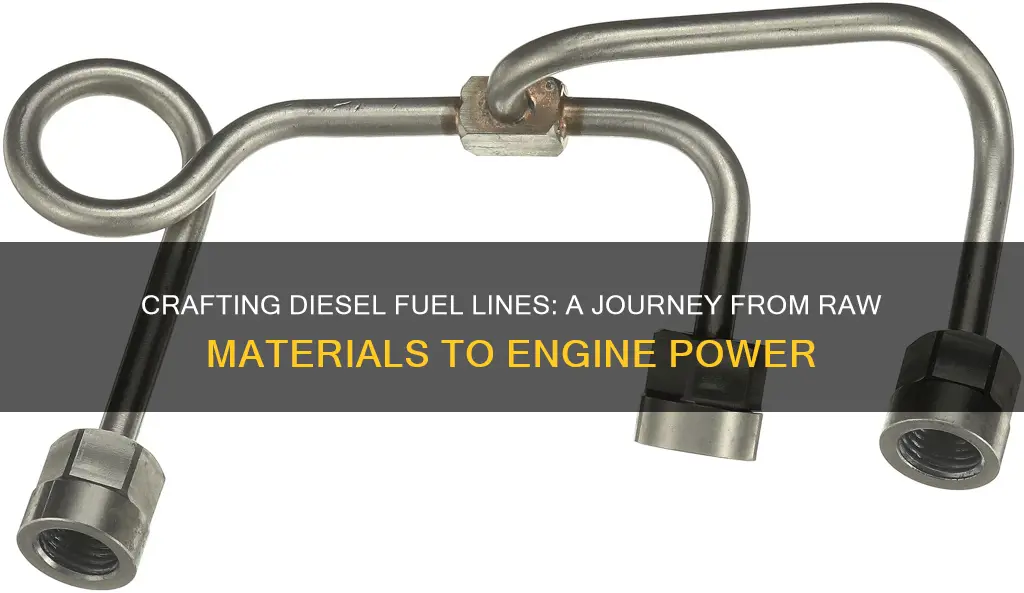
Diesel fuel lines are an essential component in the delivery of fuel from the tank to the engine, and their manufacturing process is a precise and intricate one. These lines are typically made from high-quality materials such as steel or aluminum, which are carefully selected for their durability and resistance to corrosion. The manufacturing process involves several steps, including extrusion, where the material is forced through a die to create the desired shape, and then it is heat-treated to enhance its strength and flexibility. The lines are also often coated with a protective layer to prevent fuel leakage and ensure a reliable fuel supply to the engine. This intricate process ensures that the fuel lines can withstand the high pressures and temperatures encountered in diesel engines, making them a critical part of any vehicle's fuel system.
What You'll Learn
- Raw Materials: Crude oil is refined to create the base diesel fuel
- Distillation: Crude oil is heated to separate into different fractions, including diesel
- Additives: Detergents and antioxidants are added to improve fuel stability and performance
- Filtering: Impurities are removed through filtration to ensure clean fuel
- Storage and Distribution: Fuel is stored and transported to fueling stations
Raw Materials: Crude oil is refined to create the base diesel fuel
The process of creating diesel fuel begins with the raw material of crude oil, a complex mixture of hydrocarbons and other organic compounds. This raw material is the foundation for all petroleum-based products, including diesel. The journey from crude oil to diesel involves a series of intricate refining processes.
The first step in refining crude oil is to separate it into various components through a process known as fractional distillation. This is done in a large, tall column called a fractional distillation tower. Crude oil is heated and vaporized, and as it rises through the tower, it cools and condenses at different temperatures, separating into different fractions or 'cuts'. These cuts include various hydrocarbons of different molecular weights and structures. The lighter fractions, such as gasoline, are collected at the top, while the heavier fractions, like diesel, are collected at the bottom.
The diesel fraction obtained from the distillation process is not yet in its final form. It is a mixture of various hydrocarbons, including alkanes, cycloalkanes, and aromatic hydrocarbons. To convert this mixture into the desired diesel fuel, further refining processes are required. One common method is the use of a process called 'cracking'. Cracking involves breaking down larger, heavier hydrocarbons into smaller, lighter ones through the application of heat and pressure. This process helps to reduce the molecular weight of the diesel fraction, making it more suitable for combustion in diesel engines.
Another crucial step in refining diesel fuel is the process of 'catalytic cracking'. This method uses catalysts, typically made of zeolites or metals, to facilitate the breaking and rearranging of hydrocarbon molecules. By applying heat and pressure in the presence of these catalysts, the diesel fraction can be further refined, resulting in a more consistent and high-quality diesel product.
After these refining processes, the resulting diesel fuel is a complex mixture of hydrocarbons with specific properties, such as cetane number and sulfur content, which are crucial for its performance and environmental impact. The final product is then stored, transported, and distributed for various applications, powering vehicles, machinery, and other equipment that rely on diesel engines.
Mastering Fuel Line Separation: A Step-by-Step Guide
You may want to see also
Distillation: Crude oil is heated to separate into different fractions, including diesel
The process of creating diesel fuel begins with crude oil, a complex mixture of various hydrocarbons and other organic compounds. The first step in the production of diesel is distillation, a crucial process that utilizes the principle of fractional distillation. This method involves heating the crude oil to an extremely high temperature, typically around 400°C (752°F), in a large distillation tower. As the oil is heated, it undergoes a phase change and becomes a vapor. The vapor then rises through the tower, where it is cooled and condensed back into a liquid state.
During this distillation process, the different components of crude oil separate into distinct fractions based on their boiling points. The tower is designed with a series of trays or plates that provide a large surface area for the vapor to come into contact with a cooling medium, usually a stream of cold liquid or a cooling tower. As the vapor cools, it condenses, and the different fractions start to form distinct layers. These fractions are collected at different levels of the tower, and each layer represents a specific range of boiling points and hydrocarbon types.
The lower fractions, closer to the bottom of the tower, have lower boiling points and are primarily composed of lighter hydrocarbons, including gasoline and naphtha. As you move up the tower, the fractions become heavier and contain more complex hydrocarbons. The middle fractions, such as kerosene and diesel, have boiling points that fall within a specific range, typically between 180°C and 350°C (356°F and 662°F). These fractions are collected in the middle sections of the tower.
Diesel fuel is specifically targeted during this distillation process. The diesel fraction is carefully collected and further processed to meet the required specifications. This involves removing any impurities and ensuring the fuel meets the desired cetane number, which indicates its ignition quality. The collected diesel fraction is then sent for further refining, where it undergoes additional processes to improve its quality and meet the standards for various applications.
After distillation, the diesel fuel is further processed through various refining techniques, such as solvent extraction, to remove any remaining impurities and ensure the final product meets the required specifications for its intended use. This detailed process ensures that the diesel fuel produced is of high quality and suitable for powering vehicles and machinery.
Fixing Fuel Leaks: A Guide to Rubber Fuel Line Repairs
You may want to see also
Additives: Detergents and antioxidants are added to improve fuel stability and performance
The process of manufacturing diesel fuel lines involves several crucial steps to ensure the final product meets the required standards and performs optimally. One essential aspect of this manufacturing process is the addition of specific additives to the fuel, which significantly enhances its stability and overall performance.
Detergents are a class of additives that play a vital role in maintaining the cleanliness of diesel fuel systems. These compounds are carefully designed to neutralize the acidic byproducts formed during the combustion process. When diesel fuel is burned, it can produce sulfuric acid, which, if left unchecked, can lead to the formation of harmful deposits and sludge in the fuel system. Detergents effectively combat this issue by neutralizing these acids, preventing the accumulation of harmful substances and ensuring the fuel remains clean and free-flowing. This is particularly important in diesel engines, where fuel system cleanliness is critical to performance and longevity.
Antioxidants, another essential additive, are added to diesel fuel to combat oxidation, a natural process that occurs when fuel is exposed to air. Oxidation can lead to the degradation of fuel, causing it to become less efficient and potentially harmful to the engine. Antioxidants work by inhibiting this oxidation process, thus preserving the fuel's quality and performance over time. This is especially critical in diesel fuel, as it is more susceptible to oxidation due to its higher sulfur content compared to gasoline. By adding antioxidants, manufacturers ensure that the fuel remains stable and performs consistently, even when stored for extended periods.
The combination of detergents and antioxidants in diesel fuel is a strategic approach to enhancing its overall quality. These additives work synergistically to improve fuel stability, ensuring that it remains effective and safe for use in engines. Detergents maintain the cleanliness of the fuel system, preventing the buildup of harmful deposits, while antioxidants protect the fuel from degradation caused by oxidation. This two-pronged strategy is a key factor in the manufacturing process, contributing to the reliability and performance of diesel fuel lines.
In summary, the addition of detergents and antioxidants to diesel fuel is a critical step in the manufacturing process, designed to optimize fuel stability and performance. These additives address specific challenges associated with diesel fuel, ensuring that it remains clean, efficient, and safe for use in various applications. By incorporating these additives, manufacturers can deliver a high-quality product that meets the demands of modern diesel engines.
Unveiling the Material Mystery: What Fuels Clear Fuel Lines?
You may want to see also
Filtering: Impurities are removed through filtration to ensure clean fuel
The process of filtering diesel fuel is a critical step in ensuring the quality and performance of the fuel. Impurities in diesel can lead to various issues, including engine misfires, reduced power, and increased wear and tear on engine components. Therefore, effective filtration is essential to maintain the efficiency and longevity of diesel engines.
Filtering begins with the raw diesel fuel, which is typically a mixture of hydrocarbons and other organic compounds. The first line of defense against impurities is the initial filter, often located near the fuel tank. This filter is designed to capture larger particles and debris that may be present in the fuel, such as dirt, rust, and water. It acts as a physical barrier, preventing these contaminants from entering the fuel system further. The initial filter is usually a simple mesh or pleated element that traps particles as the fuel passes through it.
After the initial filtration, diesel fuel lines employ more advanced filtration systems to ensure the highest level of cleanliness. One common method is the use of a multi-stage filtration process. This involves passing the fuel through multiple filters, each with a different micron rating, to capture a wide range of impurities. The first stage might use a coarse filter to remove larger particles, followed by finer filters to trap smaller contaminants. This multi-stage approach ensures that the fuel is thoroughly cleaned, removing not only visible particles but also microscopic ones.
In addition to mechanical filters, diesel fuel lines may also incorporate chemical filtration techniques. This involves adding specific chemicals to the fuel to neutralize or precipitate out impurities. For example, fuel lines might use a fuel additive that reacts with water, causing it to separate and settle at the bottom of the fuel tank. This process helps to remove water-borne contaminants, ensuring that the fuel remains free from moisture-related issues.
The filtering process is an ongoing one, as diesel fuel lines are designed to continuously filter impurities. Filters are regularly replaced or cleaned to maintain their effectiveness. This maintenance is crucial, as clogged or ineffective filters can lead to fuel contamination, causing engine problems. Therefore, proper filtration is a vital component of diesel fuel production and distribution, ensuring that the fuel delivered to engines is clean, reliable, and of high quality.
Marine Fuel Line Compression Fittings: A Comprehensive Guide
You may want to see also
Storage and Distribution: Fuel is stored and transported to fueling stations
The process of storing and distributing diesel fuel involves a series of steps to ensure the fuel remains stable and safe until it reaches the end consumer. Once the fuel is produced and refined, it is transported to storage facilities, often located away from urban areas to minimize environmental risks. These storage facilities are designed with multiple layers of protection to prevent any potential hazards. The fuel is typically stored in large tanks, each with its own safety measures, such as emergency shut-off valves and fire suppression systems. The tanks are regularly inspected and maintained to ensure they are in optimal condition.
Storage facilities are equipped with advanced monitoring systems that track fuel levels, temperature, and pressure. This data is crucial for efficient management and helps prevent overfilling or underfilling of storage tanks. The fuel is kept under controlled conditions to maintain its quality and prevent degradation. Temperature and humidity are carefully regulated to ensure the fuel remains stable and does not spoil. This is particularly important for diesel fuel, as it can be sensitive to changes in temperature and may require specific storage conditions to remain effective.
Transportation of diesel fuel from storage facilities to fueling stations is a critical part of the distribution process. This is typically done using large, specialized trucks designed to carry bulk fuel. These trucks are equipped with advanced fuel management systems that ensure precise control over the fuel's temperature and pressure during transit. The fuel is transported in insulated tanks to maintain its stability and prevent any temperature fluctuations that could affect its quality.
During transportation, fuel lines are carefully managed to ensure a continuous and safe supply. The fuel lines are designed to handle the pressure and volume of the fuel, with multiple layers of protection to prevent leaks or spills. These lines are often made of durable materials such as steel or high-density polyethylene (HDPE) to withstand the rigors of transportation and potential environmental factors. Specialized connectors and valves are used to join the fuel lines, ensuring a secure and leak-proof connection.
Upon arrival at the fueling station, the fuel is carefully offloaded and stored in additional tanks. These tanks are also regularly inspected and maintained to ensure they are in good working order. The fueling station's infrastructure is designed to handle the fuel efficiently, with pumps and dispensing systems that are regularly calibrated to provide accurate fuel measurements. This final stage of distribution ensures that diesel fuel is readily available for customers, meeting the demands of various industries and applications.
Stock FE Fuel Line: Understanding the Optimal End Size
You may want to see also
Frequently asked questions
Diesel fuel lines are commonly made from materials such as steel, aluminum, or specialized polymers like polyvinyl chloride (PVC) or high-density polyethylene (HDPE). These materials are chosen for their durability, resistance to fuel degradation, and ability to withstand high-pressure environments.
The manufacturing process for diesel fuel lines can vary slightly compared to gasoline lines. Diesel fuel often requires additional considerations due to its higher boiling point and potential for contamination. Manufacturers might use different sealing methods, such as crimp seals or compression fittings, to ensure a secure connection. The materials used may also be more resistant to thermal and chemical degradation to handle the higher fuel temperatures.
Yes, diesel fuel lines are subject to various industry standards and regulations to ensure safety and performance. For example, the fuel lines should be able to withstand pressure tests, temperature variations, and chemical compatibility with the fuel. Standards like ISO 22299 and specific vehicle manufacturer guidelines often dictate the design, material selection, and testing requirements for diesel fuel lines to ensure they meet the necessary quality and safety standards.