed valve, which is usually a small, screw-on cap or a dedicated valve on the fuel line. It might be positioned near the fuel filter or at a strategic point along the line to facilitate air removal. Ensure the engine is off and the vehicle is in a stable position to avoid any spills or accidents.
Once you've identified the bleed valve, use a flat-head screwdriver or a similar tool to carefully pry it open. This action will release the air trapped in the fuel line. As you do this, you might hear a hissing sound, indicating the escape of air bubbles. Keep the valve open for a few seconds to allow for a steady flow of air release.
After releasing the air, close the bleed valve securely. This step is crucial to prevent any fuel from escaping and to maintain the integrity of the fuel system. Re-check the valve to ensure it is tightly sealed.
Start the engine and let it run for a few minutes. Listen for any unusual noises, especially hissing or bubbling sounds, which could indicate that air is still present in the system. If you hear such noises, locate the bleed valve again and repeat the process of opening and closing it until the sounds subside.
Remember, this process might require patience and a bit of trial and error. It's essential to be methodical and ensure that all air bubbles are eliminated to maintain optimal engine performance and prevent potential issues caused by air in the fuel.
Step-by-Step Guide: Easily Remove Fuel Line from Eskimo Ice Auger
You may want to see also
Vacuum Pump: Employ a vacuum pump to extract air and ensure fuel purity
The use of a vacuum pump is an effective method to remove air from a diesel fuel line and ensure the purity of the fuel. This process is crucial as air in the fuel can lead to various performance issues and potential damage to the engine. Here's a step-by-step guide on how to employ a vacuum pump for this purpose:
Step 1: Prepare the Equipment
Before starting, ensure you have the necessary tools and equipment. You will need a suitable vacuum pump, preferably a diaphragm or a liquid ring pump, designed for fuel-handling applications. Additionally, gather the required fittings, hoses, and adapters to connect the pump to the fuel line. It is essential to use compatible materials to avoid any contamination.
Step 2: Locate the Fuel Line
Identify the diesel fuel line that you want to purge of air. This line typically connects the fuel tank to the engine or the fuel injection system. Ensure you have access to both ends of the line to facilitate the pumping process.
Step 3: Set Up the Vacuum Pump
Place the vacuum pump in a position where it can be connected to the fuel line. Securely attach the pump's intake hose to one end of the fuel line, creating a sealed connection. The pump's exhaust should be directed to a suitable container or the atmosphere, depending on your preference.
Step 4: Start the Pumping Process
Turn on the vacuum pump and allow it to run for an initial period. The duration can vary, but it is generally recommended to run the pump for at least 10-15 minutes to ensure a thorough extraction of air. During this time, the pump will create a vacuum, pulling out the air from the fuel line.
Step 5: Monitor and Adjust
While the pump is running, monitor the pressure gauge to ensure it maintains a consistent vacuum level. If the pressure drops significantly, it may indicate a leak in the system. Adjust the pump's settings or tighten connections as necessary to maintain the desired vacuum.
Step 6: Complete the Process
After the initial pumping period, continue running the vacuum pump for an additional 5-10 minutes to ensure complete air removal. Then, carefully disconnect the pump from the fuel line, ensuring no fuel or air is released back into the system.
By following these steps, you can effectively use a vacuum pump to remove air from the diesel fuel line, resulting in a pure and clean fuel supply, which is essential for optimal engine performance and longevity.
Volvo VNL Fuel Line Sizing: Expert Guide
You may want to see also
Fuel Filter: Regularly clean or replace filters to prevent air entry
The fuel filter is a critical component in your diesel engine's fuel system, and its primary function is to prevent contaminants, including air, from entering the engine. Over time, fuel filters can become clogged or damaged, which can lead to air entering the fuel line, causing various performance issues. Regular maintenance and attention to the fuel filter are essential to ensure optimal engine performance and longevity.
To maintain a healthy fuel system, it is recommended to regularly inspect and clean or replace the fuel filter. This process is relatively straightforward and can be done by following a few simple steps. First, locate the fuel filter, which is typically positioned along the fuel line, often near the engine or the fuel tank. You may need to consult your vehicle's manual to identify the exact location. Once located, you can start the cleaning or replacement process.
Cleaning the fuel filter is a viable option if it is not excessively clogged. Start by draining any remaining fuel from the system to avoid spills. Then, carefully remove the filter and inspect it for debris, dirt, or any signs of damage. If the filter is clean and in good condition, you can reinstall it. However, if it appears clogged or damaged, it is best to replace it with a new one. Ensure you use the correct type and size of replacement filter compatible with your vehicle.
Replacing the fuel filter is a more comprehensive solution, especially if the current filter is old or frequently clogged. When replacing it, follow the same steps as cleaning, but take extra care to avoid any fuel spills. After replacing the filter, it is crucial to flush the fuel system to remove any contaminants that may have accumulated. This process involves running the engine with the fuel pump on to ensure the new filter is fully functional.
By regularly cleaning or replacing the fuel filter, you can effectively prevent air from entering the diesel fuel line. This simple maintenance task can help maintain engine performance, improve fuel efficiency, and reduce the risk of costly repairs due to air-related issues. Remember, proper maintenance of the fuel system is essential for the overall health and longevity of your diesel engine.
Fuel Line Repair: Revive Your Impala's Performance with These Steps
You may want to see also
Pressure Relief: Install pressure relief valves to vent excess air pressure
When dealing with diesel fuel lines, ensuring that air is effectively removed is crucial to maintaining optimal engine performance. One effective method to achieve this is by installing pressure relief valves, which serve as a vital component in managing the air pressure within the fuel system. These valves are designed to automatically open and release excess air pressure, preventing potential issues caused by air bubbles in the fuel.
The primary function of pressure relief valves is to provide a safe and controlled release of air. When the fuel system operates under pressure, these valves act as a safety net, allowing air to escape and maintaining a consistent and stable fuel-air mixture. This is particularly important in diesel engines, where even small amounts of air can lead to reduced power output, inefficient combustion, and potential engine damage.
Installation of pressure relief valves is a relatively straightforward process. It typically involves connecting the valve to the fuel line at a strategic point where air accumulation is likely. The valve should be positioned in a way that allows it to vent air effectively without causing any disruption to the fuel flow. This might require some customization based on the specific fuel line configuration and engine requirements.
When selecting pressure relief valves, it is essential to consider factors such as the maximum operating pressure of the fuel system and the desired relief pressure. Valves should be chosen to match or slightly exceed the system's maximum pressure to ensure reliable performance. Additionally, the valve's capacity to handle the expected volume of air should be evaluated to guarantee efficient air removal.
By implementing pressure relief valves, you create a dynamic system that actively manages air pressure, ensuring a clean and efficient diesel fuel supply. This method not only helps in removing air but also contributes to the overall longevity and reliability of the engine, making it a valuable addition to any diesel fuel line setup.
Fuel Line Cut: Understanding Gas Flow and Pressure
You may want to see also
Fuel Tank Venting: Ensure proper venting of the fuel tank to maintain atmospheric pressure
Proper venting of the fuel tank is an essential aspect of maintaining the performance and longevity of a diesel engine. When a fuel tank is filled, it creates a vacuum effect, and without adequate venting, air bubbles can form and travel through the fuel lines, leading to various issues. Here's a comprehensive guide to ensuring your fuel tank is properly vented:
Understanding the Importance of Venting:
Venting serves a critical purpose in the fuel system. It allows air to escape from the tank as fuel is added, preventing the formation of vacuum pockets. These pockets can cause air locks, which are essentially bubbles of air in the fuel lines. Air locks can lead to poor engine performance, reduced power, and even engine misfires. Over time, air in the fuel can also cause corrosion in the fuel system, leading to expensive repairs.
Venting Methods:
There are several ways to ensure proper venting:
- Breather Cap: One of the most common methods is using a breather cap on the fuel tank. This cap has a small opening that allows air to escape while preventing dust and debris from entering. It is designed to release pressure as fuel is added, ensuring a smooth flow of fuel into the engine.
- Vent Line: A dedicated vent line can be installed from the fuel tank to the atmosphere. This line should be routed away from the engine to prevent any potential contamination. The vent line allows air to escape, maintaining a consistent pressure within the tank.
- Fuel Pump Breather: Some diesel engines have a built-in breather system associated with the fuel pump. This system vents air directly to the atmosphere, ensuring a continuous flow of fuel without air bubbles.
Installation and Maintenance:
When installing a venting system, it's crucial to follow the manufacturer's guidelines. Ensure the vent line is properly sealed to prevent fuel leakage. Regularly inspect the breather cap and vent lines for any signs of damage or blockage. Clogged vents can lead to increased pressure buildup, which may result in fuel spillage or engine issues. Cleaning or replacing vents as needed will help maintain optimal performance.
Additional Tips:
- Keep the fuel tank's breathing system free from obstructions to ensure efficient venting.
- Consider using a fuel stabilizer, especially if the fuel is stored for extended periods, to minimize the formation of air bubbles.
- Regularly check for any signs of fuel contamination, which may indicate a venting issue.
By implementing these venting methods and maintaining the fuel tank's breathing system, you can effectively remove air from the diesel fuel line, ensuring smooth engine operation and prolonging the life of your vehicle's fuel system.
Thawing Fuel Lines: A Step-by-Step Guide to Unfreezing
You may want to see also
Frequently asked questions
To eliminate air from a diesel fuel line, you can start by ensuring that the fuel tank is properly sealed and there are no leaks. Check for any loose connections or damaged components in the fuel system and tighten or replace them as needed. One effective method is to use a fuel vacuum pump or a manual hand pump to draw the air out. Connect the pump to the fuel line, ensuring a tight seal, and pump the fuel until the air is expelled.
Air in the diesel fuel line can cause several issues, such as poor engine performance, reduced power, and potential engine damage. Common signs include engine misfires, rough idling, reduced fuel efficiency, and the engine may even stall. You might also notice a hissing or bubbling sound coming from the fuel tank or lines when the engine is running.
While a fuel filter can help improve the quality of the fuel and capture some contaminants, it is not primarily designed to remove air. Air bubbles can pass through the filter, so it's essential to use other methods, such as the ones mentioned above, to ensure the air is completely eliminated from the fuel line.
Driving with air in the diesel fuel line is not recommended as it can lead to engine problems and potential damage. The air can cause fuel atomization issues, leading to poor combustion and reduced engine performance. In some cases, it may even result in engine stall, especially during acceleration or when the engine is under load. It is best to address the air issue promptly to ensure safe and efficient operation of the vehicle.